Pull-out (sometimes called pull-off) testing is a method used to assess the coupling strength of a hole-based fixing into concrete. The process is vital in the construction sector and geotechnical engineering to ensure the reliability and durability of attachment interfaces of devices, construction elements, and machines to concrete surfaces.
Pull-out testing involves applying a tensile force to a concrete-embedded or expansion-retained fastener until it breaks free of the substrate. It is used as a comparison proxy for the strength of concrete, often expressed in force per unit area (e.g., psi or MPa).
This article will discuss what the pullout test is, its importance, and how it works.
What Is a Pullout Test?
A pullout or pull-off test is a type of material evaluation test designed to quantify the strength of a concrete sample and its relationship to the fastener engagement approach. This method is commonly used in construction to assess the quality of geosynthetic materials and their respective resilience.
In a pullout test, a controlled force is applied to the fastener in a direction perpendicular to the coupled surface — axially loading the fastener. The objective is to measure the force required to separate or load the fastener to create a bursting force until failure occurs. The results of the test provide valuable information about the concrete strength, allowing direct performance comparisons between concrete samples and fastener systems.
What Is the Importance of the Pullout Test?
The pullout or pull-off test holds significant importance for several reasons. It quantitatively measures the coupling strength between structural concrete and equipment/devices/construction elements attached to it, quantifying load capacity. In concrete structures, the pullout test is a crucial quality-control method to ensure that the concrete meets specified standards, minimizing the risk of defects. The test aids in selecting appropriate concrete formulations, processing methods, and attachment systems. This information is valuable for choosing the right solutions for specific applications. The test results can be used to predict how well an application will perform under stress in real-world applications, guiding engineers in optimizing designs and preventing potential failures.
Is Pullout Testing the Same as Shear Testing?
No, they are different in the direction of applied force. A pullout or pull-off test applies a load that is perpendicular to the coupled/bonded surfaces and along the axis of any fixings that are part of the joint. A shear test applies load in a direction parallel to the coupled surfaces and perpendicular to the axes of any fasteners/fixings that are part of the jointing process.
How Does Pullout Testing Work?
Pullout or pull-off testing typically follows these general steps:
- Ensure that the surfaces to be tested are clean and free from contaminants, as the presence of irregularities can impose sudden variation in the test setup as high points crush, invalidating measurements.
- Secure the sample in a suitable testing apparatus, ensuring that the force can be applied perpendicular to the bonded interface and that no extraneous irregularities can disrupt the smooth application of load.
- Apply a gradually increasing tensile force to the fixing, reacting to the surface of the test region. The force is incremented until failure occurs at the pulling out of a fastener, or the required performance level is achieved.
- Measure and record the force applied during the test. Record any corresponding displacement or deformation data.
- Analyze the data to determine the maximum force (peak load) required to cause failure. In non-destructive tests, log the maximum load reached and record the condition of the sample (fractured = failure).
- Additional analyses may involve studying the load-displacement curve and understanding failure modes. This can be used to assess the elasticity of the sample, in addition to the failure load and form.
- Compare the results to relevant standards, specifications, or performance requirements that refer to expected load-bearing capacity.
The specifics of testing procedures vary based on the needs of the evaluation, the standards, and the materials involved. Pullout tests are conducted both on-site and in laboratories, both using specialized testing equipment. These tests are essential for quality control, material selection, and process optimization/repeatability tests.
What Is the Pullout Test Used For?
A pullout or pull-off test is used to assess the strength performance of a bonded or fixing-coupled joint between two components. It delivers a direct measurement of the strength in resisting surface-perpendicular forces that are applied to part of the surfaces.
Variations in factors such as the rate of application of load and the nature of the failure will produce results in terms of load/displacement data that allow direct and simplified comparison between samples. These data serve to allow a comparison between alternative coupling methods that might be options, so designers can assess the effectiveness of their attachment choices, a comparison between differential methods in the application of the same coupling materials/fixings to optimize production methods, and QA evaluation of production for ongoing quality issues, by batch sampling/testing to confirm inter- and intra-batch consistency in performance.
What Is the Device Used for Pullout Testing?
Pullout testing requires specialized equipment to apply controlled tensile forces to materials and measure the resulting responses. The specific equipment used may vary based on the nature of the test and the materials involved. Some common types of equipment used for pullout testing include:
- Universal Tensile Testing Machine (UTM): A UTM is a flexible testing apparatus that can be configured for a wide spectrum of mechanical tests, including pullout testing.
- Anchor Pullout Testers: Used for geotechnical applications to evaluate the anchorage strength of anchors, soil nails, or geosynthetic materials in soil. These can be applied to pure pullout tests in concrete.
Fastener Pullout Testers: Developed specifically for testing the pullout strength of fasteners, such as: screws, bolts, or anchors, embedded in materials like: wood, concrete, or metal.
What Are the Different Types of Pullout Testing?
The different types of pullout testing are discussed below:
1. CAPO Test
The Cut-and-Pull-Out or CAPO test is performed as an in-situ strength evaluation method for concrete. It offers a generalized assessment of the tensile strength of the finished material, based on a standardized test format that enables comparison between different samples at separate times and locations, or performance against a standard.
