Whether designing a bridge, making aircraft components, or working on a smaller project, you’ll need to know and understand the flexural properties of the material to make sure it can live through whatever stresses you intend to put it under. Flexure (or bend) testing is the way to do this. Read on to find out exactly what it is, how it works, and how to do it.
What is Flexure/Bend Testing?
Flexure/bend testing is a straightforward and dependable mechanical testing method used to evaluate the behavior of a material when it’s subjected to bending forces. It can be done on a variety of different materials, including:
- Metal (steel, aluminum, copper, alloys)
- Plastic (thermoplastics, thermosetting plastics)
- Composites (combination of different materials like fibers and resins)
- Brittle materials (ceramics, ceramic composites)
- Wood (plywood, particleboard, and other wood-based materials)
- Paper (cardboard and similar)
This test provides information on the material’s mechanical properties, namely flexural strength, flexural modulus, bending stiffness, surface behavior, and response to bending stress. Knowing these helps in the material selection process as you can compare the performance of different materials under bending loads to choose the most suitable one for your particular project. In addition, it provides essential data for research and development purposes in the study and improvement of materials, the development of new products, optimizing designs, and enhancing structural integrity.
It’s worth noting, however, that the size and thickness of the samples tested can influence the results (i.e., it can be hard to get uniform stress distribution on thin samples). For useful data, you’ll need to test on a piece representative of the intended application. There are also various standards to adhere to (which we’ll cover a little further down), and choosing the appropriate one for a specific material or application can sometimes be quite the challenge.
Applications
Flexure or bend testing is a go-to method across industries like engineering, construction, aerospace, and manufacturing. It helps professionals understand how materials behave under load, ensuring they can handle real-world stresses. For engineers, it’s particularly important so they can design strong, reliable structures like bridges and beams. Manufacturers use it to verify product quality and compliance with industry standards. In aerospace, where materials face extreme forces, flexure testing helps ensure the safety and performance of aircraft components. Many industries even require this test to meet regulations, making it a must for assessing material durability and reliability.
Testing Flexure/Bend
There are three main types of flexure tests based on the number of support points involved. The below table provides all the necessary differentiating characteristics of each test, and further down, you’ll be able to see images with examples for each type.
Test Type | Setup | Effect | Applications |
---|---|---|---|
Test Type Two-Point | Setup One end clamped, force applied at a set distance from the clamp | Effect Creates a deflection-causing bending moment | Applications Thin and flexible materials like paper, cardboard, and films |
Test Type Three-Point | Setup Sample supported at two outer points, load applied in the center | Effect Localized force at the midpoint | Applications Tough and elastic materials, widely used for plastics, metals, and composites |
Test Type Four-Point | Setup Sample supported at two outer points, load applied at two inner points | Effect A more complex bending moment with uniform stress distribution, reducing peak stress | Applications Brittle materials like ceramics and glass-fiber composites |
Flexure Bend Test Types
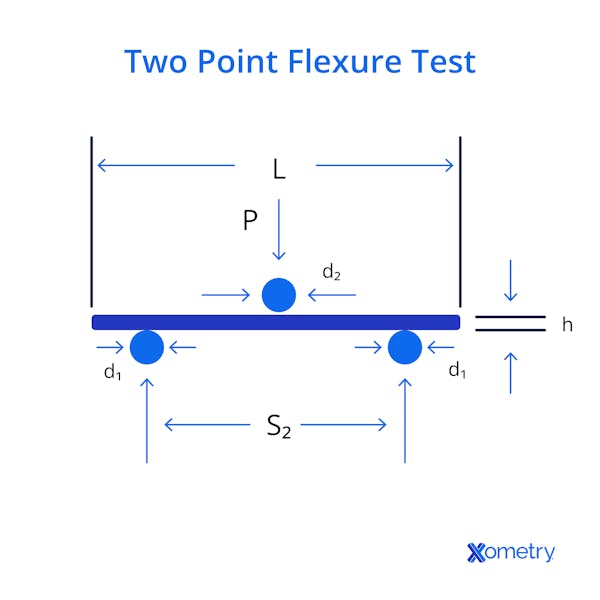
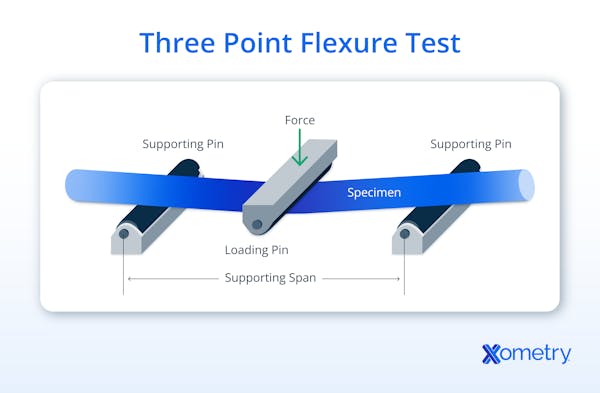
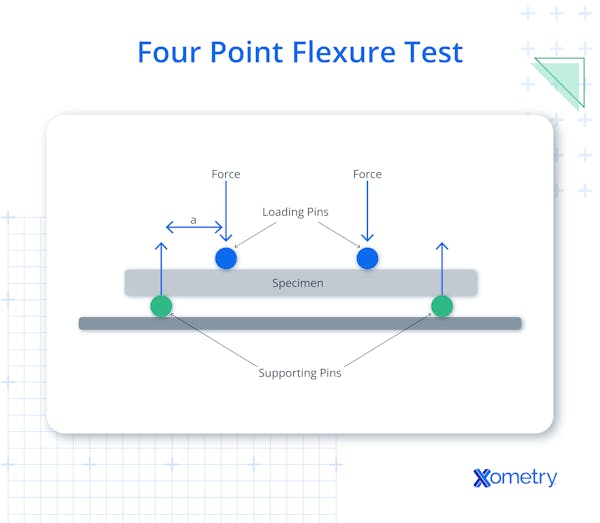
An illustration of a two point flexure test.
