Wire electrical discharge machining, better known as wire EDM, is a very precise manufacturing process that has become an industry staple, particularly in aerospace, automotive, and medical. So, what exactly is it, how does it work, and what are its drawbacks? Let’s find out.
What is Wire EDM?
Wire EDM uses electrical discharges to erode and ultimately cut through materials. A wire electrode is continuously fed under tension on a vertical axis. Through it, a discharge voltage is applied and it crosses via a dielectric liquid and then hits the workpiece, which actually moves from side to side as the machine cuts to trace out the shape that’s needed. The erosion can either start from the outer edges, or a hole can be drilled first and used as a starting point for the rest of the cut. Here are some of its advantages:
- Easy to achieve high-quality surface finish
- Doesn’t need much post-processing
- Can work with all conductive materials of any hardness or brittleness
- Has extreme tolerances
- Feature accuracy close to 10 millionths of an inch
- General tolerance of around 40 millionths of an inch
- Low distortion (practically zero—no bulk heating, tearing, fracture, or impact)
- Unlimited feature complexity for 2D parts (the wire can move around infinitely) — although limited 3D complexity in 5-axis production
- Safe operation, despite high voltages
A Brief History
The first form of wire EDM was developed by engineers in the Soviet Union in 1943. This was a basic yet extremely precise machine that was able to erode materials otherwise hard to work with (i.e., tungsten). The machine used discharges from a simple resistor-capacitor network. Over the next 20 years, several people worked hard at refining the technology and creating upgraded versions.
Around the same time, engineers in the US were developing a spark-erosion machine designed to remove broken bolts and taps from aluminum castings. That machine could only arc at around 60 discharges per second. As it continued evolving and eventually vacuum tube pulse generation was used, it was able to make several thousand arcs per second.
After experimenting with punch-card-driven mills converted into wire eroders, the Soviet Union developed the first successful wire EDM machine in 1967. By the 1980s, these machines could operate at 64 mm²/min, making them a very practical way of machining through tough materials.
How it Works
This entire process usually takes place in an electrolyte bath of paraffin or deionized water, which acts as a kind of coolant and semiconductor. It’s also a great way of flushing out any debris because that can prove to be a bit of a pain when cutting. When Wire EDM machines first became available on the market, they were more like arc bandsaws or generic EDM cutters, focusing on complex 2D shapes. They’ve since developed into more complicated machines, with many 5-axis machines capable of cutting very intricate shapes.
Wire EDM is especially useful when processing hard materials from raw to finished form in one step. Among its many advantages, which we’ll consider later on, is the fact that this procedure works well with pre-hardened tool steels, which are usually quite difficult to machine because of internal stresses and distortion. Aside from all the good things, there are a few potential drawbacks, too. For instance, it doesn’t work with plastics, composites, and non-conductive natural materials. It’s also rather slow, which results in parts usually being pricier than other methods, and consumables can work out quite expensive, too, as the wire can’t be reused. The following image shows an example of a part made using this technique:
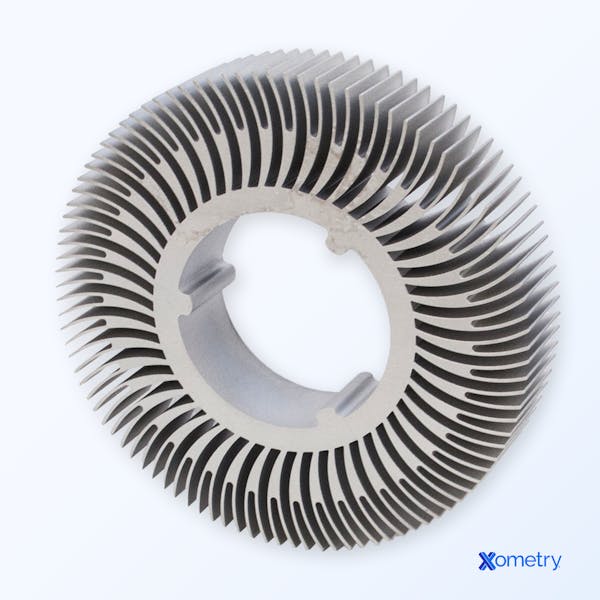
The way this technique works, namely that the workpiece is moved around while the machine cuts it, allows it to be extremely precise, in fact, no other CNC method comes close. The spark gap where the arc forms is usually very small, but under no circumstances does the wire actually touch the workpiece.
The Wire
There isn’t necessarily a one-wire-fits-all. They come in different grades, and they usually include copper, brass, tungsten, molybdenum, coated (zinc-coated and diffusion-annealed), and steel-core. As the wire is basically considered the cutting tool, the type you use will have an effect on the overall performance. Once each wire is used, it practically becomes useless and has to be thrown away because it breaks down. You can typically find wire sold based on its weight and classification.
Frequently Asked Questions on Wire EDM
Is this procedure known by any other names?
As a matter of fact, yes. Wire EDM has lots of different names, which can be a little confusing. Some refer to it as spark erosion, spark eroding, wire erosion, wire burning, wire cutting, or die sinking.
What specific examples of materials can it cut?
Basically, it can cut all metals. It’s better suited for pre-hardened die steels, titanium, austenitic stainless steels, tungsten, and molybdenum. Although it can cut them, it’s not the best or most cost-effective way of cutting soft materials like copper, bronze, brass, or non-hardened steel, all of which can be worked on with cheaper machines and methods. If you want to manufacture a part in one stage or without the addition of heat, EDM may be the only option you have.
Wire cut EDM vs EDM—What’s the difference?
EDM is different in that it uses a shaped electrode made using conventional machining, usually made of copper or carbon, to cut complex partial 3D cavities. The process involves pulsing the electrode, which allows cooling and flushing, and how precise it is depends on how accurately it’s made. It’s a good way of making complex shapes in molds and die-casting tools and works great on pre-hardened materials, ultimately bringing the cost down and preventing potential tool distortion.
How Xometry Can Help
Machining your parts is more than possible at Xometry, and we have a long list of manufacturing services you can get instant quotes for depending on your needs, including CNC machining, laser cutting, 3D printing, and other related customized services. You can get your project off the ground today by requesting a free, no-obligation quote.
Disclaimer
The content appearing on this webpage is for informational purposes only. Xometry makes no representation or warranty of any kind, be it expressed or implied, as to the accuracy, completeness, or validity of the information. Any performance parameters, geometric tolerances, specific design features, quality and types of materials, or processes should not be inferred to represent what will be delivered by third-party suppliers or manufacturers through Xometry’s network. Buyers seeking quotes for parts are responsible for defining the specific requirements for those parts. Please refer to our terms and conditions for more information.
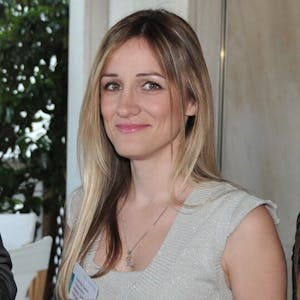