Of the various stainless steel types you’ll have at your fingertips to choose from, 420 stainless steel is a versatile choice that has distinct properties in comparison to others. Its characteristics know no bounds, and you’ll find it worked into cutlery, surgical instruments, and industrial components, thanks to its fantastic strength, resistance to wear resistance and corrosion, and ductility. You can learn more about it in our rundown below.
What Is 420 Stainless Steel?
Meet the martensitic stainless steel that has a unique blend of strength, corrosion resistance, and wear resistance. It does all of this at a relatively affordable price, too, as it has a fairly high carbon level (0.15 to 0.4%) (giving you ample hardness and strength) and around 12% chromium, which knocks out corrosion. You’ll also find manganese and silicon in the mix, which helps with deoxidization and strength, respectively. Any hints of phosphorus and sulfur you come across will be totally minimal as far as impurities go.
Although it gives good corrosion resistance in mild environments, it may not be the best choice for highly corrosive or extreme conditions. In these instances, you’ll be better off with the likes of 316 and 304 steels.
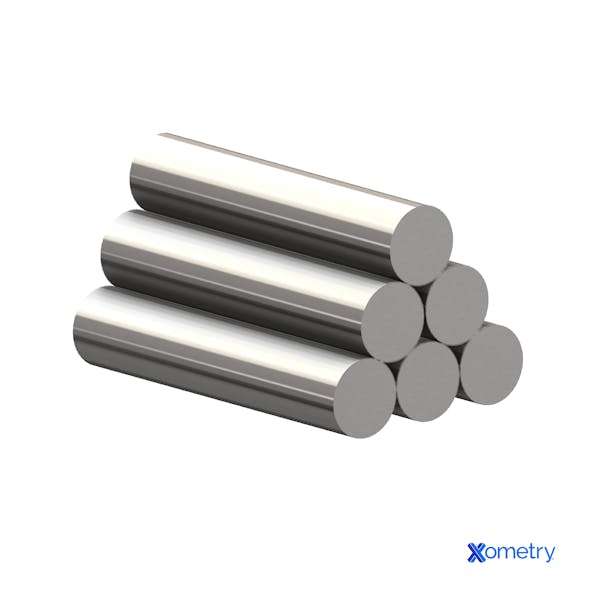
How It’s Made
Here’s a look at how 420 stainless steel is made in eight steps, through the processes of melting, refining, casting, heat treating, and more:
- First, the specific amounts of the raw ingredients needed for this type of steel are mixed and melted together in an electric arc furnace or an induction furnace, usually to 1,500°C or hotter.
- Then, the molten metal is rid of impurities to clean up the steel and make sure the properties you want are present.
- Following this, it gets cast into various formats, depending on what you selected (like billets or ingots).
- After casting, it’ll go through hot working like extrusion, rolling, or forging.
- Then comes annealing, which heat treats the steel and cools it slowly.
- Then the steel will be heated and cooled rapidly (quenching), which hardens it.
- The steel is heated to a high temperature and rapidly cooled (quenched) to harden it, balancing out hardness and toughness.
- After all of these treatments, the steel might head out for finishing processes like grinding or polishing. Then it’s ready for its intended application.
Chemical Composition
The chemical composition of 420 stainless steel is:
- 0.15–0.4% carbon
- 1% (max) of manganese
- 1% (max) of silicon
- 12–14% chromium
- 0.5% (max) of nickel
- 0.5% (max) of molybdenum
- 0.04% (max) of phosphorus
- 0.03% (max) of sulfur
- 0.5% (max) of copper
- 0.15% (max) of aluminum
- 0.05% (max) of tin
- 85–88% iron
Physical and Thermal Properties of 420 Stainless Steel
In the upcoming table, you can learn all about the properties that 420 holds, many of which make it a valuable material:
Property | Value |
---|---|
Property Density | Value 7.74 g/cm3 |
Property Elastic Modulus | Value 200 GPa |
Property Electrical Resistivity | Value 0.55 x 10-7 .m |
Property Tensile Strength | Value 655 MPa |
Property Elongation (% in 50 mm) | Value 25 |
Property Yield strength (Temper: Annealed) Minimum 0.2% offset | Value 40,000 psi |
Property Yield Strength (Temper: Hardened + 350°F) Typical 2% offset | Value 195,000 psi |
Property Brinell Hardness | Value 241 max |
Property Machinability | Value 36–56% |
Property Magnetic | Value Yes |
Property Melting Point | Value 1,495°C |
Property Thermal Conductivity (at 100 °C) | Value 24.9 W/m·K |
Property Thermal Conductivity (at 500 °C) | Value 28.7 W/m·K |
Property Specific Heat (0–100 °C) | Value 0.46 kJ/kg·K |
Property Mean Coefficient of Thermal Expansion (0-100 °C) | Value 10.2 µm/m·K |
Property Mean Coefficient of Thermal Expansion (0-649 °C) | Value 12.1 µm/m·K |
How To Heat Treat 420 Stainless Steel
After a closer look at the heat treating process? For 420 steel, you can make this happen through annealing and hardening. To anneal this steel, it gets evenly heated to around 840 to 900°C. The important part is keeping this temperature consistent for one (or two hours) per inch of thickness of the steel. After it’s annealed, it cools down in a furnace set to 600°C to reduce the possibility of internal stresses and soften the steel. The final step is air cooling.
