Hastelloy® metals are considered to be high-performance, corrosion-resistant alloys. They are often referred to as "superalloys." They comprise a diverse range of over two dozen alloys, each tailored for specific purposes based on its unique elemental composition. What makes Hastelloys exceptional is their ability to survive in extremely corrosive environments, outperforming stainless steel in challenging conditions. Hastelloys have excellent fabrication characteristics, remain thermally stable (they maintain their microstructural integrity and mechanical properties at high temperatures), and demonstrate remarkable resistance to acids such as sulfuric and hydrochloric. These qualities make Hastelloy metals a popular choice for demanding applications in the chemical processing and aerospace industries, among others.
This article focuses specifically on Hastelloys: what they are, their compositions, properties, applications, advantages, disadvantages, and more.
What Is Hastelloy?
Hastelloy is the trade name given to a group of corrosion-resistant nickel-based alloys. In addition to nickel, these alloys also contain other elements like molybdenum and chromium. These alloys are especially known for their corrosion resistance, good fabricability, and medium- to high-temperature resistance (depending on the alloy grade). Hastelloy alloys are typically metastable within their normal operating temperature range (room temperature to approximately 427 °C). This metastability is characterized by a gamma (FCC) phase microstructure, achieved through solution annealing and rapid cooling. While designed to resist precipitation of second phases during short-term thermal excursions above 500 °C, long-term exposure reveals their equilibrium, multiple-phase nature.
What Is the Other Term for Hastelloy Metals?
There isn't another single term that universally represents all the alloys within the Hastelloy family. However, Hastelloy metal is a type of superalloy. This term refers to a group of high-performance alloys characterized by their excellent mechanical strength, resistance to thermal creep deformation, and outstanding corrosion resistance, especially at high temperatures. Each specific alloy within the Hastelloy family, such as Hastelloy C-276, Hastelloy C-22, and Hastelloy B-2, represents a unique composition within this broader category of superalloys.
What Is the Origin of Hastelloys?
Hastelloy is a registered trademark owned by Haynes International, Inc., an American-based company specializing in the development and production of high-performance alloys. The nickel-based superalloy industry had its beginnings in 1921 when a patent was secured for a nickel-molybdenum composition range. This laid the foundation for the gradual development of the entire Hastelloy family of alloys, known for their ability to resist corrosion and withstand high temperatures. The first metals called by the Hastelloy name, Hastelloy A and Hastelloy B, were introduced shortly thereafter. The unique composition of Hastelloy B is still in use today.
In 1926, Hastelloy C alloy was created. The latest version, Hastelloy C-2000 alloy, is widely used in the chemical process industry. Around the same time, Hastelloy D alloy, which is a nickel-silicon-copper alloy, was developed. Today, the latest variation, known as Hastelloy D-205 alloy, is employed in chemical plants dealing with hot and highly concentrated sulfuric acid.
What Are Hastelloy Metals Made Of?
Hastelloys are nickel-based alloys that typically consist of about 40-70% nickel. Other metals, such as chromium (1-33%) and molybdenum (5-30%) are added to increase the metal’s corrosion resistance. Iron may also be added in percentages ranging from 0 to 18%. Other components that might also be included in varying percentages include: tungsten, carbon, cobalt, zirconium, titanium, aluminum, copper, and manganese. The exact chemical composition of some common Hastelloy grades varies depending on the desired characteristics.
How Are Hastelloy Metals Made?
Hastelloys are manufactured by blending pure elements in a liquid state to achieve specific chemical compositions for various grades. The mixture typically includes nickel, chromium, molybdenum, and iron, with additional elements like tungsten, vanadium, carbon, and titanium depending on the grade. After combining the elements, the alloy undergoes smelting at high temperatures to ensure uniform mixing. The molten Hastelloy is then cast into forms such as ingots. Following casting, the material undergoes forming processes like forging or rolling, and heat treatment to optimize mechanical properties. Final machining shapes the alloy for specific applications.
What Is the Color of Hastelloy Metals?
