Grinding machines come in many types, from light and portable to large and precise. Each has unique applications, costs, and power ratings. Manually operated grinding machines are used for low-precision cutting, cleaning, sharpening, and polishing work while large CNC-operated precision grinders are used to create perfectly flat or cylindrical surfaces that meet tight tolerances. In all cases, grinding is a conventional process that uses mechanical force to slowly cut away material. Grinding machines can be used to create sharp cutting tools, flat cylinder heads, gear wheels, cutting tools, and much more. This article explores 19 types of grinding machines and examines how they work, how they differ, and how much they might cost you.
1. Angle Grinder
An angle grinder, also referred to as a side grinder, uses a grinding disc to cut, deburr, polish, and clean. Angle grinders are unique in that they’re portable, handheld devices. The electric motor is housed within the tool’s body or head and spins whichever attachment you affix to it. The most common attachments are grinding discs and wire wheels. The high-speed rotation of the grinding disc allows the toothless disc to cut through metal with ease. The grinding disc cuts via abrasion rather than shearing forces. Angle grinders can cut, polish, sand, and grind. Sanding and grinding functions are usually used to remove paint and rust or to deburr metal. Common commercial hand-held angle grinders have power ratings of 500 and 2000 W. Prices vary depending on the make, power rating, and battery type (if cordless). Prices can be as low as $30 or run up to $900.
2. Bench Grinder
A bench grinder is bolted to whatever surface the user chooses. It is typically mounted on a workbench — hence the name. It usually has two wheels: one coarse wheel for heavy-duty grinding and a finer wheel for polishing. This reduces the time spent changing wheels. A bench grinder works by spinning a grinding wheel at high speed to abrade anything it comes into contact with. Generally, bench grinders have three uses: sharpening cutting tools, shaping metal parts, and smoothing metal prior to welding. Bench grinders can come in different sizes but generally use 6-inch or 8-inch grinding wheels. Bench grinders usually have power ratings of between 500 and 3000 W and cost $50-$1000.
3. Die Grinder
A die grinder is a small, lightweight handheld grinder that’s usually operated with one hand. Die grinders are used for grinding, sanding, and polishing. They are usually used for fine detailing and light work. Air-powered die grinders are used for heavier work, and electric die grinders are used for the lightest work. Die grinders abrade material using an abrasive disc or other attachment on the spindle. They usually have a power rating of 500-1000 W and weigh 2-4 lbs. Die grinders cost between $24 and $600.
4. Hand Grinder
The term, “hand grinder,” applies to a broad category that includes all hand-held grinding tools such as angle grinders and die grinders. Hand grinders are sometimes also referred to as portable grinders as all hand grinders benefit from some degree of portability, depending on whether they are corded or cordless. They can be used for grinding, sanding, and polishing. Hand grinders are usually used for non-precision work, light jobs, and situations that demand portability. Nearly all of them accept different attachments like grinding discs, wire wheels, and disc sanders. The power output ranges between 500 and 2000 W and they cost $24-$1,000.
5. Belt Grinder
Belt grinders are similar to bench grinders in that they are fixed to a workstation. However, they use a gritted belt rather than an abrasive disc. The belt moves at high speeds to abrade the surface of any item it contacts. Belt grinding can be used for shaping, sanding, deburring, and polishing. These devices are similar in size to bench grinders and are classified by belt sizes such as 1 x 30 (1 inch in width and 30 inches in length), or 2 x 72 (2 inches in width and 72 inches long). Belt grinders come in power ratings of 500-3000 W, and cost between $60 and $4,800.
6. Pedestal Grinder
A pedestal grinder is the same machine as a bench grinder, except it’s mounted to its own dedicated pedestal as opposed to a workbench. Pedestal grinders use abrasive discs to grind materials and usually have a fine and coarse grit disc attached at any one time. The machines can be used for grinding, shaping, cleaning, deburring, and polishing. They usually fit either 6- or 8-inch discs, are rated at 500-3000 W, and cost between $120 and $5,000. Pedestal grinder prices vary depending on the power rating, quality, and whether they come with the pedestal or if it is sold separately.
