Xometry offers a wide range of alloy steels, from stainless steel to tool steel, low carbon steel, and more. Alloy steel is a type of steel that has certain elements other than carbon, like nickel, chromium, or cobalt added to it, to make it better suited for certain situations. It’s a type of steel that’s used by almost every industry because it’s versatile, and its composition and grade can be changed depending on what it’s needed for. In this article, we’ll look at alloy steel in more detail, as well as its composition, properties, and uses.
What is Alloy Steel?
Quite simply, alloy steel is an iron-based material (in addition to containing carbon) that has at least one more element added to it. These elements are added to improve the mechanical or physical properties of the steel like its hardness, strength, or corrosion resistance, and make up 1–50 wt% (weight percentage) of its composition.
Alloy steels can be grouped in a few different ways, such as their major alloying elements (i.e. stainless steel has large amounts of chromium) or the percentage of all the different alloying elements in the steel. For example, high-alloy steel could have more than 8% alloying elements, while low-alloy steel will have less.
Adding various elements—and in different amounts—will give the alloy steel different properties. But the most common ones are durability, high strength and performance, and corrosion and weather resistance.
For extra durability or corrosion resistance, elements like chromium or nickel are commonly added to the steel. Less common elements, like lead, tin, or zirconium can also be used. Most steels have a carbon content of less than 0.35 wt%, like the type that’s used for welding, which might even be lower than 0.15 wt%. Other types of steel like tool steels can contain a much higher amount of carbon, likely between 0.7 and 1.5 wt%.
Alloy Steel: How It’s Made
Alloy steel is made by melting all the base alloys in an electric furnace at over 1600°C for between 8 and 12 hours. When that’s done, it’s annealed at over 500°C ,which will remove any impurities and modify its chemical and physical properties. Then, hydrofluoric acid is used to get rid of the mill scale from the surface, which is produced during annealing. Annealing and descaling typically need to be repeated until the steel has melted and is ready for rolling and shaping.
In general, steel can be made using either a blast furnace or an electric arc furnace (EAF). The blast furnace is the first step in turning iron oxides into steel, like pig iron, which is made using coke, limestone, and iron ore. EAF, though, melts scrap steel, direct reduction iron, or pig iron using an electrical current.
Not all alloy steels can be heat-treated. For example, ferritic and austenitic stainless steels cannot be heat-treated. For steel to be hardenable enough, carbon will need to be used to harden it. On the other hand, martensitic (and similar) steels are fine to be hardened, and that’s because they contain a high amount of carbon. Alloy steels that contain enough carbon to be hardened usually require a temperature of between 760–1300°C depending on the carbon content. Much like with other types of steel, the hardening process will require controlled heating and cooling.
Alloy Steel Applications
We see our customers using alloy steel in a variety of applications. The application of any given alloy steel will mainly depend on which category it falls into. We can split alloy steels into two main categories: low-alloy steels and high-alloy steels.
Some of them are used to make pipes, especially in energy-related sectors, whereas others are used in the production of corrosion-resistant containers, silverware, pots, pans, and other kinds of kitchen equipment.
Low-alloy steels are strong and affordable, making them a hit with Xometry customers when it comes to CNC machined or sheet-cut components. You can find these alloys on ships, pipelines, pressure vessels, oil drilling platforms, military vehicles, and construction equipment.
High-alloy steels are more expensive to produce and not as easy to work with. On the bright side, they’re perfect for use in automotive, chemical processing, and power generation equipment as they are tough, corrosion-resistant, and strong. Thus, making the extra cost often worth it for these applications.
Both types (particularly low-alloy) are also suitable for injection molding tooling. Grade P20, for instance, can be used for molds that are used for common plastics because they don’t cause corrosion and don’t wear out easily.If your interested in learning more about the tooling options we offer for injection molding, you can learn more on our injection molding service page.
Need Custom Steel Parts?
