Laser fusion cutting refers to a laser cutting technique used to cut metals by first melting them and then blowing out the molten material using a high-pressure inert .gas. This process is used primarily on thin sheets and can prevent oxidation from forming on the cut edges.
Unlike laser flame cutting, all the energy in laser fusion cutting is provided by the laser, making these laser cutting machines less energy efficient. This article will describe the laser fusion cutting process, its advantages, disadvantages, and applications.
What Is Laser Fusion Cutting?
Laser fusion cutting is one method of laser cutting metal that is used in both CO2 and fiber laser cutters. This process relies solely on the energy provided by the laser to successfully cut through the metal. Unlike laser flame cutting, this process does not make use of oxygen to initiate an oxidation process that reduces the energy required for the laser. This technique is used primarily due to the exceptional finish that is produced and reduces or eliminates the need for post-processing by preventing oxidation on the cut edge.
How Does Laser Fusion Cutting Work?
Laser fusion cutting can be performed with a CO2 laser as well as a fiber laser provided the power levels are high enough for cutting metal. The laser begins by heating the metal to a molten state. Once this is achieved, a high-pressure stream of an inert gas like nitrogen or argon is blown out of the cutting head into the molten material, which is then ejected out the bottom of the plate. In some cases, oxygen can be used during the initial piercing phase to help cut through the plate, thereafter inert gas is used. As the beam moves through the material, it continues to melt the metal and the inert gas ejects the molten material from the cut. The inert gas also protects the cut edge from oxidizing and serves to cool it so that it won’t oxidize once the cutting head has moved on.
What Are the Advantages of Laser Fusion Cutting?
Laser fusion cutting is a popular laser cutting technique due to a range of advantages as listed below:
- Oxide-Free Cut Edge: The inert gas protects the hot cut edge from reacting with atmospheric oxygen and prevents any oxidation from occurring. This is especially effective for stainless steel parts which form an oxide layer on the cut edges that must be removed using a pickling and passivation process.
- Localized Heating: The inert gas needs to cool the cut to prevent oxidation. This has the added benefit of preventing heat transfer to the rest of the plate or sheet being cut. This means there is less thermal warping, which is especially common in stainless steel. As such, thin sheets can be cut into intricate patterns without any warping.
- Lower Energy Requirements Compared to Vaporization: Vaporization laser cutting techniques require that the material be heated to the point of vaporization. This requires significantly more energy when compared to fusion laser cutting which only needs to heat the material into liquid form.
- High-Speed Cutting of Thin Sheets: Fusion laser cutting is a high-speed production technology, especially with thin sheets. The cooling effect of the inert gas means that more energy can be utilized without the risk of warping thin sheets.
What Are the Disadvantages of Laser Fusion Cutting?
Despite the many advantages of laser fusion cutting, there are some disadvantages as listed below:
- High Energy Compared to Laser Flame Cutting: Laser fusion cutting makes use of inert gas during cutting. This means that all the energy required to liquefy the metal must come from the laser. This is in contrast to laser flame laser cutting, a process in which some of the energy is generated by the oxidation of the metal due to a continuous oxygen supply.
- Thin Sheet Metal Only: Due to the high energy requirements, only thin sheets are recommended for laser fusion cutting. Thicker sheets require excessive energy to melt through the plate, and in some cases, the melt will never reach through the entire width of the plate. This can be mitigated to an extent by using oxygen for the initial piercing action.
- Striation Formation: Striations are formed when the molten material in the cutting front reaches a critical point and is ejected by high-pressure gas. Every time this happens, a line is formed on the cutting edge which is also referred to as a striation. Striations reduce the quality of the cut edge and are undesirable.
For more information, see our guide on the Advantages and Disadvantages of Laser Cutting.
How Does Laser Fusion Cutting Differ From Other Types of Cutting?
Laser fusion cutting differs primarily in the type of cut edge that is left after cutting, i.e., unoxidized. Other cutting methods like laser flame cutting and vaporization cutting will produce a cut edge that has been oxidized. This oxidation must be removed for aesthetic purposes as well as to prepare the edge for subsequent welding. Laser fusion cutting requires more energy than laser flame cutting but less than vaporization cutting when referring to the cutting of metal. Laser fusion cutting is particularly useful for the cutting of thin stainless steel sheets due to the elimination of oxidation as well as ensuring that the heat is localized in the cut and not transferred to the rest of the plate to cause warping.
