EDM (electrical discharge machining) is among the newer metal processing techniques, compared to rotating cutters, shearing, and forging. Rapidly pulsed high-voltage electrical discharges (sparks) are passed across the gap between the electrode and the grounded workpiece, removing material from the workpiece by erosion. Even the hardest and most intractable material can be cut and machined with very little bulk heating and virtually no application of macro forces, provided that the material is electrically conductive. This results in very low distortion and no addition of meaningful residual stresses to the workpiece.
The first EDM method, developed by Stark, Harding, and Beaver (and in parallel Lazarenko in the USSR), was hole-drilling EDM. Its earliest application was in the mid-1940s for the removal of sheared-off bolts and taps in high-value aluminum castings. Out of this relatively simple drilling method, the second branch of EDM processing developed: ram EDM or sinker discharge machining. This technique is essentially identical to EDM drilling, except that a complex form can be added to the end of the “drill” electrode. This process allows a finished, refined, and precise cavity-bottom shape to be formed in a single action. The third EDM type is wire-cut, which uses a straight wire electrode to cut a vertical or angled slot (slightly wider than the wire), as the wire is slowly fed through the cut to maintain ‘new’ electrode at all times.
This article will describe EDM machining, discuss the three main EDM methods, highlight important technical aspects of each, and identify applications that use each EDM method. It will also focus on practical applications, selection of the appropriate method, and the primary benefits of each method.
1. Wire Cut Electrical Discharge Machining
Wire cutting electrical discharge machining, commonly referred to as wire cut EDM, uses a wire as the “cutter” and erodes material by sparking between wire and workpiece. The wire electrode discharges along the whole length of a cut and feeds through, aiding the removal of cuttings. The technique developed as a way of performing 2D cuts (cuts that could only proceed along the x and y axes of a part, with the z-axis the thickness of the material) in hard materials, but it has grown in complexity. Offsetting the wire rollers from each other made cuts at a controlled angle to the z-axis possible. Later, it also became possible to add a rotational axis to the wire EDM process, resulting in highly capable 5-axis wire EDM centers.
This method can make start-free cuts. It is most commonly used for making extrusion tools and punch/die sets when combined with EDM drilling (to lace the electrode). Brass, zinc-coated brass, and zinc-diffused copper (stratified wire), running on sapphire or diamond guides are used as electrodes in the wire EDM process. Various conductivities, hardnesses, and tensile strengths of electrode wire offer different machining characteristics. For more information, see our guide on All About Wire EDM Machining.
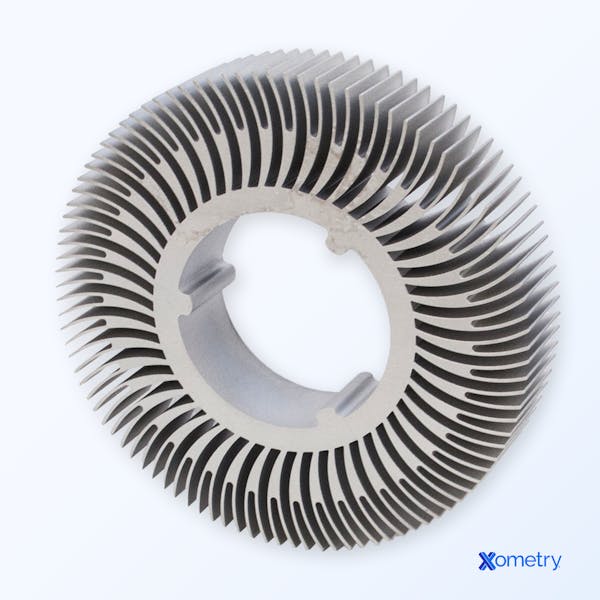
2. Sinker Discharge Machining
Sinker discharge machining (also known as "ram" or "cavity" EDM) uses discharge from an essentially 2D electrode. This 2D electrode can have a complex 3D-shaped end that is repeatedly plunged to arc erode into the work and raised a short distance on the Z axis to clear debris. This electrode can have any cross-sectional shape and a complex end form (without undercuts). For sinker discharge machining, precise copper and/or graphite electrodes are first machined to the desired cavity shape and then used to erode the shape into hard materials.
Ram EDM is widely employed in the injection molding and die-casting tool-making sectors. It is used to make nonmachinable complexity and finely detailed cavity features in molds without imposing any machining or impact stress on the mold. It also reduces the need for post-processing for surface quality improvement or hardening.