Types of Alloy Steel
While low-alloy and high-alloy can be used to categorize alloy steels in a broad sense, we can actually get a bit more granular. In the table below, we break out the different types of alloy steel into seven categories instead of just the two we mentioned in the prior section. Following the table, we’ll go into a little more detail about each category. Here’s the breakdown:
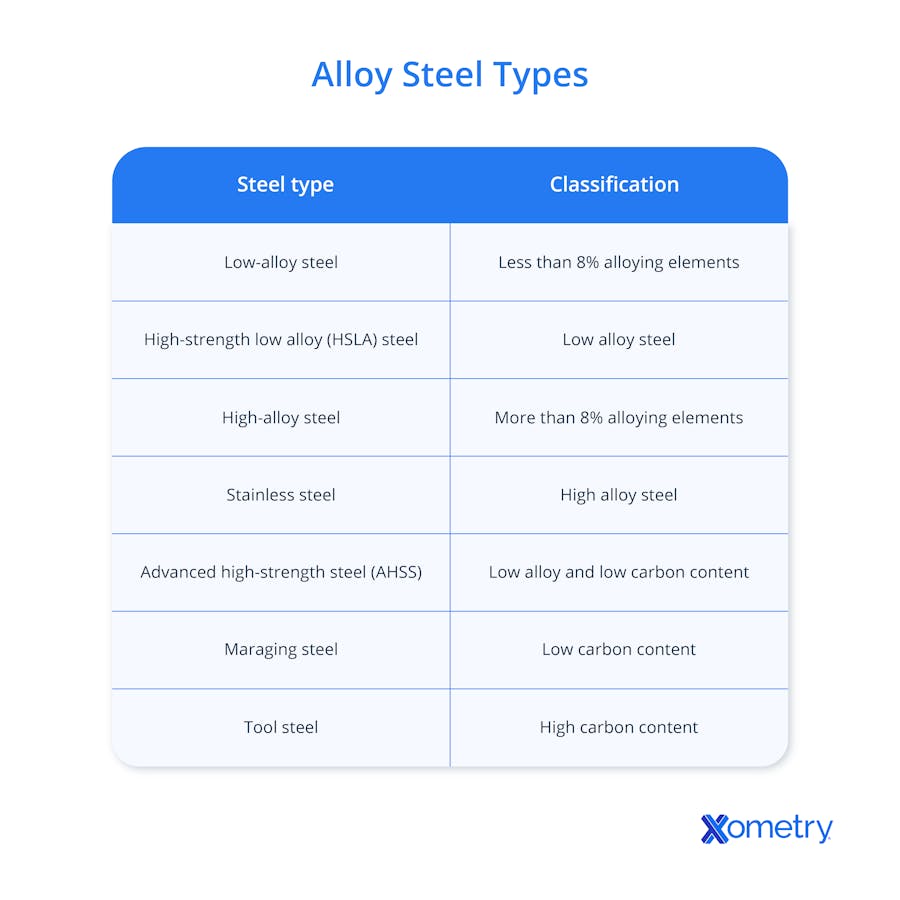
Low-alloy steels contain elements (usually less than 8% of their total composition) that are added to improve the steel’s mechanical properties. So if molybdenum is added, it would increase the steel’s strength. To make it corrosion-resistant and improve its toughness and high-temperature strength, nickel and chromium could be added.
High-strength low-alloy (HSLA) steel, also known as micro-alloyed steel, is strong and resistant to atmospheric corrosion. It’s often either hot-rolled or cold-rolled for the automotive industry to make things like suspension systems, wheels, seat mechanisms, or seat brackets. We can break down HSLA steel into six sub-categories: weathering steel, acicular ferrite steel, pearlite-reduced steel, dual-phase steel, control-rolled steel, and micro-alloyed ferrite-pearlite steel. HSLA steel can be very strong but hard to form. Sometimes, zirconium or calcium can be added to make it easier to work with.
