Silicone and polyurethane are both thermosetting polymers. They are typically processed in liquid form, and then begin internal cross-linking as the material cools within a mold. This ultimately causes the material to set (harden). While both materials are thermosetting polymers, they have vastly different chemistries and properties. Silicone is an inorganic polymer built on a silicon-oxygen backbone. Polyurethane, on the other hand, is an organic polymer made of a polyol and an isocyanate with a wide range of chemical configurations. Silicone has excellent thermal and UV resistance whereas polyurethane has excellent tensile strength and abrasion resistance. Each of these polymers is available in a number of different formulations that result in a wide range of physical and mechanical properties, allowing the design engineer to select the grade best suited to an application. This article will compare silicone vs polyurethane, comparing the two materials and discussing the differences between them in general terms.
What is Silicone?
Silicone is an inorganic thermosetting polymer. It is made up of repeating molecular units that form long chains. These polymer chains consist of a silicon-oxygen backbone, with hydrocarbon groups branching off of the main silicon-oxygen backbone. As a thermosetting material, silicone is typically mixed in liquid form. Upon mixing, it begins to cure. It undergoes an exothermic chemical reaction in which adjacent branches of the polymer chains join up, or cross-link with each other.
Silicone is typically processed via open mold casting, compression molding, or injection molding. It is broken down into three subcategories: LSR (Liquid Silicone Rubber), HCR (Heat Cured Rubber), and RTV (Room Temperature Vulcanizing). RTV silicone is further broken down into RTV-1 and RTV-2 types. RTV-1 is typically dispensed from a tube and begins curing when exposed to air. RTV-2, which is a mixture of a pre-polymer and a catalyst, begins to cure at room temperature when its two component parts are mixed together.
Silicones are available in many different hardnesses within the Shore A hardness scale, typically between Shore 10 A and Shore 90 A. Silicones have excellent high temperature, UV (ultraviolet), and ozone resistance but have poor cut and tear resistance, poor tensile strength, and poor abrasion resistance. For more information, see our guide on Silicone.
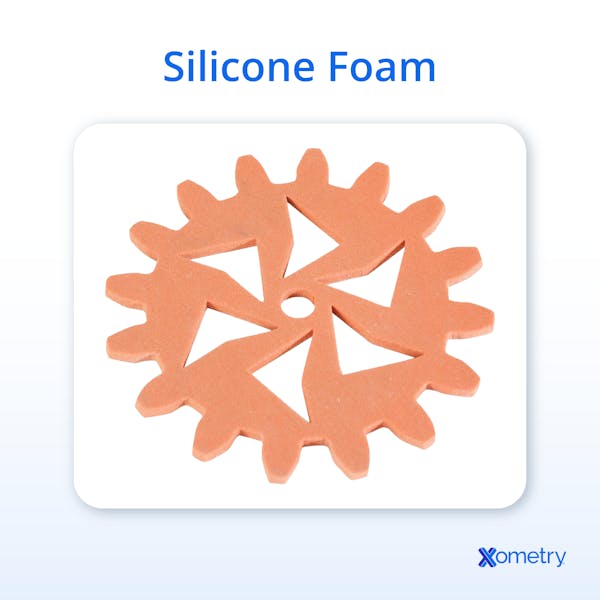
What is Polyurethane?
Polyurethanes are thermosetting organic polymers. They are made up of complex molecular chains that form hard and soft segments, where the soft segments give polyurethanes their flexibility, and the hard segments provide their strength. The term “polyurethane” covers thousands of different material formulations, generally categorized as either polyesters or polyethers. Figure 1 is an example of a polyurethane gear:
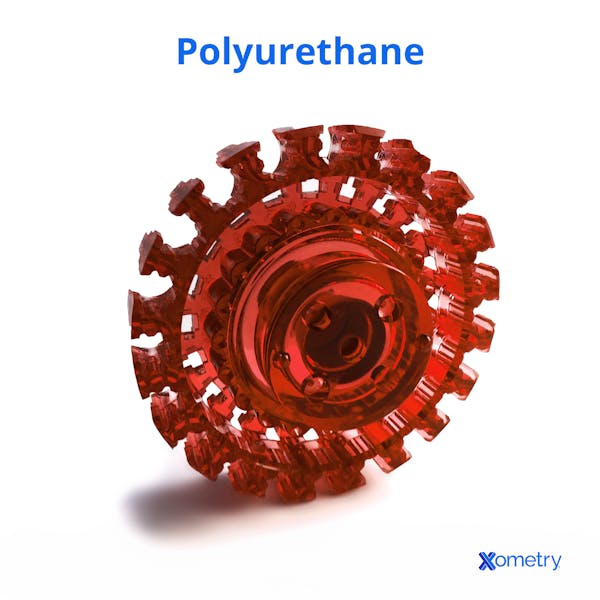
Polyurethanes can be processed using open mold casting, rotational casting, or reaction injection molding. Since they are thermosetting materials, polyurethanes are typically mixed in liquid form. A prepolymer is generally mixed with a catalyst, either at room temperature (for cold curing) or at elevated temperatures (for hot curing). Upon mixing, the polyurethane begins to cure in an exothermic (heat-releasing) reaction. Hot-cure polyurethane has better mechanical properties than cold-cure polyurethane.