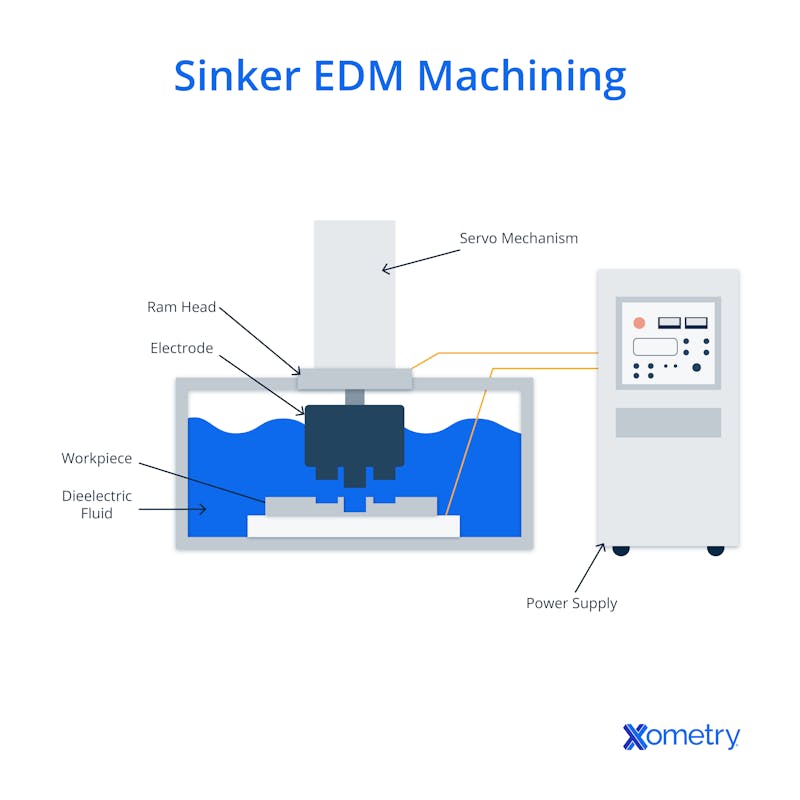
3. Hole Drilling Electric Discharge Machining
Hole drilling EDM was the earliest electrical discharge machining technique developed and remains a critically important tool in various fields, including the control of gas discharge in rocket engines/medical and scientific equipment and in opening cooling ways in gas turbine blades. Long straight small bore holes can only be cut by EDM drilling. A straight electrode is used to erode a hole that is a perfect reflection of the profile of the tool. It maintains precise dimensional accuracy along the entire length of the hole. This method allows for small diameter, high aspect ratio, straight holes of any depth, 0.0015” or larger in diameter. EDM drilling allows the drilling of both blind and through-holes, with smooth walls to be drilled in otherwise unworkable materials or to achieve difficult geometries. The as-machined surface finish of holes made by EDM is smooth enough to be used as bearing surfaces without additional processing steps.
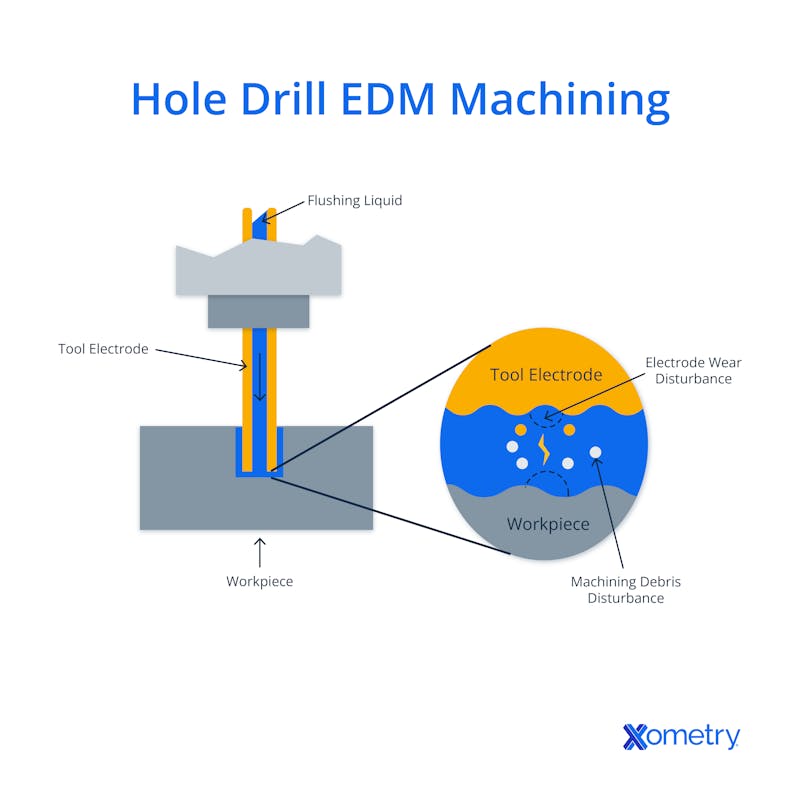
What Is EDM Machining?
EDM (electrical discharge machining) is a non-contact machining method used to cut nonmachinable complexity shapes and cavities in very hard, difficult-to-machine materials. With the workpiece and electrode submerged in a dielectric fluid (generally paraffin or kerosene), a high electrical potential at the electrode finds a path to ground through the workpiece. Each spark generates a localized temperature spike of up to 12,000 °C. This temperature melts/vaporizes some of the workpiece (and the electrode). Clearing cutting detritus is important to avoid short circuits, so drill and ram tools are Z cycled where the electrode feed of wire cut achieves the same.
