Taps make threaded holes so that they’re ready for fasteners like screws and bolts to be inserted or tightened with a drill or appropriate hand tool. Turning the tap by hand creates threads inside pre-drilled holes. They’re found in manufacturing parts, like vehicles and structures, and they’re also in flat-packed furniture—handy for those putting it together as they won’t have to manually make these holes.
Thread Tap Types
There are tons of different types of thread taps with many varying endpoints, tapers, and flutings. Let’s look at 13 of them to help you decide on the right one for your needs—because, let’s face it, knowing which one to use is a total shot in the dark.
Hand Taps
Hand taps are multifunctional and work either by hand or with a power tool. They’re used for machine tapping in general and most materials with blind or through holes. These have straight flutes used in shallow blind or through holes. A standard hand tap set has three separate types, which we’ll discuss below.
Plug Taps
A plug tap has a five-thread cutting chamfer that slowly cuts away material to create the thread, starting with the smaller diameter. They’re used when there is enough space at a blind hole’s bottom part, or to make through-holes. They make a more complete set of threads compared to taper taps, but aren’t as well suited to finishing threads in blind-holes as bottoming taps.
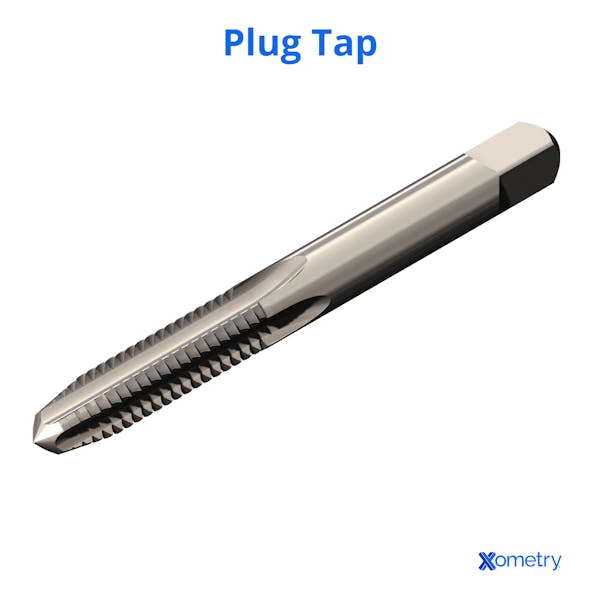
Taper Taps
These have nine-thread chamfers and the smallest diameter of any hand taps. Taper taps are typically the starting point for blind- or through-hole applications. One of their biggest advantages is they clear out most of the material early in the process. They shouldn’t be used for finishing the bottom of blind holes since they can leave incomplete threads.
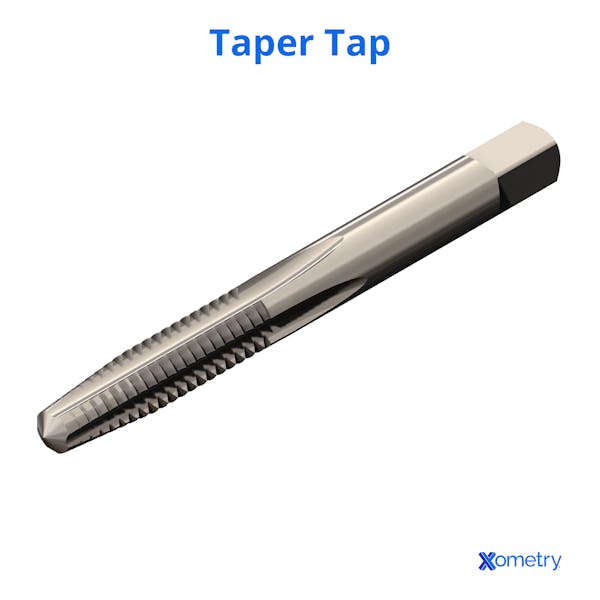
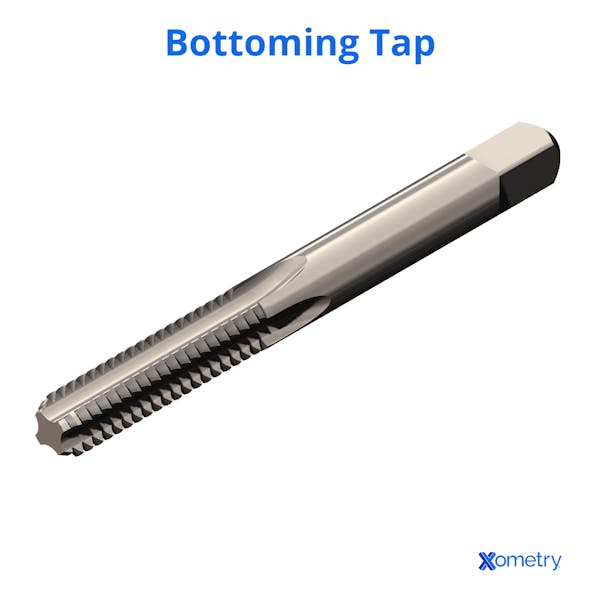
