Anodizing colors into metals is an effective way of actually improving the overall quality of the material, as well as making it look pretty. Hard anodization helps refine aluminum alloys, as well as other metals functionally. The anodic layer—otherwise known as the aluminum oxide coating—that gets created in the process encases the metal and keeps it protected over time. We’re going to discuss how the process is done and what methods are available.
What is Hard Coat Anodizing?
Also known as Type III, hard coat anodizing is a kind of electrochemical process that gives aluminum (and other non-ferrous metals) a protective oxide film or layer. Aside from keeping the metal safe, it’s also used to create decorative finishes and make products like jewelry and metal household parts look nicer.
During the process of electrolysis, certain conditions have to be in place for it to work. For example, the temperature of the bath that the metal gets submerged in needs to be between 28°F and 32°F, and the DC voltage applied should start at a low value (around 25V) and gradually increase to a higher value (between 60–100V). If the process is executed properly, you should get a surface hardness upwards of 60 Rockwell C. Parts that are anodized can become extremely durable and have fantastic corrosion resistance in addition to a beautiful array of colors, as shown in the picture below.
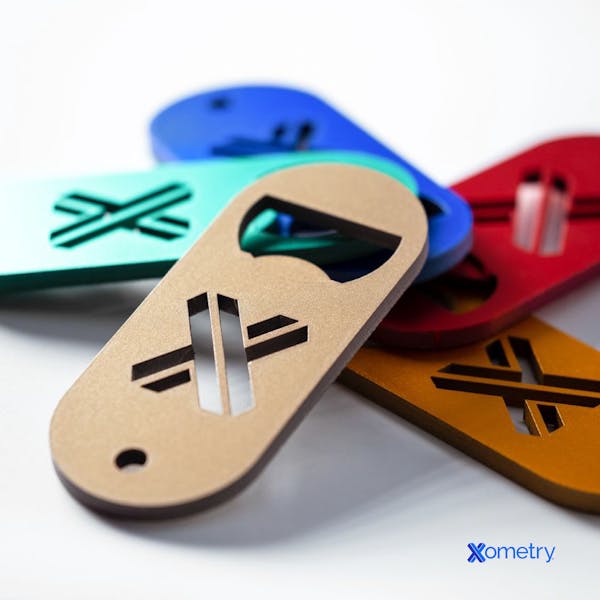
How it Works
The first step in this process is to clean the aluminum (or whichever type of metal you’re using) in a sodium hydroxide solution, also known as lye. This solution must be diluted in distilled water. Usually, mixing three tablespoons of lye in half a gallon of distilled water works well. Aluminum will have a natural oxide layer already on it that needs to be removed.
The metal is then connected to an electrical circuit with the electrolyte—usually a 50/50 mix of water and sulfuric acid—and put into the solution for 45 minutes (ish). The anodized metal is then removed from the sulfuric acid bath (in a well-ventilated area), immersed in a hot dye for 15 minutes, and coated with a chemical sealant when removed.
Anodizing Types
As well as Type III anodizing, there are also types I and II. The table below explains their main differences.
Type | Electrolyte | Color Range | Characteristics | Applications |
---|---|---|---|---|
Type Type I | Electrolyte Chromic acid | Color Range Limited (e.g., gray, black) | Characteristics Thin, non-conductive oxide layer, better adhesion before painting, fatigue strength, structural integrity of base material | Applications Aerospace, military equipment requiring corrosion resistance |
Type Type II | Electrolyte Sulfuric acid | Color Range Gold, bronze, blue, green, red, silver, black | Characteristics Thicker layer, leaves a porous anodic finish, allows for more dye to be absorbed before sealing to retain color | Applications Consumer products, household fixtures, automotive parts |
Type Type III | Electrolyte Sulfuric acid | Color Range Darker tones (black, gray, deep colors) | Characteristics Thickest of the three, wear-resistant, suitable for harsher environments | Applications Industrial components, heavy machinery, outdoor equipment |
Anodizing Types
The image below shows a Xometry logo that has been anodized using the type II method:
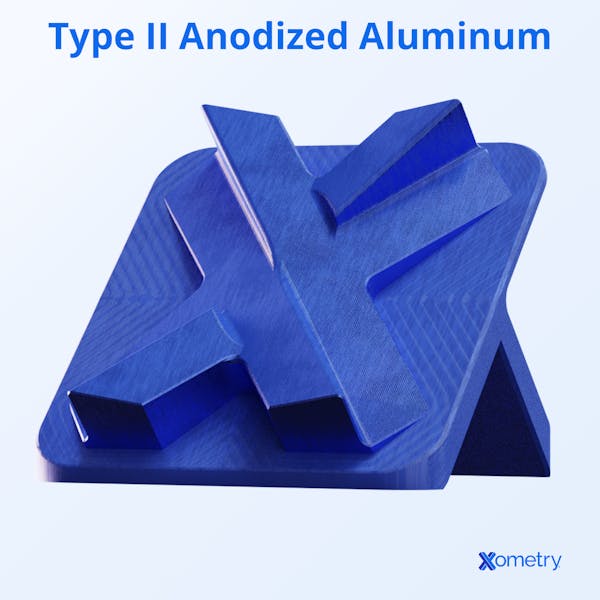
FAQs on Hard Anodizing Colors
What types of acids are used in the process?
Two main acids are used in this process depending on the anodizing type: sulfuric acid and chromic acid. Sulfuric acid, also known as "oil of vitriol," is the most common and highly effective method for color anodizing metals. It forms an oxide layer that not only coats the metal but also penetrates it. The thickness of this film falls between 0.0001” and 0.001” or 100 to 1000 microinches. Chromic acid (H₂CrO₄) produces quite a thin oxide layer, usually between 0.00002” and 0.0001” or 20 to 100 microinches. Despite its thinner profile, when properly sealed, it provides the same level of corrosion resistance as sulfuric acid.
How can I get better color consistency on anodized parts?
For your parts to have the same color after anodizing, don’t rely on pictures as these aren’t likely to exactly match the end result. Instead, ask the anodizing facility to send you a sample so you can see the shade up close. Also, have all the parts needing to be the same color anodized in the same batch. Sending your parts to the same processing facility will also help reduce the chance of color variations.
Can anodized metal colors fade over time?
Depending on whether they’re exposed to intense sunlight or harsh environmental conditions—ultimately, yes. You can reduce the risk of the colors fading, or at least the amount they fade, by sealing the metal after the anodizing process.
How Xometry Can Help
This article covered the basics of hard coat anodizing colors, so if you need any more specific information on this or related processes, please reach out to one of our representatives. We also have an anodizing service that could get your parts to you within a couple of days. Get started by requesting a free, no-obligation quote which will arrive in your inbox in two hours.
Disclaimer
The content appearing on this webpage is for informational purposes only. Xometry makes no representation or warranty of any kind, be it expressed or implied, as to the accuracy, completeness, or validity of the information. Any performance parameters, geometric tolerances, specific design features, quality and types of materials, or processes should not be inferred to represent what will be delivered by third-party suppliers or manufacturers through Xometry’s network. Buyers seeking quotes for parts are responsible for defining the specific requirements for those parts. Please refer to our terms and conditions for more information.
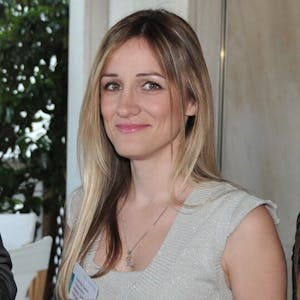