7. Bore Grinder
Bore grinding, which is also known as internal grinding, inside diameter grinding, or inner diameter grinding, is a process used to precisely grind the inner circumference of a cylindrical and tapered workpiece. The workpiece is centered in a chuck which rotates the part at high speed, the grinding cylinder is then spun in the opposite direction and engaged with the inner surface of the workpiece. Depending on the make, size, and power of the bore grinding machine, machines can cost between $8,000 - +$100,000.
8. Precision Grinder
“Precision grinder” is a group term used to describe machines that abrade material from a part with a very high precision. There are a number of grinding methods within precision grinding, including: cylindrical grinding, surface grinding, jig grinding, creep fatigue grinding, and centerless grinding.
Since precision grinding is a category rather than a specific type, the machines used vary greatly in power and price. Similarly, the power ratings range from 500 to 24,000 W and they may cost as little as $1,000 or as much as $100,000. Precision grinding is not usually used for cutting or deburring but instead for shaping and polishing materials.
9. Universal Grinder
A universal grinding machine is a stationary machine that can be used for both cylindrical and flat-surface grinding. Every universal grinder has a stationary rotating wheel and a holding fixture that together gives it 6 degrees of freedom. Universal grinders have a range of applications, as the name suggests. However, a common use is for sharpening all types of cutting tools. Universal grinders vary greatly in size from small workbench sizes, as in Figure 8, to much larger stand-alone units. Universal grinders can have power ratings between 500 W and 20 kW and range in price between $1,000 and $40,000.
10. Jig Grinder
A jig grinder is a precision grinder for meeting fine tolerances and high-quality surface finishes on parts with complex geometries. A jig grinder uses a grinding tool on the end of an arm that has 3 degrees of freedom to grind circular, linear, and complex geometries in multiple locations. Price will vary depending on make and model but you can expect them to cost more than $5,000.
11. Gear Grinder
Gear grinders are used specifically for producing gears. Gear grinders cut the gear teeth to improve their dimensional tolerances and surface finish. It’s usually done through one of two methods. For method one, a grinding wheel in the shape of a worm gear is meshed with the wheel gear. As the worm gear rotates, it grinds the teeth of the wheel gear. The second method uses a large grinding disc that grinds between two tear teeth at a time. Gear grinders vary in price, power, and weight, depending on the make, model, and condition. As an example, a Reishauer NZA gear grinder runs at 9 kW and weighs a little over 10,000 lbs.
12. Surface Grinder
Surface grinders are used to abrade the surfaces of flat parts to improve their finishes and tolerances. Surface grinders use a stationary rotating abrasive wheel, which is fed to the workpiece using a moving bed. The surface grinder is one of the most common grinding machines in machine shops (other than angle and pedestal grinders). Some are configured with horizontal wheels while others have vertical wheels. Surface grinders can vary in price from $5,000-130,000.
13. Cylindrical Grinder
A cylindrical grinder, as the name suggests, grinds the surfaces of cylindrical objects that can be mounted on a central axis of rotation. Common targets include: cylinders, pistons, rods, bars, and tubes. There are different variations of cylindrical grinders but the most common works similarly to a lathe — the cylindrical workpiece is placed between a head and tailstock. The cylinder is then rotated and a grinding wheel rotates to oppose it. The grinding wheel can move in and out toward the axis as well as translate in the axial direction just like a lathe’s tool. As well as grinding the outside diameter, some cylindrical grinders can also perform inner-diameter grinding, centerless grinding, creep-feed grinding, and plunge grinding. Every cylindrical grinder is very different so price and size will vary. Prices start at approximately $7,000.