Hastelloys typically have a silver-gray metallic color.
What Does a Hastelloy Metal Look Like?
Hastelloys do not have a distinct visual appearance that sets them apart from other metals simply by sight. In their finished form, they typically look like any other grayish metallic alloy, and their appearance can vary somewhat based on the specific grade. These alloys are often silvery or metallic in color, similar to other nickel-based alloys. The specific grade and surface finish (such as polished or matte) may impact its visual appearance, but these variations are subtle.
What Are the Different Hastelloy Grades?
There are several types and grades of Hastelloys, which are set apart by differences in their chemical compositions. Common Hastelloy grades include:
- B-Type Hastelloys: Known for their high molybdenum content, B-type Hastelloys can withstand extreme reducing environments. Hastelloy B-2 (UNS N10665) and Hastelloy B-3 (UNS N10675) are two grades of Hastelloy that fall into this category. B-2 offers exceptional corrosion resistance to hydrochloric acids but is less effective against oxidizing agents, whereas B-3 demonstrates exceptional resistance to pitting corrosion and has excellent thermal stability compared to B-2 alloys.
- C-Type Hastelloys: The C-type Hastelloys, which are based on a nickel alloy, are characterized by their high percentages of nickel, chromium, and molybdenum. Compared to the B-type alloys, the C-type alloys contain roughly half the amount of molybdenum but a significantly higher percentage of chromium. This increased chromium content enhances their formability. Additionally, C-type Hastelloys include a minor addition of iron, roughly double that of the B alloys, which is believed to facilitate the use of higher amounts of chromium, possibly by enhancing solubility or stability within the alloy. Some popular grades in this category include: Hastelloy C-4 (UNS N06455), Hastelloy C-22 (UNS N06022), and Hastelloy C-276 (UNS N10276). C-4 exhibits high ductility and corrosion resistance and it is suitable for deep drawing applications. C-22, on the other hand, is recognized for its weldability and finds application in desulfurization systems and pharmaceutical reaction vessels. C-276 is a very well-known grade of Hastelloy that is mainly found in petrochemical applications. It offers excellent resistance to pitting, intergranular corrosion, and oxidizing agents. Hastelloy C-2000 (UNS N06200) is a unique member of the C-type group due to its deliberate copper addition. This copper content enhances the alloy's resistance to sulfuric acid, making it distinct from the nickel-chromium-molybdenum materials.
- G-Type Hastelloys: G alloys are distinguished by their low Mo content compared to other Hastelloys. They also have ten times as much Si as the others., and their carbon content is considerably higher. G-type Hastelloys are weldable using various techniques. Two key members in this group are Hastelloy G-3 (UNS N06985) and Hastelloy G-30 (UNS N06030). G-3 exhibits good corrosion resistance and is known for its resistance to oxidation and stress corrosion cracking. It also excels in environments mixed with commercial phosphoric acid and highly oxidizing acid media.
- Hastelloy X: Hastelloy X, also known as Hastelloy HX, is a nickel-based superalloy distinguished by its diverse composition, including nickel, chromium, molybdenum, cobalt, and tungsten, along with additional elements like iron and manganese. This unique blend provides excellent high-temperature strength and superior oxidation resistance. Hastelloy X is primarily used in industrial furnaces and gas turbine engines, where its ability to withstand high temperatures and maintain structural integrity is essential. Its versatility and reliability make it a valuable material for high-heat applications in aerospace and power generation industries.
- Hastelloy N: With a composition of 71% nickel, 16% molybdenum, and 7% chromium, Hastelloy N excels in higher temperature oxidation resistance, making it a preferred choice in industrial applications such as chemical process equipment.
What Are the Chemical Properties of Hastelloys?
The chemical properties of the Hastelloys are as follows:
- Grades like C-276, for example, have good pitting and crevice corrosion resistance and are resistant to stress corrosion cracking.
- High chemical resistance including acids, alkalis, and salts.
- Maintains oxidation resistance at high temperatures.
