Inconel® and Monel® are distinct families of nickel-based alloys, each tailored for specific environments and performance demands. The primary alloying element in most Inconel® grades is chromium, with additional elements such as iron and molybdenum, which enhance their strength and oxidation resistance at elevated temperatures. In contrast, Monel® alloys are primarily composed of nickel and copper, with copper being the main alloying addition. This composition provides Monel with excellent corrosion resistance, especially in marine and chemical processing environments, and makes it suitable for moderately high-temperature applications, although typically not as high as those of Inconel.
This article explores and compares these two alloy families in terms of their chemical composition, manufacturing methods, common types, key properties, typical applications, and respective advantages and disadvantages.
What Is Monel?
Monel is a trademarked name for a group of nickel alloys, primarily composed of nickel, copper, and small amounts of other elements such as iron and manganese, among others. However, the exact composition of a particular type of Monel will depend on the desired properties and intended use. Monels are typically known for their corrosion resistance (in both fresh and saltwater environments) and high strength, as well as their good low- and medium-temperature resistance. Monel alloys are often used in environments where corrosion and erosion are significant concerns, such as in the marine and chemical processing industries.
To learn more, see our guide on What is Monel Material.
What Is Monel Made Of?
Alloys in the Monel family consist of 52-67% nickel, approximately 28-34% copper, and small amounts of other elements, such as iron, manganese, aluminum, silicon, sulfur, titanium, and carbon.
How Is Monel Made?
Monel is typically manufactured through a multi-step process of melting and casting. The process begins with high-purity nickel and copper — the primary components of Monel. These raw materials are melted in a furnace, often an electric arc or induction furnace. Alloying elements, including small amounts of iron, manganese, silicon, and others, are carefully added to attain specific mechanical and chemical properties. Once the alloy is molten, it is cast into the desired shape, such as ingots or billets. It can also be continuously cast.
Following casting, the alloy undergoes various forming processes to achieve its final form. These may include hot rolling, cold rolling, forging, extrusion, cast-to-shape products, Monel powders, and additive manufacturing (3D printing). Through methods, the alloy is either molded into the intended shapes, such as sheets, bars, plates, rods, or wires, or shaped into the final product through processes like 3D printing.
Some Monel alloys may undergo heat treatment to optimize their mechanical properties. This involves controlled heating and cooling to induce specific microstructural changes. Finally, the finished Monel products may undergo additional processes, such as machining and polishing, to meet precise dimensional specifications and surface finish requirements.
What Are the Different Types of Monel?
There are numerous Monel alloy grades available on the market. Each of these grades has a somewhat different alloy composition and mechanical properties, and therefore has various applications. Some of the common grades include Monel 400, 401, 404, 405, 450, K-500, and 502.
Each Monel grade serves specific needs dictated by its composition and mechanical attributes. Alloy 400 exhibits high strength and corrosion resistance, making it suitable for use in hydrocarbon processing, marine applications, and heat exchangers. Alloy 401, with its compatible brazing properties (enabling effective joining with other metals through a brazing process), finds application in electrical and electronic contexts, including precision electronic components, electronic assemblies, and electronic connectors and contacts. The ability to be effectively brazed is crucial in electronic and electrical applications, as it enables the creation of strong, reliable joints between various components. The compatibility of Monel 401 with brazing means it can be securely joined to other metals without compromising its integrity or the functionality of the electronic device.
Alloy 404, renowned for its low magnetic permeability, is utilized in various electrical and electronic applications. Alloy 405 is a free-machining version of Monel 400. It shares many of the same properties as Monel 400, including its high strength and resistance to corrosion. The primary distinction between Monel 405 and Monel 400 lies in Monel 405's increased sulfur content, which is specifically added to enhance its machinability.
What Are the Advantages of Monel?
Monel offers the following advantages and benefits:
- Combination of high strength and exceptional corrosion resistance. It has good corrosion resistance properties in different environments. This includes resistance to acids, alkalis, and exposure to both fresh and saltwater. Its corrosion resistance surpasses that of other common corrosion-resistant metals such as 316 stainless steel.
- Monel, particularly Monel 400, has a higher yield and tensile strength compared to 316 stainless steel.
