Arc welding is a highly versatile process that is used to create strong, permanent joints in metals. In arc welding, an electric arc created by direct current (DC) or alternating current (AC) heats the workpiece and the electrode to extremely high temperatures to melt a localized area of the two pieces to be joined. There are many variations in the basic arc welding process. Each type of arc welding has its own set of advantages and disadvantages which make it better-suited for a particular job, depending on the application. This article will review 11 types of arc welding and describe the applications and benefits of each.
1. Submerged Arc Welding
Submerged arc welding (SAW) is one of many types of arc welding that use a continuously fed electrode wire, but it is the only one that maintains the arc under a blanket of flux particles. The electric arc generated between the electrode and workpiece in SAW is covered at all times by granules of solid flux material. When a weld pool forms, the flux melts and partially vaporizes to form a protective liquid slag over the weld, as well as shield gas that prevents the workpiece material from reacting with atmospheric gasses such as oxygen and nitrogen.
Because of the blanket of flux, splatter and spark production is eliminated, which helps maintain a clean work environment. Additionally, the flux blanket helps to suppress toxic fumes and harmful UV radiation. However, the SAW process cannot be used in vertical or overhead positions, is limited to use on ferrous materials, and requires slag to be removed between each pass. SAW is commonly used to produce butt welds in pipelines and pressure vessels.
2. Flux-Cored Arc Welding
Flux-cored arc welding, or FCAW, is an arc welding process that employs a continuous-feed hollow electrode filled with flux. Once the arc is generated, a power supply provides a constant arc length. Since the electrode is cored with flux, shielding gas is not needed but can still be used as an extra precaution to prevent weld pools from reacting with elements in the air.
Because of the flux-cored electrode, FCAW can be used indoors or outdoors. Additionally, FCAW is great for welding contaminated or dirty workpieces. However, the disadvantages of FCAW include: higher costs for electrode wire and the need to remove slag after welding. FCAW is commonly used in construction and shipbuilding.
3. Plasma Arc Welding
Plasma arc welding (PAW) is a type of arc welding that uses a non-consumable tungsten electrode placed within the torch (welding gun) body. The electric arc ionizes a gas (a different gas from the shielding gas) that is emitted from the torch to produce plasma. Because of the electrode’s position in the weld gun and the geometry of the nozzle into which the plasma is released, the emitted plasma is separated from the shielding gas.
The advantages of PAW include the ability to produce deep, precise welds at a rapid rate and the ability for the process to be automated. Another advantage of PAW is that the workpiece can be approached from any angle. However, the disadvantages of PAW are: the equipment can be expensive, the emission of ultraviolet (UV), and the need for parts to be water-cooled. PAW is commonly used in electronics and the medical industry due to its precision and speed.
4. Carbon Arc Welding
Carbon arc welding (CAW) is the oldest type of arc welding. It uses a non-consumable carbon electrode typically made from graphite, and an electric arc to melt and join workpieces together. The process’s low cost, ability to be automated, and ability to produce joints with low distortion are some advantages of CAW. However, disadvantages include: porous joints and the possibility of carbon contaminating welds to produce carbides. CAW has largely been replaced by TIG (GTAW) welding but is still sometimes used to weld thin workpieces and for brazing, preheating, and post-heating of joints.
5. Electroslag Welding
Electroslag welding, also known as ESW, is a type of arc welding in which a pool of molten slag is formed in the joint area due to the heat generated from the electric current that passes between the workpiece and the electrode. Electroslag welding is a vertical process and works by first filling the gap between the adjoining materials with flux. Then, the arc is generated to weld the two parts together. The welder starts from the bottom of the gap between the parts and moves upward to weld the entire gap.
Electroslag welding has many advantages, including: the production of welds with little distortion, low slag consumption, and the ability to weld exceptionally thick materials together. Disadvantages of electroslag welding include welds with low strength, coarse weld surfaces, and the limitation on welding position to only vertical joints. Its advantages make electroslag welding an excellent option for welding large workpieces, especially in the marine and construction industries.
6. Stud Arc Welding
Stud arc welding, specifically capacitor discharge (CD) stud arc welding, is a type of arc welding where the arc is struck between a charged capacitor and the metal workpiece to which the stud will be welded. A charged capacitor on the tip of the stud is triggered to discharge electricity and is consumed during the welding process. An electric current passes through the stud and generates an arc between it and the base metal. After a pool of molten metal forms on the base metal’s surface and the stud begins to melt, the stud is forced into the pool and allowed to cool to form a strong joint. Stud welding is a quick process that doesn’t require prefabricated holes to be completed.
7. Atomic Hydrogen Welding
Atomic hydrogen welding is an arc welding method that utilizes an arc generated between two tungsten electrodes surrounded by hydrogen gas. The arc between the tungsten electrodes is generated by an exothermic reaction of hydrogen atoms combining into hydrogen gas and is used to join workpieces together.
