If you’ve been curious about the different avenues you can take for machining projects, you’ve come to the right place. We’re fans (and experts) here at Xometry when it comes to machining, and there are numerous approaches to choose between—nine of which we’ll take a closer look at, from milling and grinding to broaching and electro chemical machining.
1. Turning
First up to the plate is a type of machining that can make many different shapes thanks to a lathe that rotates your material while a cutting tool shapes it, removing excess bits. You can choose from many different lathes, like turret, engine, or special-purpose options, and the whole process can help you make a wide range of holes, grooves, threads, and tapers. This is why many manufacturers like to use it to make bats, camshafts, cue sticks, sign boards, musical instruments, and the list goes on. Originally, turning was a manual process, but nowadays the most common form is computer numerical control (CNC), pictured below, which can be programmed through code and left to run on its own.
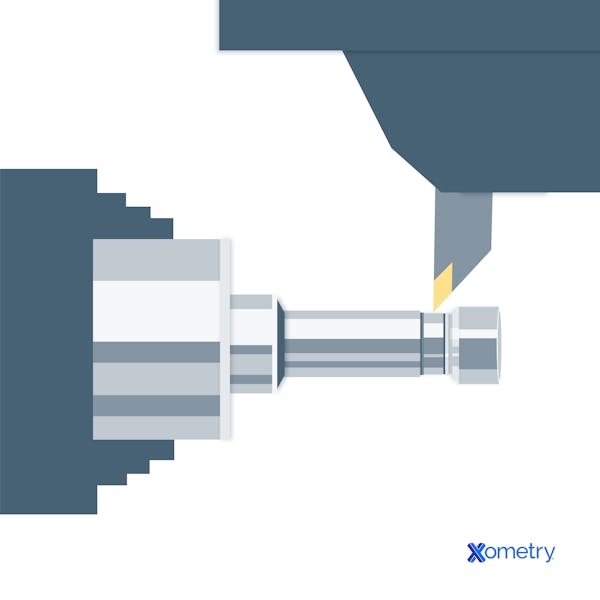
2. Drilling
With the help of several drill bits, drilling is a process that is ideal for creating holes in workpieces. The machine will push the drill bit toward the material you’re working on, giving it vertically aligned holes and allowing the waste material to drop off—some special machines can even drill in an angular fashion.
There are plenty of drill bits out there for specific applications, whether you need a shallow pilot hole (look to a spotting drill) or fewer chips (try a peck drill). There are also drills that can widen existing holes, such as a chucking reamer. This kind of machining process is used across the medical, construction, transportation, and electronic sectors.
3. End Milling
This is another machining technique that—like turning—removes material from a workpiece by using a multi-point cutting tool. In CNC milling, the cutting tool and workpiece will rotate in the same direction, but if you decide to go with manual milling, you’ll have the two pieces working in opposite directions.
There are different types of mills you’ll have available, like end, helical, and chamfer mills—which can be horizontally or vertically oriented and have several different axes, all of which will relate to what you’re aiming to machine. There is no shortage of mill machine types either, including hand, plain, universal, and omniversal types, and they’re ideal for making gears, cutting slots and grooves, or creating more complex shapes. You can see an example of an end mill in the illustration down below.
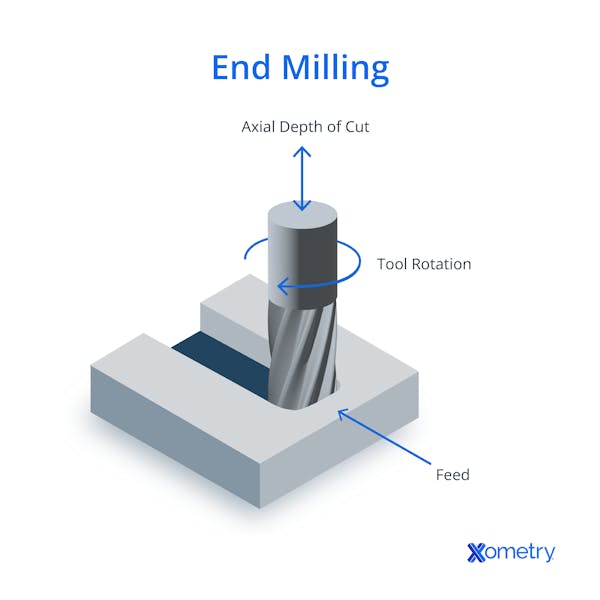
4. Grinding
To kick off the processing of a product, grinding is one form of machining you can turn to. It uses a wheel with an abrasive surface to smooth down your workpiece. This is a popular processing method, and it’s usually used for finishing products and getting their surfaces to an acceptable point before going through lapping, honing, and superfinishing.