14. Flexible Grinder
A flexible grinder is a grinding disc that is powered by a long, flexible rotating shaft powered by a stationary electrical motor. Flexible grinders are used to cut, clean, deburr, and polish parts that are too large to be put into other grinding machines. The grinding wheel may be up to 9 inches in diameter and the motor provides up to 2,500 W of power. Flexible grinders have a more consistent power output, demand less maintenance, and sell for cheaper than universal grinders.
15. Tool and Cutter Grinder
A tool and cutter grinder is specifically made to sharpen cutting tools such as: drill bits, milling cutters, reamers, and blades. The machine uses a stationary grinding wheel and a moveable spindle which holds the cutting tool to be sharpened. Tool and cutter grinding can be either manually or CNC controlled, which will have a big impact on the price. Prices start at around $1,000 and can exceed $11,000.
16. Center Grinder
A center grinder is a machine that grinds cylindrical shapes that have uniform axes of rotation such as cylindrical bars. These machines cannot grind cylinders that don’t have central axes of rotation such as camshafts (they require something like a jig grinder). A center grinder is a form of cylindrical grinder and works the same way as many lathes. The part is placed between the head and tail stock and rotated. The grinding wheel is then rotated the opposite way and makes contact with the part to grind the surface. Center grinders start at $10,000 and may exceed $100,000. Their power draw can range from around 5,000 W to over 11,000 W.
17. Centerless Grinder
A centerless grinder is used to grind parts that have no set axes of rotation. The centerless grinder uses two wheels which both rotate in the same direction. One of the wheels will rotate in a stationary position (it is called the regulating wheel) and the other (the abrasive wheel) will not only rotate but also apply pressure to the part as it grinds. The workpiece is passed between the two grinding wheels so they can create a continuous diameter or a taper. Centerless grinders can exceed 30,000 W in power and cost as little as $6,000 or exceed $100,000.
18. Form Grinder
A form grinder is a machine that uses the geometry of the grinding surface to impart its specialized dimensions to the part being ground. One example of form grinding is gear grinding where the disc used to cut the teeth of the gear wheel is shaped with the exact dimensions of the final product. Form grinders can exceed $90,000 in price and 24,000 W in power.
19. Plunge-Cut Grinder
Plunge-cut grinding (also known as in-feed grinding) is similar to center grinding. Prices start at $10,000 and can exceed $80,000. This process grinds the outer surface of an object which is held between a head and tailstock. The difference is that while center grinding cuts an object with a uniform diameter, the plunge cut style only creates a uniform diameter in the portion where the grinding wheel contacts it.
What Is a Grinding Machine?
A grinding machine is a mechanical tool that’s equipped with an abrasive wheel intended to make shallow cuts on metals or other materials. With the right attachments, it’s also capable of polishing or putting other finishing touches on the workpiece. This type of operation is employed to improve the dimensional accuracy or appearance of a previously machined product. Grinding machines are used on workpieces that need highly precise forms, dimensions, or surface qualities. These machines remove relatively little metal — usually between 0.25 and 0.50 mm in depth. To learn more, see our Grinding Machine article.
How To Choose a Grinding Machine?
There are several factors to consider when buying a grinding machine. Firstly, you must decide what types of materials you’ll be processing. Certain grinders and grinding materials are better suited to some materials than others. Secondly, the machine specifications must be considered, including: the size of the grinding wheel, the input power needed to operate the machine, its frequency and colt rating, the type of control for the grinding head, the spindle orientation, its no-load speed, and the choice between a CNC-operated or hand-controlled grinding machine. All of these will inform your choice of grinding machine.
What Is the Most Popular Type of Grinding Machine?
Surface grinding machines are the most common style. This type works on either a horizontal or vertical axis and is used to produce either angular, flat, or irregular surfaces. It is popular because it is capable of refining and smoothing processes for a wide variety of metal and nonmetal materials and it’s relatively simple to use.
What Type of Grinding Machine Is Best for Beginners?