The surface surrounding the test location is flattened and ground smooth before an 18.4 mm hole is drilled/ground perpendicular to the surface. This is most commonly performed using a diamond coring bit, for smooth and fracture-free drilling.
An undercut is then made in the hole with a diameter of 25 mm, at a depth of 25 mm, using an expanding T cutter. Into this recess, a split ring is expanded and destructively loaded to pull it out using a standard pull machine reacting against a 55 mm internal diameter counterpressure ring that is resting on the ground outer surface of the test sample.
The concrete pinched between the buried ring and the counterpressure pad is broken out by the steadily increased loading. The fracture-inducing pullout force F required is directly proportional to the compressive strength of the concrete.
The CAPO-test system therefore delivers a localized damage and compressive strength measurement of concrete, applicable to test samples and existing structures, in compliance with ASTM C900, BS 1881:207, or EN 12504-3.
2. LOK Test
The LOK test (originating from the Danish word for punch) is a cast-in method (as opposed to drilled and expanded anchors) of assessing the performance of anchors in concrete.
A preformed steel disc of 25 mm diameter is attached to a smaller diameter pull-shaft and embedded in wet concrete at a depth of 25 mm. With the concrete appropriately cured, the pull shaft is tensioned against a 55 mm internal diameter counterpressure ring resting flat on the pre-ground surface of the test material.
The force applied to the pull shaft induces compressive loading in the concrete between the embedded steel strong point and the counterpressure ring. Loading can either be performed at steadily increasing levels until a target test level is achieved, or the load can be increased until fracture of the concrete column occurs. Destructive testing is generally more common, but both approaches are encompassed within the relevant standards.
The LOK-test system provides repeatable and comparable evaluations of the compressive strength of concrete, both in test pieces and in completed structures. This test is compliant with the methods prescribed in ASTM C900, BS 1881:207, or EN 12504-3
How Does Pullout Testing Work?
In simplified terms, the pullout method to test the compressive strength of concrete is either to drill in place (CAPO) or cast-in (LOK). A steel disc or expanded ring is then pulled out of the concrete using a mechanical or hydraulic device that reacts against the smoothed surface of the test area.
The failure mode is generally a conical brittle fracture between the embedded standardized ring and the standardized surface reaction foot that has a larger inner diameter.
How Strong Is the Pullout Test?
It depends. CAPO and LOK tests commonly provide measurements of force at failure that range from 10 to as high as 60 kN, depending on the nature of the concrete being tested. The correlation between the two test types is widely considered to be close, although direct comparisons between CAPO and LOK test results are not usually treated as reliable.
What Is the Standard Measure for Concrete in a Pullout Test?
The standard measure for concrete in a pullout test is the compressive strength of the concrete, for comparison purposes. The pullout test is a method used to assess the retention strength of standardized embedded or internally expanded elements. The test involves applying a force to pull a steel rod attached to the embedded or expanded ring element out of a concrete sample, by inducing local compressive failure.
The testing standards and procedures for pullout tests may vary based on the specific standards adopted by different organizations or regions. Common standards such as ASTM (American Society for Testing and Materials) or ISO (International Organization for Standardization) provide guidelines for conducting pullout tests and interpreting the results and for specifications of the testing procedure.
How Does the Pullout Test Differ From Other Material Tests?
The pullout test is a specific type of test used to assess the compressive strength of concrete. It differs from other material tests in its focus on evaluating the integrity of the retention strength between the concrete and the embedded test ring. Pullout tests such as CAPO and LOK are specific to the compressive strength of concrete and similar geosynthetics.
Other material tests involve a wide range of different procedures depending on the property being measured. Tests can be compressive, tensile, shear, fatigue, bending, or peel, depending on the materials and components under test and the desired evaluations.
When To Do a Pullout Test?
Pullout testing is typically performed in construction projects to facilitate comparative assessments of the compressive strength of concrete samples and installations. The testing is carried out at specific stages of a project to ensure the quality and integrity of the concrete structures and to validate adherence to required installation practices/standards.
Pullout tests are often performed during the construction phase to ensure that the concrete mix used on-site meets the specified requirements for compressive strength. This helps in maintaining the overall quality of the concrete structures. In infrastructure projects like bridge and highway construction, pullout testing is crucial to ensure the integrity of the reinforced concrete structures. It helps verify the effectiveness of the concrete installation and material quality.
Pullout testing may also be performed when repairing or rehabilitating existing structures to assess the condition of the existing concrete, verify the quality of construction materials, such as the concrete formulation and handling/cure processes, and be part of a broader structural assessment to evaluate the overall condition of a concrete structure.
How Long Does a Pullout Test Take?
The duration of a pullout test can vary depending on several factors, including: the specific testing equipment used, the size and complexity of the specimen, and the testing procedures followed. Generally, the actual pullout test itself may take only a few minutes, but the overall process, including preparation and data analysis, can extend the total testing duration to 20–30 minutes per test site. If the time for sample production is included, then the casting and cure process will extend the test time considerably.
