Aluminum bronze is a strong and corrosion-resistant alloy used in many industries, including aeronautical and marine. In this article, we’ll look at what it’s made of, what exactly it’s used for, and all its pros and cons.
What is Aluminum Bronze?
Also known as "aluminum gold" or "gold bronze," thanks to its light gold hue, aluminum bronze is an alloy mainly made of copper and aluminum. It can contain anywhere from 88–92% copper and 4–14% aluminum, along with varying amounts of other alloying elements like silicon, nickel, iron, or manganese.
Adding aluminum to copper gives the alloy its strength by forming a hardy and protective aluminum oxide layer that sticks to the material’s surface. Alloys with high aluminum content can be as strong as medium-carbon steel, and much more corrosion-resistant, too. To make it even harder, a good post-processing treatment, like cold working stress, will do the trick.
Adding in small amounts of other alloying elements could give the material even more benefits. For example, iron could ramp up its mechanical strength, and nickel makes it more corrosion-resistant. These durable alloys are particularly handy for parts that have to withstand harsh conditions (think industrial engineering, aerospace, and marine).
Aluminum Bronze—A Brief History
Scientists first started experimenting with the copper/aluminum combo in the mid-1800s but couldn’t get very far as the materials and production processes were very expensive and rather complex. In 1913, a French metallurgist, Pierre Durville, started making aluminum bronze billets by finding solutions to the oxide inclusion (impurities) and shrinkage problems with the tilting ladle method. This created much stronger alloys with greater corrosion resistance.
A short while later, another metallurgist and engineer, Charles H. Meigh, improved this technique and created nickel aluminum bronze with some help from the French Admiralty. There was no denying this alloy’s benefits, but the material was hard to cast so the public wasn’t very keen to try it out.
It was only after World War II that aluminum bronze really started taking off thanks to the industrial boom, which included the expansion of the offshore oil and marine sectors, and the need for strong and corrosion-resistant propellers for much larger and faster ships and submarines. Since then, use of aluminum bronze has only increased, and it’s used to make many things like marine hardware, pump and valve components, bearings, bushings, and gears.
Types of Aluminum Bronze
Aluminum bronze alloys fall into four categories: (1) high alloyed two-phase aluminum bronzes, (2) low nickel aluminum bronze, (3) silicon aluminum bronzes, and (4) manganese aluminum bronzes. You’ll find more information on these different types in the table below.
Type | Composition | Specifications |
---|---|---|
Type High alloyed two-phase aluminum bronzes | Composition 8–11% aluminum, often with added iron or nickel | Specifications
|
Type Low nickel aluminum bronze | Composition Less than 8% aluminum | Specifications
|
Type Silicon-aluminum bronzes | Composition Up to 2% silicon and 6% aluminum | Specifications
|
Type Manganese-aluminum bronzes | Composition 8–9% aluminum, 13% manganese | Specifications
|
Types of Aluminum Bronze
Composition of Aluminum Bronze
Over the years, hundreds of different aluminum-bronze alloy types have been developed, each with its own specific combination of materials which makes them ideal for different uses. Each type has its own Unified Numbering System (UNS) designation. In the table below, you’ll find examples of some of the most common types of aluminum bronze alloys and their compositions.
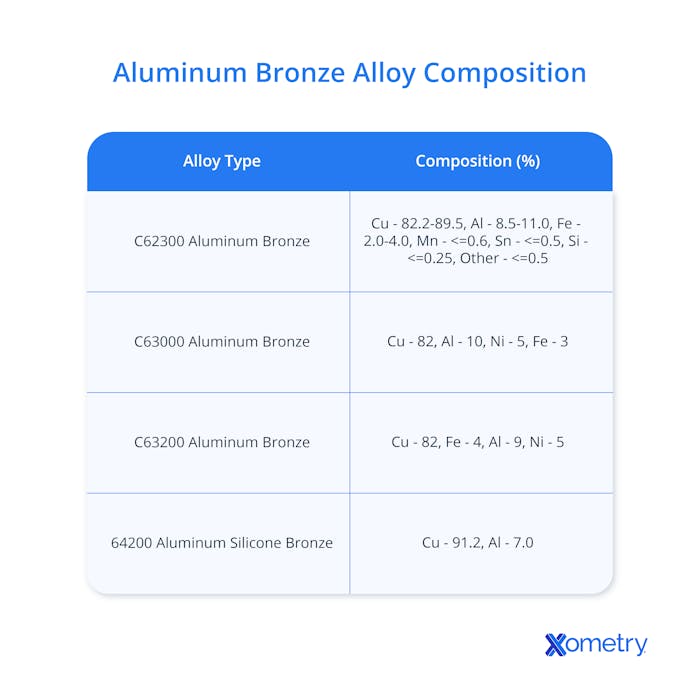
Aluminum bronze alloy composition.
