Xometry offers a wide range of finishing options for our customer's custom-made parts, including anodizing, metal plating, and powder coating, to name a few. Abrasive media blasting is a cost-effective way to prepare the surface of your part or alter the cosmetic appearance. This article will walk through one of our most common media blasting finishes; bead blasting. You will learn what bead blasting is, what sort of applications it is used for, and get tips on how to get the most out of the process.
What is Bead Blasting?
Bead blasting is a type of abrasive blasting process in which media is projected onto a surface. The process is often performed using abrasive blast cabinets, which typically use compressed air to accelerate the media. They also provide an enclosed space for the operator to work up close with parts and help avoid spreading dust or contaminants into the air. Round glass beads are widely used for bead blasting and Xometry's media of choice for the process.
Unlike other types of media blasting, which typically use angular-shaped media, bead blasting is associated with the use of spherical-shaped media. When a piece of rounded media impacts a part's surface, it produces a tiny dimple at the impact location. As the process continues, thousands of these dimples consistently form over the surface. When using finer grades, the blasted surface will appear bright with a matte or satin-like texture due to how light reflects off the dimpled surface. Coarser beads can be used to produce a rougher but uniform surface.
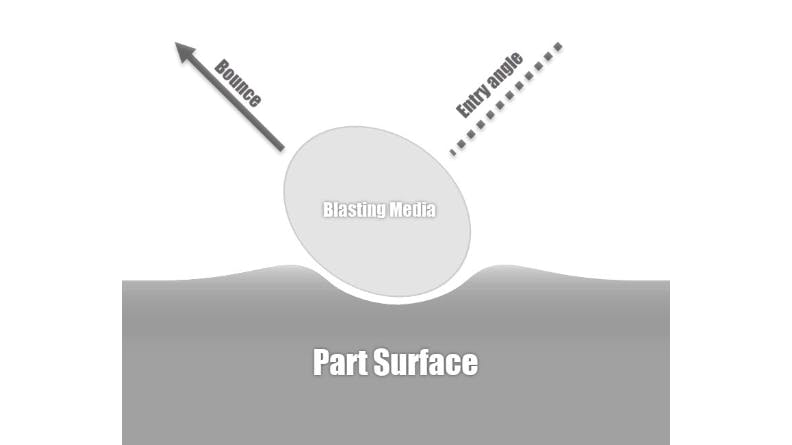
Diagram of a surface dimple created during the bead blasting process
Materials Used for Bead Blasting
Glass Bead
Glass beads are one of the most commonly used media types for the bead blasting process. They are usually made from a type of lead-free, soda-lime glass which is environmentally friendly as it does not contain free silica and is chemically inert. When used appropriately, glass bead media is quite durable and can often be re-used up to 30 times. This type of media will not colorize the surface on impact and thus help maintain the material's base color.
While versatile for many applications, glass bead may not be as suitable for extremely tough materials and is ineffective at etching the surface for paint preparation. This type of media is ideal for surface cleaning, semi-polishing, or peening applications.
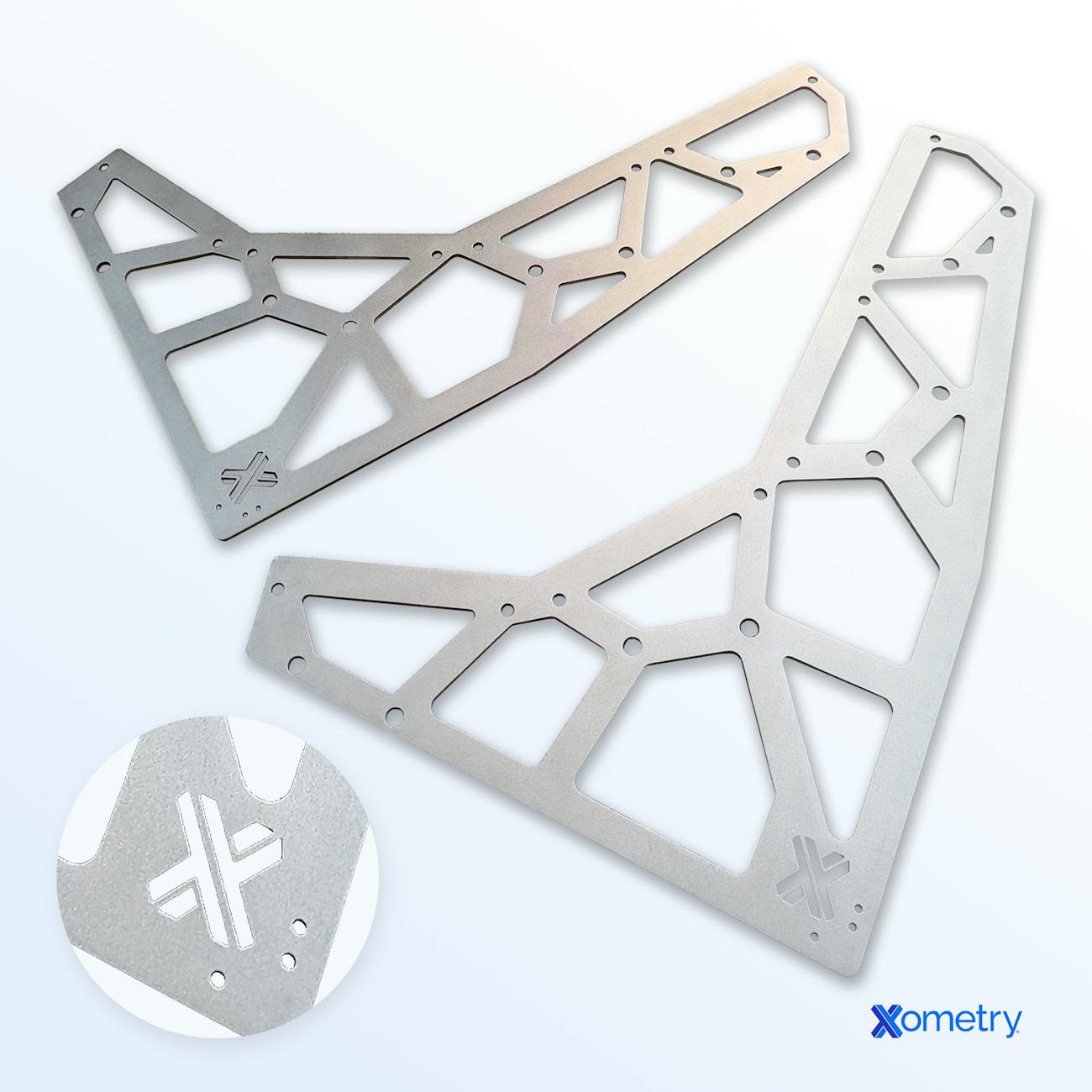
Steel Shot
Steel shot is another type of media that can be used. It is made by casting small steel beads according to SAE standard sizes ranging from S-70 (~0.125mm screen size) to S930 (~3mm screen size). There are also multiple hardness ranges, which go from a hardness of 40 Rc up to 62 Rc. The hardness and density of steel shot make it highly durable and in many cases enable it to be re-used for hundreds of cycles! The most common uses for this type of media are cleaning, de-rusting, stripping, and shot peening applications. Metal surfaces can be stress-relieved and hardened to prevent metal fatigue when shot peened using steel shot media.
