Force-measurement devices are used to quantify the magnitude and direction of forces acting between physical bodies. These forces may include tension, compression, shear, bending, and torque, depending on the application. A common example is measuring the gravitational force (weight) of an object.
Accurate force measurement is vital in engineering, manufacturing, material testing, structural monitoring, and robotics. This article explores the main types of force-measurement devices, their functional characteristics, and their intended use cases across various industries.
A variety of measuring instruments can be used to measure forces, as discussed in the article below. This article explores the types, characteristics, and purposes of force-measurement devices.
What Is a Force-Measurement Device?
A force-measurement device is a piece of equipment used to quantify the magnitude and direction of an applied force or load. The device typically consists of a force transducer (such as a load cell or strain gauge) that senses the applied force, and a signal processing/display unit to present the measurement. In mechanical (analog) devices, spring-based systems like Bourdon tubes or dial gauges are used instead of electronic transducers. Several types of force-measurement devices can measure a range of loads for different applications.
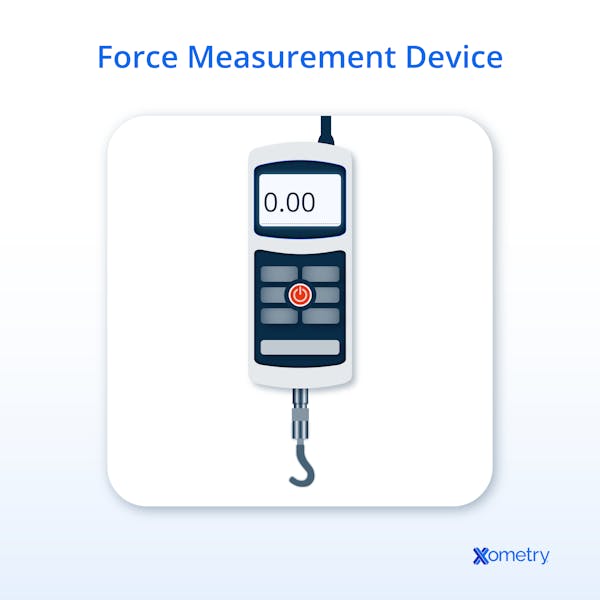
Why Are Force-Measurement Devices Used?
Force-measurement devices are used for a variety of purposes: research, testing, quality assurance, and production applications. Force-measurement devices can be used to determine whether a fastener is sufficiently tight, the tensile or compressive strength of a material, the tension in a cable, the power output of a motor, or the weight of an object.
What Is the Purpose of Force-Measurement Devices?
The purpose of a force-measurement device is to accurately determine the forces acting on an object. This could include: the force required to break a material, the weight of an object, the load carried by a cable, the surface tension of a liquid, or the force applied through a fastener. Each of these purposes requires a different type of force-measurement device. Typical applications of force-measurement devices include: safety testing, quality assurance, in-service testing, research, and process control purposes.
Why Are Force-Measurement Devices Used?
Force-measurement devices are used for a variety of purposes: research, testing, quality assurance, and production applications. Force-measurement devices can be used to determine whether a fastener is sufficiently tight, the tensile or compressive strength of a material, the tension in a cable, the power output of a motor, or the weight of an object.
What Is the Purpose of Force-Measurement Devices?
The purpose of a force-measurement device is to accurately determine the forces acting on an object. This could include: the force required to break a material, the weight of an object, the load carried by a cable, the surface tension of a liquid, or the force applied through a fastener. Each of these purposes requires a different type of force-measurement device. Typical applications of force-measurement devices include: safety testing, quality assurance, in-service testing, research, and process control purposes.
Who Requires Force Testing?
Force testing is used by production, research, and quality assurance personnel, as well as testing laboratories and organizations that set material and design standards. Each of these organizations uses force testing in every industry, including the automotive, aerospace, oil and gas, medical, electrical, and construction industries. Each application may require a different force-measuring device, but all force-measurement devices work by measuring a displacement to determine an applied load.
