Monel® and Hastelloy® are two unique alloys that are well-known for their remarkable resistance to corrosion in harsh settings. Monel is made mostly of nickel and copper. It is incredibly strong and resistant to acidic environments. Conversely, the nickel-chromium-molybdenum alloy Hastelloy performs exceptionally well in corrosive and high-temperature environments.
Hastelloy is praised for its resistance to a wider spectrum of corrosive chemicals than Monel, which is valued for its versatility. It is essential to comprehend the subtle differences between these materials to choose the best solution for a range of industrial uses.
This article will compare Monel vs Hastelloy in terms of composition, applications, types, advantages, and disadvantages.
What Is Monel?
Monel is an alloy that combines nickel and copper with trace elements like iron and manganese. Surpassing the strength of pure nickel, Monel exhibits resilience to corrosion from various agents, including seawater. Its exceptional versatility enables easy fabrication through hot- and cold-working, machining, and welding. Monel stands out in applications requiring both robust corrosion resistance and mechanical strength, making it a crucial material in diverse industries.
What Is Monel Made Of?
Monel is composed of approximately 66% nickel, 31.5% copper, and minor proportions of iron, manganese, carbon, and silicon. Monel gains exceptional strength and resistance to corrosion from this combination, which makes it a useful material for a variety of industrial applications. The alloy is very adaptive and resilient in harsh settings because of its unique composition.
How Is Monel Made?
Monel metal, characterized by a composition of 0.08–0.15% carbon, 1.8–2.2% iron, 0.08–0.12% silicon, 1.3–1.8% manganese, 31.5–33.5% copper, and the remainder as nickel, undergoes a meticulous production process. After batching and pre-treatment, the raw materials undergo specific baking steps. Subsequently, melting occurs at 1,400–1,450 °C, incorporating nickel-magnesium alloy. The refining process, involving argon-gas protection, follows. Finally, thermometric continuous casting, facilitated by industrial equipment, yields Monel metal ingot casting. The entire process emphasizes controlled conditions to ensure precise alloy composition and quality.
What Are the Different Types of Monel?
One of the commercial varieties of Monel is Alloy 400, which is known for not corroding in maritime conditions. Alloy 400 can also be free-machined to create Alloy R-405. Precipitation-hardening of Monel creates Alloy 450 (or Monel 450). Alloy 401 provides increased hardness and strength. A copper-nickel alloy with a reputation for being corrosion-resistant in marine conditions is Monel 404, whereas alloy K-500 combines strength and resistance to corrosion. Every variety serves certain purposes, demonstrating Monel's flexibility in a range of industrial settings.
What Are the Advantages of Monel?
The advantages of Monel include:
- Maintains an appealing aesthetic, contributing to its suitability in various industries.
- The term ductility describes the capacity of Monel to undergo shaping or deformation without breaking, which makes manufacturing operations easier.
- Compatible with welding, brazing, and soldering techniques, which facilitates joining processes, ensuring efficient fabrication.
- Can be used in load-bearing and structural applications because of its high mechanical qualities.
- Exhibits exceptional durability in the presence of corrosive substances like acids and alkalis, making it suitable for applications in challenging chemical environments.
What Are the Disadvantages of Monel?
The disadvantages of Monel include:
- Monel's higher density, compared to other materials, is a drawback in weight-sensitive applications.
- Due to high nickel content, Monel alloys pose challenges in welding, with a tendency to crack during the process.
- Is costlier than materials like stainless steel and aluminum, making Monel less favorable in budget-conscious applications.
- High strength and toughness make Monel alloys challenging to machine, leading to tool wear and difficulty in achieving tight tolerances.
Is Monel Better Than Hastelloy?
No. Hastelloy and Monel have distinct functions. While Monel, an alloy of nickel and copper, is excellent at resisting corrosion, it might not be as adaptable to harsh conditions as Hastelloy. Due to its greater corrosion resistance across a wider range of chemicals and temperatures, Hastelloy, an alloy based on nickel, is commonly employed for demanding applications.
What Is Hastelloy?
