Spot welding is a contact welding technique used extensively in the automotive industry for strong and aesthetic welds. It works by using two electrodes to pass a current through the weld spot to increase the heat of the weld site, melt the metal, and fuse the parts. Spot welding is efficient and can be automated, however, it is limited to 3 mm thick welds.
What Is Spot Welding?
Spot welding works by applying an electrical current across the mating surfaces of two (or more) pieces of metal to melt and bond them. This is achieved using two copper alloy probes which apply the current across the metals. The resistance to the applied current increases the temperature of the metal, which in turn melts it. The probes also apply pressure to keep the material in place.
What Is the Other Term for Spot Welding?
Spot welding is known as “spot welding” because it leaves spot marks behind. However, it is also known as “resistance welding” or “spot resistance welding” as it relies on the resistance of the two materials to work.
What Is the Importance of Spot Welding?
Spot welding has an important role in car manufacturing in which spot welders can be used in an automated assembly line. The automated assembly line, and therefore spot welding, increase overall production capacity while keeping costs low.
What Is the Purpose of Spot Welding?
The purpose of spot welding is to fabricate two or more pieces of metal, usually in sheet form. By using spot welding, a structural joint can be made with an automated process without filler materials or post-processing.
How Does a Spot Welding Work?
Spot welding is a three-step process that involves aligning the workpiece, applying electrode pressure, and then using current to bond the metal. The three steps are described below in detail:
- Aligning the Metal: First align the metals correctly, as once welded they cannot be changed. The alignment must be secured properly as the process will cause the metal to warp. The welding locations must follow an order which will minimize warping. For example, welding two sheets may require welding one corner, then the other, then the middle. This will prevent the weld from deforming as the joint is welded from one corner to another.
- Applying Pressure: The second stage of welding is applying the right amount of pressure to the electrodes. By applying pressure, the molten metal created by the resistance of the current traveling through the separate pieces will be forced together. The use of copper electrodes is common as they can withstand heat and pressure without oxidizing.
- Current Flow: Lastly the current is applied. If the welding is not automated, a foot pedal is usually used to apply the current. The time and intensity of the current applied depends on the thickness of the material. For a short time after the current stops the metal will remain clamped to allow the metals to fuse properly.
What Are the Key Parameters of Spot Welding?
Four main variables need to be considered when spot welding. They are pressure, current, tip area, and welding time cycle.
The application of too much pressure from the electrodes can cause material thinning and cracking. Conversely, not enough pressure can cause a weak weld due to inadequate fusion. As a rule of thumb, the materials being welded should not reduce by more than 25% of their thickness. The current used directly affects the heat produced for welding. To choose the right current, the materials’ resistivity, and melting point needs to be considered.
The tip size of the electrodes controls the weld size. A size that is too small will result in a weaker joint, and a size too big can create voids within the weld.
The weld time cycle is the amount of time the metals are exposed to pressure and current.
What Are the Applications or Uses of Spot Welding?
There are multiple applications of spot welding which include the: automotive industry, electronics industry, nail manufacturing, and medical industry. The automotive industry favors spot welding as it is quick, reliable, and cost-effective. Spot welding can also be performed by an automated robot on an assembly line which drives production up and costs down with consistent quality. The electronics industry uses spot welding as it can produce welds at lower temperatures than other methods. This protects components from overheating during manufacture. The manufacturing of nails employs spot welding to fuse the nails with a steel wire to make rolls of nails. This method is very fast at about 1,200 nails/minute. In the medical industry spot welding is used to fasten dental implants.
How To Spot Weld?
The spot welding process is relatively simple. The process below lays out in four steps how to spot weld:
- Hold the two metal parts firmly.
- Apply pressure to the site to be welded using the electrodes.
- Apply a sufficiently high current through the electrodes.
- Keep the electrode pressure on the weld site while it solidifies.
What Are Tips and Strategies To Have a High-Quality Spot Weld?
There are some tips and strategies that will increase the ability to achieve high-quality spot welding. The most important tip is to read the user manual of the spot welder to understand how to use it best! Other tips include:
- Use shorter tongs (electrodes) for more heat. Long tongs are susceptible to bending, reducing pressure, and causing misalignment.
- Ensure there is never a gap between the two pieces of metal being welded.
- Make sure the two electrodes align properly for proper current flow.
- The geometry of the tip will affect the finished look of the part.
- Keep electrode tips clean to ensure proper contact for the current flow.
Is Spot Welding Hard?
No, spot welding is not hard, it is relatively simple as long as the process is followed correctly. While this is true for low-carbon steels, high-carbon steels can be harder to weld due to their low resistance, requiring more current to heat up the workpieces. This also results in spot welds that are brittle and prone to cracking.
What Are the Materials That Can Be Used in Spot Welding?
A range of metals can be spot welded. The metals best suited for welding have low thermal conductivity and high resistance. Metals that can be spot welded include:
1. Aluminum
Aluminum is becoming a more popular spot welding material as it overtakes the use of steel in the automotive industry in which light weight is important. Aluminum has a high electrical and thermal conductivity which makes it hard to spot weld. To overcome this problem, a current two or three times more intense than that used for steel is required to melt and weld aluminum. Because of this, the electrodes used must be water-cooled. For more information, see our guide on what is aluminum?