What Are the Different Types of Force-Measurement Devices?
There is a wide range of instruments used to measure force in various industrial, research, and commercial applications. Some of these are discussed in the sections below.
1. Load Cells
A load cell is a type of force transducer that converts applied tension, compression, or shear force into a measurable signal, most commonly an electrical signal generated via strain gauges. Load cells are by far the most widely used type of force-measurement device. Load cells are used in most test equipment for force and weight measurement, including tensile test machines and industrial/commercial scales.
There are several types of load cells, including strain gauge (electrical), hydraulic, and pneumatic models, each using a different principle to measure applied load. The main advantages of using load cells are that they are very precise, require little maintenance, have a long service life, and can be used in a wide range of applications. The disadvantages of load cells are that they can be bulky depending on design and capacity, and that they require appropriate signal conditioning equipment, which can be costly, especially for high-precision systems. Load cells can be used to measure the forces on or the weight of any material. Most industries utilize load cells in some capacity, including testing, quality assurance, and process control.
2. Spring Scales
Spring scales, also known as spring balances, are analog force-measurement devices that determine the force applied by measuring the extension of the scale’s spring while under load. Spring scales are used to measure the force applied by gravity (weight), by connecting the attachment point of the device to a stable fixture and then suspending the material to be measured from the other end of the device. The device works on the principle of Hooke's Law, which describes the relationship between the extension of a spring and the force applied to the spring.
The main advantages of spring scales are that they are simple in design, cheap, and portable. The disadvantages are that they are less accurate than electronic alternatives, can not measure high loads, and require frequent recalibration.
Temperature variations affect measurement accuracy, as the spring’s elastic modulus changes, altering the force-extension relationship defined by Hooke’s Law.
Spring scales can be used in various settings to measure light loads and liquids; however, when measuring the weight of liquids, a container of a known weight will be required.
To learn more, see our full guide on Spring Testing.
3. Force Gauges
Force gauges, also known as push-pull force gauges or tension and compression force gauges, are used to measure an applied load in either tension or compression for testing, process control, quality assurance, or research. Force gauges come in two forms: analog and digital.
Analog force gauges use a spring or a load cell to detect the applied force and then mechanically display the magnitude of the force by moving a needle gauge. Analog force gauges are easy to use, portable, and low maintenance.
Digital force gauges work similarly to analog gauges in force detection but convert the signal into an electrical output displayed digitally. The movement detected by the load cell or strain gauge is converted into an electrical signal, which can be shown on a digital display. While digital force gauges are more expensive than analog gauges, they can record and store the measurements, making it easier to monitor force changes over time. Force gauges can be used in the sports industry to test grip strength, in the manufacturing industry to conduct compression or tensile tests, and in research to test the strength of adhesives through bond tests.
4. Torque Wrenches
A torque wrench is different from most other force-measurement devices as it not only measures an applied force, but it is also used to apply the force. A torque force is an applied load that causes a body to rotate, and it is most commonly applied when tightening fasteners such as bolts and nuts. A torque wrench, as the name suggests, measures the applied torque, specifically for fasteners such as bolts. There are several types of torque wrenches, including click, electronic, and hydraulic.
A click torque wrench works by setting the desired torque for a fastener and then tightening the fastener until you hear a click. This click confirms to the user that the fastener has experienced the right torque. Electronic torque wrenches work similarly but can additionally record and store torque data for analysis and quality control. A hydraulic torque wrench works by placing the wrench drive socket on the fastener to be tightened, and then a hydraulic pump pumps hydraulic fluid into a piston, which extends and rotates the driving socket. Once the piston has fully extended, it is retracted, and the internal ratchet system prevents the driving socket from turning with the piston. The piston can then continue to be extended repeatedly until the desired torque force is achieved.