Cylindrical grinding requires you to put your item in the center of the machine and it will rotate it while the outside of the wheel grinds it down. With centerless grinding, centering isn’t necessary, and it’s a better choice if you have a large quantity of items.
5. Planing
If you have large, flat surfaces you’re working with that’ll be processed further, planing is a great place to start. This method uses linear toolpaths to make cuts and carve off material with a cutting tool. Then, down the road you can send the workpiece off for things like scraping, once this is complete.
6. Sawing
If you’re looking for a way to create shorter lengths and cuts, sawing is it. There are tons of saws available, whether you need band saws that can slice through soft or hard materials, like band, hacksaw, and circular models. The speeds at which they can cut also vary, and it will depend on the material you have on hand. Sometimes 30 fpm is essential; other times, you’ll need a quicker clip of 1,000 fpm or more.
7. Broaching
In this kind of machining, you’re working with a tool called a broach, that’s essentially a cylindrical tool with teeth that are in increasingly larger sizes down the length of the tool. It cuts through material in two kinds of methods, push or pull. The former uses a vertical press-type machine, and the latter can use both a vertical and horizontal press-type machine to make square holes, keyways, spline holes, and more. These are usually backed by hydraulic power and, like saws, have a range of speeds, from as low as 5 fpm to as high as 50 fpm, depending on the metal or material you’re broaching.
8. Electric Discharge Machining
Also called EDM, for short, electric discharge machining releases electric discharges that create tiny craters into the surface of your workpiece. The quick succession of these fiery arcs leads to complete cuts (and gives it its other nickname, spark machining).
It’s a nice option if you need to create complex geometrical shapes, especially when you’re working with harder materials or designs that require close tolerances. One limiting factor is that the material needs to have electrical conductivity. However, they’re perfect if you need small, highly detailed parts that other kinds of machining wouldn’t be able to handle. You can see the science behind the technology of an EDM machine in the following illustration.
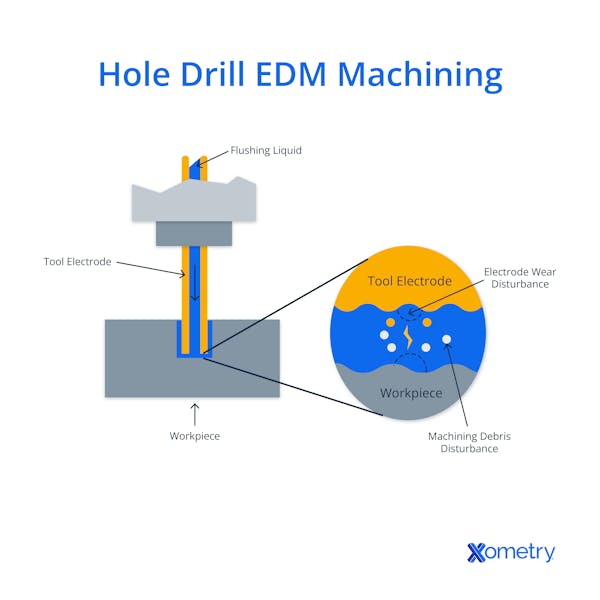
9. Electro Chemical Machining
This is another style of machining that uses electricity to make cuts—more specifically, holes. You’d want to opt for this when you’re set on creating a smooth, aesthetically pleasing surface finish, free of flaws. This happens through reverse electroplating (and it’s capable of cutting unique shapes and angles that other machines can’t. It’s a cold machining process, and it’s suitable for harder and less common metals like cobalt, rhenium, and other alloys.
