Silicon bronze is an alloy made primarily of copper that contains small amounts of other elements like silicon, zinc, and manganese. It is renowned for its strength, which exceeds that of most bronze types.
This copper alloy has a distinct reddish-brown color that, alongside its physical properties, sets it aside from other alloys. Because it resists corrosion, silicon bronze is popular in architectural and marine industries, among others.
This article will define silicon bronze and explore its composition, properties, and diverse applications across various sectors.
What Is Silicon Bronze?
Silicon bronze is a copper alloy composed mainly of copper, which accounts for about 96% of the composition. The remainder consists of: silicon, zinc, manganese, iron, tin, and/or lead. With less lead than traditional bronze, it’s considered a low-lead bronze alloy. Instead, it embraces silicon as its primary alloying element.
Its large percentage of copper gives silicon bronze a characteristic reddish-brown color. This alloy is renowned for the properties that silicon imparts to it. It is very thermally conductive, easily machinable, stronger than most bronzes, and highly corrosion-resistant.
What Is the History of Silicon Bronze?
Bronze in general can be traced back to the bronze age, around 3300–1200 BCE. Composed mainly of copper with tin as its primary alloying element, bronze proved to be an excellent replacement for stone tools. Its use gradually spread throughout Eurasia and Africa.
Over time, metallurgists experimented with different alloying elements to further enhance the properties of the alloy. Silicon was often chosen because it significantly improved the alloy’s strength and corrosion resistance ability.
What Is Another Term for Silicon Bronze?
Silicon bronze is also known by trade names such as Everdur® and Cusilman as well as numerical classifications like C65500. These terms and numerical classifications are used to identify the specific composition and properties of different silicon bronze alloys.
Everdur is an American trade name for a specific type of silicon bronze that is widely used in artistry like sculpting. Cusilman, on the other hand, is an Australian type that’s shipped in sheets and plates.
A typical numerical designation of silicon bronze is C65500, which fits into the unified numbering system (UNS) for metal alloys. The C indicates copper, the main element in silicon bronze, while the numbers indicate the alloying elements' prevalence.
What Is Silicon Bronze Made Of?
Silicon Bronze is a metal alloy that is primarily composed of copper, which constitutes about 96% of the alloy composition. The remaining 4% is derived from alloying elements like: silicon (the primary alloying element), tin, iron, zinc, manganese, and lead.
Silicon is the primary alloying element, enhancing the alloy’s strength and corrosion resistance ability. It constitutes about 2% to 4% of the alloy. The other alloying elements are added in smaller amounts to improve the metal’s overall properties. The specific properties they impart vary, depending on the desired application of the silicon bronze alloy.
How Are Silicon Bronzes Made?
Silicon bronzes are made through a process called alloying. This process involves melting specific constituent elements of the alloy in prescribed proportions. Alloying usually follows a few main steps:
- Raw material selection: The proper raw materials include copper and silicon, plus small amounts of tin, iron, zinc, manganese, and/or lead, depending on the formulation.
- Melting: An electric arc furnace or induction furnace transforms the raw materials from solid to liquid.
- Adding the alloying elements: The addition of the primary alloying element, silicon, is crucial to attain the desired properties of silicon bronze, but the other constituents must meet the right percentages too.
- Stirring: All constituents must be evenly distributed in the molten alloy.
- Casting: This sets the molten alloy into your desired shapes. It can be done through sand casting, die casting, or other methods.
- Cooling and solidification: The silicon bronze cast is allowed to cool enough that it will retain the mold’s shape.
What Are the Characteristics of Silicon Bronze?
Silicon bronze exhibits distinct characteristics that make it useful in numerous industries. These characteristics include:
- High resistance to corrosion and corrosive conditions.
- Good strength and durability.
- Relatively malleable structure that can be molded into various shapes and forms.
- Distinct reddish-brown color owing to the presence of copper.
- High levels of thermal conductivity.
- Resistance to wear and tear.
- Highly biocompatible.
How Does Silicon Bronze Differ From Other Types of Bronze?
Silicon bronze differs from other types of bronze like phosphor bronze and aluminum bronze in terms of alloy composition, color, appearance, and application in industries.
- Alloy Composition: All bronzes are composed primarily of copper, but their primary alloying elements differ. For silicon bronze, that element is silicon, as the name implies. Phosphor bronze and aluminum bronze are primarily alloyed with phosphorus and aluminum, respectively.
