No doubt you’ve encountered a variety of drilling machines for different applications. There is a surprising variety of forms, sizes and complexities of such devices, so we offer here a review of the key types and how you might use them. From handheld drills to multi-head turret drills, each type has its own particular quirks, advantages, disadvantages, and use-cases.
This article is a way for us to share our experience with making holes in different ways, using a range of machines, from simple to more exotic, found across our shops. We hope it’s useful to you to help sort out the complexities of what can be a pretty simple process!
Let’s Begin - What Is a Drilling Machine?
You probably already know that a drilling machine is used to make holes. The machine's purpose is to hold a drill bit or other form of cutter rigidly and traverse it along the spindle axis to cut the required holes. In reality, some machines move the workpiece rather than the cutter, while others can move both as required.
A drilling machine's speed is necessarily adjustable, to suit the type of cutter, the material being worked, and the precision/surface quality needed in the hole. The feed or plunge rate into the workpiece can be altered either manually or automatically, depending on the complexity of the machine you’re using.
Drilling machines can be mounted directly to a concrete floor or a work table, or they can even be portable or for freehand use. We have seen it done in multiple ways. Figure 1 below is a diagram of a fairly typical simple drill press, with a manually positioned workpiece you locate and restrain by hand or by clamping it in a vice, which may or may not be itself clamped to the table:
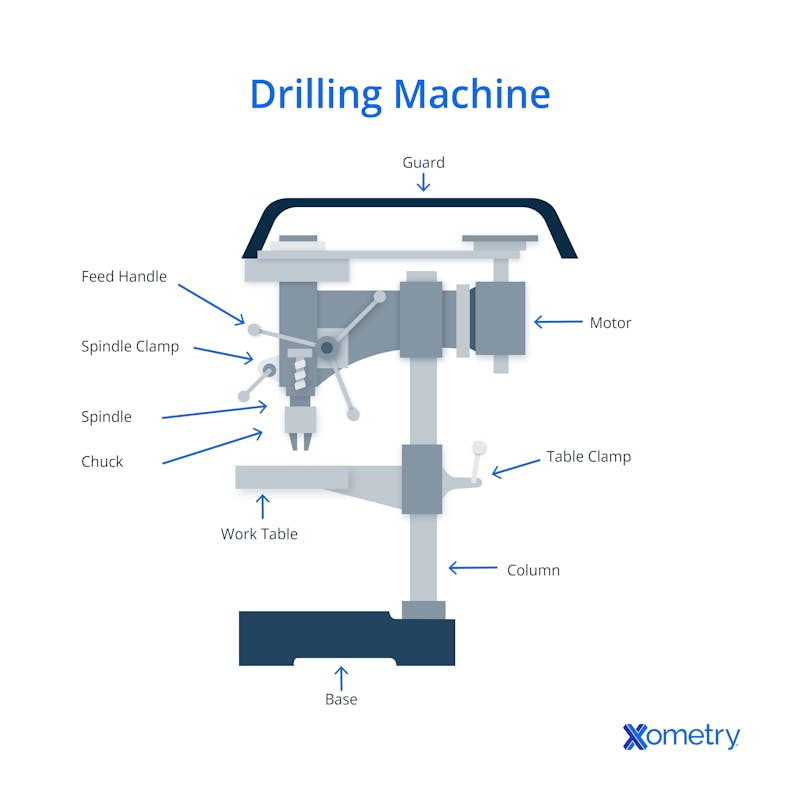
The Uses of a Drilling Machine
You can use a typical drilling machine for cutting blind holes (part way) or through-holes in almost any material — from popular metals we offer such as titanium, steel, and aluminum to machinable ceramics and engineering plastics like ULTEM; jobbing drills can handle it all. These devices come in all sizes and types and are generally flexible and highly amenable to most drilling operations and hole types:
- Drilling: When you need a simple, not too large or small parallel sided hole in a workpiece, that requires a basic drilling operation.
- Reaming: When you need that parallel sided hole to be of a precise diameter and roundness. For example, so you can make a running fit for a shaft, then a reamer is needed. It’s a specialist and precise drill with many flutes (cutters) that is intended for very shallow finish cutting.
- Countersinking: Often the corner at the throat of the hole needs to be either broken with a slight bevel or opened to a taper that allows for a fastener head or similar to be accommodated. This uses a heavily tapered drill called a countersink - you can get these in a variety of angles to suit your needs.