High-alloy steel stands out because of its high alloy content, which is usually more than 8% of its total composition. It’s not the cheapest to make or the easiest to work with. However, because this type of alloy steel is very tough and corrosion resistant, it’s perfect for applications within the automotive, structural components, chemical processing, and power generation equipment sectors.
Stainless steel is probably the most well-known alloy steel around the world and one of the most popular types of steel Xometry customers choose for CNC machined parts. It’s also the most corrosion-resistant. It’s generally alloyed with some combination of nickel, chromium, and molybdenum as its major alloying elements, and these make up around 11–30% of its total composition. There are three subcategories: austenitic, ferritic, and martensitic. Let’s take a look at each of them.
- Austenitic steels are common within the pharmaceutical, architectural, chemical, and mining sectors, where they’re used to contain corrosive liquids and machinery. They can contain a lot of nickel (up to 35%), molybdenum, chromium (16–26%), and niobium, and up to 0.15% carbon. They’re usually the most corrosion-resistant of all the stainless steels and have high formability and strength. They’re also great for extreme temperatures.
- Ferritic steel contains less than 0.10% carbon and more than 12% chromium, which gives it its stainless properties. You’ll see this type of stainless steel used in industrial machinery and cars, and that’s mainly because it was designed to resist corrosion and oxidation, specifically stress cracking corrosion. Ferritic steel is basically unable to be hardened through heat treatment and can only be marginally hardened by cold rolling.
- The last of the stainless steel sub-categories is martensitic steel which you probably have in your own home. It’s often used to make cutlery and has a general chromium content of 11.6% to 18%, as well as 1.2% carbon, and sometimes nickel is added. Generally, the highest chromium content of martensitic steels is lower than the highest in the other two categories. It hardens excellently but is only somewhat corrosion-resistant, making it ideal for cutlery, wrenches, surgical instruments, and turbines.
Advanced high-strength steel (AHSS) is mainly found in automobiles as it’s great for reducing vehicle weight. It’s also very strong and easy to form with processes like sheet metal bending and metal stamping, both of which are services Xometry offers its customers.
Maraging steel is a special kind of steel alloy that has a low carbon content. Compared to most other types, maraging steel is incredibly strong, tough, and ductile. However, instead of carbon, precipitation of intermetallic compounds processes are used to harden it. The main precipitate types are Ni3Mo, Ni3Ti, Ni3Al, and Fe2Mo, which are also found in high-volume fractions. This is another steel type that’s popular in aerospace, as well as tool and weapon production. It can be 3D printed with our direct metal laser sintering (DMLS) process.
Tool steel is a broad term that refers to a range of carbon and alloy steels that are suitable (i.e. hard, tough, wear-resistant, and can hold their own in high temps) for making tools. This type of alloy steel is used to make things like machine dies and hand tools, among others.
How Xometry Can Help
We hope you now have a clearer understanding of alloy steel and its various types! If you are looking to utilize alloy steels in your next project, consider our services. You can get instant lead times and pricing for steel parts made via CNC machining, sheet cutting, sheet metal fabrication, 3D printing, and more! Simply upload your designs to the Xometry Instant Quoting Engine® today to get started.
Disclaimer
The content appearing on this webpage is for informational purposes only. Xometry makes no representation or warranty of any kind, be it expressed or implied, as to the accuracy, completeness, or validity of the information. Any performance parameters, geometric tolerances, specific design features, quality and types of materials, or processes should not be inferred to represent what will be delivered by third-party suppliers or manufacturers through Xometry’s network. Buyers seeking quotes for parts are responsible for defining the specific requirements for those parts. Please refer to our terms and conditions for more information.
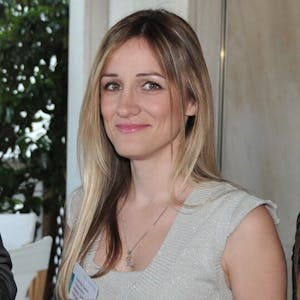