2. Copper
Spot welding copper requires special tooling. Copper’s high conductivity of heat and electricity means it tends to weld itself to standard copper alloy electrodes. To prevent this, tungsten and molybdenum electrodes are used. For more information, see our guide on copper properties.
3. Steel
Steel is a mixture of carbon and iron that combine to make a much stronger substance than its constituent materials. Steel is one of the easiest and most common materials to spot weld. Low-carbon steels are easier to weld because of their low thermal conductivity and high resistance. Steel is spot welded in the automotive industry in the manufacture of car chassis and bodies. For more information, see our guide on the composition of steel.
4. Nickel
Nickel is a silvery white metal used in the production of cells. Spot welders are used to weld the terminals of battery cells to nickel strips. Nickel is also welded in the production of the cells in a battery.
5. Brass
Brass is a soft metal that can be spot welded to create pipes, jewelry, and musical instruments. Brass has a low melting point and is very malleable which makes it easy to spot weld and easy to form into complex geometries. For more information, see our guide on the composition of brass.
6. Zinc-coated Steel
The main difference between welding zinc-coated steel and non-coated steel is that a higher welding current is required and the coating will react with the electrode, which shortens its life. Zinc has a lower melting point than steel, and so will melt first and mostly be squeezed out of the weld.
What Are the Materials That Cannot Be Used in Spot Welding?
Generally, materials that cannot be welded are non-metallic materials including composites, plastics, and wood. Some materials are hard to weld, usually due to their high thermal conductivity, low conductivity, or high melting point.
What Type of Laser Is Used in Spot Welding?
Laser spot welding is a more modern process. Laser spot welding is a non-contact weld that is faster and more cost-effective than electrode spot welding. Fiber, CO2, and Nd:YAG lasers are used for spot welding. Fiber lasers offer better precision, better electrical efficiency, lower maintenance, and lower operating costs over CO2 and Nd:YAG laser spot welding machines.
How Strong Is a Spot Weld?
A spot weld is a very strong way to fabricate two pieces of metal. However, the particular strength of a weld is determined by many factors including the size of the weld, the thickness of the material, the reduction in thickness of the weld, and the presence of defects. One of the biggest limiting factors of the strength of a spot weld is that it can only be used on metal no more than 3 mm thick.
How Much Does a Spot Welding Machine Cost?
Spot welding machines will vary in price depending on the maximum power output of the machine. Prices start around $1,500 for a handheld 6 Kva spot welder and reach up to $60,000 for a high-powered spot welder.
How Long Does a Spot Welding Machine Last?
A good spot welding machine can last over 20 years. However, the life expectancy of a spot welding machine will vary with its usage and maintenance. A machine that is better maintained will last longer. Some key signs to look out for to determine if a new spot welder is required are:
- Repair Cost: A machine may last forever, but a significant increase in repair costs makes it worth considering a new machine.
- Productivity: Buying a new machine may be worth the investment if the existing machine is slowing down or there are more modern machines that weld faster and will increase productivity.
- High Energy Bills: Spot welders use a lot of energy, and as the parts of the machine get older they will increase in resistance and use more energy, in which case it may be worth upgrading.
What Are the Advantages of Spot Welding?
Spot welding is advantageous over other forms of welding as it has both good functional and aesthetic properties which are required in the automobile industry. Other advantages of spot welding include:
- It is fast and efficient, with minimal post-processing required.
- Does not require extensive training.
- Safer than other welding processes which require gases and open flames.
- Can be effectively performed by robots.
- Can join more than two sheets of metal at once.
- No filler material is required.
- Cost effective.
What Are the Disadvantages of Spot Welding?
There are some drawbacks to spot welding, most notably that a small misalignment in the welding apparatus can result in a failed weld. Other disadvantages include:
- It is possible to permanently deform the metal due to a bad weld—which results in a high scrap rate.
- It does not work on metal thicker than 3 mm.
- The welding joint is localized, which can lead to a weaker weld.
- A small variability in pressure can cause large changes to product quality.
- The electrodes fail due to thermal cracking.
What Are the Side-Effects of Spot Welding?
Spot welding can be particularly hazardous—which can result in side effects. Other side effects experienced include:
- Creation of harmful gases.
- The burning risk from hot metal/hot electrodes.
- Electrical sparking.
- Potential fire risk.
Summary
This article presented spot welding, explained it, and discussed how it works and its various advantages. To learn more about spot welding, contact a Xometry representative.
Xometry provides a wide range of manufacturing capabilities, including sheet cutting and other value-added services for all of your prototyping and production needs. Visit our website to learn more or to request a free, no-obligation quote.
Disclaimer
The content appearing on this webpage is for informational purposes only. Xometry makes no representation or warranty of any kind, be it expressed or implied, as to the accuracy, completeness, or validity of the information. Any performance parameters, geometric tolerances, specific design features, quality and types of materials, or processes should not be inferred to represent what will be delivered by third-party suppliers or manufacturers through Xometry’s network. Buyers seeking quotes for parts are responsible for defining the specific requirements for those parts. Please refer to our terms and conditions for more information.
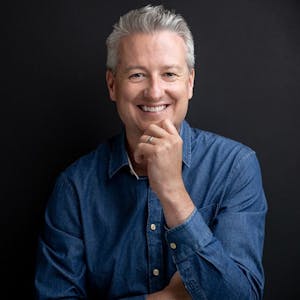