Rapid welding speed and hydrogen gas that effectively acts as a shielding gas are two advantages of atomic hydrogen welding. Disadvantages of atomic hydrogen welding are: the process is expensive, is only effective in a horizontal orientation, and is dangerous due to highly flammable hydrogen gas in the presence of oxygen. Atomic hydrogen welding is not often used but can be used to weld thin sheet metal workpieces and different types of metals.
8. Shielded Metal Arc Welding (SMAW or Stick Welding)
Shielded metal arc welding (SMAW), also known as stick welding or flux-shielded arc welding, is a type of arc welding where both the consumable flux-coated electrode rod and the workpiece surface melt together to form the weld joint. Stick welding works by holding the rod close to the workpiece to generate the arc. Once the arc is generated, the welder methodically moves the clamped electrode rod to join the materials together. As the weld is created, the flux-coated rod is depleted and eventually replaced with a new rod.
Advantages of stick welding include low equipment cost, equipment portability, and the ability to weld in various environments including outdoors on windy days. However, stick welding is not ideal for thin workpieces and electrodes must be replaced frequently. Regardless, stick welding is commonly used in a variety of industries including construction, mining, heavy machinery, oil and gas, and more.
9. Gas Metal Arc Welding (MIG Welding)
Gas metal arc welding (GMAW), also known as MIG welding, is the arc welding process in which a continuously fed wire from a welding gun is used as the electrode. A shielding gas, typically an argon/carbon dioxide blend, protects the molten weld pool from oxidizing and interacting with O2 and N2 in the air. MIG welding works by striking the wire against the workpiece and pulling it back to generate an arc. Once the arc is generated, the wire is slowly fed out of the welding gun as adjoining materials are slowly welded together.
Easy control of the welding process, fast welding, and welds with high quality are all advantages of MIG welding. Cumbersome welding equipment including gas canisters and welding equipment make on-demand welding more difficult. Additionally, burning through materials roughly 1/16” and smaller in thickness, and an inability to weld in various environments are disadvantages of MIG welding. MIG welding's advantages in speed and high-quality weld production make it an attractive process in the aerospace industry.
10. Gas Tungsten Arc Welding (TIG Welding)
Gas tungsten welding (GTAW), also known as TIG welding, is a type of arc welding where a nonconsumable tungsten electrode is used to conduct electricity and melt materials together and form a weld joint. An inert shield gas such as argon or nitrogen is released while a shroud around the toch ensures the gas protects the weld area during the welding process.
Advantages of TIG welding include offering operators easy control over the welding process, creating the strongest bond out of any type of arc welding, and producing a contaminant-free weld compared to other types of arc welding. Disadvantages of TIG welding include being slower than other types of welding, requiring more experienced operators, and not being easily automated. TIG welding is often used in applications where joints that are both strong and ductile are required.
11. Drawn Arc (DA) Stud Welding
Drawn arc (DA) stud welding is a type of arc welding where the operator uses a stud loaded onto a welding gun to weld a stud to a base metal. Stud welding by lifting the stud to a predetermined height above the base metal. When lifted, an arc develops between the stud base and the base material to create a pool of molten metal directly underneath the stud. Afterward, the stud is forced into the pool and held in place until the molten metal cools and solidifies.
The advantages of DA stud welding are that the process is fast and welds can be achieved from one side of the workpiece. Additionally, holes for the studs do not need to be prefabricated. DA stud welding is often used when the other side of a workpiece is inaccessible.
How to Choose the Best Type of Arc Welding For Your Needs
With so many variations on the basic arc welding process available, it can be difficult to know which method is best for a given application. The table below offers tips on how to choose the best type of arc welding for a particular project:
- Consider the materials of the workpieces to be joined. Some types of arc welding, such as FCAW, can only be used on ferrous materials while others, like plasma welding, can be used on all types of metals.
- Consider the position of the weld joint. Will welds be completed horizontally, vertically, or at an angle? Some welding processes, like ESW, are ideal for vertical-orientation welding.
- Consider the location where welding will occur and pick the best type of welding for it. Some types of welding, like stick and FCAW, can be completed outdoors in windy and rainy conditions while others, like atomic hydrogen welding and submerged arc welding, need a highly controlled environment. Additionally, available electrical power will vary depending on the welding location.
- Consider welding volume. Some welding processes, like electroslag welding and MIG welding, are ideal for higher-volume production and can be automated while others, like TIG welding and SAW, are better for lower-volume production or specialty projects.
What Type of Arc Welding Uses a Nonconsumable Tungsten Electrode to Produce the Weld?
Gas tungsten arc welding (TIG) is a type of welding that utilizes a nonconsumable tungsten electrode and a filler wire to produce the weld. TIG welding is best for welding applications that require greater welding control, high-strength joints, and defect-free welds. MIG is a great alternative if welding speed is a critical factor in a manufacturing operation.