Characteristics of Aluminum Bronze
Aluminum bronze is known for its excellent wear resistance, which is why it’s commonly used in products that need to last a long time in harsh environments. The alloy is non-sparking, making it the perfect choice for making tools for chemical and petroleum industries, mine maintenance, explosive handling, and gas equipment.
Thanks to the quick-forming aluminum oxide protective coating, aluminum bronzes are a common choice in the chemical, atmospheric, and marine sectors. Their impressive corrosion resistance makes them a common go-to. Even if the coatings do get scratched or damaged, they can be fixed almost immediately.
This alloy can be both cold and hot worked. Aluminum bronzes with less than 8–10% of aluminum in them are used for cold working to easily shape things like tube sheets, flats, and wires. Alloys with 8–10% aluminum start to have more strength and hardness, so they’ll need hot working procedures and they can certainly withstand the high temperatures involved during shaping and forming. The best temperature to hot work these alloys is 1300°F and higher.
In terms of what it looks like, as we’ve already briefly covered, aluminum usually has a warm, golden hue, with coppery tones—but not always. Its final color will depend on its exact content, i.e., more copper will lend the alloy a deeper orange color. Overall, this alloy is one of the most attractive, and can even be polished to make it reflective and even prettier. Below is an image of the different shades that aluminum bronze can come in. As you’ll note, some don’t even look like bronze!
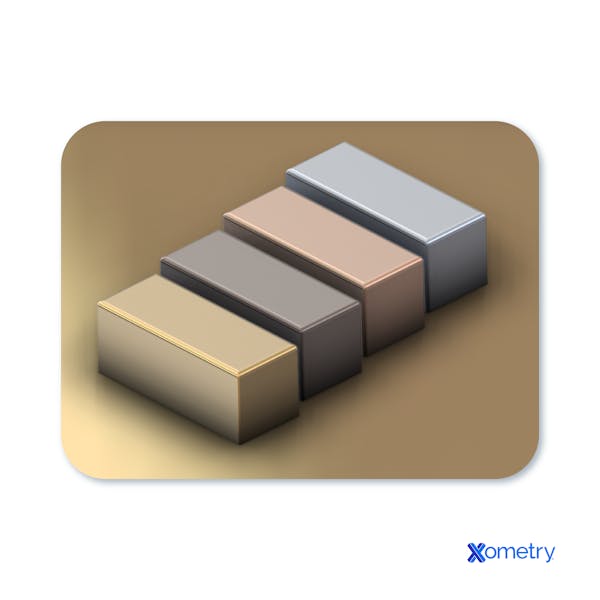
Different shades of aluminum bronze.
Below is an example of what a final aluminum bronze product can look like.
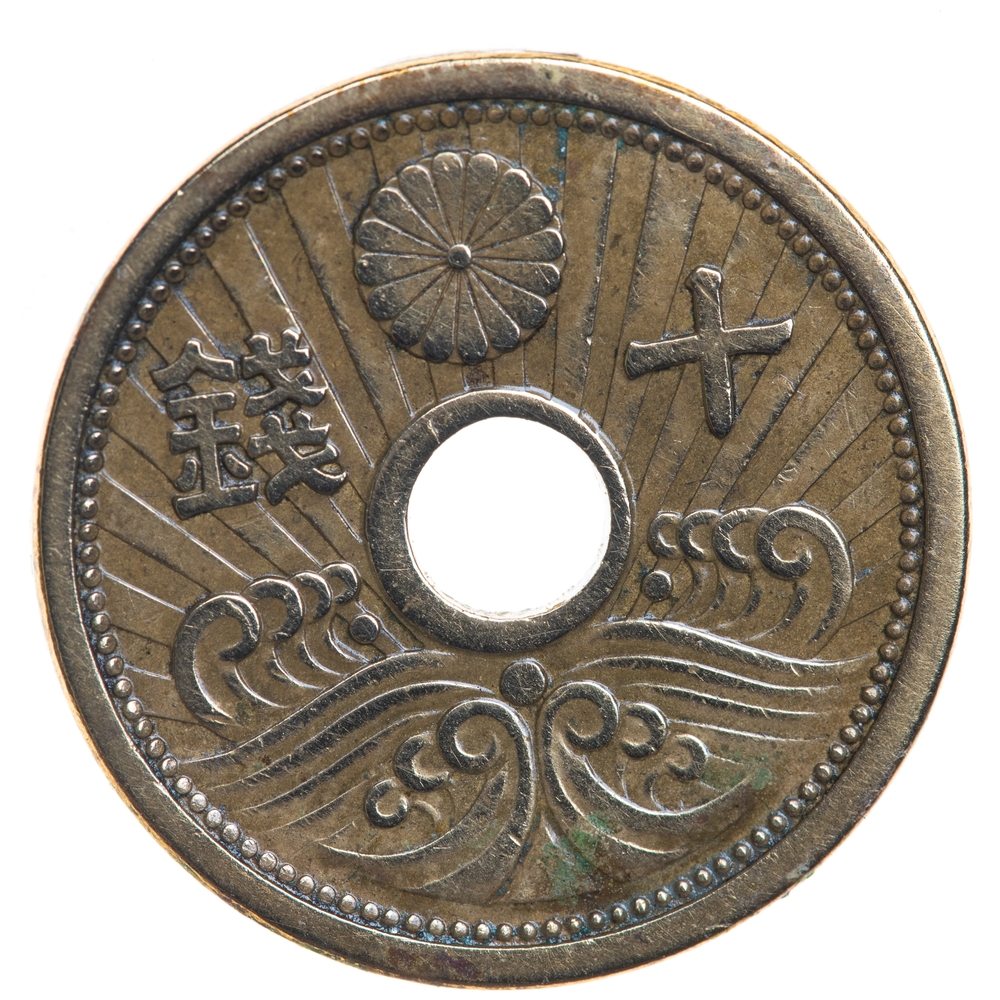
Coin made of aluminum bronze.