Typically, the most ideal type of grinding machine for beginners is the bench grinder. This grinding machine is a relatively simple workshop tool that does not require any experience or complicated operations on the part of the user. There are only a few major components and the machines are easy to understand. A bench grinder is an appliance used to sharpen tools and is a good choice for beginners.
What Is the Cheapest Type of Grinding Machine?
One of the cheapest types of grinding machines is the bore grinding machine. This is used to bore holes into wood, stone, and metal. It has a relatively simplistic design and is intended for private use. As such, it does not require intricate training or programming like some industrial grinding machines. Additionally, these machines are highly durable, so you’re unlikely to need to repair or replace them often. Finally, bore grinding machines consume small amounts of energy compared to most.
What Is the Most Expensive Type of Grinding Machine?
One of the most expensive types of grinding machines is the jig grinder. These devices have very small grinding heads in order to cut detailed features into their workpieces. However, extreme precision is expensive to create, calibrate, and operate. To achieve it, they are very complex and thus very expensive.
What Type of Grinding Machine is Good for Cutting Metal?
All types of grinding machines can be used to cut metal, but some types are better suited to certain material types than others. Belt grinding machines, for example, are specifically designed to shave metal from flat surfaces while gear cutting machines grind specific shapes deep into the part. The volume of metal that needs to be cut must be taken into consideration. For example, large-scale production requires a grinding machine such as the SMSB SGC 3000 that can grind 40 times more metal than many similar grinding machines. The size of the wheel is proportional to the size of the workpiece. However, all grinding machines are capable of cutting metal and can be used to remove material.
To learn more, see our guide on Metalloid Properties.
Can a Grinding Machine Be Used for Cutting Plastic?
Yes, grinding machines can be used for cutting plastics if outfitted properly. One of the most common reasons is to crush plastic waste into a usable form for recycling. Materials such as pipes, bottles, and plastic sheets are all examples of plastics that can be cut with grinding machines.
To learn more, see our article on What is Plastic.
What Are the Uses of Grinding Machines?
Grinding machines are primarily used to change the quality and physical appearance of a workpiece by altering its dimensions, shape, and/or surface. It is an operation that improves upon a previously machined product to achieve light cuts or fine finishes, such as sharpening the edges of blades. This method can be used on a variety of materials, such as: metal, wood, plastic, and stone. However, it is primarily performed on steel or iron.
Are Grinding Machines Dangerous?
Yes, grinding machines can be dangerous when used improperly or without adequate safety precautions. Their abrasive wheels operate at high speeds to cut through dense materials such as ceramic and metal. Contact with the wheel while in use could therefore easily damage human tissue. Additionally, the grinding action throws off tiny fragments of metal that can harm the eyes. Concrete, meanwhile, will release silica dust that can cause lung irritation and pulmonary diseases after long-term exposure. Proper PPE is critical.
Summary
This article presented types of grinding machines, explained each of them, and discussed when to use them best. To learn more about grinding, contact a Xometry representative.
Xometry provides a wide range of manufacturing capabilities, including machining and other value-added services for all of your prototyping and production needs. Visit our website to learn more or to request a free, no-obligation quote.
Disclaimer
The content appearing on this webpage is for informational purposes only. Xometry makes no representation or warranty of any kind, be it expressed or implied, as to the accuracy, completeness, or validity of the information. Any performance parameters, geometric tolerances, specific design features, quality and types of materials, or processes should not be inferred to represent what will be delivered by third-party suppliers or manufacturers through Xometry’s network. Buyers seeking quotes for parts are responsible for defining the specific requirements for those parts. Please refer to our terms and conditions for more information.
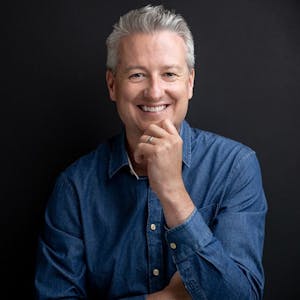