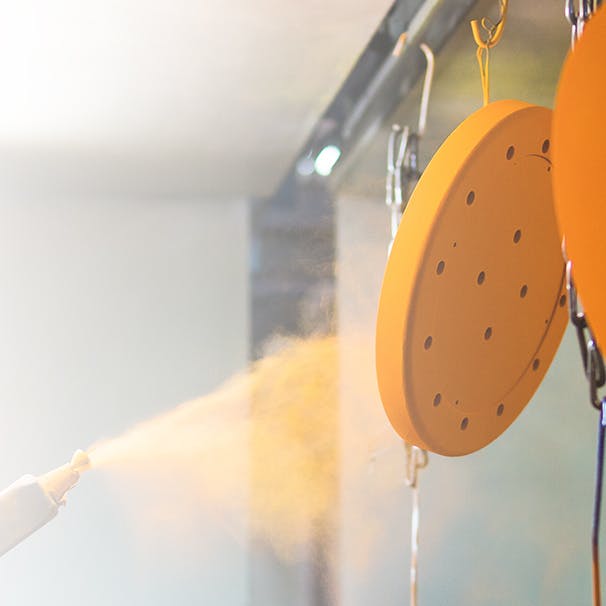
Anodized Parts On-Demand
Instant quotes on build-to-print machined parts, including anodizing and other finishes
ITAR Registered
ISO 9001
ISO 13485
IATF 16949
AS9100D Certified
Anodizing Overview
Anodizing is a common electrolytic passivation process often used to grow the thickness of the natural oxide layer on the surface of metal parts. It improves corrosion and wear resistance and provides better adhesion for paint primers and glues than bare or untreated metal. Anodizing changes the microscopic texture of the metal's surface by changing the crystal structure of the metal. Thick anodized coatings are usually porous, so sealing processes are often needed to help achieve corrosion resistance. Anodic films are usually much stronger and adhere more easily than paint and metal plating, but sometimes more brittle. This makes them less likely to crack and peel from aging and wear but more susceptible to cracking from thermal stress. Anodic films can also be used for cosmetic effects, either with thick porous coatings that can absorb dyes in any number of colors or with thin transparent coatings that add interference effects to reflected light. Anodic films are most commonly applied to protect aluminum alloys. However, processes also exist that allow these films to be applied to other common materials as well.
Anodizing Types Available from Xometry: Type II Anodize, Type III Hard coat, Type III w/ PTFE
- Improved Aesthetics
- Better Bonding
- Wear Resistance
- Corrosion Resistance
- Heat Dissipation
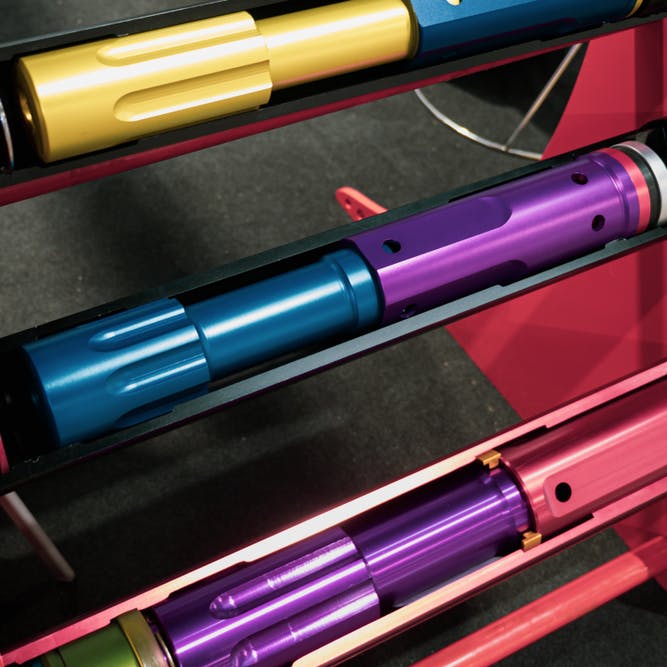
A World-Class Network of Turnkey Manufacturing at Your Fingertips
Competitive Pricing
Massive Network Capacity means Quick Lead Times and Competitive Prices
Fast Quoting
Instant Quoting of Parts with Anodize or Other Finishing without the Wait
Streamlined Communication
Xometry Manages Your Project and Supply Chain to Assure Quality and Timeliness
Other Finishing Services Available
Anodizing
- Type II Anodize
- Type III Hard coat
- Type III w/ PTFE
Metal Plating
- Copper Plating
- Electroless Nickel
- Electrolytic Nickel
- Nickel Plating
- Nickel Sulfamate
- Nickel Watts
- Tin
- Zinc
Adhesives and Coatings
- Black Oxide
- Dry Film Lubricants
- Powder Coat
- Wet Paint
Conversion and Pretreatments
- Chem Film
- Chromate Conversion Coating
- Heat Treat
- Passivation
- Pickle and Oil
Surface Treatments
- Bead Blasting
- Electropolishing
- Etching
Part Marking
- Ink Stamping
- Laser Marking
- Silk Screening
Heat Treatments
- Annealing
- Carburizing
- Cryogenic Treatment
- Flame Hardening
- Hydrogen Embrittlement Relief
- Induction Hardening
- Nitriding
- Stress Relieving
Certifications
- AS 9100D
- ISO 13485
- ISO 9001:2015
- ITAR
- NADCAP
- RoHS
Turnkey Part Finishing Services at Xometry
Upload Your CAD and Drawing
Use the Xometry Instant Quoting Engine® to securely load projects and specify your part requirements and quantities.
Order Parts
Order your parts through our automated checkout or with a purchase order. We'll take it from there.
Track Your Order
Xometry's platform provides visibility of your project, with milestones, updates, and tracking information all in one place.
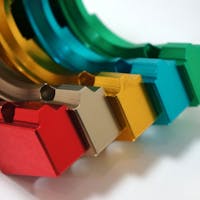