Pipe Tap
Pipe taps carve threads for pipes internally for pressure-tight joints. Some pipe taps are made for hydraulic and gas purposes, and others for mechanical joints and hose couplings. They have to be done more carefully than other types because they’re designed to mechanically seal a joint to add pressure and prevent leaks.
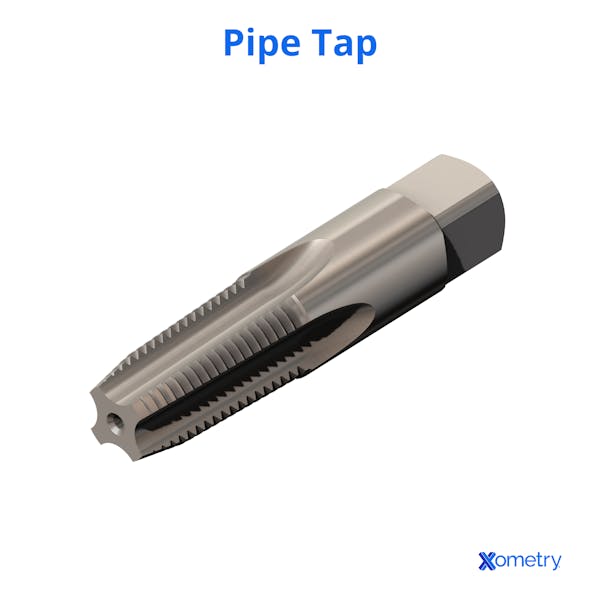
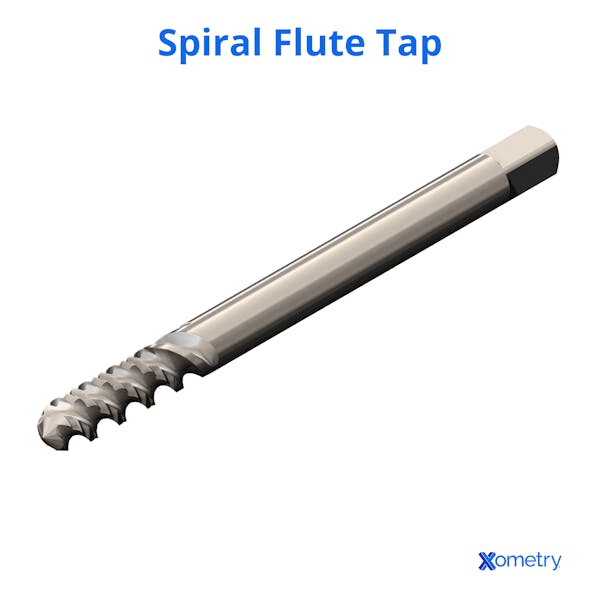
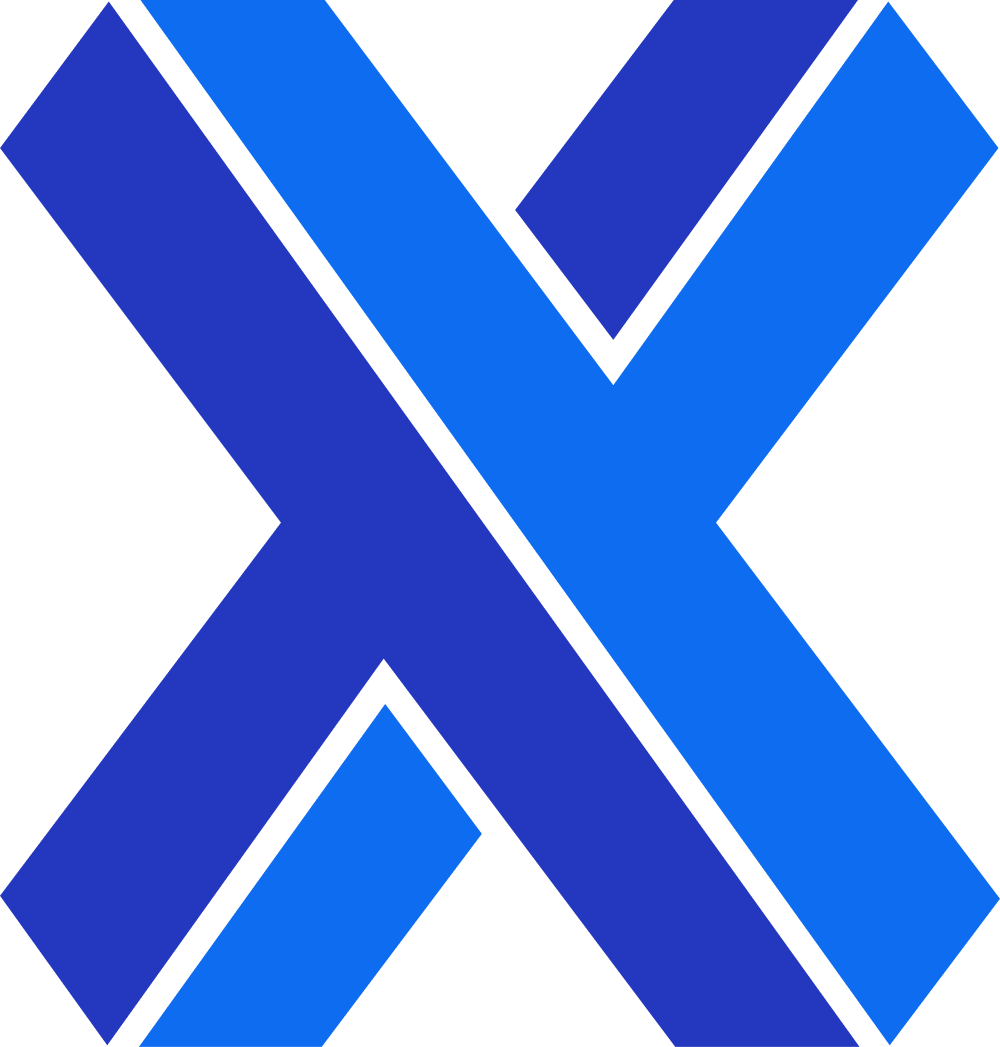
Machine Tap
The growing use of machinery in manufacturing has meant an increase in machine taps, too. These have to be durable and particularly resistant to wear. Automated machining processes (like CNC) use these taps to create both blind holes and through holes on hard materials, where spiral flute taps won’t be strong enough. Sometimes their cutting end is coated with titanium nitride (shown in the below image) to give it more wear resistance and increase its lifespan.