- Color and Appearance: Silicon bronze has a reddish-brown color, phosphor bronze has a relatively golden or pale color, and aluminum bronze has a yellowish or golden hue.
- Applications: Silicon bronze is widely employed in architectural elements, marine equipment, and artistry because of its corrosion resistance and strength. Phosphor bronze is utilized in electrical components, fasteners, and springs due to its strength and electrical conductivity. Aluminum bronze is used in heavy machinery, marine applications, and corrosion-resistant components.
What Is the Color of Silicon Bronze?
Silicon bronze has a distinctive reddish-brown color. This comes mainly from the orange-red hue of ordinary copper. The silicon bronze alloy’s color varies depending on its specific composition, the presence of impurities, and the surface finish. The reddish-brown color of silicon bronze gives it a unique appearance and aesthetic appeal.
What Does Silicon Bronze Look Like?
Silicon bronze surfaces can vary in appearance based on the manufacturing process and any additional treatments applied. The alloy can have a smooth, polished finish or a slightly textured surface, depending on factors such as casting methods or machining processes.
The metal typically exhibits a warm and rich reddish-brown or golden-brown hue. This coloration results from the combination of copper, the base metal, with silicon and other alloying elements.
The appearance and aesthetic appeal of silicon bronze make it a popular material in various industries, including architecture, marine engineering, and artistry.
What Are the Different Types of Silicon Bronze?
Silicon bronze alloys can be classified into different types based on their specific compositions and applications. Some of the common types of silicon bronze include:
- C65500 Alloy: This is a common silicon bronze alloy designated under the unified numbering system (UNS). The C in the name represents copper, the main element in the alloy. The numbers are indicative of the proportions of the other alloying elements used in the production of this particular silicon bronze alloy. This type of silicon bronze can be seen in bolts, nuts, screws, rods, fasteners, and wires.
- C65100 Alloy: This is another UNS silicon bronze designation. It consists of copper, silicon, zinc, iron, manganese, and lead. It is widely applied in electrical connectors, fasteners, bolts, bushings, bearings, and valves.
What Are the Physical Properties of Silicon Bronze?
The physical properties of silicon bronze determine how it can be used. These physical properties include:
- Density: The density of silicon bronze is typically between 8.53 and 8.83 grams per cubic centimeter. This influences the overall weight and mass of components made from the alloy.
- Thermal Conductivity: Silicon bronze exhibits good thermal conductivity, so it makes a good heat transfer medium. The specific thermal conductivity can vary based on the alloy composition.
- Electrical Conductivity: Silicon bronze is known for its electrical conductivity, making it suitable for use in electrical connectors and other electronic components.
- Hardness: The hardness of silicon bronze contributes to its strength and wear resistance. This can be influenced by the alloy composition and any heat treatments applied.
- Tensile Strength: The tensile strength is the maximum amount of stress the material can undergo before it breaks or fractures. This is typically in the range of 70,000 to 90,000 pounds per square inch for silicon bronze. The exact figure depends on the specific alloy and heat treatment.
- Magnetic Properties: Silicon bronze is non-magnetic, which can be advantageous where magnetic interference is a concern.
How Hard Is Silicon Bronze?
The hardness of silicon bronze can vary depending on the specific alloy composition and any heat treatments applied during manufacturing. Generally, silicon bronzes exhibit moderate hardness, which gives them a balance between strength and malleability.
The hardness of a silicon bronze can be measured using the Rockwell hardness test or the Brinell hardness test. The Rockwell hardness value for silicon bronze is usually 51 while Brinell hardness can range from approximately 80 to 120.
Is Silicon Bronze Malleable?
Yes, silicon bronze is generally considered to be malleable. Malleability is a measure of how much a material can deform under compressive stress without fracturing and also retain the deformation after the stress is removed.
The malleability of silicon bronze enhances its mechanical properties, contributing to its strength, formability, and weldability. This property makes silicon bronze well-suited for various manufacturing processes, including: casting, forging, and machining.
What Are the Chemical Properties of Silicon Bronze?