- Monel has a lower coefficient of thermal expansion compared to austenitic stainless steels. This is a significant advantage in applications where dimensional stability is critical under varying temperature conditions.
- Can be easily welded, soldered, and brazed.
- Performs well in both low- and high-temperature applications. It maintains its strength in temperatures ranging from sub-zero to 480 °C.
- Monel is non-magnetic and has a very low Curie point.
- A key benefit of wrought, nickel-based alloys, known for their corrosion resistance, is their strong ability to withstand chloride-induced stress corrosion cracking (SCC). This type of corrosion is a common issue for stainless steels. Interestingly, it has been observed that the resistance of these nickel alloys to SCC decreases as their iron content increases. This implies that nickel alloys with lower iron content are more effective in resisting this particularly damaging form of corrosion. However, both Monel K-500 and Alloy 400 are vulnerable to stress corrosion cracking, but they are generally still considered better than austenitic stainless in that regard.
What Are the Disadvantages of Monel?
Monel has the following disadvantages relative to other potential materials for corrosive environments:
- Their rate of work hardening during machining is very high. This makes subsequent cuts more challenging and contributes to accelerated tool wear. To address this, Monel R-405 has been specially developed to enhance machinability.
- Although Monels exhibit resistance to fast-flowing seawater, they are susceptible to pitting corrosion when exposed to seawater for extended periods at low flow velocities.
- Galvanic corrosion can occur when certain metals, including aluminum, zinc, and iron, are in direct contact with Monel and simultaneously exposed to harsh weather elements. As a result, using these metals as fasteners or connectors in conjunction with Monel is generally not advisable to prevent corrosion.
- Monels are expensive due to their composition. These alloys are more expensive than some alternative materials with similar properties, such as duplex stainless steel, particularly grades like 2205.
What is Inconel?
The name Inconel refers to a group of nickel-based superalloys that have chromium as their major alloying element (14-31 wt%) and may contain iron, molybdenum, copper, titanium, aluminum, and niobium in smaller amounts to enhance specific mechanical or physical properties. The Inconels are renowned for their outstanding corrosion and oxidation resistance, impressive strength at high temperatures, and excellent mechanical properties.
Inconel alloys are well-suited for use in extreme environments, including high-temperature and corrosive conditions. They are strong, ductile, and creep- and oxidation-resistant under elevated temperature conditions, making them valuable in industries such as aerospace, chemical processing, and marine engineering. Some of their applications include nuclear reactors and gas turbines, for example.
What is Inconel Made of?
The exact composition of Inconel can vary significantly from grade to grade. The initial Inconel alloy, designated as Inconel 600, has a composition comprising over 72% nickel, 14–17% chromium, 6–10% iron, and approximately 1% manganese. Additionally, traces of other elements, such as copper, silicon, carbon, and sulfur, are also present. The proportions of these constituents can vary, and other alloys within the Inconel family incorporate additional elements to tailor their properties for specific applications. These supplementary elements may include niobium, molybdenum, cobalt, tantalum, titanium, lead, aluminum, and boron, each contributing distinct characteristics to the alloy, such as enhanced corrosion resistance, high-temperature strength, and other desirable mechanical properties.
How Is Inconel Made?
The production of Inconel alloys involves melting nickel with chromium and other elements such as iron, molybdenum, and niobium in precise proportions to achieve the desired material properties. This is done using an electric arc or vacuum induction furnace. The molten alloy is then cast into forms such as ingots or billets. After solidification, the alloy undergoes heat treatments, including solution annealing, quenching, and precipitation hardening (also known as age hardening), to enhance its mechanical properties and corrosion resistance. Solution annealing involves heating the alloy and rapidly cooling it, while precipitation hardening further strengthens the alloy by heating it at lower temperatures for an extended period. Once heat-treated, Inconel is formed into various shapes, such as sheets, bars, or tubes, through methods like forging or extrusion. The process concludes with finishing steps such as machining or surface treatments to achieve the desired dimensions and surface quality. The specific conditions for each step vary depending on the Inconel grade, to optimize strength, ductility, and corrosion resistance.
What are the Different Types of Inconel?