Equipment
To perform a flexure/bend test, you’ll need the material sample being tested, which is usually rectangular or cylindrical, and a universal testing machine (UTM), which is a specialized flexure testing device that applies the load and measures the response. In addition, fixtures, supports, and anvils to hold the specimen in place (based on the test type) are needed, as well as measurement devices, like strain gauges, extensometers, or displacement sensors to track deflection and stress distribution.
Process
Once you’ve got all the necessary equipment, here are the steps in the flexure/bend testing process:
- Cut and prep your sample, and inspect it for defects.
- Place the material on the supports and calibrate the machine according to the chosen testing standard (ASTM, ISO, etc.).
- Set the machine to apply the force at the designated point(s), which will cause the sample to bend.
- Measure track deflection, stress, and strain as the force increases.
- Keep going until the sample reaches its breaking point or its maximum deflection limit.
Standard | Material | Tests |
---|---|---|
Standard ASTM C674-88(2006) | Material Ceramic whiteware | Tests Flexural properties |
Standard ASTM D790-03 | Material Reinforced and unreinforced plastics and electrical insulating materials | Tests Flexural properties |
Standard ASTM E855-08 | Material Flat metals for spring applications involving static loading | Tests Bend testing |
Standard BS EN 2746:1998 | Material Glass-fiber-reinforced plastics | Tests Flexural tests with the three-point bend method |
Standard BS EN ISO 8491:2004 | Material Metals in the form of tubes with full sections | Tests Bend test |
Standard ISO 9538:2017 | Material Hydraulic tubing joints and aerospace fittings | Tests Planar flexure test |
Standard ISO 178:2019 | Material Plastics | Tests Flexural properties |
Standard JEDEC JESD 22B113 | Material Mounted electronic products at board level | Tests Cyclic bend testing |
Standard IPC JEDEC 9702 | Material Interconnects at (printed circuit) board level | Tests Monotonic bend testing |
Standards for Flexure Bend
FAQs on Flexure/Bend Testing
What’s the difference between flexure/bend and ductility testing?
Ductility testing measures a material's ability to undergo plastic deformation without fracturing under tensile stress—basically how much it can stretch before breaking under tension. Flexure/bend testing, as we’ve discussed, evaluates a material’s ability to withstand bending stress. Flexure testing is used on materials that will be made into load-bearing structures, but ductility testing helps assess a material’s suitability for applications requiring stretchability, such as metal forming. In a ductility test, the sample is subjected to a uniaxial tensile load until it fractures, while elongation and reduction in the cross-sectional area are monitored and measured.
Is footing a flexural member?
No, they’re not. While they might see some degree of bending due to the applied loads, footings (foundations) aren’t typically treated as flexural members in the same sense as beams. Footings mainly support vertical loads and resist forces like shear and compression rather than bending. Beams, on the other hand, are considered flexural members because they are designed to carry bending loads, and their design focuses on their resistance to bending moments. The design and analysis of footings focus on different failure modes and considerations, such as the prevention of punching shear failure and the distribution of loads to the underlying soil.
How Xometry Can Help
For more info on flexure/bend tests, get in touch! If you’re good on the material testing front, let’s work together to get your manufacturing projects underway. Xometry offers dozens of unique materials from plastics, metals, composites, and more. Find these materials in the Xometry Instant Quoting Engine® and get automatic pricing and lead times on various manufacturing processes like CNC machining, 3D printing, casting, and more!
Disclaimer
The content appearing on this webpage is for informational purposes only. Xometry makes no representation or warranty of any kind, be it expressed or implied, as to the accuracy, completeness, or validity of the information. Any performance parameters, geometric tolerances, specific design features, quality and types of materials, or processes should not be inferred to represent what will be delivered by third-party suppliers or manufacturers through Xometry’s network. Buyers seeking quotes for parts are responsible for defining the specific requirements for those parts. Please refer to our terms and conditions for more information.
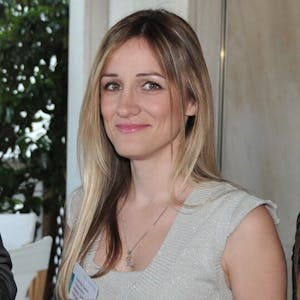