Image Credit: Shutterstock.com/CL Shebley
Aluminum Bronze Properties
Aluminum bronze has an array of impressive properties, both physical and chemical, but it also has a few disadvantages meaning that it can’t be used for everything. Let’s have a look at these below.
Advantages
Strength and durability: Aluminum bronze is very hard and has a compressive and high tensile strength, meaning it will wear out and/or break at a much slower rate than other materials. Depending on the exact alloy composition and heat treatment, its strength can be compared to that of some low alloy steels, and even some stainless steels. It can withstand both wear and abrasion, making it extremely durable, too.
Rust, corrosion, oxidation, tarnish resistance: Aluminum bronze doesn’t rust (the term “rust” refers to the corrosion of iron and iron-based alloys). It has a high level of corrosion resistance, even when exposed to seawater and acids, thanks to its ability to form a tough aluminum oxide (alumina) protective layer. Even in higher temperatures, its oxidation rates are low. It’s also the most tarnish-resistant of all the copper alloys, remaining entirely unaffected when faced with atmospheric corrosion.
Reactivity: Aluminum bronze is generally less reactive than pure metals on their own, like aluminum or copper, making it more compatible with other metals and materials for many different uses.
Low friction: Aluminum bronze has a friction coefficient of about 0.18 when unlubricated, generating much less friction between itself and other materials compared to other materials, including tool steel (coefficient of 1.11). This helps it slide smoothly on other surfaces and reduces the level of wear and heat generated during operation.
Heat resistant and non-sparking: This alloy will generally stay stable even at high temperatures. It’s also non-sparking making it ideal for use in environments where sparks could be a safety hazard and ignite flammable gases, vapors, or dusts. This is a particularly useful perk to have in industries like oil and gas, chemical, and mining.
Antimicrobial: Depending on its specific makeup, some aluminum bronze alloys are suitable for medical applications (i.e., dental alloy), thanks to their biocompatibility.
Variety and aesthetic appeal: The sheer variety of aluminum bronze alloys offers a lot of manufacturing flexibility and possibilities. The different and attractive color available also gives you many aesthetic options.
Disadvantages
Hard to machine/forge: Aluminum bronze has excellent strength, abrasiveness, thermal conductivity, and copper content, but its poor chip formation and hardness (which is a perk in many instances) make machining quite challenging. Also, despite its good casting qualities, it’s difficult to forge.
High maintenance: This diva of an alloy needs quite particular and specific care to keep up its appearance. It needs to be cleaned with gentle soap and water solution, and then dried with a soft cloth.
High cost: Aluminum bronze is most often more expensive than other similar materials because of its pricey ingredients (like tin, aluminum, and silicon). The perks these additions offer, however, often justify the increased cost.
Limited availability: This alloy is not as widely available as other options, and you could find yourself struggling to source it, especially if you need lots of it.
Chemical Properties of Aluminum Bronze
Just to recap, the chemical properties of aluminum bronze are its composition of 4–14% aluminum by weight, with the rest being copper along with small amounts of other alloying materials like iron, nickel, manganese, silicon, and zinc. It has low oxidation rates even in higher temperatures, and it’s highly corrosion resistant, thanks to the alumina layer that it forms. It’s less reactive than aluminum or copper materials alone, and although it can oxidize over time, the rates are low. It’s also heat resistant and stays stable at higher temps.
Physical Properties of Aluminum Bronze
In addition to all the properties mentioned above under “Advantages,” here’s a table of some of the more technical physical properties of aluminum bronze.