Machining Processes—Recap
So, which one of these is best for your projects? The below table should be able to help you decide.
Machining Process | Type | Machinery Used | Applications and Industries | What It Can Make |
---|---|---|---|---|
Machining Process Turning | Type Material removal | Machinery Used Lathes (turret, engine, CNC, etc.) | Applications and Industries Automotive, sports, furniture, musical instruments | What It Can Make Shafts, grooves, threads, tapers, bats, camshafts, cue sticks, signboards, and more |
Machining Process Drilling | Type Material removal | Machinery Used Drill presses, CNC drills | Applications and Industries Medical, construction, transportation, electronics | What It Can Make Holes (pilot holes, angular holes, reamed holes) |
Machining Process End milling | Type Material removal | Machinery Used Milling machines (CNC/manual, horizontal/vertical) | Applications and Industries Manufacturing, automotive, aerospace | What It Can Make Gears, slots, grooves, complex shapes |
Machining Process Grinding | Type Material finishing | Machinery Used Grinding machines (cylindrical, centerless) | Applications and Industries Manufacturing, toolmaking, metal finishing | What It Can Make Smooth surfaces, prepped surfaces for lapping or honing |
Machining Process Planing | Type Material removal | Machinery Used Planing machines | Applications and Industries Heavy equipment manufacturing, construction | What It Can Make Flat surfaces for further processing, large panels |
Machining Process Sawing | Type Material cutting | Machinery Used Saws (band, hacksaw, circular, etc.) | Applications and Industries Construction, manufacturing, woodworking | What It Can Make Shorter lengths of material, custom-sized components |
Machining Process Broaching | Type Material cutting | Machinery Used Broaching machines (hydraulic press-type) | Applications and Industries Automotive, aerospace, manufacturing | What It Can Make Square holes, keyways, spline holes |
Machining Process EDM | Type Precision machining | Machinery Used EDM machines | Applications and Industries Aerospace, medical, toolmaking | What It Can Make Complex geometrical shapes, detailed parts, hard materials |
Machining Process ECM | Type Precision machining | Machinery Used ECM machines | Applications and Industries Aerospace, medical, exotic metalworking | What It Can Make Smooth surfaces, unique shapes, high precision cuts |
Machining Processes Recap
What materials can be machined?
Oh so many! Metals like steel, aluminum, and titanium are often machines, as well as plastics and composites. You can also machine ceramics and exotic alloys with some of the processes listed above.
How do I choose the right process?
This will depend on the material you want to use, how complex your design is, and how precise you need it to be. So, for cylindrical shapes, for instance, you’d go for turning, but for more intricate designs and shapes on harder materials, EDM is best.
What’s the difference between CNC and manual machining?
As briefly covered above, CNC uses programmed software to move the tool automatically, but manual machining will need a human operator to do this. CNC can offer more precision and can work for a lot longer without getting fatigued, making it ideal for bulk production.
How Xometry Can Help
As a customer of ours, you get to choose from a long list of services, including machining for different materials. You can get a free quote for rapid machining, Swiss machining, phenolic machining, and more on our website.
Disclaimer
The content appearing on this webpage is for informational purposes only. Xometry makes no representation or warranty of any kind, be it expressed or implied, as to the accuracy, completeness, or validity of the information. Any performance parameters, geometric tolerances, specific design features, quality and types of materials, or processes should not be inferred to represent what will be delivered by third-party suppliers or manufacturers through Xometry’s network. Buyers seeking quotes for parts are responsible for defining the specific requirements for those parts. Please refer to our terms and conditions for more information.
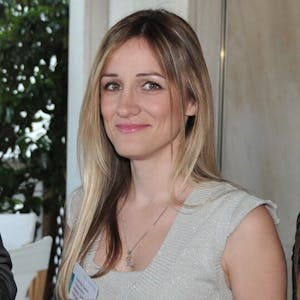