Computer numerical control machining—which more simply goes by CNC—is one type of subtractive manufacturing process that companies lean on for everything from turbine blades to decorative parts for furniture. There are tons of materials that can be used with a CNC machine, whether you need polyurethane foam parts or strong components constructed of a superalloy. It’s one of the most requested services here at Xometry and in this article, we’ll go over important aspects of CNC machining and what the process looks like, as well as its benefits and downsides.
What Is CNC Machining?
CNC machining is a manufacturing technology that works by pulling out material through instructions fed to the machine by a computer called G-code. There are typically two kinds of basic CNC machines you’ll find, one that holds the stock while a rotating tool cuts it and another machine that rotates the stock material while a stationary tool cuts it up. Then, you’ll find more complex machines that are built up from these standard workings. You can see an example of a CNC machined metal Xometry logo below.
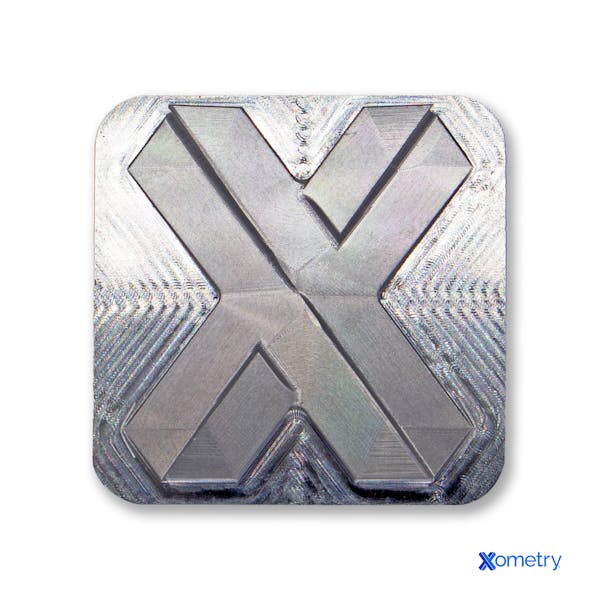
How It Works
Although you’ll find that each CNC machine has a slightly different way of operating and programming, they all generally have the same approach. Here’s how it works:
- Designing the CAD Model: First an engineer or designer will create a computer-aided design (CAD) model in a 3D format. It will be created specifically with CNC machines in mind so it can be manufactured correctly.
- Converting the CAD File: Once the CAD file is created, it’ll be converted into a computer aided manufacturing (CAM) software package that renders G-code for the CNC machine to read.
- Preparing the CNC Machine: Next, the operator will prepare the machine by checking it for flaws or wear and tear. Then, they’ll either add the tools necessary or the machine will do so automatically and put the stock material in place.
- Executing the Machining Operation: After the material is set up, the G-code is ready to go, and the right tools are selected, the machining can get going. The cycle will start and the workpiece or the tool will move, cutting out the material as it was designed until it’s complete. In some cases, the operator may have to move the workpiece throughout. You can see an example of what a three-axis CNC machine looks like in the picture below.
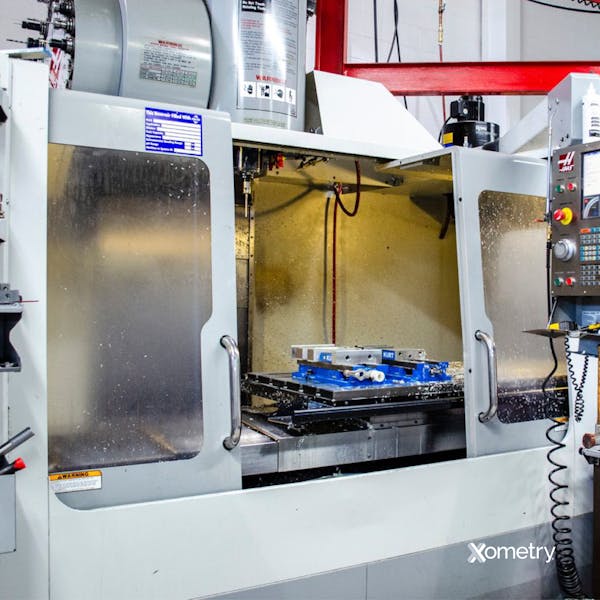
Types of CNC Machines
There are about a dozen CNC machine types out there, but when you break it down to the most fundamental levels, there are two main technologies you’ll find:
CNC Lathe
A lathe features a spindle and a tool post. It works by moving a cutting tool around a spinning, cylindrical piece of material on the spindle. More complex machines (like a Swiss variation) can lathe materials that aren’t in a cylindrical shape. Usually, this is used for products that have a consistent design around their long axis. The illustration below shows how a lathe looks.