Steel shot is best used for heavy-duty applications and materials such as steel and cast iron; it is not generally suitable for softer metals or plastics.
Aluminum Oxide
Aluminum Oxide is a tough and abrasive grit media with an angular shape and is often used as a substitute in the sand blasting process. Due to its hardness and angular shape, it is effective at quickly cutting into and etching even the hardest materials. It is often used to prepare surfaces for paint, round sharp edges, and provide a consistent-looking finish. The roughness of the finish will generally correlate to the grit size used. Larger-sized grit will etch the surface more quickly and leave a rougher finish, while finer grits will leave a smoother finish with longer processing times.
Surfaces blasted with aluminum oxide will attain a consistent matte finish with a dull appearance. Aluminum oxide is generally brown in color and can cause some discoloration. Aluminum oxide can be used prior to anodizing to produce uniformly matte anodized parts. It is not suitable for applying finishes to plastic parts.
Plastic Media
While there are multiple types of plastic blasting media, the most common and widely used is called Urea. It is made of angular-shaped grains of recycled plastic materials. Being plastic, it is much more gentle than most other abrasives, highly re-usable, and lightweight. This makes it ideal for use on delicate parts or materials without causing damage. Blasting equipment can accelerate the lightweight plastic particles to high velocities, making it effective at quickly stripping light coatings. Plastic blast media is also helpful for de-flashing and deburring operations for molded parts.
While plastic media such as Urea is excellent for cleaning and stripping applications, it is not a good option for achieving cosmetic finishes since the media does not dimple the surface like other types of media.
Bead Blasting vs. Sand Blasting
While both bead blasting and sand blasting are similar in that they are types of media blasting techniques and sometimes share similar purposes, each is distinct with its advantages and disadvantages. To help you better understand the differences and make the right choices for your project, we have outlined some of the critical aspects for each below.
Bead Blasting
In bead blasting, spherical-shaped media usually made of glass is accelerated to high speed towards the work surface. The round shape of the media has a peening effect and creates small dimples on the surface. The dimples act like miniature mirrors that scatter and reflect light towards the viewer, giving the part a bright and uniform satin-like appearance.