It is not uncommon for the entire process, including preparation, testing, and analysis, to take a few hours to a day. The complexity of the testing and the number of specimens being tested can influence the overall duration. Larger sequences of tests can result in shorter per-test durations through economies of scale.
What Are the Advantages of the Pullout Test?
The pullout test is a relatively simple and practical undertaking that facilitates comparison between the compressive resilience of a range of samples. Its advantages include:
- Can be carried out on-site, making them suitable for field applications. They can also be executed on disconnected material samples in a laboratory, under more tightly controlled conditions for higher-precision results.
- Serve as a quality-control measure during the construction phase. It ensures that the concrete mix and construction practices meet the specified requirements for compressive strength, resulting in higher-quality and more durable structures.
- Allows for the verification of the quality of raw materials and processes, for greater certainty of repeatable results.
- Identifying strength issues early allows for corrective measures to be implemented with minimal disruption.
- Can be part of ongoing structural health monitoring programs. Regular assessments of bond strength over time can assist in identifying deterioration or changes in the structural performance of a concrete element.
- Researchers use pullout tests to study and develop new construction materials or construction techniques, advancing the field of concrete technology.
- In cases of structural failure or rehabilitation projects, pullout tests can be used for forensic analysis.
What Are the Disadvantages of the Pullout Test?
While the pullout test has its advantages, it also has some disadvantages and limitations that should be considered:
- The results of pullout tests can be sensitive to various test variables, including: concrete mix properties, surface conditions, curing methods, and testing procedures. Small changes in these variables can impact the test outcomes.
- Provide a direct evaluation of material strength only at the test site. Extrapolation of these results into a whole-structure conclusion is fraught with difficulties and risks, so results must be presented with caveats.
- Destructive test that requires removing or damaging a portion of the concrete structure. This may not be feasible in certain situations. In ongoing assessments, this can result in damaged sites that can undermine confidence in the structure's integrity.
- The condition of the concrete surface at the test location can significantly impact the test results. Poor surface preparation or contamination may lead to inaccurate assessments of strength as the surface adjusts under load, shocking the bulk material.
- Interpreting the results of pullout tests requires expertise and an understanding of various factors influencing the strength and the interpolation between tested and untested regions.
What Are the Types of Failures in Pullout Testing?
In a pullout test, the failure modes are brittle and are generally described as concrete cone failure. This occurs when the concrete in the vicinity of the embedded reinforcement is pulled out, with the fracture zone resulting in a roughly conical separation. This failure mode typically suggests good-quality concrete.
In cases in which the material strength is extremely low, the splitting failure may involve a less conical and more cylindrical pull out of the embedded ring.
Aggregate interlock failure is an unusual mode that involves the separation of coarse aggregates from the surrounding matrix due to applied tensile forces, implying material structure failure in a localized distributed mode. This type of failure may occur in regions with an excessive concentration of aggregates and insufficient mixing or improper material formulation at pour.
Is It Hard to Pullout Test?
No, pullout tests are easy to perform with appropriate equipment and a little training/experience. They are a necessary and regular feature of QA and evaluation of concrete processes. It is critically important that a consistent technique is used to facilitate comparisons between tests and test regions.
Is the Pullout Test Dangerous?
Yes, if inappropriate practices are applied, such as fingers near the failure zone or eye protection not used, then there is potential for injury.
The pullout test is liable to a sudden fracture termination, as the load is generally (but not always) increased to the failure point to assess the strength of the concrete. However, the stored energy in the tension of the test equipment is not great and the failure does not tend to produce either large-scale movement or shrapnel that is liable to harm.
There can be dust and small particles released and hands must be kept away from the pre-failure zone. Appropriate safety gear includes eye protection and might also include a filter mask. With these precautions, the operator and collateral hazards in these tests are negligible.
What Is the Difference Between Pullout Testing and Tensile Testing?
Pullout testing is a subset of tensile testing that only evaluates the compressive strength of concrete in resisting the pull forces applied to a fixing point, in a standardized and simplified way. General tensile testing might involve a wide range of materials or fastening methods and may involve significant plastic and elastic behavior that are largely absent in the testing of such intrinsically brittle materials as concrete.
Summary
This article presented pullout tests, explained them, and discussed their importance and how they work. To learn more about pullout tests, contact a Xometry representative.
Xometry provides a wide range of manufacturing capabilities and other value-added services for all of your prototyping and production needs. Visit our website to learn more or to request a free, no-obligation quote.
Disclaimer
The content appearing on this webpage is for informational purposes only. Xometry makes no representation or warranty of any kind, be it expressed or implied, as to the accuracy, completeness, or validity of the information. Any performance parameters, geometric tolerances, specific design features, quality and types of materials, or processes should not be inferred to represent what will be delivered by third-party suppliers or manufacturers through Xometry’s network. Buyers seeking quotes for parts are responsible for defining the specific requirements for those parts. Please refer to our terms and conditions for more information.
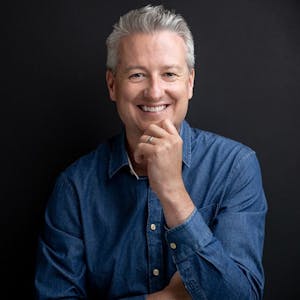