- Melting temperature range of 1260-1400 °C.
What Are the Physical Properties of Hastelloys?
The physical properties of various Hastelloy grades are outlined in Table 1 below:
Type | Density (g/cm3) | Melting Point (°C) | Tensile Strength (MPa) | Yield Strength (0.2 % Offset) (MPa) | Elongation (%) |
---|---|---|---|---|---|
Type B2 | Density (g/cm3) 9.2 | Melting Point (°C) 1370 | Tensile Strength (MPa) 760 | Yield Strength (0.2 % Offset) (MPa) 350 | Elongation (%) 40 |
Type B3 | Density (g/cm3) 9.2 | Melting Point (°C) 1370 | Tensile Strength (MPa) 760 | Yield Strength (0.2 % Offset) (MPa) 350 | Elongation (%) 40 |
Type C4 | Density (g/cm3) 8.64 | Melting Point (°C) 1350-1400 | Tensile Strength (MPa) 783 | Yield Strength (0.2 % Offset) (MPa) 365 | Elongation (%) 55 |
Type C22 | Density (g/cm3) 8.69 | Melting Point (°C) 1399 | Tensile Strength (MPa) 690 | Yield Strength (0.2 % Offset) (MPa) 310 | Elongation (%) 45 |
Type C276 | Density (g/cm3) 8.89 | Melting Point (°C) 1370 | Tensile Strength (MPa) 790 | Yield Strength (0.2 % Offset) (MPa) 355 | Elongation (%) 40 |
Type X | Density (g/cm3) 8.22 | Melting Point (°C) 1355 | Tensile Strength (MPa) 655 | Yield Strength (0.2 % Offset) (MPa) 240 | Elongation (%) 35 |
Table Credit: https://www.amardeepsteel.com/blog/SpecificBlog/inconel-hastelloy/inconel-vs-hastelloy.html
Are Hastelloys Stronger Than Stainless Steel?
No. Stainless steels are slightly stronger than Hastelloys, but both metals display very good strength-to-weight ratios. Hastelloy does have better corrosion resistance, which makes it a better choice for use in highly corrosive environments or with highly corrosive materials.
Are Hastelloy Metals Magnetic?
No, the Hastellloys are non-magnetic. These nickel-based superalloys are designed for high corrosion resistance and strength, and their composition typically results in non-magnetic properties.
Can You Laser Weld Hastelloy Metals?
Yes, the Hastelloys can be laser welded. One study found that Hastelloy C-276 can be laser-welded effectively and safely, while another study found that Hastelloy X can be laser-welded with continuous laser welding, but experiences cracking and faulty welds when pulsed-laser welding was applied. Care should be taken to use the correct laser welding technique and parameters for the specific grade of Hastelloy.
To learn more, see our full guide on How Does Laser Welding Work.
Do Hastelloys Rust?
No, Hastelloys do not rust because they are not iron-based alloys. Hastelloys are specifically designed to be extremely corrosion resistant, showing better corrosion resistance than stainless steel, for example. This corrosion resistance makes Hastelloy a suitable candidate for applications where it would be outdoors or in corrosive environments. Hastelloy is typically resistant to strong acids, strong alkalis, chlorides, nitrates, hydroxides, sulfates, and more.
What Are the Applications of Hastelloys?
The following lists some applications of Hastelloy metals:
1. Liners
Hastelloy C-276 and C-22 are often used as linings for chemical processing equipment such as reactors, storage tanks, and heat exchangers. These linings are particularly valuable in environments with highly corrosive substances like acids, chlorides, or sulfur compounds. By lining the interior surfaces, the Hastelloy provides excellent corrosion and oxidation resistance, protecting the equipment from damage.
This approach is cost-effective because it allows for the corrosion resistance benefits of high-performance Hastelloy without the need to construct the entire piece of equipment from it. Additionally, Hastelloy linings can be used to retrofit existing equipment, significantly improving its resistance to corrosion and extending its service life, making them a practical solution in the chemical and petrochemical industries.