Pros
- No free silica or silica dust
- Gentle on materials
- Does not affect part dimensions
- Media is often highly re-usable for multiple cycles
Cons
- Slow at removing paint and coatings
- Does not etch surfaces for paint adherence
- Slow to work with on harder materials
Sand Blasting
Sand blasting is a more traditional abrasive media blasting technique in which silica sand is propelled under high pressure towards the workpiece. The irregular shape and sharpness of the sand particles can cut into and etch surfaces with ease. Due to high abrasion, sand blasting can be used to shape surfaces, smooth rough surfaces, and remove surface contaminants such as rust or corrosion. While silica sand is still used in some cases, it is being moved away from due to potential health hazards, and other types of abrasive media are now commonly used in its place. Generally, abrasion blasted parts will have a duller appearance than those that are bead blasted.
Pros
- Very fast at removing paint and coatings
- Can prepare surfaces for paint adhesion by etching the surface
- Works on the toughest materials
Cons
- Potential health hazards (e.g., Silicosis) related to free silica when using sand media
- Not suitable for fragile components or materials
- Can result in material removal, which can affect part dimensions; not suitable for tight toleranced components
Blasting Media Selection Chart
To help you decide what type of media may be the best for your project, we have made a comparison chart comparing the effectiveness and properties of different media types for various applications. Keep in mind the chart is meant as a general reference guide. Factors such as blast pressure, workpiece hardness, media shape, and operator technique can affect the effectiveness and life of the media.
Blasting Media Selection Chart
Characteristic / Media | Glass Bead | Steel Shot | Ceramic Shot | Aluminum Oxide | Garnet | Plastic Media |
---|---|---|---|---|---|---|
Characteristic / Media Cleaning / Removal | Glass Bead ✔️ | Steel Shot ✔️ | Ceramic Shot ✔️ | Aluminum Oxide ✔️ | Garnet ✔️ | Plastic Media ✔️ |
Characteristic / Media Peening | Glass Bead ✔️ | Steel Shot ✔️ | Ceramic Shot ✔️ | Aluminum Oxide -- | Garnet -- | Plastic Media -- |
Characteristic / Media Surface Etching | Glass Bead -- | Steel Shot -- | Ceramic Shot -- | Aluminum Oxide ✔️ | Garnet ✔️ | Plastic Media ✔️ |
Characteristic / Media Recyclability / Media Life | Glass Bead Medium | Steel Shot High | Ceramic Shot Very-High | Aluminum Oxide Med-High | Garnet Med-Low | Plastic Media Medium |
Characteristic / Media Probability of Material Removal | Glass Bead Very Low | Steel Shot Very Low | Ceramic Shot Very Low | Aluminum Oxide Med-High | Garnet Medium | Plastic Media Very Low |
Characteristic / Media Mohs' Hardness | Glass Bead 5.5 | Steel Shot 6-7.5 | Ceramic Shot 7 | Aluminum Oxide 8-9 | Garnet 8 | Plastic Media 3-4 |
Characteristic / Media Typical Blast Pressure (PSI) | Glass Bead 20-55 | Steel Shot 20-90 | Ceramic Shot 20-90 | Aluminum Oxide 20-90 | Garnet 30-80 | Plastic Media 20-60 |
Characteristic / Media Media Shape | Glass Bead ⬤ | Steel Shot ⬤ | Ceramic Shot ⬤ | Aluminum Oxide ▲ | Garnet ▲ / ⬤ | Plastic Media ▲ |
✔️ = Suitable
⬤ = Spherical
▲ = Angular
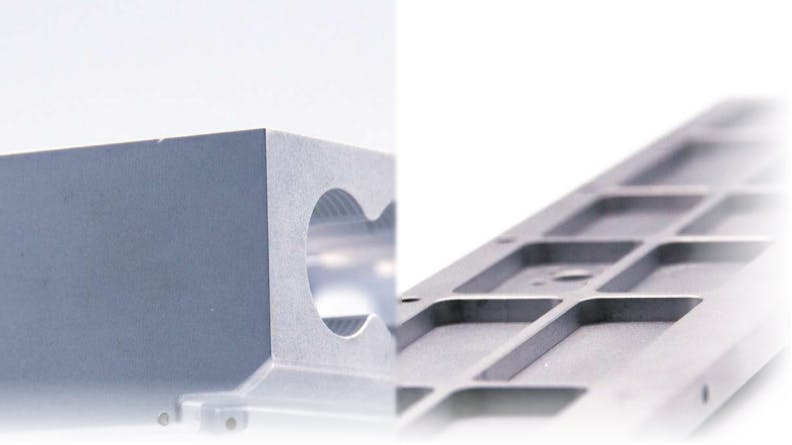
From the wide selection of available media to the applied pressure and technique, many variables can influence the appearance of your bead blast finished parts. Suppose you are looking to achieve a particular finish. In that case, it is essential to provide specifications to control some of these variables to guide the intended result. When striving for consistent results across production runs or multiple batches, specifications are critical.