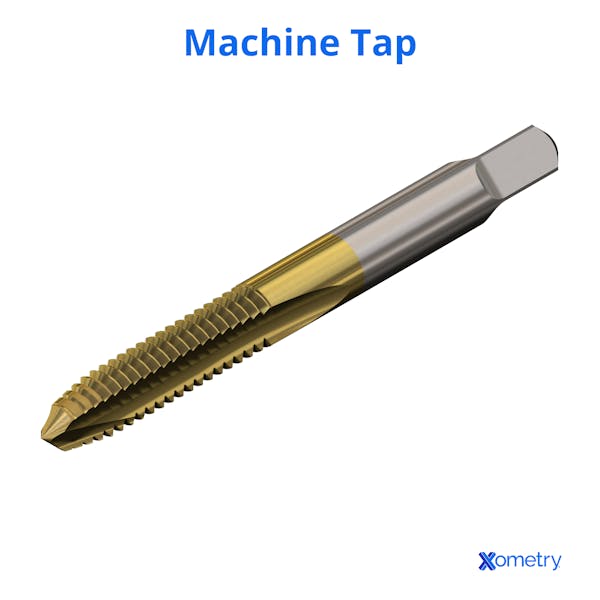
Thread-Forming Tap
Also known as fluteless taps or rolled threads, these taps don’t actually cut threads; they cold-form them instead, during which the metal isn’t cut, but moved away before being compressed into position. No chips are formed in the process, meaning you don’t have to remove any. These taps make stronger threads that are less likely to break.
We suggest using form taps instead of cutting taps whenever you can, as long as the material isn’t too hard. Lots of people think that these are only good for soft materials like aluminum, but they work with any material with a hardness of 36 HRC (or 340 BHN). That covers a bunch of materials, including a lot of steel types.
Pro tip: It’s important to know that form taps need different feeds and speeds, as well as different starting hole sizes. There’s another common hiccup among quite a few roll-forming taps: the oil can build up back pressure as the tap goes in, and eventually act like