The advantages of using a torque wrench are that the operator can tighten the fastener and check the resulting value of torque at the same time; the tool is portable; and the torque wrench can also be very accurate (depending on the type of torque wrench used). Torque wrenches are used exclusively to tighten fasteners. They are used in many manufacturing and service industries that use fasteners, including automotive, aerospace, marine, and other heavy industries.
To learn more, see our full guide on Torque Testing.
5. Pressure Sensors
Pressure sensors are very similar to load cells. However, the difference is that load cells directly measure the applied force, whereas pressure sensors indirectly measure the force.
Pressure sensors are often used to measure pressure in gases or liquids, and while related to force measurement in hydraulic systems, they do not directly measure force like load cells do. Pressure sensors measure force indirectly by detecting the pressure of hydraulic fluid in a system. The pressure of hydraulic fluid can be influenced by factors such as the weight of the fluid column (hydrostatic pressure). Additionally, friction in the hydraulic cylinder or piping can affect the relationship between pressure and the actual applied force.
6. Piezoelectric Force Sensors
Piezoelectric force sensors work by using a quartz crystal to detect a change in applied loading. The pressure applied to the quartz crystal generates an electrical signal that can be digitized and stored or read from a digital display. Piezoelectric force sensors are used to detect rapidly applied loads in impact testing or for oscillating loads because they can rapidly detect changes in applied loads.
The advantages of piezoelectric force sensors are that they are fast at detecting changes in force, they can measure a very large range of loads, and they are compact. The disadvantage of a piezoelectric force sensor is that it is prone to drift, which means that when the voltage is removed from the quartz, internal charges slowly dissipate. While the quartz recovers, the crystal will expand or contract.
This slightly changes the relationship between the applied force and the electrical charge generated. So, over time, the amount of electricity generated for the same force is different, and this produces inaccuracies. This disadvantage is less of a problem when measuring large loads (kilonewtons and above) because the changes caused by drift do not make a substantial difference to the value of the applied load.
Piezoelectric force sensors are used in spot welding, impact resistance testing, ultrasonic transducers, diesel fuel injectors, grill igniters, microwaves, electric toothbrushes, and automotive crash testing.
7. Dynamometers
Dynamometers are force-measuring devices that measure tension, torque, speed, or power. They are used mainly in the automotive and construction industries. There are two main types of dynamometers: the first measures the power output of motors, and the second one measures force, usually tension or compression.
The motor-testing dynamometer is essentially an electrical generator that applies a load to the motor being tested and then reads the electrical power produced as the motor drives the dynamometer. They are widely used in the automotive industry to measure engine torque and rotational speed, which are used to calculate power output (typically in horsepower or kilowatts).
A tension dynamometer has a cable that runs through three pulleys. The two outer pulleys are stationary, while the middle one is spring-loaded. The more tension the cable is under, the more the middle pulley moves. The displacement of the middle pulley is measured and displayed as a tension force. This type of mechanical or electronic tension dynamometer is used in rigging, structural monitoring, and load testing of cables in infrastructure such as bridges, cranes, lifts, and utility lines.
8. Tensiometers
Tensiometers are used to measure surface tension, dynamic contact angle, surface free energy, powder wettability, and interfacial properties. Tensiometer test equipment details may differ, but they all work on the same general principle, which is to use a transducer to measure the force required to lift a test probe out of a liquid or to measure the weight gain of a submerged specimen.
For example, the wettability of fibers is tested by lowering the fibers into the test liquid and then measuring the increase in weight of the fibers. This determines how well the liquid wets (adheres to) the fibers.
To measure surface tension, a probe is lowered into the liquid, and the force required to detach the liquid from the probe is measured. The force required to remove the probe is measured, and the surface tension can be calculated using the force measurement. To achieve these measurements, the tensiometer must be very sensitive.
The advantages of a tensiometer are that it is highly accurate and uniquely suited for surface science applications such as measuring surface tension, wettability, and surface free energy. The disadvantages are that it is very expensive and it requires skilled technicians to operate it.
What Characteristics Do Force-Measurement Devices Have in Common?