Just like Monel, Inconel is available in various grades, each with its own unique composition and specific use cases. Some common types of Inconel include Inconel 600, Inconel 601, Inconel 625, Inconel 690, Inconel 718, Inconel X-750, and Inconel 792. Inconel 600, the original Inconel alloy, is renowned for its exceptional heat and corrosion resistance, making it an ideal choice for chemical plant components. Inconel 601 excels in high-temperature organic-chemical plants, displaying excellent oxidation resistance and resistance to carburization. Inconel 625 surpasses both 601 and 600 in corrosion resistance, creep resistance, and in retaining strength up to 980 °C.
Inconel 718 is designed for precipitation hardening and provides good strength and toughness up to 650 °C, along with excellent corrosion and oxidation resistance. Inconel X-750 has even better corrosion resistance and oxidation resistance than Inconel 718, which is especially beneficial for aerospace and industrial gas turbine components. Inconel 690 offers superior resistance to chloride corrosion and is commonly used in environments such as nitric acid, steam generators, and nuclear waste treatment plants. Lastly, Inconel 702 is a casting alloy with notably high strength.
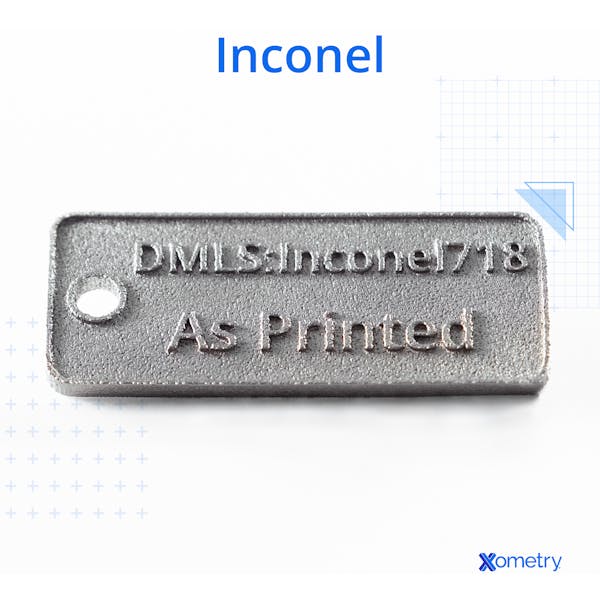
What Are the Advantages of Inconel?
Inconel alloys offer several advantages, such as:
- Exceptional resistance to corrosion, particularly in aggressive environments such as those involving seawater, acids, or high-pressure steam.
- High strength and structural stability at elevated temperatures.
- Excellent oxidation resistance.
- Availability in various grades, each engineered to offer specific combinations of corrosion resistance, mechanical strength, and heat resistance for targeted applications.
- Some grades, such as Inconel 625, provide outstanding resistance to creep deformation at high temperatures, ensuring long-term reliability in thermally stressed systems.
- Good fatigue strength, enabling the alloy to endure cyclic loading and extended operational lifespans without failure.
- Generally good weldability, although specific welding techniques and filler materials may be required to preserve alloy integrity and prevent cracking.
What Are the Disadvantages of Inconel?
Although Inconel comes with a lot of notable advantages, it also has some disadvantages to consider, such as:
- Inconel alloys are significantly more expensive than standard stainless steels or other conventional metals, due to their high nickel content and complex manufacturing processes.
- Inconel is notoriously hard to machine, requiring specialized tools, cutting techniques, and slower processing speeds to avoid excessive tool wear and workpiece hardening.
- Some grades, such as Inconel 718, are susceptible to hydrogen embrittlement, particularly under high-pressure or high-temperature hydrogen exposure, which can compromise mechanical performance.
How To Choose Between Monel and Inconel
When deciding between Monel and Inconel, several key factors come into play, including specific application requirements, cost considerations, and the environmental conditions to which the alloys will be exposed.
Both are nickel-based alloys, with Monel incorporating copper as its secondary alloyant, and Inconel utilizing chromium. In terms of performance, Monel excels in corrosion resistance in very aggressive solutions at mid-range temperatures, while Inconel excels in high-temperature strength, creep resistance, and oxidation resistance.
