HDPE (high-density polyethylene) is a common thermoplastic built from polyethylene, the highest production volume plastic in the world. HDPE has an excellent strength-to-weight ratio as well as good chemical resistance. HDPE is widely used for water tanks, food packaging, and piping. HDPE can be manufactured using extrusion, injection molding, and rotomolding.
PTFE (polytetrafluoroethylene) is an engineered thermoplastic with exceptional chemical and thermal resistance as well as a very low coefficient of friction. PTFE is often used in applications that require corrosion resistance, such as valve components like the balls in a ball valve or the flap in a butterfly valve. PTFE is typically processed using compression molding. This article will compare the properties, costs, and common applications of HDPE and PTFE.
What is HDPE?
HDPE (high-density polyethylene), sometimes referred to as PE-HD (polyethylene-high-density), is a semicrystalline thermoplastic homopolymer with limited or no branching off the main molecular chain. HDPE forms part of the PE (polyethylene) group of plastics, which consists of LDPE (low-density polyethylene), LLDPE (linear low-density polyethylene), and UHMWPE (ultra-high molecular weight polyethylene).
HDPE is produced from petroleum products through a polymerization process. Ethylene can be polymerized into polyethylene only in the presence of a suitable catalyst, such as metallocene or Ziegler-Natta-type catalysts. Once polymerized, the HDPE is extruded into long filaments which are then cut into pellets. These pellets can be processed using fabrication techniques, such as rotomolding or extrusion.
HDPE has an excellent strength-to-weight ratio. It can be fabricated by extrusion, injection molding, rotomolding, and CNC machining. It can also be joined using plastic welding techniques. HDPE is often used for water tanks, piping, shopping bags, and food packaging. For more information, see our guide on High-Density Polyethylene (HDPE).
What is PTFE?
PTFE (Polytetrafluoroethylene) is a semicrystalline fluoropolymer-based thermoplastic. It is made up of just carbon and fluorine atoms. PTFE is often referred to by its Dupont™ trade name, Teflon®. PTFE has one of the highest temperature resistances of common engineering plastics. It is also exceptionally corrosion-resistant. In addition, PTFE has a very low coefficient of friction, which makes it popular for cookware coatings. PTFE absorbs virtually no moisture (it is hydrophobic).
PTFE can be synthesized from the tetrafluoroethylene (TFE) monomer via free radical addition polymerization. During the polymerization process, a linear molecular chain consisting of a carbon backbone surrounded by fluorine atoms forms. These fluorine atoms behave as a boundary layer that prevents chemical attack on the carbon, making PTFE exceptionally corrosion resistant.
Fillers such as glass fibers are often added to PTFE to improve its mechanical properties. Creep resistance (resistance to deformation under low stress at high temperatures) of PTFE is greatly improved by the addition of glass fiber fillers, making it suitable for use at high temperatures. Carbon can be added to improve hardness and wear resistance. To improve thermal and electrical conductivity, small amounts of bronze powder can be added to PTFE. Up to 40% by volume of the additives mentioned above can be included in the formulation. Although up to 40% by volume can be additive materials, a balance must be struck between the improvement of the desired special property and the potential for degradation of other properties of PTFE because of the dilution of the original material.
PTFE is not typically processed using standard thermoforming processes due to its high melting temperature. Instead, compression molding is the most common method used to fabricate parts and coatings from PTFE.