Physical Property | Description |
---|---|
Physical Property Young's modulus | Description 110 GPa |
Physical Property Density | Description 7.45 g/cm³ at 20°C |
Physical Property Melting point (solidus) | Description 1030°C |
Physical Property Thermal conductivity | Description 59 W/mK |
Physical Property Brinell hardness | Description 170–177 BHN |
Physical Property Ultimate tensile strength | Description 550–900 MPa |
Physical Properties of Aluminum Bronze
Applications of Aluminum Bronze
Aluminum bronze alloy is used in many industries for everything from engine components and marine hardware to guitar strings. The alloy's exact chemical composition will determine its manufacturing and environmental compatibility, however.
Thanks to its strength, resistance to wear and corrosion, and effective heat dissipation and stability, it’s commonly chosen for vehicle engine parts (i.e. piston pins) that must have the ability to withstand repetitive stress and friction. It’s used in aviation parts (i.e. bushings and bearings), and in marine components that need to resist saltwater corrosion. All these benefits make it a top choice for the manufacturing of actuated butterfly valves, too.
In addition, the chemical industry likes this alloy as it holds its own in acidic conditions, making it perfect for processing equipment handling of non-oxidizing acids, like hydrochloric acid. Its resistance to many fluids (i.e., acids and alkalis) also makes it valuable in industrial process fluid equipment. Last but not least, you may have noticed that guitar strings are often made from aluminum bronze. They have bright tones, are super strong, and can last through a whole lot of strumming.
Aluminum Bronze Manufacturing Processes
There are many manufacturing processes that can be used with aluminum bronze, including welding, and laser cutting. Before we go into those, let’s look at how to actually make this alloy from scratch using the classic bronze casting process.
First things first, you’ll need all the proper protective gear and make sure your working area is clean and well-ventilated. You’ll also need the appropriate manufacturing equipment like an industrial-grade crucible or forge (although, for small-scale forging, you can use a blowtorch). The aluminum and copper should be weighed in a 9:1 ratio before being put in the crucible. The metals then need to be melted together at 1,038 °C and stirred with a graphite rod until they are thoroughly mixed.
After pouring the mixture into a mold, it should be left to cool and firm for 20 minutes, before being carefully removed (it will obviously still be very hot). For a shiny finish, dunk it in water to quench it. Other casting methods used to make aluminum bronze include centrifugal, continuous, investment, and sand casting processes.
After casting, the alloy can be made into many different items using various manufacturing methods. These include machining (milling, turning, drilling, grinding, and CNC machining), heat treatment (annealing, quenching, tempering), surface treatment (polishing, coating, plating), forging, extrusion, cold working, powder metallurgy, die casting, and joining via various welding methods.
Laser cutting is a great way to cut aluminum bronze. Compared to other more traditional cutting methods, laser cutting has a minimal heat-affected zone (HAZ), reducing the risk of the material becoming distorted or losing any of its valuable properties. It’s also versatile and can cut alloys of various thicknesses.
Aluminum bronze is also easy to weld. It usually needs no preheating (except for particularly thick sections), but a thorough clean before and after each pass will help prevent porosity. A MIG welder is a great option because it creates strong bonds and keeps all the alloy’s good properties.
Aluminum Bronze vs. Brass
While both aluminum bronze and brass are copper alloys, aluminum bronze has aluminum, tin, iron, and nickel in addition to copper. Instead of tin or aluminum, the major alloying element in brass is zinc. Aluminum bronze is stronger and more resilient than brass. It has a tensile strength of 780 MPa, compared to brass’s 200 to 500 MPa.
Bronze vs. Aluminum Bronze
Aluminum bronze and bronze are also quite different. Traditional bronze is usually made up of copper and tin, but aluminum bronze’s extra alloying elements make it better than bronze in many ways. It has a higher strength and level of durability, thanks to the aluminum content, and adding copper into the mix helps make it even stronger with heat treatment.
Aluminum Bronze—Summary
We hope we covered everything you wanted to know about aluminum bronze, but if there’s anything we haven’t answered about this useful alloy, please reach out to a Xometry representative. We also offer a wide range of manufacturing services, so feel free to visit our website to learn more or request a free, no-obligation quote.
Disclaimer
The content appearing on this webpage is for informational purposes only. Xometry makes no representation or warranty of any kind, be it expressed or implied, as to the accuracy, completeness, or validity of the information. Any performance parameters, geometric tolerances, specific design features, quality and types of materials, or processes should not be inferred to represent what will be delivered by third-party suppliers or manufacturers through Xometry’s network. Buyers seeking quotes for parts are responsible for defining the specific requirements for those parts. Please refer to our terms and conditions for more information.
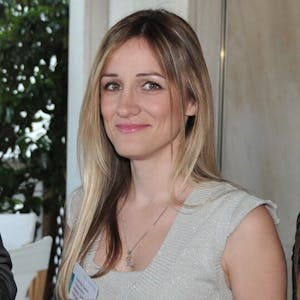