Price-wise, Inconel is generally considered to be more expensive than Monel, primarily due to its composition, which often includes higher amounts of nickel and chromium. However, it's important to note that the cost difference is not fixed and can vary based on several factors. These include fluctuations in commodity prices, particularly for nickel and chromium, as well as the specific grades and alloy compositions being considered. Market conditions and the demand for particular alloy properties can also impact the relative pricing of Inconel and Monel.
Corrosion resistance is excellent in both alloys, with Monel excelling in seawater resistance due to its copper content, but Inconel 625 also does particularly well in seawater conditions. However, Inconel's high-temperature oxidation resistance is a key characteristic that sets it apart, especially in applications where exposure to high temperatures and oxidizing conditions is a primary concern.
Monel, while excellent in corrosion resistance, also has a respectable high-temperature performance for a range of applications. It can typically operate effectively in temperatures up to approximately 600 °C (1112 °F). Inconel, on the other hand, is known for its exceptional high-temperature capabilities due to its higher nickel and chromium content. It can maintain its strength and resist oxidation at much higher temperatures, often up to around 982 °C (1800 °F) or more, depending on the specific grade.
The alloys also differ in their melting points, densities, and heat treatment methods. Additionally, Inconel alloys have higher yield and tensile strengths than Monel, making them suitable for applications such as structural products or use in chemical plants.
When examining typical applications, Monel is commonly used in marine hardware, chemical processing equipment, and hydrocarbon processing systems. Inconel, in contrast, is frequently utilized in turbine blades, nuclear reactor components, and exhaust systems in high-performance automotive and aerospace industries. These applications reflect the alloys' respective strengths in corrosion resistance and high-temperature performance.
What Are the Properties of Monel and Inconel?
The properties of Inconel and Monel are outlined in Tables 1 and 2, respectively.
Grade | Density (g/cc) | Melting Point (°C) | Tensile Strength (MPa) | Yield Strength (0.2% offset) (MPa) | Elongation (%) |
---|---|---|---|---|---|
Grade 600 | Density (g/cc) 8.47 | Melting Point (°C) 1413 | Tensile Strength (MPa) 655 | Yield Strength (0.2% offset) (MPa) 310 | Elongation (%) 40 |
Grade 601 | Density (g/cc) 8.1 | Melting Point (°C) 1411 | Tensile Strength (MPa) 550 | Yield Strength (0.2% offset) (MPa) 205 | Elongation (%) 30 |
Grade 617 | Density (g/cc) 8.3 | Melting Point (°C) 1363 | Tensile Strength (MPa) >=485 | Yield Strength (0.2% offset) (MPa) >=275 | Elongation (%) 25 |
Grade 625 | Density (g/cc) 8.4 | Melting Point (°C) 1350 | Tensile Strength (MPa) 930 | Yield Strength (0.2% offset) (MPa) 517 | Elongation (%) 42.5 |
Grade 690 | Density (g/cc) 8.3 | Melting Point (°C) 1363 | Tensile Strength (MPa) >=485 | Yield Strength (0.2% offset) (MPa) >=275 | Elongation (%) 25 |
Grade 718 | Density (g/cc) 8.2 | Melting Point (°C) 1350 | Tensile Strength (MPa) 930 | Yield Strength (0.2% offset) (MPa) 482 | Elongation (%) 45 |
Grade 725 | Density (g/cc) 8.31 | Melting Point (°C) 1271 | Tensile Strength (MPa) 1137 | Yield Strength (0.2% offset) (MPa) 827 | Elongation (%) 20 |
Grade X-750 | Density (g/cc) 8.28 | Melting Point (°C) 1430 | Tensile Strength (MPa) 1267 | Yield Strength (0.2% offset) (MPa) 868 | Elongation (%) 25 |
Table Credit: https://www.oshwin.com/blog/inconel-vs-monel.html
Grade | Density (g/cc) | Melting Point (°C) | Tensile Strength (MPa) | Yield Strength (0.2% Offset) (MPa) | Elongation (%) |
---|---|---|---|---|---|
Grade Alloy 400 | Density (g/cc) 8.8 | Melting Point (°C) 1350 | Tensile Strength (MPa) 550 | Yield Strength (0.2% Offset) (MPa) 240 | Elongation (%) 40 |
Grade Alloy 404 | Density (g/cc) 8.91 | Melting Point (°C) 1300 | Tensile Strength (MPa) >=483 | Yield Strength (0.2% Offset) (MPa) >=172 | Elongation (%) 35 |
Grade Alloy 405 | Density (g/cc) 8.8 | Melting Point (°C) 1300 | Tensile Strength (MPa) 550 | Yield Strength (0.2% Offset) (MPa) 240 | Elongation (%) 40 |
Grade Alloy K500 | Density (g/cc) 8.44 | Melting Point (°C) 1350 | Tensile Strength (MPa) 1100 | Yield Strength (0.2% Offset) (MPa) 790 | Elongation (%) 20 |
Table Credit: https://www.oshwin.com/blog/inconel-vs-monel.html
What Are the Applications of Monel and Inconel?