a plug that blocks the tap from getting further into the hole. There has to be a groove to let cutting oil escape, or room at the root or crest of the thread.
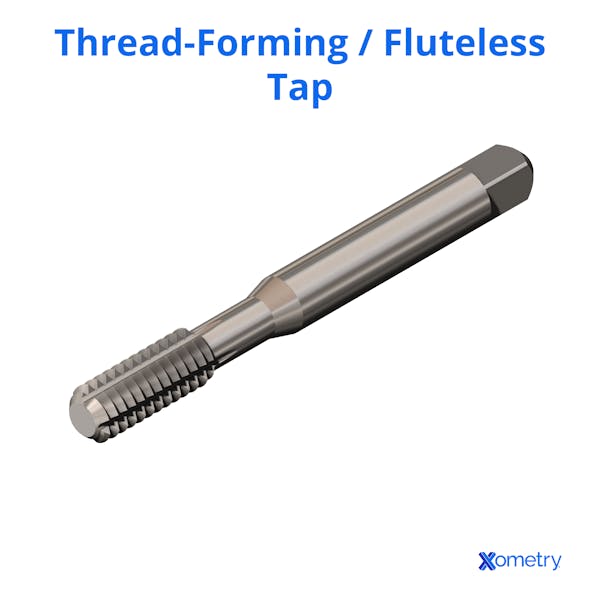
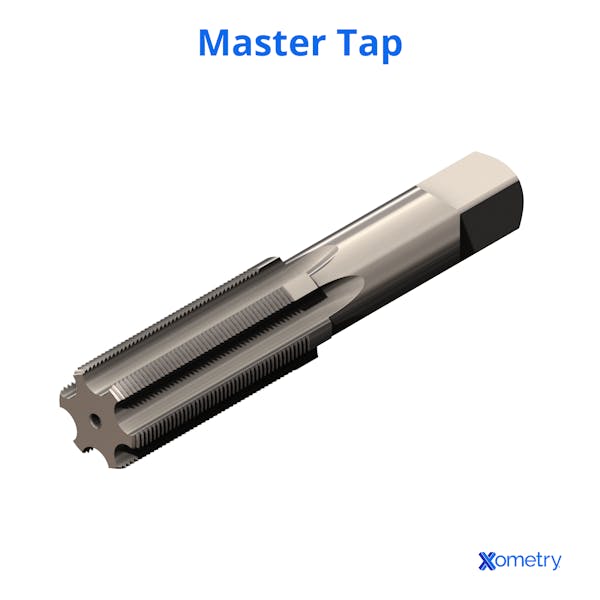
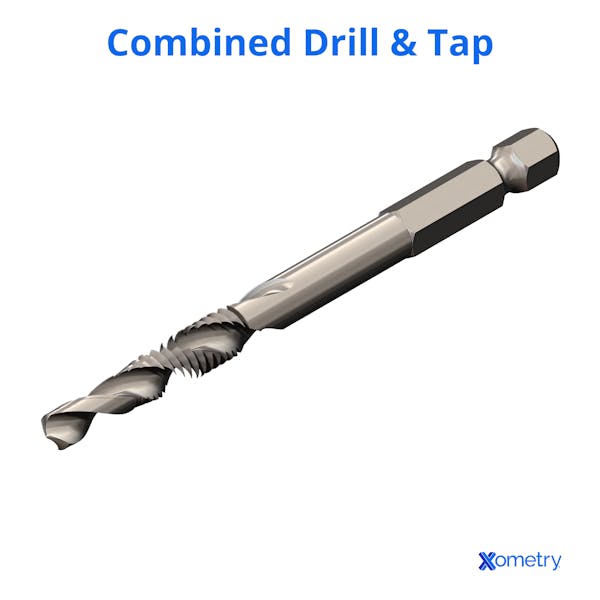

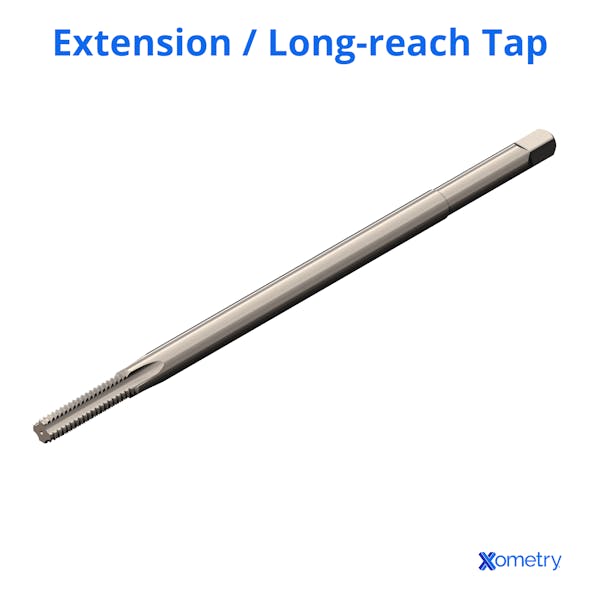
Spiral Point Tap
These taps are strong and made to work faster than regular taps on hard materials, and don’t need as much power, either. They make shallow grooves that can remove more metal in one go. Some feel they are similar to straight flute taps since they share the same general shape, but they have different cutting faces.
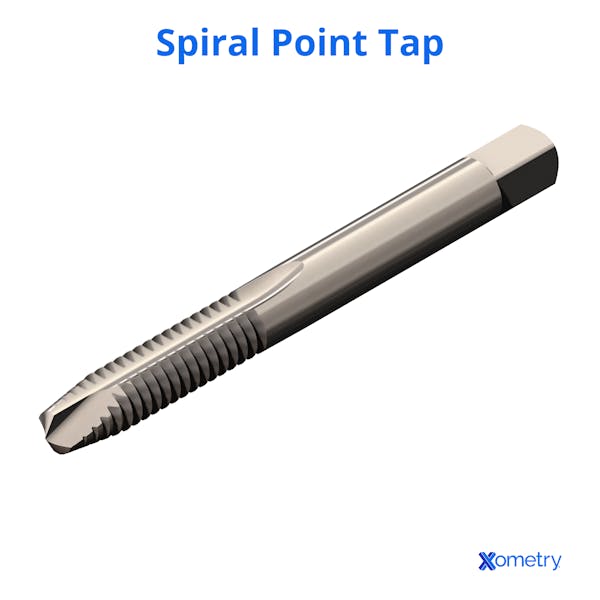
Stay Bolt Tap
A stay bolt tap is around 15-20 inches long. It’s designed to cut threads in drilled holes for threaded machine screws or threaded bolts to be screwed in, in the exact diameter of the stay bolt nut. They were commonly used in installing and repairing fireboxes in steam locomotives.
