Plasma cutting is a process that delivers plasma (a highly charged particle stream) via a cutting torch to quickly cut through metal items. The plasma nozzle applies an electric current to a high-velocity jet of gas. This ionizes the gas and forms a plasma that melts/vaporizes its way through metal to create a clean, precise cut.
The plasma is formed by sending an electric current through a gas (typically compressed air or nitrogen) which is then forced through a small nozzle. As the gas passes through the nozzle, it gets superheated and ionized, creating plasma. The plasma is directed toward the metal workpiece in a narrow stream. Its intense heat melts and vaporizes the metal, creating a narrow kerf or cut. The thicker the material, though, the wider the kerf.
Plasma cutting is common in metal fabrication, automotive repair, and heavy equipment manufacturing. It allows for precise cuts in a variety of metals with thicknesses from ⅛ inch to ¾ inch (in steels) and can be used on both ferrous and non-ferrous materials. This article will describe what plasma cutting is, how it works, where it is used, its advantages and disadvantages, and the materials that can be cut.
What Is Plasma Cutting?
A plasma cutter’s metal-penetrating plasma stream carries a large amount of energy. On contact with the electrically conductive target material, the ionized gas stream reverts instantly to its natural state, releasing all of the ionization energy in one highly focused point on the metal. This release of energy melts/vaporizes the material that it contacts and the gas stream ejects any molten material from the cut. The cut point travels rapidly through the metal, allowing fast, deep cuts. The gas stream is generally composed of argon, an argon/hydrogen mix, or nitrogen to keep the removed metal from burning (oxidizing) during the process. Burnt metal can interfere with the cut quality and generate significant additional heat in the target.
Air plasma cutting is reserved for lower-reactivity metals such as stainless steel. However, it requires an electrode made from zirconium or hafnium to reduce oxidative destruction at the arc point.
Plasma cutting was first demonstrated by Dr. Robert Gage at Union Carbide in 1957 as a substitute for oxy-acetylene cutting. Later developments, particularly in the oil industry, allowed plasma cutting to be done underwater.
Where Is Plasma Cutting Being Used?
Shipbuilding, heavy machinery, construction, and military manufacturers all make extensive use of plasma cutting. The technology allows the fast and low-cost processing of large steel, stainless steel, and other metal components.
What Are the Advantages and Disadvantages of Plasma Cutting?
The advantages of plasma cutting are listed below:
- Faster piercing than oxy-fuel and doesn’t require the pre-heat that oxy-fuel needs.
- Cheaper to run than oxy-fuel per cut length.
- Narrower, more precise cuts than oxy-fuel.
- Reasonable thickness range — from ⅛ inch up to ¾ inch steel.
- Simpler and less energy-intensive than similarly capable laser cutters.
- The equipment can be portable (for hand use).
- Hand plasma cutting can be precise in skilled hands, though CNC plasma cutting is more reliable and precise.
- Can be performed on a wide variety of materials and requires less setup and tuning than laser cutting.
- Inherent safety feature: the power shuts off when the arc breaks.
The disadvantages are listed below:
- More limited in terms of part thickness than laser cutting. The gas stream remains less coherent with depth, making for larger kerfs than laser cutting.
- Minimum part thickness is also limited. The initial part of the cut requires support to prevent it from becoming excessively violent and destructive.
- The kerf is angled due to expansion in the gas stream. Perpendicular edges are not possible without post-processing (such as an angle-offset second cut).
- Plasma cutting is dirty, noisy, and produces irritating dust.
What Are the Materials Plasma Cutting Can Cut?
Any conductive material can be cut with plasma, although the technique is rarely used on anything but metals and composites. A particular exception to this rule is semiconductor substrates, which can still accept plasma cutting. Examples of the most common materials are:
- Aluminum
- Brass
- Carbon steel
- Copper
- Expanded steel
- Mild steel
- Stainless steel
How Much Does a Plasma Cutter Machine Cost?