When ordering bead blasted parts through Xometry's Instant Quoting Engine, if no further instructions are provided, we will defer to using glass bead media and sufficient pressure to remove tool marks and smooth the surface without damaging the part. The sections below go over tips and best practices you can incorporate to achieve greater control of the process and more predictable and consistent bead blast finishes.
Media Specification
The type of media or abrasive used will significantly influence the look and feel of your finish. For instance, fine glass beads will produce a consistent, satin-like finish, whereas aluminum oxide will yield a uniform but duller appearance. It may take some experimentation to determine what media works best for your project, but you will want to include that information in your order or part drawings notes section once you do. In addition to the type of media, be sure to specify its shape if there are multiple options to choose from.
Abrasive Grade / Grit Size
Another variable that plays a role in how your finish comes out is the particle size of your chosen media. Suppliers often refer to the abrasion grade or grit. The grit is very similar to what you would find when shopping for sandpaper at your local hardware store. The lower the grit, the larger and more coarse the particles are. On the other hand, higher grits will be of finer particles. Mesh size is often referred to as well. The easiest way to understand mesh size is if you were to observe a 1"x1" screen made up of equally sized holes. With a mesh size of 20, there would be 20 holes in the screen, and particles smaller than those holes will pass through, while larger ones will be blocked. With a mesh size of 200, there would be 200 holes in the same 1"x1" area, and thus would be much smaller and only allow finer particles to pass through.
Media size is typically broken down into coarse, medium, fine, and very fine grades. Calling out a grade will simplify your notes and prevent being overly specific, which can limit a manufacturer's options.
Avoid Tight Surface Roughness Callouts
By the nature of the blasting process, the part's surface roughness will be directly impacted. It can be challenging for shops to maintain tight surface roughness requirements while also applying a media blasted finish. When these requirements mix, it is often the case that a shop will want to pause the project and get clarification on what the expectations are.
We recommend limiting surface roughness to no lower than 32 µin Ra when you need a smooth bead blasted part. We do not recommend blasting surfaces that must be lower than 32 µin Ra and instead call out for masking on just those surfaces. Take note that masking requirements can significantly increase labor time and thus cost.
Provide a Boundary Sample
A boundary sample can be invaluable for manufacturers when producing a finish that meets expectations. If your project has strict finishing criteria or detailed notes, a boundary sample can help resolve concerns and provide clarity. Manufacturers can use their knowledge and expertise to produce an output that matches provided examples, reducing the need for detailed notes. If a physical sample is not available, the next best thing would be high-resolution photos taken at various angles. Xometry's engineers and case managers can help you make such arrangements with our manufacturers after placing your order.
Masking Callouts for Critical Features
Lastly, we recommend including masking notes if your part has any critical features or surfaces that should be guarded against abrasion. Examples of these features are sealing surfaces and o-ring grooves. Although most shops already do this per shop practice, we recommend adding masking requirements for threaded features, especially for small or fine pitch threads.
Example drawing notes for bead blasted finishes:
- "Bead blast all surfaces using fine grade glass bead media."
- "Media blast with #70-100 glass bead at 50-60psi."
- "Mask indicated surfaces and tapped holes prior to media blasting. Media blast un-masked surfaces with medium grade aluminum oxide."
How Xometry Can Help
Bead blasting uses spherical shaped media to semi-polish, peen, or apply satin finishes to metal parts amongst other numerous applications, all while maintaining dimensional accuracy. Xometry makes it easy to get custom parts with bead blast or other finishes! Simply upload your files to the Xometry Instant Quoting Engine® and select "Bead Blast" from the finishes dropdown to get an instant quote on your parts today!
Disclaimer
The content appearing on this webpage is for informational purposes only. Xometry makes no representation or warranty of any kind, be it expressed or implied, as to the accuracy, completeness, or validity of the information. Any performance parameters, geometric tolerances, specific design features, quality and types of materials, or processes should not be inferred to represent what will be delivered by third-party suppliers or manufacturers through Xometry’s network. Buyers seeking quotes for parts are responsible for defining the specific requirements for those parts. Please refer to our terms and conditions for more information.
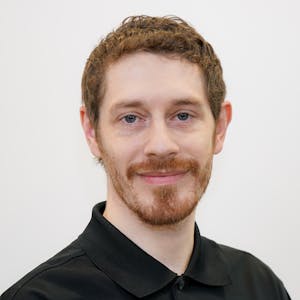