Which Arc Welding Processes Use a Continuously Fed Consumable Wire Electrode?
MIG, FCAW, SAW, and ESW welding, are all arc welding processes that uses a continuously fed wire that acts as the electrode. The four welding processes are briefly described below:
- MIG welding uses a continuously fed wire and an inert shielding gas to protect the weld pool.
- FCAW uses a continuously fed flux-cored electrode and does not require shielding gas to protect the weld pool.
- SAW uses a continuously fed wire electrode and flux that blankets the welding area to protect the weld pool.
- ESW uses a continuously fed wire electrode and a blanketed flux to protect the weld pool in vertically oriented joints.
What Type of Arc Welding Produces a Molten Slag Pool Between Two Thick Metal Pieces?
Electroslag welding (ESW) is an arc welding process that produces a molten slag pool between two materials. It is a vertical welding process that is great for joining large parts up to 300 mm thick. Therefore, electroslag welding is often used in shipbuilding, high-rise construction, and the fabrication of large storage tanks.
What Type of Arc Welding Uses a Plasma Arc to Create the Weld?
Technically, all arc welding processes make use of ionized gas, or plasma, to complete the electrical circuit conducting heat to the weld zone. But one arc welding method, plasma arc welding (PAW) confines and shapes the arc to achieve higher energy density. This advantage can be converted to higher welding speeds, deeper penetration for thick materials, or more precise, smaller welds on thin materials. TIG (GTAW) welding is a good alternative to plasma arc welding if welding speed is not a critical concern.
What Type of Arc Weld Is the Strongest?
TIG welding is considered to produce the strongest arc weld joints. In TIG welding, tungsten, which has one of the highest melting points out of any element on the periodic table, is used as the electrode. The intense heat generated by TIG welding, over 6,500 °F, means parts need more time to cool. Consequently, the slow cooling rate leads to high tensile strength and ductility in the joint.
What Is Arc Welding?
Arc welding is a process that joins materials together by using an electric discharge to rapidly heat and melt the adjoining materials. The electric arc in a welding process is produced by a direct current (DC) or alternating current (AC) that passes through a consumable or non-consumable electrode. Electrodes are typically made from electrically conductive materials such as copper, mild steel, brass, and aluminum that are coated with a flux coating that protects the electrode and the adjoining materials from reacting with elements in the air. The molten weld pool in all arc welding processes must be protected either by using inert shielding gasses like argon or oxygen or by using flux. Flux coatings are typically made from materials like borax, hydrochloric acid, and zinc chloride, among other things. Arc welding is a joining process used in many industries, including automotive, aerospace, construction, oil and gas, power, and more.
How Does Arc Welding Work?
While there are many different types of arc welding processes, the underlying concepts that enable materials to be melted and joined together are similar for all. Arc welding works by melting, and fusing metals together using the energy generated by electrons trying to complete the electrical circuit across the gap between an electrode and the ground (the workpiece). The high-energy electrons ionize the gasses in the gap so that they conduct current into the work, heating and melting it. The arc between the electrode and the workpiece can reach extremely high temperatures of around 6,500 °F that can easily melt base materials and create pools of molten material to join workpieces together. Once the arc is generated, the electrode is moved along the planned path of the weld joint. Since metals are chemically reactive to elements in the air, a shielding gas such as argon, oxygen, or nitrogen is dispersed to protect the molten metal and prevent oxides and nitrides from forming in the joint. As the molten metal pool between the materials cools, it hardens to form a strong, permanent joint.
What Is the Main Purpose of Arc Welding?
The main purpose of arc welding is to create a strong, permanent joint between two metals in a cost-effective manner. While other methods can be used to join materials together, arc welding produces joints with unmatched strength. Additionally, arc welding equipment is affordable, widely available, and portable which enables welding to be carried out on-site, in many different environments.
Summary
This article presented the different types of arc welding, explained each one, and discussed their various benefits and uses. To learn more about arc welding, contact a Xometry representative.
Xometry provides a wide range of manufacturing capabilities, including sheet cutting and other value-added services for all of your prototyping and production needs. Visit our website to learn more or to request a free, no-obligation quote.
Disclaimer
The content appearing on this webpage is for informational purposes only. Xometry makes no representation or warranty of any kind, be it expressed or implied, as to the accuracy, completeness, or validity of the information. Any performance parameters, geometric tolerances, specific design features, quality and types of materials, or processes should not be inferred to represent what will be delivered by third-party suppliers or manufacturers through Xometry’s network. Buyers seeking quotes for parts are responsible for defining the specific requirements for those parts. Please refer to our terms and conditions for more information.
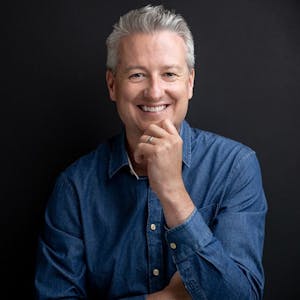