Hastelloy is a corrosion-resistant nickel metal alloy, enhanced with molybdenum and chromium. Its various grades are tailored for specific properties, offering excellent corrosion resistance, good weldability, and resistance to oxidizing agents and acids. The high molybdenum content enhances workability, making Hastelloy preferable in severely corrosive environments over other specialty metals like Incoloy®.
What Is Hastelloy Made Of?
The main elements of Hastelloy are 13% molybdenum, 22% chromium, and 56% nickel. It also contains iron in varying degrees, depending on the variant; and might also have trace levels of cobalt and tungsten. Hastelloy's outstanding resistance to corrosion is a result of its exact alloy composition (for each variant).
How Is Hastelloy Made?
The production of Hastelloy involves a multi-step process. It begins with smelting, where strict control over the chemical composition, including nickel (about 56%), molybdenum (13–17%), chromium (14.5–16.5%), and iron (4–7%), ensures optimal performance for every alloy variant. Different variants may have varying percentages to meet specific application needs. Casting follows, utilizing precise parameters to achieve a uniform, defect-free structure. Heat treatment adjusts the microstructure and mechanical properties. Finally, processing involves cold and hot working, selected based on specific application requirements and further contributing to Hastelloy's exceptional properties.
What Are the Different Types of Hastelloy?
Hastelloy refers to a family of nickel-based alloys that are resistant to corrosion and are designed for particular uses. Molybdenum-rich Hastelloy B-3 is resistant to air pressure and acids. While C-4 exhibits corrosion resistance in chloride conditions, Hastelloy C excels in radiation resistance. While C-276 stands out for its ability to withstand a variety of chemical processes, making it perfect for hostile environments. C-22 is an excellent all-around alloy with remarkable corrosion resistance.
What Are the Advantages of Hastelloy?
The advantages of Hastelloy include:
- The alloy's ease of welding simplifies manufacturing processes, allowing for efficient joining of components without compromising the material's corrosion-resistant properties.
- Provides remarkable resistance to localized corrosion, preventing weaknesses in certain regions and ensuring reliability in important parts subjected to corrosive substances.
- Strong resistance to uniform assault in Hastelloy provides durability in corrosive conditions, guarding against surface erosion and preserving structural integrity even in abrasive chemical exposures.
- The capacity to create complex and long-lasting components is made possible by Hastelloy's enhanced versatility through compatibility with fabrication procedures. Its ability to change in shape enhances the accuracy and efficiency of production processes.
- As a result of Hastelloy's exceptional resistance to stress corrosion cracking, the material integrity is protected from the initiation and spread of cracks that could undermine it under mechanical stress and corrosive environments.
What Are the Disadvantages of Hastelloy?
The disadvantages of Hastelloy include:
- Exposure to high stress, as in welding or machining, can lead to stress cracking and potential component failure.
- Finding supplies for Hastelloy can be difficult due to its relatively high cost, particularly in industries such as the chemical industry.
- Incompatible with lead or zinc, restricting its use in applications involving these materials.
- Applications that demand extensive machining are not suitable for Hastelloy due to the tendency to bring about hardness and brittleness.
Is Hastelloy Better Than Monel?
No. While Hastelloy excels in corrosion resistance, Monel has its merits, offering high strength and toughness. Monel is suitable for specific environments, such as marine applications. The choice between Hastelloy and Monel depends on the specific needs of a project, considering factors like strength, corrosion resistance, and cost.
How To Choose Between Monel and Hastelloy?
When choosing between Hastelloy and Monel, take into account the circumstances in which Hastelloy performs best, especially when managing harsh environments such as chemical processing. On the other hand, choose Monel in environments that are marine or when sturdiness and resilience are important factors. Examine project-specific needs and consider factors including: strength, corrosion resistance, and cost when selecting one of these alloys.
What Are the Properties of Monel and Hastelloy?
Table 1 shows the comparison between the properties of Monel and Hastelloy:
Property | Monel | Hastelloy |
---|---|---|
Property Corrosion Resistance | Monel Excellent | Hastelloy Excellent |
Property Tensile Strength | Monel 550–1,100 MPa | Hastelloy 690–783 Mpa |
Property Melting Point | Monel 1,300–1,350 °C | Hastelloy 1,323–1,371 °C |
Property Density | Monel 8.80 g/cm³ | Hastelloy 8.89 g/cm³ |
Property Magnetism | Monel Non-magnetic | Hastelloy Non-magnetic |
Can You Laser Weld Monel and Hastelloy?