Monel and Inconel each have their ideal use cases. Each grade within the Monel and Inconel families has its unique composition and thus specific properties that make it suitable for certain environments and uses. For example, some grades may be more resistant to certain types of corrosion, while others may exhibit better high-temperature strength or resistance to thermal cycling.
Therefore, when selecting a grade of Monel or Inconel for a particular application, it's important to consider the specific environmental conditions, temperature ranges, mechanical stresses, and corrosion types that the alloy will encounter.
The general applications for both of these alloy groups are listed below. The exact applications of specific types will, however, be slightly different based on their composition and properties.
Monel alloys—particularly Monel 400, Monel K-500, and Monel 404—are widely used across various industries due to their excellent resistance to corrosion and good mechanical properties. Typical applications include:
- Marine engineering: Monel alloys, especially Monel 400 and Monel K-500, are extensively used in marine environments due to their exceptional resistance to saltwater corrosion. Typical components include propeller shafts, seawater valves, pump shafts, and other shipbuilding components.
- Chemical processing: Equipment such as heat exchangers, reaction vessels, and piping systems often utilizes Monel 400 and 404, which resist corrosive chemicals, including hydrofluoric and sulfuric acids.
- The aerospace industry utilizes Monel K-500, which offers enhanced strength and corrosion resistance, in aircraft structural components, exhaust systems, and rocket engine parts where moderate to high-temperature strength is crucial.
- The oil and gas sector utilizes Monel alloys, including Monel 400 and Monel K-500, in valves, pumps, and tubing for oil and gas extraction and processing, where durability in sour gas and corrosive fluids is crucial.
- Electronics: Monel 404 is utilized in electronic components and connectors due to its high electrical conductivity and low magnetic permeability, making it suitable for sensitive instrumentation and shielding applications.
Inconel alloys are extensively used in demanding environments due to their exceptional resistance to high temperatures, corrosion, and mechanical stress. Notable applications include:
- Aerospace industry: Inconel is a key material in jet engines and other aerospace systems where components must withstand extreme heat and mechanical stress. Typical parts include turbine blades, exhaust systems, fuel nozzles, afterburner rings, and structural components in rocket engines and space vehicles. Standard aerospace-grade alloys include Inconel 718 and Inconel 625, which are valued for their high strength, oxidation resistance, and excellent fatigue performance.
- Nuclear power industry: Inconel is utilized in nuclear reactor components, particularly reactor pressure vessels, steam generators, and control rod mechanisms. These applications require outstanding high-temperature strength and corrosion resistance. Common grades include Inconel 690 and Inconel 600, noted for their resistance to stress corrosion cracking and high-temperature oxidation.
- Thermal processing equipment: Due to its ability to maintain structural integrity across extreme temperature fluctuations, Inconel is ideal for heat treatment fixtures, such as baskets, trays, and racks used to hold steel or titanium components. These components endure cycling from cryogenic temperatures to elevated heat, while exhibiting minimal thermal expansion and excellent fatigue resistance.
- Automotive and motorsports: Inconel 625 is favored in high-performance and motorsport vehicles (e.g., Formula 1) for its thermal stability, corrosion resistance, and durability. Applications include exhaust systems, turbochargers, braking components, engine internals, and electrical shielding for connectors and control units, where exposure to extreme heat is a common occurrence.