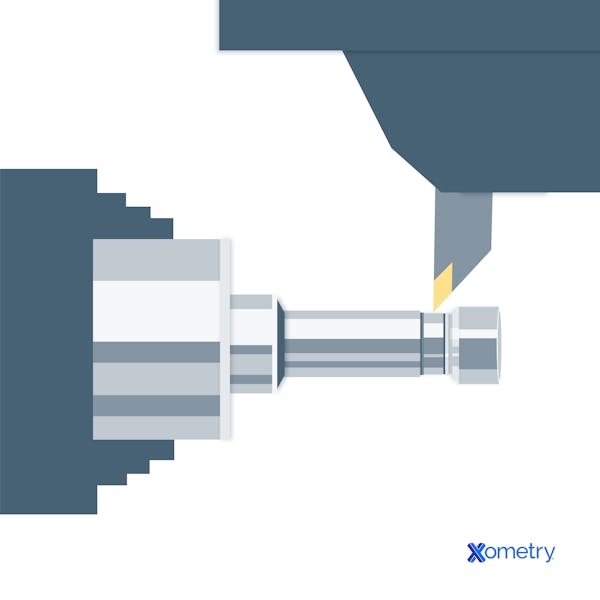
CNC Mill
This kind of machine has a tool spindle and a table with a vise that keeps the material stable and secured to the worktop. Machines with more automated functionality usually have a pneumatic vise and robotic arm that moves the workpiece around. In machines with manual configurations, an operator will need to take this job on. Once the cutting tool is mounted on the spindle, it will move on X, Y, and Z axes depending on how advanced the machine is.

Materials
CNC machining is one of those great manufacturing technologies that can handle a vast range of materials, such as the following:
- Metal: This is the most popular and common material used with CNC machines, especially since nearly any metal is fair game. From free-machined brass to nickel superalloys like Inconel, you can cut a bunch of different products, like shafts and gears.
- Plastic: When it comes to plastic, injection molding is usually how products are made, but it’s possible to create certain components like valve bodies and bushings from ABS, nylon, and polycarbonate with CNC.
- Wood: You’ll find CNC routers are used to shape and carve wood in this capacity. It’s usually for decorative purposes over more functional ones.
- Foam: You can use closed or open-cell polyurethane foam with a CNC machine to cut things like packaging for the insides of toolboxes.
- Composites: Everything from fiberglass to carbon fiber to aramid can be cut with CNC machines, however, they’re incredibly rough on tools so you can expect them to wear down quicker.
Applications and Industries
There is no shortage of uses for CNC machining, but we’ve listed out some of the most typical applications and industries where you’ll find it being used:
- Woodworking: You’ll find that CNC machining cuts down on the time it takes to create wooden parts, especially decorative items with finer details.
- Lettering and engraving: This is done for parts that need to be serialized or simply engraved with artistic designs.
- Electrical industry: You’ll find CNC machines creating holes in printed circuit boards and making copper heat sinks.
- Pharmaceuticals: It’s possible to make ingredient-dispensing nozzles, packaging, and metering pumps with CNC machines for this industry.
Food and beverage: Also within a CNC machine’s remit is its ability to make packaging for different foods and drinks.
FAQs About CNC Machining
With a CNC machine, a few questions often crop up about costs and pros vs. cons.
What Are the Benefits of CNC Machining?
CNC machines have quite a few perks. They are able to produce high-precision parts and meet quality expectations without human error impacting the finished product. They’re also impressive in that they can run for 24 hours, seven days a week if they have the right materials to do so and have the right automation capabilities.
What Are the Disadvantages of CNC Machining?
There are a few disadvantages to working with a CNC machine, one being that it takes a decent amount of training for an operator to be familiar with running one. CNC machines are also pretty expensive when compared to other options, and it’s worth thinking about if the workload you’re planning on will pay off the investment in the long run.
How Much Does CNC Machining Cost?
For professional-scale machines, you’ll be looking at a price that starts around $5,000 all the way to hundreds of thousands of dollars. There are smaller machines that can cost anywhere from $300 to $1,000, but these usually aren’t fit for large production runs.
How Xometry Can Help
At Xometry, we offer a few different CNC services to help you create the exact products you’re after. Aside from CNC machining, you can get free quotes for CNC milling, CNC routing, and CNC turning.
Disclaimer
The content appearing on this webpage is for informational purposes only. Xometry makes no representation or warranty of any kind, be it expressed or implied, as to the accuracy, completeness, or validity of the information. Any performance parameters, geometric tolerances, specific design features, quality and types of materials, or processes should not be inferred to represent what will be delivered by third-party suppliers or manufacturers through Xometry’s network. Buyers seeking quotes for parts are responsible for defining the specific requirements for those parts. Please refer to our terms and conditions for more information.
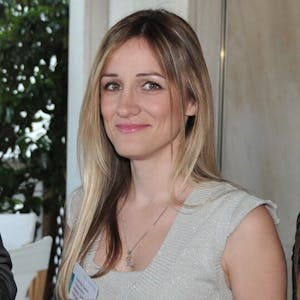