2. Pressure Vessels
Pressure vessels in the chemical, petrochemical, and manufacturing industries are used to contain and manage both liquids and gasses under pressure. These vessels are essential for various processes, including storing gasses at high pressure, keeping volatile liquids from vaporizing by applying pressure to the vapor space and maintaining substances in a liquid state that would otherwise be gaseous under normal conditions.
In chemical processing, pressure vessels play a critical role in reaction processes, separation processes, and storage. They are designed to operate safely at specific pressures and temperatures, depending on the nature of the substances they contain. The design and material selection for these vessels are crucial for ensuring safety, efficiency, and longevity, especially when dealing with corrosive or volatile substances. Hastelloys, with their extremely high corrosion resistance, can be used to manufacture pressure vessels for these corrosive liquids and can be used for decades with proper maintenance. The durability and long lifespan of Hastelloy pressure vessels make them cost-effective over their lifetimes. Hastelloy C-276 and Hastelloy B-3 are commonly used for pressure vessels.
3. Turbine Combustors
Turbine combustors, or burners, are the components where combustion occurs in gas turbine engines. These combustors are subjected to extreme temperatures, as well as highly corrosive fuels. Hastelloy X is commonly used for turbine combustors in gas turbine engines because it's really strong at high temperatures and resists corrosion extremely well. It also has excellent oxidation resistance at extreme temperatures. This makes it ideal for handling the high-temperature and corrosive conditions typical in these engine components. These features help make it durable, especially when it's used in well-designed components. When engineers use Hastelloy correctly in their designs, it helps ensure that these parts of the engine can handle the intense heat and corrosive fuels they're exposed to, and last a long time.
4. Pipes or Valves
Pipes and valves are part of the equipment used in every petrochemical and chemical processing operation. Many of the chemicals that are transported through these pipelines are highly corrosive. Hastelloy piping has high corrosion resistance and very good durability, which make it an ideal choice for safely transporting and controlling the flow of these corrosive chemicals. For instance, Hastelloy C-276 is commonly used in these applications.
Hastelloy C-276 is particularly well-suited for handling a wide range of aggressive chemicals due to its outstanding resistance to pitting, crevice corrosion, and stress-corrosion cracking. This alloy's unique composition, including nickel, molybdenum, and chromium, provides excellent performance in environments where other materials might fail, such as in the presence of chlorides, sulfur compounds, and acidic media.
How Can Xometry Help You With Your Hastelloy Needs?
Xometry is a manufacturing marketplace that connects businesses with a network of qualified manufacturers offering a range of services. Whether you require precision machining, 3D printing, sheet metal fabrication, or other manufacturing processes, Xometry's platform allows you to access a variety of manufacturing capabilities. Simply upload your Hastelloy project specifications, and Xometry provides instant quotes, lead times, and the option to choose from a diverse pool of manufacturers.
What Are the Disadvantages of Hastelloys?
Some of the disadvantages of the Hastelloy family of metals include the following:
- They are generally more expensive than high-performance alloys, such as stainless steel.
- Machining difficulties with Hastelloy grades like C-276 arise from properties such as low thermal conductivity, work hardening tendency, and the alloy's propensity to adhere to cutting tools. The low thermal conductivity leads to high heat at the cutting interface, affecting tool life. Hastelloy's rapid work hardening during machining makes it harder to cut as the process progresses
- instead of reacting chemically with tool materials, Hastelloy tends to adhere to them due to friction, causing built-up edge and tool wear. Specialized techniques and tools are often required to overcome issues such as: heating of the interface between tool and workpiece, increased tool wear, and work hardening, resulting in the alloy becoming stronger/harder as machining proceeds.
What Are the Advantages of Hastelloys?
Some of the advantages and benefits of using a Hastelloy include:
- Performs well in extremely corrosive and high-stress environments.
- Have good formability. This means that the alloy responds well to metal spinning and can be used to produce strong and rigid parts that are of high quality and suitable for use in demanding applications.