- Marine and offshore engineering: Inconel alloys, particularly Inconel 625, are employed in seawater and salt-laden environments due to their exceptional pitting and crevice corrosion resistance. Applications include wire ropes, propeller blades, propulsion motors, downhole equipment, risers, platform hangers, and undersea cable sheathing. These alloys perform reliably in both static and dynamic loading conditions in corrosive marine settings.
How Much Do Monel and Inconel Cost?
The cost of Monel and Inconel alloys is influenced by their high nickel content and the inclusion of other expensive alloying elements. In Monel, copper is a significant element, alongside nickel, that contributes to its corrosion resistance and strength. Inconel, however, includes a considerable amount of chromium, enhancing its high-temperature strength and corrosion resistance. Chromium, being more expensive than copper, contributes to Inconel's higher cost. Additionally, Inconel often contains other costly elements, such as niobium, titanium, and molybdenum, further increasing its price. Both alloys are more expensive than standard stainless steel, with Inconel generally commanding a higher price due to its specialized alloy composition, which enables superior performance in extreme conditions.
Common FAQs About Monel and Inconel
Can You Laser Weld Monel and Inconel?
Yes, both Monel and Inconel can be laser welded; however, this is only true for some grades. Grades that can be welded include Monel 400, Inconel 600, Inconel 718, and Inconel 825.
To learn more, see our full guide on What is Laser Welding.
Is Monel Harder Than Inconel?
Monel and Inconel can exhibit similar high strength and hardness. Still, within each alloy family, the hardness depends on the particular alloy composition and heat-treatment condition of a given sample. It is, however, common for Inconel alloys to be stronger and more complex than Monels.
Can You Laser Cut Monel and Inconel?
Yes, both Monel and Inconel alloys can be laser cut. However, they can be challenging to cut because of their high reflectivity and melting temperatures. This can be overcome with the right equipment and cutting parameters.
Fiber lasers are ideal for cutting reflective materials such as Monel and Inconel. Different grades of Monel and Inconel will, however, perform differently with laser cutters due to their differences in properties. Inconel 718 is one of the materials that performs well with a laser cutter. Monel 400 has also been successfully cut using laser technology.
Does Inconel Rust?
No, Inconel is a nickel-based alloy with minimal iron content and does not rust like iron-based alloys do. Rust is specific to iron and steel, involving the formation of iron oxides. Instead, Inconel forms a tightly adherent oxide passivating layer that protects the metal from further corrosion. This oxide layer is primarily composed of chromium oxide, which forms on the surface of the Inconel when it is exposed to oxygen. The presence of this protective layer is a key factor in Inconel's high corrosion resistance, particularly in extreme environments.
While Inconel is highly resistant to various forms of corrosion, including pitting and crevice corrosion, it is not immune to all types of corrosion, particularly in extreme conditions. However, its corrosion resistance exceeds that of stainless steel, but this comes with a higher price point. Inconel alloy 625 is particularly renowned for its exceptional corrosion resistance, particularly in seawater applications, with resistance to both pitting and crevice corrosion. Additionally, it possesses high tensile strength, high corrosion-fatigue strength, and is resistant to chloride-ion stress-corrosion cracking.
Summary
This article presented Monel® and Inconel®, explained each of them, and discussed their various key differences. To learn more about Monel® and Inconel®, contact a Xometry representative.
Xometry provides a wide range of manufacturing capabilities and other value-added services for all of your prototyping and production needs. Visit our website to learn more or to request a free, no-obligation quote.
Copyright and Trademark and Notices
- Inconel® and Monel® are registered trademarks of Special Metals Corporation.
Disclaimer
The content appearing on this webpage is for informational purposes only. Xometry makes no representation or warranty of any kind, be it expressed or implied, as to the accuracy, completeness, or validity of the information. Any performance parameters, geometric tolerances, specific design features, quality and types of materials, or processes should not be inferred to represent what will be delivered by third-party suppliers or manufacturers through Xometry’s network. Buyers seeking quotes for parts are responsible for defining the specific requirements for those parts. Please refer to our terms and conditions for more information.
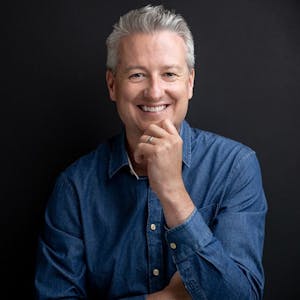