Polyurethanes have excellent toughness and abrasion resistance. They can be produced in a wide range of hardnesses from Shore 35 A all the way up to Shore 70 D. Polyurethane can only be used at temperatures up to 80°C. It will begin to chemically break down at higher temperatures. Its mechanical properties, such as hardness and abrasion resistance, also begin dropping at elevated temperatures.
Silicone vs. Polyurethane: Applications and Uses
Polyurethane is used in a wide range of applications that benefit from its increased toughness and wear resistance. Some typical applications are listed below:
- Forklift wheels, skateboard wheels, and shoe soles.
- Impact arrestors on railways and elevators.
- Pipe linings, pump impellers, casings, seals, molds, and conveyor belts.
- Chute linings, vibratory screens, and cyclones.
- Electrical potting or encapsulation.
Silicone is available in many different forms with varying degrees of mechanical strength, thermal resistance, and biocompatibility. Some typical applications are listed below:
- High-temperature cookware like utensils and bowls.
- Molds, in some cases for casting polyurethane.
- Industrial sealing and bonding.
- Catheters, hoses, implants.
- Seals, and gaskets.
Silicone vs. Polyurethane: Physical Properties
The terms ”silicone” and “polyurethane” are both used loosely to refer to families consisting of hundreds of different compounds with extensive ranges of properties. Therefore, raw materials suppliers must be consulted for the properties of any specific formulation. Table 1 below shows comparisons between silicone and polyurethane at similar Shore hardnesses:
Properties | Silicone | Polyurethane |
---|---|---|
Properties Type | Silicone RTV-2 | Polyurethane Polyester |
Properties Hardness (Shore A) | Silicone 58 A | Polyurethane 70 A |
Properties Abrasion Resistance (DIN mm3) | Silicone — | Polyurethane 70 |
Properties Elongation (%) | Silicone 200 | Polyurethane 675 |
Properties Chemical Resistance | Silicone Resistant to high-temperature water, salt water, brake fluid, chlorinated hydrocarbons | Polyurethane Resistant to fuel, oil, solvents, and weak bases/acids |
Properties Melting Point (°C) | Silicone 250 | Polyurethane 80 |
Properties Heat Resistance | Silicone Excellent | Polyurethane Poor |
Properties Electrical Insulation | Silicone Behaves as an insulator | Polyurethane Behaves as an insulator, however, can absorb water, which negatively affects its insulator properties |
It must, however, be noted that the above two materials are often used in very different applications and a direct comparison between the two may not give the full picture.
Silicone vs. Polyurethane: Recyclability and Sustainability
Both silicone and polyurethane are thermosetting polymers that break down into harmful chemicals if heated past their maximum operating temperatures, and do not resolidify in useful form the way thermoplastics do. For this reason, while recycling silicone and polyurethane is theoretically possible, it is difficult, and most recycling facilities do not have the capability to economically recycle these materials. One potential method of recycling is mechanical granulation, i.e., grinding the material into small particles. These granules can then be used as filler materials.
Silicone and polyurethane are not considered to be sustainable materials, as they are not produced from renewable resources.
Silicone vs. Polyurethane: Cost
Silicone and polyurethane are advanced engineering materials. As such, they are costly. The cost of the material depends on the grade used and can vary wildly. For example, RTV-1 silicone is relatively inexpensive, whereas RTV-2 silicone is significantly more expensive. With polyurethane, cold-cast materials tend to be more expensive than hot-cast materials.
Alternative Materials to Silicone and Polyurethane
Silicone and polyurethane are thermosetting elastomers that do not have many alternatives. However (TPE) thermoplastic elastomers can be used as alternatives in some cases. Thermoplastic rubber (TPR) and thermoplastic polyurethane (TPU) can both serve as suitable alternatives to thermosetting silicone and polyurethane and can be processed using standard thermoforming techniques, like injection molding, rotomolding, and blow molding.
Summary
This article presented silicone and polyurethane, explained what they are, and discussed how to use both materials in manufacturing. To learn more about silicone and polyurethane, contact a Xometry representative.
Xometry provides a wide range of manufacturing capabilities and other value-added services for all of your prototyping and production needs. Visit our website to learn more or to request a free, no-obligation quote.
Disclaimer
The content appearing on this webpage is for informational purposes only. Xometry makes no representation or warranty of any kind, be it expressed or implied, as to the accuracy, completeness, or validity of the information. Any performance parameters, geometric tolerances, specific design features, quality and types of materials, or processes should not be inferred to represent what will be delivered by third-party suppliers or manufacturers through Xometry’s network. Buyers seeking quotes for parts are responsible for defining the specific requirements for those parts. Please refer to our terms and conditions for more information.
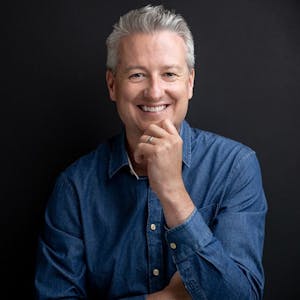