The chemical properties of silicon bronze are outlined and discussed in Table 1 below:
Chemical Property | Description |
---|---|
Chemical Property Base Metal Composition | Description Predominantly composed of copper (Cu). |
Chemical Property Alloying Elements | Description Silicon primarily and trace amounts of manganese (Mn), zinc (Zn), tin (Sn), and sometimes aluminum (Al) or lead (Pb). |
Chemical Property Electrochemical Behavior | Description Corrosion-resistant, pitting-resistant, anodic behavior, ion migration. |
Chemical Property Reaction with Oxygen | Description Copper reacts with oxygen to form copper oxide (CuO). |
Chemical Property Reaction with Moisture | Description Copper reacts with moisture and atmospheric elements to gradually form a protective patina. |
Chemical Property Reaction with Sulfur Compounds | Description Relatively resistant to corrosion in the presence of sulfur compounds. |
Chemical Property Reaction with Nitrogen Compounds | Description Stable in the presence of nitrogen compounds. |
Chemical Property Formation of Intermetallic Compounds | Description It may form intermetallic compounds with certain alloying elements. |
Chemical Property Thermal Conductivity | Description Maintains good thermal conductivity and is suitable for applications where heat transfer is essential. |
Chemical Property Resistance to Acidic Environments | Description Generally resists corrosion in acidic environments. |
Chemical Property Resistance to Alkaline Environments | Description Exhibits resistance to alkaline substances. |
What Are the Applications of Silicon Bronze?
Listed below are some applications of silicon bronze:
1. Hydraulic Products
Hydraulic systems and devices use fluids to transmit mechanical power. Silicon bronze is utilized for hydraulic components such as: valves, fittings, and connectors. The alloy's resistance to corrosion is crucial in fluid environments, and its strength and malleability are important factors as well. Silicon bronze ensures the longevity and reliability of hydraulic components, as it can withstand the adverse conditions associated with hydraulic systems, including exposure to moisture and hydraulic fluids.
2. Tubing
Hollow cylindrical tubing can carry a host of different fluids. Silicon bronze tubing is great where corrosion resistance and durability are essential, such as in the transport of water or corrosive liquids — it will last longer than many other metals. The alloy’s malleability also comes into play, so it can be bent and shaped to meet specific requirements.
3. Welding Rods
Welding rods are consumable electrodes used in welding processes to join metals. Silicon bronze welding rods are popular for joining copper, brass, and other non-ferrous metals. They offer good fluidity during welding and produce strong, corrosion-resistant joints. Silicon bronze welding rods are thus suitable for various applications, including those in marine environments.
4. Hardware Products
Hardware products is an umbrella term for a wide range of metallic components, including: fasteners, hinges, and decorative elements. Silicon bronze works well for these items because of its corrosion resistance and aesthetic appeal. The corrosion resistance of silicon bronze ensures the durability of hardware products, especially in outdoor or marine applications.
5. U-Bolts
U-bolts are U-shaped fasteners that are used to secure pipes or tubes to support structures. Because it resists corrosion so well, silicon bronze is an ideal choice for these elements if they’re exposed to the elements. The resistance to corrosion and the alloy's strength make silicon bronze U-bolts reliable for securing pipes and tubes, especially in marine or outdoor installations.
6. Architectural Applications
Architects and builders use silicon bronze materials in construction and design elements. It ends up in elements like fasteners, decorative hardware, and sculptures, mainly because of aesthetics. The corrosion resistance ensures the longevity of architectural elements, while the reddish-brown color adds an attractive and distinctive finish.
7. Marine Shafting
Marine propulsion shafts are regularly made of silicon bronze because it is strong, resists corrosion, and remains durable even in saltwater environments. Silicon bronze's resistance to corrosion is crucial for preventing the degradation of shafts, ensuring reliable and long-lasting performance in marine propulsion systems.
Can You Use Silicon Bronze on Aluminum?
Yes, silicon bronze is compatible with aluminum in several ways. It’s not unusual to weld, braze, or fasten aluminum parts using silicon bronze. The bronze will act as a filler material, creating strong and durable joints with aluminum components. The versatility of silicon bronze, with its corrosion resistance and strength, complements the lightweight nature of aluminum. This compatibility enhances the performance and longevity of aluminum-based structures.
What Are the Advantages of Silicon Bronze?
The advantages of silicon bronze contribute to its versatility across industries. These advantages include:
- It is highly resistant to corrosion and corrosive conditions. The presence of silicon in the alloy enhances its resistance to agents that might otherwise accelerate the corrosion process.
- It exhibits excellent mechanical properties, including high tensile strength.
- The reddish-brown color is appealing. This adds to the visual appearance of finished products.
- Silicon bronze is relatively malleable, which allows for easy shaping, forging, and machining.
- It is highly resistant to wear and tear, which makes it a preferred option for components that are constantly exposed to friction and mechanical stress.
- Thermal conductivity is strong, making it useful in applications where heat transfer is essential.