- Tapping: With a nice round hole drilled, it’s often the case that we will need to cut a thread into the wall of the bore. This is done using a specialist drill called a tap that has vertical (hand tap) or spiral (machine tap) flutes and the male thread cut on it. The flutes make many cutting edges and clear away the debris, a tapered start allows you to engage the tap with less struggle and error.
- Boring: We don’t like to be “bored,” but a hole often needs to be expanded. This is typically because a big drill is not very good at cutting at its tip, so stepping up through several boring stages will allow you an easier and more accurate process.
- Counterboring: Very often a hole needs to step in diameter, to accommodate fasteners with shouldered heads (as opposed to countersinks). This requires a partially drilled hole using a counterbore drill, which locates in the original hole and then cuts with a diameter step. Counterbores are usually 90° shoulders but they can be sloped, if required.
Need parts with drilled holes?
How a Drilling Machine Works
Drilling machines typically use an electric motor connected to a spindle to rotate a cylindrical cutting tool on its axis and drives the tool’s sharp end into a workpiece, often with considerable force, and hopefully with good accuracy in position and entry angle. The ability for drilling machines to quickly and precisely drill holes with minimal setup time is in large part what makes them useful to have around.
It’s important that the workpiece be securely held in place on the machine table, because if it gets free it will spin with a lot of speed and can cause serious damage. How the workpiece is retained varies widely, from ad-hoc clamping to high quality X-Y moved vices and work chucks, which some models include.
Generally, drilling machines are oriented with the spindle vertical, but some are constructed to drill horizontally. In many cases, the angle to the quill (the axis drive of the spindle) can be adjusted and locked, to drill holes that are non-perpendicular to the table. This reorientation greatly increases the applicability of a drilling machine to more varied tasks.
Parts of a Drilling Machine
1. Base
A fixed machine needs a platform for floor or bench mounting, so it can be attached to a heavy or fixed surface that stops it from wandering. In many drilling machines this is a heavy, iron casting that lends stability and spreads out the load to the machine, and is rigid and vertical - even if its drilling axis is horizontal.
2. Column
A column is simply a post, a stem, or a pillar. It connects the business end you use to the base of the machine. Depending on the quality of the machine, there are many formats, from massive and rigid to just strong enough.
3. Radial Arm
Larger machines often have a swing arm that allows the quill/spindle to move on an arc, allowing a greater range of area to be addressed without you moving the workpiece. These devices offer great flexibility in hand operation and can be adapted to CNC.
4. Drill Head
The drill head generally consists of the spindle motor, the chuck, and methods for clamping the head in position. In many cases, the motor is remote (behind) the drill head and connects to the spindle via a belt drive gearbox.
5. Worktable
The work table of a typical drill machine is a cast iron platform that includes clamping methods such as T slots or a grid of holes for locating clamps. It has a flat surface onto which workpieces and machine/hand vices can be placed/clamped.
6. Feed Mechanism
The feed mechanism, or quill of a drill machine, is a spindle-axis motion that allows the drill bit to traverse along its axis and apply the necessary load at the cutting edges to progress the drilling. You’ll find many forms of mechanism that fit this purpose, from CNC axis slides to simple hand levers. Sometimes, the motor moves to enable this motion, but more often, there is a linear slide capability between the drill chuck and the drive point.
7. Spindle
The spindle connects the drive application point or the motor itself, if it is drill-coaxial, to the drill chuck that holds the cutters. It is key to machine performance in precision and repeatability that this mechanism has no runout (axial slack) or misalignment (axial wobble).
8. Chuck
The chuck is a mechanism used to grip the tool tightly enough to stop it from slipping during drilling operations. A drill chuck typically has three jaws that move together to accommodate varied drill bit diameters. These devices are often key operated but in better quality equipment their outside is knurled and the drive applied to the jaws is at a high gear ratio, so hand operation will grip the drill sufficiently.
9. Electric Motor
The electric motor drives the spindle either directly with an axial - often epicyclic (planetary) gearbox or with a series of belts and stepped pulleys. The gearbox, of whatever type, allows for a wide range of speed settings to suit drills from the smallest practical (⌀1mm in some machines, smaller in the most precise equipment) to the largest the chuck can hold. You’ll find that many drills need to have very low minimum speeds at the spindle, to allow for highly controlled tapping. In some cases of more modern and costly equipment, a variable speed drive (VSD) motor speed controller is installed.