There are a few characteristics that all force-measurement devices must have, and that all devices have in common. These common features are listed below:
- Point for force application
- Method to output measured force (digital or analog display, signal output, etc.)
- Structural rigidity to minimize deformation and maintain measurement accuracy
- Sensing element (such as a spring, strain gauge, piezoelectric crystal, or hydraulic/pneumatic mechanism)
What Are the Different Types of Force Gauges?
The two main types of force gauges are listed and discussed below:
1. Spring-Meter Gauge
Spring-meter gauges are force-measurement devices that use the extension of a spring within the device to determine the applied force or weight of the measured material. Spring gauges are often analog and work using the principle of Hooke's Law, which describes the relationship between the extension of a spring and the force applied to it. The extension causes a mechanical linkage to move a pointer or needle on a calibrated scale. The more load is applied, the more the spring extends, resulting in a higher needle reading.
The advantages of spring gauges are that they are usually cheaper than digital gauges, they are portable, and simple to use. Their disadvantages are that they may be less accurate and require more frequent calibration than digital gauges. Furthermore, they are usually only analog devices and can not record data. Spring gauges are often limited in the force range they can measure. Additionally, spring gauges that are subject to large temperature changes become less accurate as the relationship between applied force and material extension changes due to the material’s change in elastic modulus. Also, metal fatigue can lead to the failure of the spring.
2. Digital-Meter Gauge
Digital meter gauges use transducers, typically strain gauge-based or piezoelectric, to measure an applied load. The mechanical strain alters electrical resistance, which is converted into a digital signal that can be stored or displayed digitally. The advantages of a digital meter gauge are that it is usually more accurate, easier to calibrate, can measure a wider range of loads, and can record the forces measured for later review. The disadvantages include being more expensive and requiring a power source.
How Is Force Calculated?
Force is calculated in different ways depending on the device and context. For spring-based devices, Hooke’s Law is used. Hooke's Law describes the relationship between the extension of a spring and the applied load. Hooke's Law is displayed below:
Force = Spring constant * length of extension
The equation shows that if the spring constant is known, then the force can be determined by measuring the spring’s extension. Spring-based devices use this principle, often with a mechanical linkage moving a needle to indicate force. Other devices, like load cells, use strain gauge principles and output electrical signals based on deformation.
Do Manufacturers Conduct Force Testing?
Yes, manufacturers conduct force testing on products to measure the difficulty or ease with which something can be pulled, pushed, compressed, bent, peeled, cut, etc. Measuring the force required to perform these actions on products can determine whether they meet design requirements and are “fit for purpose.”
An example of manufacturer testing is tensile testing, which can be performed on a wide range of materials, such as plastics, composites, and metals. In this testing, the manufacturer applies force to the product until it breaks, providing them with valuable information regarding the material’s properties, including its yield strength, ultimate tensile strength, and ductility. This allows companies to determine if a material will have sufficient durability in an application.
Summary
This article presented force measurement devices, explained them, and discussed their various types and characteristics. To learn more about force measurement devices, contact a Xometry representative.
Xometry provides a wide range of manufacturing capabilities and other value-added services for all of your prototyping and production needs. Visit our website to learn more or to request a free, no-obligation quote.
Disclaimer
The content appearing on this webpage is for informational purposes only. Xometry makes no representation or warranty of any kind, be it expressed or implied, as to the accuracy, completeness, or validity of the information. Any performance parameters, geometric tolerances, specific design features, quality and types of materials, or processes should not be inferred to represent what will be delivered by third-party suppliers or manufacturers through Xometry’s network. Buyers seeking quotes for parts are responsible for defining the specific requirements for those parts. Please refer to our terms and conditions for more information.
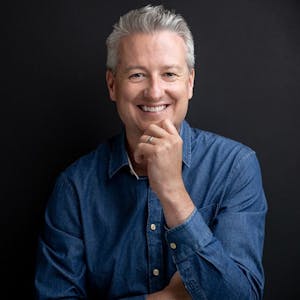