Interrupted Thread Tap
This type of tap only has a tooth for every other thread. It’s designed to provide better chip extraction. Removing every other tooth helps with breaking up the chips. It also gives more room, both for the chip to clear out and the lubricant to enter.
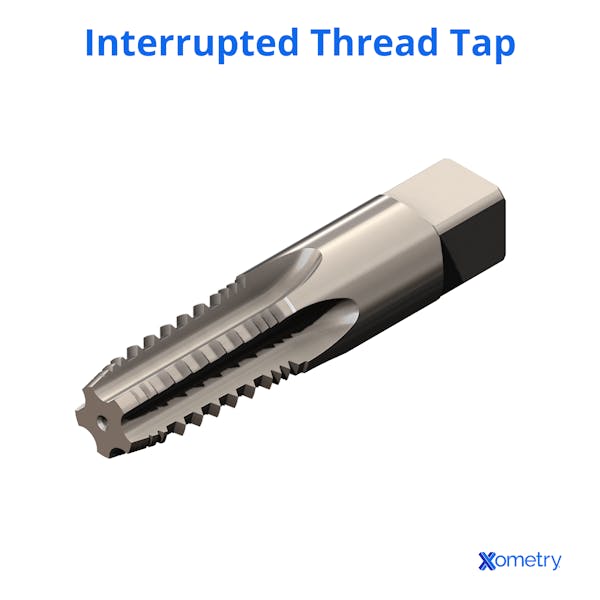
Type | Hole Size/Type | Chamfer Type/Flute Design | Material | Uses |
---|---|---|---|---|
Type Plug | Hole Size/Type M3–M12, blind and through | Chamfer Type/Flute Design 5-thread, straight | Material HSS (high-speed steel) | Uses Finishing threads |
Type Taper | Hole Size/Type M3–M12, blind and through | Chamfer Type/Flute Design 9-thread, straight | Material HSS | Uses Starting threads |
Type Bottoming | Hole Size/Type M3–M12, blind | Chamfer Type/Flute Design 1.5-thread, straight | Material HSS | Uses Completing threads to the bottom of blind holes |
Type Pipe | Hole Size/Type NPT/NPTF* | Chamfer Type/Flute Design n/a, straight | Material HSS | Uses Sealing pressure-tight joints |
Type Spiral flute | Hole Size/Type M3–M12, blind | Chamfer Type/Flute Design n/a, helical flutes | Material HSS, coated HSS | Uses Tapping blind holes, evacuating chips upwards |
Type Gas | Hole Size/Type M3–M12, cylindrical and conical | Chamfer Type/Flute Design 1–2-thread, straight | Material HSS | Uses Gas and hydraulic systems, deep thread cutting |
Type Machine | Hole Size/Type M3–M20, blind and through | Chamfer Type/Flute Design 3–7-thread, straight | Material HSS, TiN-coated HSS | Uses CNC machining, automation on hard materials |
Type Thread-forming | Hole Size/Type M3–M12, through | Chamfer Type/Flute Design n/a (forms threads) | Material HSS, carbide | Uses Cold-forming threads, chip-free threading in materials up to 36 HRC |
Type Master | Hole Size/Type M8–M24, blind and through | Chamfer Type/Flute Design 7–10-thread, straight or spiral | Material HSS | Uses Clean threads in strong, hard materials |
Type Combined drill/tap | Hole Size/Type M3–M10, through | Chamfer Type/Flute Design n/a, helical | Material HSS, carbide | Uses Simultaneous drilling and tapping |
Type Solid carbide | Hole Size/Type M3–M20, blind and through | Chamfer Type/Flute Design n/a, straight/spiral | Material Solid carbide | Uses Hard materials with high wear resistance |
Type Extension | Hole Size/Type M5–M16, blind and hard-to-reach | Chamfer Type/Flute Design n/a, long shank, straight | Material HSS | Uses Accessing deep or narrow holes |
Type Spiral point | Hole Size/Type M3–M20, through | Chamfer Type/Flute Design n/a, shallow, forward chip ejection | Material HSS | Uses High-speed tapping with low power needs |
Type Stay bolt | Hole Size/Type Custom sizes, large-diameter holes | Chamfer Type/Flute Design n/a, long shank (15–20-inch), straight | Material HSS | Uses Bolts for fireboxes, steam trains, heavy machinery |
Type Interrupted thread | Hole Size/Type M5–M16, blind and through | Chamfer Type/Flute Design n/a, alternating teeth, straight/spiral | Material HSS | Uses Better chip clearance and lubrication access |