Types of Drilling Machines
You have no doubt experienced many different forms of drilling machines, some of which are basic workshop devices and others that serve narrow and specific applications.
1. CNC Drilling Machine
A CNC (Computer Numerical Control) drilling machine is mechanically similar to a standard drilling machine. However, its axes of workpiece and drill positioning are driven by computer-instructed motors with either open or closed loop control to deliver high precision and repeatable execution of software commands, known as G-code.
2. Sensitive Drilling Machine
A sensitive drilling machine is a type of drill press typically used for low-volume drilling of smaller diameter holes. The quill feed of these machines is manually controlled by operating a hand lever that executes the drilling. They’re called "sensitive drilling machines" because a skilled operator is able to feel the cutting process of the work under the drill, allowing highly sensitive adjustment of speed and pressure and awareness of the drill bit losing its edge. If you’ve used one of these before, you’ll know exactly what we mean. Although more basic than some of the other types of drilling machines we’ll cover, they are found in most machine shops, including our own, since they are inexpensive, reliable, and simple to operate.
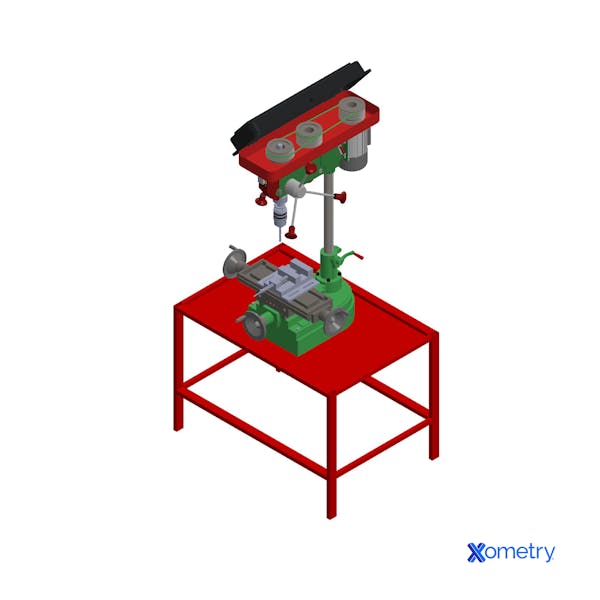
Figure 2: A typical sensitive manual drilling machine with X-Y transport for precise drill placement
3. Radial Drilling Machine
A radial drilling machine has its spindle mounted on an arm that can be radially swung (and locked) around the column while also allowing the drill head, spindle, and feed mechanism to move along the length of the arm. This machine allows us to drill in a wider area of locations without having to reposition the workpiece.
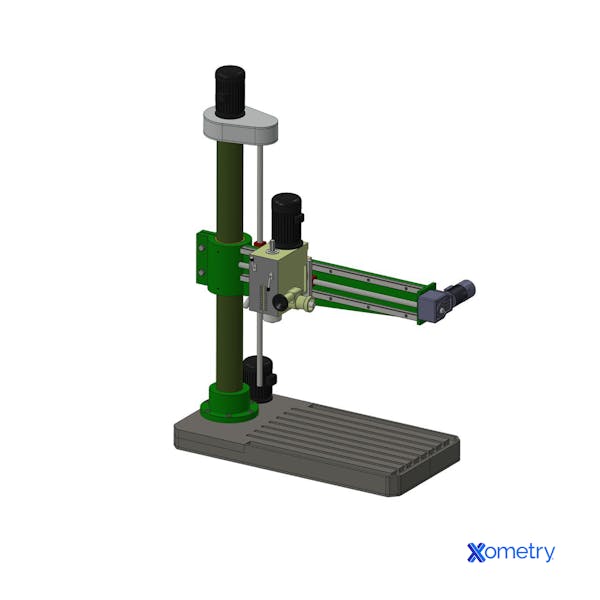
Figure 3: Radial arm drill machine that can set the spindle position on a polar coordinate system — this example is CNC controlled
4. Upright Drilling Machine
An upright drilling machine is similar in construction to a sensitive drilling machine but is more robust. It typically has a power feed that automatically plunges the tool into the workpiece. Upright drilling machines are better suited to heavy-duty applications.