What Are Some Common Applications for Laser Fusion Cutting?
Laser fusion cutting is ideal for the high-volume processing of stainless sheet metal components. Some additional applications are listed below:
- Stainless steel piping.
- Finely detailed sheet metal cutouts.
- Etching and engraving glassware.
- Cutting titanium sheeting.
- Cutting magnesium alloy sheeting.
What Materials Can Be Used With Laser Fusion Cutting?
Laser fusion cutting is especially effective with materials that are sensitive to oxidation. Examples are listed below:
- Stainless Steel Sheet: Sheets of up to 15 mm can be cut using laser fusion cutting.
- Thin stainless steel tubing: Laser cutters equipped with a fourth axis can be used to cut thin tubing.
- Alloyed steel: Alloyed steel sheeting can be readily cut without the development of oxidation on the cut surface, meaning components can be welded without additional surface preparation.
- Aluminum: Aluminum sheeting can be cut using the laser fusion technique as aluminum produces a hard oxidation layer that can impede post-processing like anodizing.
- Magnesium Alloys: When oxidized, magnesium alloys produce a high-energy reaction. As such, they must be cut in an inert atmosphere.
- Titanium Alloys: Titanium is readily oxidized at high temperatures. As such, laser fusion cutting is a good option for cutting this material as it protects the cut edge from oxidation.
What Do Laser Fusion Cutting Machines Do?
Laser fusion cutting machines are designed to cut thin metal sheeting without warping the plate or producing oxidized cut edges. This means that parts cut on these machines can be welded without the need for post-processing.
What Gas Is Used in Laser Fusion Cutting?
Inert gasses like nitrogen or argon are often used in laser fusion cutting, with nitrogen being the most commonly used. This inert gas is used so that the edges are not oxidized during cutting by keeping oxygen away from the cut. In addition to this, some laser cutting machines also make use of oxygen to assist in initial piercing.
What Is the Procedure for Laser Fusion Cutting?
The laser fusion cutting process is very similar to other laser cutting processes with a few key differences as described below:
- The sheet is placed on the cutting bed and accurately positioned.
- Once in position, the laser head moves to the initial start point and begins heating the material until it has reached a molten state throughout the thickness of the plate.
- Once the molten state has been achieved, a high-pressure stream, up to 20 bar, of inert gas (typically nitrogen), is directed at the molten metal and begins blowing it out the bottom of the plate.
- The laser head then moves along the cut path while continuously heating the material to its molten point. The inert gas continues to blow the molten material from the cut.
- During cutting, the inert gas shields the high-temperature cut edge to prevent atmospheric oxygen from oxidizing it, similar in principle to the TIG welding process.
- The inert gas also serves to keep the heating localized to the immediate cut area, this prevents excessive heat from transferring to the rest of the plate, thereby minimizing any warpage of the thin metal sheet.
- Once the parts are removed, they do not need to be post-processed to mechanically or chemically remove oxidation from the cut edge and can be welded.
Is Laser Fusion Cutting Faster Than Other Types of Laser Cutting?
Yes, for thin sheets fusion laser cutting is faster than other cutting technologies like vaporization and laser flame cutting. This is due to the inert gas keeping the cut area cool; other techniques need to limit their speed so as not to add too much heat to the plate and cause warping. However, with thicker plates, laser fusion cutting is no longer comparatively fast.
Summary
This article presented laser fusion cutting, explained what it is, and discussed the process and materials used for it. To learn more about laser fusion cutting, contact a Xometry representative.
Xometry provides a wide range of manufacturing capabilities, including sheet cutting and other value-added services for all of your prototyping and production needs. Visit our website to learn more or to request a free, no-obligation quote.
Disclaimer
The content appearing on this webpage is for informational purposes only. Xometry makes no representation or warranty of any kind, be it expressed or implied, as to the accuracy, completeness, or validity of the information. Any performance parameters, geometric tolerances, specific design features, quality and types of materials, or processes should not be inferred to represent what will be delivered by third-party suppliers or manufacturers through Xometry’s network. Buyers seeking quotes for parts are responsible for defining the specific requirements for those parts. Please refer to our terms and conditions for more information.
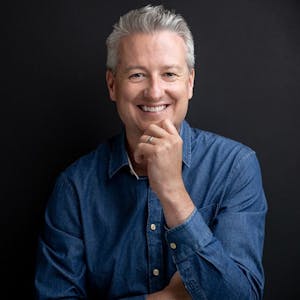