Handheld plasma cutters are widely available for as little as $1,000 for a device of moderate capability. CNC plasma cutting systems, on the other hand, go for around US$30-50k for highly capable equipment.
How Does Plasma Cutting Work?
The plasma is formed by an electrical arc running from the cutter electrode to the workpiece. A (usually) inert gas stream confines the energy of the plasma to a small-diameter spot on the target material, immediately melting it. The vapor and melted material are then ejected by the gas stream, which also cools the target. The melt/ejection progresses rapidly through the target thickness in the form of a cut that widens with depth.
What Are the Safety Equipment Used When Plasma Cutting?
Personal safety gear is a must when plasma cutting. Hot splash and irritating dust get ejected violently from the cut. The process is also noisy, as the gas stream and arc are fast and energetic. The safety equipment for plasma cutting is listed below:
- Goggles
- Breathing filter
- Coveralls
- Gloves
General environmental safety gear is also required at most sites. Some examples are:
- Signage to warn others of the process
- Barriers to keep others away
- Screens to block light and material splash
For more information, see our guide on Safety Gears when using Laser Cutters.
Common FAQs About Plasma Cutting
What Are the Best Alternatives for Plasma Cutting?
For most applications, the closest alternative process to plasma cutting is laser cutting. The methods are closely related in that they use directed energy to melt/vaporize the target material and a gas or air stream to clear debris. Plasma cutting was developed to replicate and improve on oxy-fuel cutting, a process that is still widely used as a simpler but low-precision alternative. For more information, see our guide on Alternatives to Laser Cutting.
Is it Possible to Cut Titanium With a Plasma Cutter?
Yes, titanium can be cut with a plasma arc. However, some additional precautions are required:
- The splash is lightweight and highly energetic, so it can easily ignite nearby material. Remove all combustible materials and keep fire suppression equipment on hand. Shield the operator from splash.
- Cut quality will be highest with an argon or argon/hydrogen gas stream. Nitrogen shielding gas will cause the cut quality to deteriorate. Air must not be used because it can easily allow ignition.
Can a Plasma Cutter Cut Reflective Materials?
Yes, a plasma cutter can cut reflective materials. The albedo of the cutting target has no effect on the plasma arc since energy is imparted by ionized atoms rather than photons.
What Is the Difference Between Plasma and CNC Plasma Cutting?
The difference between plasma cutting and CNC plasma cutting lies in the tools involved. Plasma cutting was first developed in the 1950s and 1960s as a hand-torch or simple pass-jig process. The advent of CNC machines in the 1960s and 1970s led to experiments with mounting a torch onto a CNC X-Y transport mechanism, allowing precise control and repeatability without requiring the same level of operator skill. For more information, see our guide on CNC Machining.
Summary
This article plasma cutting, explained what it is, and discussed the manufacturing process in detail. To learn more about plasma cutting, contact a Xometry representative.
Xometry provides a wide range of manufacturing capabilities, including plasma cutting and other value-added services for all of your prototyping and production needs. Visit our website to learn more or to request a free, no-obligation quote.
Disclaimer
The content appearing on this webpage is for informational purposes only. Xometry makes no representation or warranty of any kind, be it expressed or implied, as to the accuracy, completeness, or validity of the information. Any performance parameters, geometric tolerances, specific design features, quality and types of materials, or processes should not be inferred to represent what will be delivered by third-party suppliers or manufacturers through Xometry’s network. Buyers seeking quotes for parts are responsible for defining the specific requirements for those parts. Please refer to our terms and conditions for more information.
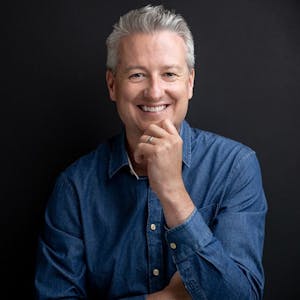