5. Gang Drilling Machine
A gang drilling machine has multiple independent columns, each with its own drive and spindle mounted to a shared base. These machines are typically used when multiple successive operations must be performed, for example, drilling and then tapping. A multi-spindle drill on the other hand is typically designed to drill multiple holes at once.
6. Deep-Hole Drilling Machine
Deep-hole drilling machines are typically used to drill holes with at most a 20:1 diameter to depth ratio. Deep-hole drilling machines are usually oriented horizontally to allow for larger workpieces to lay on their sides and require high-pressure coolant to be pumped to the cutting interface to flush chips away from the hole.
7. Multiple-Spindle Drilling Machine
Multiple-spindle drills are made in many forms and as add-ons to more general machines, to perform the drilling of multiple holes into a single workpiece in one operation. These machines are typically dedicated to a product/operation and serve in mass production.
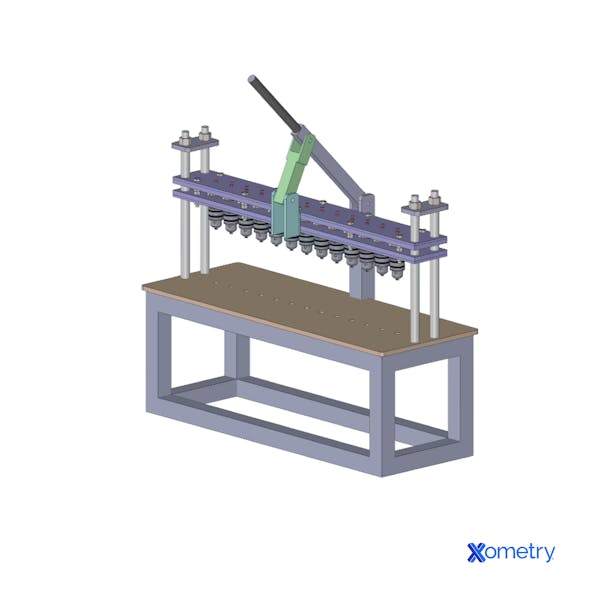
Figure 4: A gang drill for executing on a multiple hole operation
8. Portable Drilling Machine
Portable drilling machines range from small battery-operated hand drills to larger and more industrial devices, even being wheel-mounted and requiring multiple operators.
9. Micro Drill Press
A micro drill press is simply a miniaturized version of a typical workshop drill process, for making very small holes using drills that can be as small as 0.5mm, if you have the patience and skills not to snap them nearly instantly! In reality, it is increasingly common to drill such micro-holes using EDM or laser drilling, to allow greater precision and to deliver holes that are too small to see.
10. Turret-Type Drilling Machine
A turret drill is a machine that can be set up to perform multiple drilling, reaming and tapping operations without cumbersome tool changes. These turret structures can rotate in the horizontal or vertical plane and in more advanced equipment, the angle of presentation of the drill bits can be set over a wide range. The multiple tools are placed in chucks fitted to a turret that can be indexed to precisely position each of the drill bits into the same machine position. In this way a pilot hole, then a bored larger hole, then a reamer can all be operated in the same axial position, in a sequence to allow a complex hole to be completed in one setup.
Summary
In this article, we reviewed the parts, types, and different uses of drilling machines.
Here at Xometry, we provide a wide range of manufacturing capabilities, including CNC machining (including drilling) and other value-added services for all of your prototyping and production needs. You can get an instant quote on CNC machining and a whole lot more here at www.xometry.com. Try us out today!
Disclaimer
The content appearing on this webpage is for informational purposes only. Xometry makes no representation or warranty of any kind, be it expressed or implied, as to the accuracy, completeness, or validity of the information. Any performance parameters, geometric tolerances, specific design features, quality and types of materials, or processes should not be inferred to represent what will be delivered by third-party suppliers or manufacturers through Xometry’s network. Buyers seeking quotes for parts are responsible for defining the specific requirements for those parts. Please refer to our terms and conditions for more information.
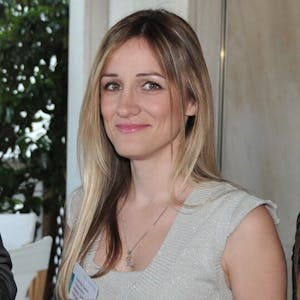