- Resistant to corrosion and a wide range of chemical substances, including: salts, strong alkalis, and strong acids.
- Maintains its strength at elevated temperatures, making it suitable for applications in high-temperature environments, such as gas turbine components.
- Offers excellent resistance to stress corrosion cracking and pitting and crevice corrosion.
How Much Does Hastelloy Cost?
Hastelloy is considered to be an expensive alloy due to its composition. Hastelloys are nickel-based, and nickel is expensive, so the even more costly alloying elements (chromium, molybdenum, tungsten, cobalt, etc.) add to an already pricey starting point. The cost of a Hastelloy can vary quite a bit for different grades, but a general ballpark price for this alloy is between $30 and $55 per kg.
Do Hastelloys Cost More Than Inconels®?
No. Inconel® is generally more expensive than Hastelloy. This is due to the higher chromium content of Inconel.
Is Hastelloy a Rare Metal?
No, Hastelloys are not considered to be rare alloys, but they are specialized high-performance materials made from a combination of various elements — primarily nickel, molybdenum, chromium, and other minor additions. used mainly in industries that require exceptional resistance to corrosion and medium to high temperatures. Some of the alloying elements in Hastelloys are considered to be more “rare” (less abundant) than others. For example, molybdenum is a less common element than nickel, and its inclusion in certain Hastelloy grades contributes significantly to the overall cost of the alloy.
What Is the Difference Between Hastelloys and Monel®?
The difference between Hastelloy and Monel® are mainly their properties and applications. Hastelloy and Monel® are the names of two popular families of nickel-based alloys which are very different in terms of properties and applications. Monel is a nickel-copper alloy, whereas Hastelloy is a nickel-based alloy with a composition including molybdenum and chromium, among other elements. Both Monels and Hastelloys perform well in corrosive environments, but Hastelloys have the added ability to perform well in higher-temperature conditions. They are also much stronger than the Monel. They can withstand pressures up to 10 times that of Monel. Moreover, Hastelloy is more suited for acidic environments, whereas Monel typically finds uses in marine applications. Hastelloys are resistant to a range of corrosive acids, including sulfuric acid, nitric acid, hydrochloric acid, hydrofluoric acid, and chromic acid. Their resistance to sulfuric acid is especially significant, as few alloys can withstand the corrosive effects of this acid. Monel alloys also leverage the properties of copper to combat biofouling. Copper has natural antimicrobial properties, making it less conducive to the growth of microorganisms. When used in Monel alloys, copper imparts these antimicrobial properties to the alloy, helping to prevent or reduce the accumulation of biological organisms on the surface. This characteristic is particularly beneficial in brine solutions, which are essentially concentrated saltwater environments.
Summary
This article presented Hastelloy metals, explained them, and discussed their composition and properties. To learn more about Hastelloy metals, contact a Xometry representative.
Xometry provides a wide range of manufacturing capabilities and other value-added services for all of your prototyping and production needs. Visit our website to learn more or to request a free, no-obligation quote.
Copyright and Trademark Notices
- HASTELLOY® is a registered trademark of Haynes International, Inc.
- Inconel® and Monel® are registered trademarks of Special Metals Corporation.
Disclaimer
The content appearing on this webpage is for informational purposes only. Xometry makes no representation or warranty of any kind, be it expressed or implied, as to the accuracy, completeness, or validity of the information. Any performance parameters, geometric tolerances, specific design features, quality and types of materials, or processes should not be inferred to represent what will be delivered by third-party suppliers or manufacturers through Xometry’s network. Buyers seeking quotes for parts are responsible for defining the specific requirements for those parts. Please refer to our terms and conditions for more information.
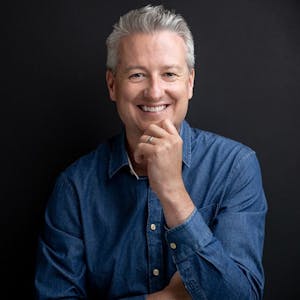