Thread Taps Summary: *NPT and NPTF are the standardized thread forms for pipe fittings in the U.S. (NPT needs a sealing material, but NPTF is self-sealing)
Standard Tap Markings
Taps have marks on the shank, so you can tell with just a look what type of thread tap you’re working with. The markings include the nominal size, which is the thread size that the tap will take. There’s also the thread form symbol, which identifies the thread family. There’s also tap material, which is usually carbide or HSS. It also typically shows the pitch diameter limit, which tells what tolerance thread will be made.
Pitch Diameter Limits
Here is a quick guide for threads with a diameter of less than an inch:
- L1 = Basic (B) to B minus .0005
- H1 = B to B plus .0005
- H2 = B plus .0005 to B plus .0010
- H3 = B plus.0010 to B plus .0015
- H4 = B plus .0015 to B plus .0020
- H5 = B plus .0020 to B plus .0025
- H6 = B plus .0025 to B plus .0030
Note: You can find these limits in G-Wizard’s thread database as well.
Choosing Thread Taps
When you’re choosing which thread tap to use, there are four main factors to think about so you can up your chances of success:
Workpiece material: Various materials have different levels of firmness and there will be a tap suitable for each level. Some will work better than others on different materials, i.e., a machine tap works well on harder materials, but a fluteless tap is best for soft materials.
Tap material: You’ll have to choose this according to the material of the piece you want to work on, e.g., carbide steel taps can cut threads quickly, and are strong enough to handle hard materials like cast iron.
Hole type: Depending on what hole you need to make, there will be a tap up to the task. Taps with 1–3 thread chamfers can create deeper holes, for instance.
Cutting speed: Some taps, i.e., spiral flute, are designed for high-speed work, while others not so much, so you’ll have to know the speed of cutting before choosing your taps.
How Xometry Can Help
At Xometry, our global manufacturing network has experience with a wide variety of taps and cutting tools to create threads in parts. We cover everything from standard unified national and metric threads to fine-pitch optical threads and even custom thread forms. If you have custom parts that need threading, we can make them! Get started by uploading your design files to the Xometry Instant Quoting Engine® and get an instant quote today!
Disclaimer
The content appearing on this webpage is for informational purposes only. Xometry makes no representation or warranty of any kind, be it expressed or implied, as to the accuracy, completeness, or validity of the information. Any performance parameters, geometric tolerances, specific design features, quality and types of materials, or processes should not be inferred to represent what will be delivered by third-party suppliers or manufacturers through Xometry’s network. Buyers seeking quotes for parts are responsible for defining the specific requirements for those parts. Please refer to our terms and conditions for more information.
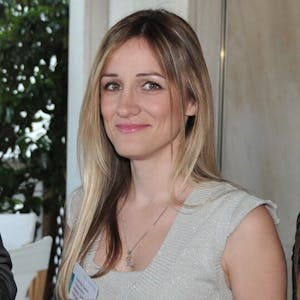