The EDM machine process results in no imposed bulk stresses in the workpiece and only limited, highly localized heating. This results in macro stress-free machining. It also allows the cutting of very thin sections and fine features that would otherwise not survive mechanical cutter-based machining. This technique has revolutionized many aspects of toolmaking. It has eliminated design limitations imposed by the need for rotating cutters, allowing intricate features that are otherwise unattainable. For more information, see our guide on the Types of Machining Processes.
Which EDM Type Is Best for Creating Parts With Complex Cavities?
Sinker discharge machining is the best EDM type for creating parts with complex cavities. It allows for the complexity of cavities that are often required in plastic and die-cast component design. The limitations on the cavity shapes that can be produced with sinker discharge EDM do not have much impact on their value as mold-making tools. The "line of the draw" that prevents EDM from producing undercuts also applies to plastic molded and die-cast parts, which enter the tool cavity as a liquid but depart it as a solid
How Are EDM Machining Types Classified?
The various types of EDM are classified based on their operation and application. For example, wire EDM uses a linear-fed wire electrode to make essentially 2D cuts. The electrode wire rests on the diamond or sapphire guides, the dielectric fluid is deionized water, and electrodes are usually made of brass or zinc-coated brass.
Sinker discharge EDM, on the other hand, allows the use of complex electrode shapes to make equally complex cavities. The graphite or copper electrode is pre-machined into the required shape and then sunk by erosion into the workpiece, resulting in a hole that is the negative of the electrode’s shape.
Hole drilling EDM can deliver smaller and deeper holes than conventional drilling. This results in high precision in diameter and roundness, with excellent surface finish and no burrs. The electrodes can have complex cross-sectional shapes. Drill tools are generally pierced through with cooling galleries, so the dielectric is pumped through them to aid in clearing cuttings.
What Is the History of EDM Machining?
All spark erosion technologies owe their existence to work done by Joseph Priestly in 1770. He was the first to observe that electrical discharges left damage at the spark points. Years later, in 1943, Lazarenko and Lazarenko (husband and wife researchers) stumbled upon the notion of making a spark erosion machine for working with refractory materials for military manufacture. Their discovery led to the development of several spark erosion machines. This includes the NC wire cut machine by Charmilles SA in 1969, the CNC wire EDM machine in 1972 by Seibu, and the primitive CNC wire EDM machine by Dulebohn in 1974.
What Is the Purpose of Using Electric Discharge Machining?
EDM is used as an alternative to conventional machining techniques for hard materials, specifically for machining refractory metals and hard-to-cut shapes. Wire EDM can achieve otherwise impossible tolerances in precision cutting, as can hole drilling EDM in terms of diameter and roundness. In general, EDM can maintain high precision and very low Ra levels (high-quality surface finish). This feature results in less post-processing, which often reduces costs on components that are otherwise very difficult to manufacture.
What Other Terms Are Used To Describe EDM Machining?
A lot of different terms are used to describe the various types of EDM including: spark machining, spark eroding/erosion, die sinking (or sinker discharge) EDM, cavity EDM, ram EDM, wire EDM, wire burning, wire erosion, and wire-cut EDM.
Common FAQs on the Types of EDM Machining
Where Is EDM Machining Used?
EDM (electric discharge machining) is used in making molds for plastic injection molding and metal die casting. It is also used to make complex cavities in pre-hardened materials. EDM is particularly useful for its ability to make precise and complex cavity shapes and perform very deep cuts. Aerospace, automobile, and electronics industries are also using EDM to make prototypes and production parts.
When Should You Use EDM Machining?
You can use EDM for several applications including: complex cavity shapes that are 3D relief shapes cut into the bottom face of essentially 2D blind cavities; extraction of precise 2D shapes from hard-to-work materials; thin sections which distort easily; and drilling fine and/or long holes in any metals. EDM imposes essentially no stress on the workpiece and can produce one-step drilled holes of any cross-section with an excellent surface finish.
What Materials Are Used in EDM Machining?
The materials most commonly processed using the EDM process are those that are hard to work by other means, such as: tungsten, molybdenum, and hardened tool steels. Materials that display extreme work hardening during mechanical machinings, such as titanium and austenitic stainless steels, are also good candidates for EDM. These materials become progressively harder to cut during the course of machining because they harden while being machined. This hardening often diminishes part feature accuracy.
Summary
How Xometry Can Help
Xometry provides a wide range of manufacturing capabilities including CNC machining, 3D printing, injection molding, laser cutting, and sheet metal fabrication. Get your instant quote today.
Disclaimer
The content appearing on this webpage is for informational purposes only. Xometry makes no representation or warranty of any kind, be it expressed or implied, as to the accuracy, completeness, or validity of the information. Any performance parameters, geometric tolerances, specific design features, quality and types of materials, or processes should not be inferred to represent what will be delivered by third-party suppliers or manufacturers through Xometry’s network. Buyers seeking quotes for parts are responsible for defining the specific requirements for those parts. Please refer to our terms and conditions for more information.
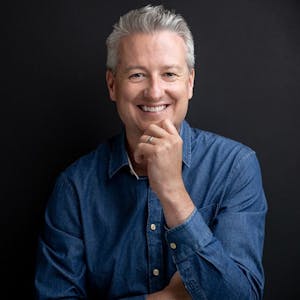