- Silicon bronze is a relatively sustainable material because its base material, copper, is highly recyclable. The recycling process has also proven to have a lower environmental impact than the extraction of raw materials.
What Are the Disadvantages of Silicon Bronze?
Silicon bronze, despite its useful properties, also presents some drawbacks. The disadvantages of silicon bronze include:
- It’s more expensive to produce than many other alloys. The inclusion of silicon and other alloying elements contributes to its enhanced properties, but it also increases production costs. The cost can be a limiting factor, especially for users with tighter budgets and spending plans.
- Its strength is limited When compared to the strength of other materials, like certain grades of steel or high-strength alloys. As a result, silicon bronze might not be the best choice if tensile strength is a deciding factor.
- It does not handle high temperatures well, so it’s not an option for particularly hot operations. At higher temperatures — even below the melting temperature — the performance of silicon bronze can be compromised.
How Can Xometry Assist You With Your Silicon Bronze Needs?
Xometry can help by connecting you with a diverse network of manufacturing suppliers. It is an online marketplace that connects manufacturers with manufacturing suppliers and simplifies the exchange of manufacturing goods.
If you need silicon bronze, Xometry offers a comprehensive set of services for its users and helps them find suppliers that can cater to their needs. It acts as a middleman between you and your potential manufacturing suppliers.
All you have to do is detail your silicon bronze needs and Xometry will match you with suppliers whose profiles match your criteria. You’ll interact with a simple, user-friendly interface that is easy to navigate and seamlessly manages your ordering process.
Does Silicon Bronze Rust?
No. Silicon bronze does not rust and in fact, has excellent resistance to corrosion and corrosive environments. Rust is a form of corrosion that is peculiar to iron or iron-containing substances. By contrast, silicon bronze contains copper as its base metal and silicon as its primary alloying element, so it cannot form the iron oxide that makes up rust.
Does Silicon Bronze Turn Green?
Yes. Silicon bronze can turn a light green shade when it undergoes oxidation instead of rusting the way ferrous materials do. The green coloration actually protects the underlying metal from further oxidation.
Can Silicon Bronze Undergo Laser Welding?
Yes, silicon bronze can be laser-welded. The laser beam gets focused onto the joint or area that needs to be welded to join two metal parts together. The heat generated by the laser melts the material. Once it cools, a solid joint is formed. Silicon bronze is durable enough to undergo laser welding processes.
To learn more, see our full guide on What is a Laser Welder.
Is Silicon Bronze a Strong Metal?
Yes, silicon bronze is considered a strong and durable metal. It exhibits a high tensile strength in the range of 70,000 to 90,000 pounds per square inch. Its strength results from the combination of copper as the base metal with silicon and other alloying elements. These alloying elements enhance the mechanical properties of silicon bronze.
What Is the Difference Between Silicon Bronze and Brass?
While silicon bronze and brass are both copper-based alloys, they differ from one another in the following ways:
- Both contain copper as their base metal, but silicon bronze uses silicon as its primary alloying element while zinc fills that role for brass.
- Silicon bronze has a characteristic reddish-brown color while brass can appear yellow, gold, or red.
- Silicon bronze exhibits higher tensile strength and hardness than brass.
To learn more, see our full guide on the Difference Between Silicon Bronze and Brass.
Summary
This article presented silicon bronze, explained it, and discussed its composition and various properties. To learn more about silicon bronze, contact a Xometry representative.
Xometry provides a wide range of manufacturing capabilities and other value-added services for all of your prototyping and production needs. Visit our website to learn more or to request a free, no-obligation quote.
Copyright and Trademark Notice
- EVERDUR Trademark of Jenavalve Technology, Inc.
Disclaimer
The content appearing on this webpage is for informational purposes only. Xometry makes no representation or warranty of any kind, be it expressed or implied, as to the accuracy, completeness, or validity of the information. Any performance parameters, geometric tolerances, specific design features, quality and types of materials, or processes should not be inferred to represent what will be delivered by third-party suppliers or manufacturers through Xometry’s network. Buyers seeking quotes for parts are responsible for defining the specific requirements for those parts. Please refer to our terms and conditions for more information.
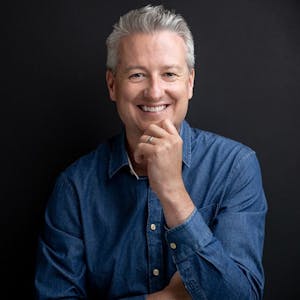