HDPE vs. PTFE: Applications and Uses
HDPE is highly flexible with an excellent strength-to-weight ratio. Some typical applications are listed below:
- Milk cartons, squeeze bottles, bottle caps, and beverage bottles
- Pipes and fittings, chemical storage tanks, and water tanks
- Shopping bags, toys, and playground equipment
- Fibers and textiles
- Vehicle fuel tanks
PTFE have excellent thermal and corrosion resistance with a very low coefficient of friction. Some typical applications are listed below:
- Gaskets
- Valve parts
- Thread tape for pipe fittings
- O-rings
- Bearings and bushings
- Non-stick coatings for cookware
HDPE vs. PTFE: Physical Properties
Table 1 below lists some key physical properties of HDPE and PTFE:
HDPE | PTFE | |
---|---|---|
HDPE Melting Point (°C) | PTFE 120 - 140 | 327 |
HDPE Density (g/cm3) | PTFE 0.96 | 2.15 |
HDPE Ultimate Tensile Strength (MPa) | PTFE 31.7 | 10.3 - 20.6 |
HDPE Water Absorption (ASTM D570) (% by weight) | PTFE 0.1 | < 0.01 |
HDPE Chemical Resistance | PTFE Resistant to both dilute and concentrated acids (e.g., hydrochloric acid), as well as some reducing and oxidizing agents. | Excellent resistance to most chemicals. However, PTFE is not resistant to dissolved alkali metals, fluorine gas, or fluorine compounds. |
HDPE Heat Deflection Temperature (°C) @ 0.45 MPa | PTFE 90 | 120 |
HDPE Tensile Elongation (%) | PTFE 600 | 100 - 200 |
HDPE Dielectric Strength (kV/mm) | PTFE 17 - 24 | 20 - 48 |
Table Credit: https://www.curbellplastics.com/
It must be noted that PTFE has a much higher heat deflection temperature and corrosion resistance whereas HDPE has an excellent strength-to-weight ratio.
HDPE vs. PTFE: Recyclability and Sustainability
HDPE is theoretically recyclable due to its thermoplastic nature as it can be melted and will harden without any significant loss in properties. Items made of HDPE can be identified by the recycling symbol stamped into the product: the number “2” enclosed within a triangle. HDPE can be recycled up to 10 times.
PTFE cannot be recycled the way standard thermoplastics can. It needs to be either pulverized or irradiated to break it down into a fine powder. This powder can then be formed into bars and rods through a heat treatment process. PTFE can only be recycled once. Despite their theoretical recyclability, the vast majority of plastics, including HDPE and PTFE, are not recycled, and simply end up in landfills or in the ocean.
HDPE and PTFE are both produced from non-renewable crude oil and are therefore not regarded as sustainable. In addition to this, PTFE makes use of a carcinogenic compound during manufacturing called Perfluorooctanoic acid (PFOA).
HDPE vs. PTFE: Cost
HDPE is a subset of polyethylene which is the most popular commodity plastic worldwide at a bulk cost of $1.22 per kilogram. PTFE is significantly more expensive than HDPE and has a bulk cost of $10.33 per kilogram. PTFE is an engineering thermoplastic whereas HDPE is a commodity plastic. PTFE is more difficult to produce and process and is therefore more costly.
Alternative Materials to HDPE and PTFE
Two suitable alternatives for HDPE are polypropylene and PVC (polyvinyl chloride) as both of these materials provide good corrosion resistance and are both used in applications in contact with acids and bases. PTFE has a unique combination of thermal and corrosion-resistant properties, making it difficult to replace. However, PCTFE (polychlorotrifluoroethylene) or FEP (fluorinated ethylene propylene) can be used as alternatives in some cases.
Summary
This article presented HDPE and PTFE, explained what they are, and discussed the properties of each material. To learn more about HDPE and PTFE, contact a Xometry representative.
Xometry provides a wide range of manufacturing capabilities and other value-added services for all of your prototyping and production needs. Visit our website to learn more or to request a free, no-obligation quote.
Copyright and Trademark Notices
- DuPont™ and Teflon® are registered trademarks of Dupont Polymers, Inc.
Disclaimer
The content appearing on this webpage is for informational purposes only. Xometry makes no representation or warranty of any kind, be it expressed or implied, as to the accuracy, completeness, or validity of the information. Any performance parameters, geometric tolerances, specific design features, quality and types of materials, or processes should not be inferred to represent what will be delivered by third-party suppliers or manufacturers through Xometry’s network. Buyers seeking quotes for parts are responsible for defining the specific requirements for those parts. Please refer to our terms and conditions for more information.
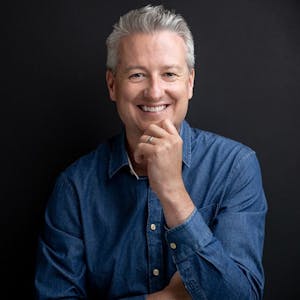