To harden this steel, you’ll take the annealed version and heat it to around 980 to 1,035°C. Once it hits this point, it’ll get rapidly quenched in oil or air, which turns it from austenite to martensite steel. After this happens, it’ll go through reheating, the exact temperature depending on the hardness and mechanical properties you want. It’ll be held at this level of heat for up to four hours, allowing for carbides to form in the structure. After this time passes, the material gets air-cooled or cooled naturally.
Common Formats of 420 Stainless Steel
You’ll find AISI 420 stainless steel available in a wide range of forms that work best for different applications. These include:
Sheet
These are flat, thin pieces of metal (between 0.5 mm and 3 mm thick) that are superb for purposes that require good corrosion, wear resistance, and strength. You can also cut and further process this kind of steel.
Bar
Bars are shaped into cylinders or rectangles and can also go through further processing, like forging and fabrication.
Plate
Like sheets, plates are flat, but they tend to be thicker (up to 200 mm). They’re a popular choice for structures or machining components, especially when sheets can’t bear the load.
Hot Rolled
This kind of steel comes about through heating and then rolling the steel into the shape you’re after. This process helps the structure of the steel recrystallize and leaves it in a softer format than before—making it easier to shape.
Annealed
Annealed is a softer steel that has a ferrite and carbide microstructure after being heated. It’ll go through a cooling process, which means you can then machine and work with it in an easier capacity.
Cold Drawn
Cold drawn is a process that pulls the stainless steel through a die at room temperature, giving it better dimensional accuracy and a nicer surface finish. Because 420 steel doesn’t do well with cold working, this is a great choice.
Applications
You’ll find 420 steel in places that need serious strength and decent corrosion resistance and hardness, like:
- Cutlery
- Needle Valves
- Pump Shafts
- Bearings
- Screens
- Fasteners
- Valve Components
- Steam/Gas Applications
- Turbines
- Ladder Rungs
- Bushings
- Knife Blades
- Surgical Equipment
- Hand tools
What Are Equivalents of 420 Stainless Steel?
You can find the name equivalents of 420 stainless steel in the table below:
Country/Body | Name |
---|---|
Country/Body UNS No. | Name S42000 |
Country/Body Old British BS | Name 420S37 |
Country/Body Old British En | Name 56C |
Country/Body Euronorm No. | Name 1.4021 |
Country/Body Euronorm Name | Name X20Cr13 |
Country/Body Swedish SS | Name 2303 |
Country/Body Japanese JIS | Name SUS 420J1 |
Equivalents of 420 Stainless Steel
Table Credit: Azom
Advantages and Disadvantages
Here are some of the top reasons why you may look to 420 stainless steel for your manufacturing needs:
- It’s strong and hard, making it great for environments where it’ll be subject to serious wear and tear, abrasion, friction, and contact with hard materials.
- It’s possible to harden it through heat treatments to adjust its physical properties.
- It’s an affordable choice when looked at against other stainless steels, giving you great properties without specialty steel prices.
While 420 stainless steel offers many benefits, it also has a few limitations. Here are the possible drawbacks to consider:
- Its resistance may not hold up in places that are extremely corrosive.
- It can stain and discolor pretty easily.
- Welding can be tricky, and it can lead to cracks if you’re not careful.
- Its heat resistance isn’t the best (especially when up against other steels), and we wouldn’t recommend it for environments over 500 to 550°C.
FAQs on 420 Stainless Steel
What Is the Difference Between 420 Stainless Steel and 2Cr13 Stainless Steel?
You’ll see that 420 stainless steel and 2Cr13 stainless steel are both magnetic martensitic stainless steels, but 420 usually has slightly higher hardness and better corrosion resistance. That said, 2Cr13 stainless steel tends to have higher toughness.
What Is the Difference Between 420 Stainless Steel and 416 Stainless Steel?
420 stainless steel and 416 stainless steel are popular martensitic stainless steel grades, the biggest difference is that 416 is the free-machining version of 420, and it’s the most machinable stainless steel grade overall.
How Xometry Can Help
You can get a free quote for a variety of different services that we offer at Xometry, including options specific to stainless steel, like laser cutting, 3D printing, and CNC machining.
Disclaimer
The content appearing on this webpage is for informational purposes only. Xometry makes no representation or warranty of any kind, be it expressed or implied, as to the accuracy, completeness, or validity of the information. Any performance parameters, geometric tolerances, specific design features, quality and types of materials, or processes should not be inferred to represent what will be delivered by third-party suppliers or manufacturers through Xometry’s network. Buyers seeking quotes for parts are responsible for defining the specific requirements for those parts. Please refer to our terms and conditions for more information.
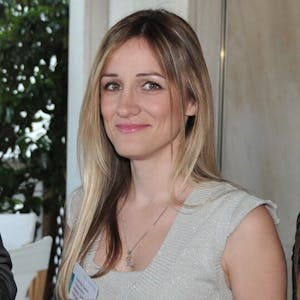