Yes, you can laser weld Monel and Hastelloy. Research indicates that with precise control of pulse energy, especially through a Nd:YAG laser, it's possible to weld thin foils of Monel 400 and Hastelloy C-276. This control allows for effective welding by managing dilution rates.
Can You Laser-Cut Monel and Hastelloy?
Yes, Monel 400 can be laser-cut with appropriate cutting speeds. Hastelloy C-276 is often cut using YAG lasers, showcasing its laser-cutting compatibility. The key lies in adjusting cutting speeds for each material, ensuring efficient and precise results.
Is Monel Metal Toxic?
Yes, it is toxic when activities like melting or processes generating metal dust occur. In solid form, Monel doesn't pose significant health risks. But during some tasks, breathing in metal dust, smoke, or fumes can introduce dangerous levels into the body, requiring quick action like getting fresh air and/or medical help.
How To Identify Monel and Hastelloy?
To differentiate between Monel and Hastelloy, obtaining a mill test report (MTR) is important. To assure product quality, manufacturers often provide MTRs. These studies provide a thorough examination of the material, including information on its mechanical and physical characteristics and elemental makeup. Based on exact analytical data, using MTRs ensures correct identification even in cases in which visual inspection may not be conclusive.
What Are the Applications of Monel and Hastelloy?
Monel finds its niche in marine and chemical processing, while Hastelloy specializes in high-temperature applications, including gas path components and nuclear reactors. Each alloy serves distinct purposes based on its unique material properties. Applications of Monel are:
- Frames of eyeglasses.
- Valves and pumps.
- Heat exchangers.
- Shafts, fittings, and fasteners.
- Marine engineering.
- Chemical and hydrocarbon processing equipment.
- Metal instruments.
Applications of Hastelloy are:
- Pipes and valves in the chemical industry.
- High-temperature gas path components (e.g., liners, flame holders, turbine combustors).
- Pressure vessels in some nuclear reactors.
- Chemical reactors.
Is Monel Suitable for Shipbuilding?
Yes, Monel is suitable for shipbuilding. In the shipbuilding industry, Monel 400 finds application in: pump shafts, propellers, valve stems, heat exchangers, gasoline tanks, as well as nuclear engineering components. Its resilience to corrosion, exceptional strength, and long-lasting nature make it a reliable option.
How Much Do Monel and Hastelloy Cost?
Hastelloy costs $1.75 per pound, while Monel ranges in price from $2.50 to $3.00 per pound, making it currently more costly than Hastelloy. The disparity in price is a reflection of the two alloys' different manufacturing procedures, material compositions, and physical characteristics.
Summary
This article presented Monel and Hastelloy, explained each of them, and discussed their key differences. To learn more about both Monel and Hastelloy, contact a Xometry representative.
Xometry provides a wide range of manufacturing capabilities and other value-added services for all of your prototyping and production needs. Visit our website to learn more or to request a free, no-obligation quote.
Copyright and Trademark Notice
- Monel® and Incoloy® are trademarks of Special Metals Corporation
- HASTELLOY® is a trademark of Haynes International, Inc.
Disclaimer
The content appearing on this webpage is for informational purposes only. Xometry makes no representation or warranty of any kind, be it expressed or implied, as to the accuracy, completeness, or validity of the information. Any performance parameters, geometric tolerances, specific design features, quality and types of materials, or processes should not be inferred to represent what will be delivered by third-party suppliers or manufacturers through Xometry’s network. Buyers seeking quotes for parts are responsible for defining the specific requirements for those parts. Please refer to our terms and conditions for more information.
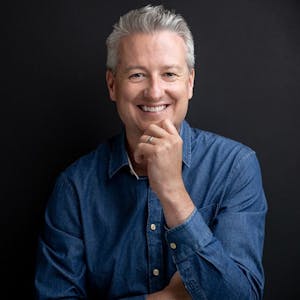