No doubt you’ve heard a lot of hype around 3D printing and additive manufacturing in the last few years, setting an expectation (in the media) that the “traditional” factory will soon be no more. The talk of miraculous new methods, of the direct printing of plastic, rubber and metal parts and the military and orbital printing of replacement parts is heralding a new dawn.
Maybe.
However, in one sector, the impact is very real and immediate and at least some of the hype is not totally misplaced!
With the rapid advances taking place in 3D printing technology, the aerospace industry is at the start line of a revolutionary journey, especially in the field of lower precision and simpler function structural components. 3D printing has emerged as a game-changing technique for rapidly creating intricate and custom-made parts, just so long as you’re not trying to find low-cost solutions.
3D printing can be used to make exceptionally lightweight and durable components of otherwise hard to manufacture design, maximizing performance and fuel efficiency while adhering to the very stringent safety standards in the sector. To understand the full potential of this groundbreaking technology, it is helpful to examine the core facts and leading edge expectations of 3D printing and how they might apply to aerospace manufacturing requirements.
In this article we will explore the complexities of 3D printing and how it is transforming the future of structural component fabrication in the aerospace sector, providing you with a primer to be able to extend your knowledge from a confident (and hype free) start point.
What Is the Purpose of 3D Printing of Aerospace Structural Components?
The main goal of 3D printing for structural aerospace components is to create parts in a way that is both commercially viable and strictly complies with applicable safety and environmental standards and aircraft safety demands. Rapidly producing intricate, lightweight parts and custom-made components that allow fast maintenance/development cycles and maintain the performance of both aircraft and spacecraft helps to deliver reliable/safe and cost-effective flight. Intricate geometries that are slow or impossible to produce using conventional methods can now be made fast, using 3D printing. The aerospace industry is beginning a new innovation process, thanks to 3D printing.
Structural Component Examples
Aerospace structural components that lend themselves to additive manufacture include:
- Fuel nozzles.
- Turbine blades.
- Unmanned aerial vehicles.
- Satellite Frames.
- Control surface actuators
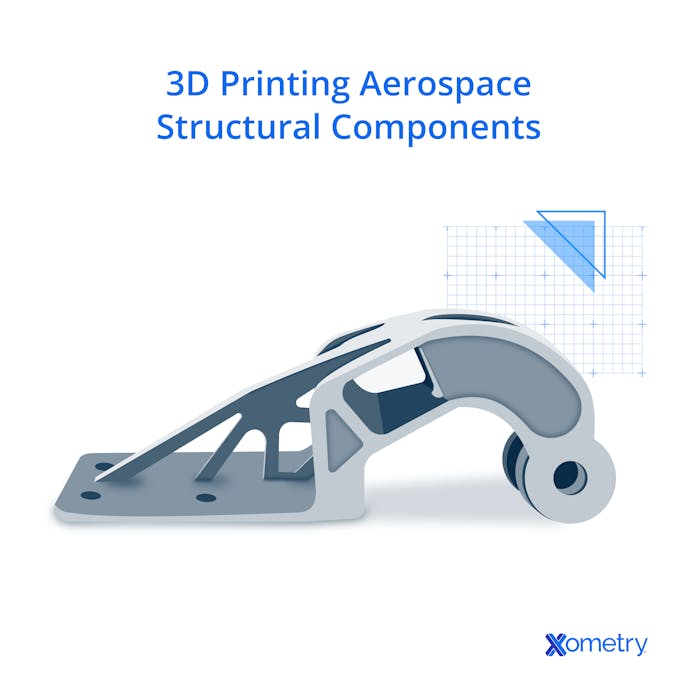
How it Works
Aerospace structural and functional components are being 3D printed using CAD (Computer-Aided Design) data processed into real objects by depositing and fusing material, layer by layer to rapidly build up finished parts. The following list outlines this process in more detail:
- A CAD designed 3D model serves as the foundation of the process.
- To create the component, the 3D printer build setup software interprets the design into a series of slices and building parameter instructions that can be read by the printer.
- The 3D printer places materials—such as metals or polymers, in filament, liquid or powder forms—onto the build platform, fusing it to itself and to the layer below.
- Layer by layer, the height builds up until the component is finished.
- The part is removed, cleaned, and post-processed. This can be manual or automated and may involve support structure removal, media blasting, or secondary finishing.
- Where higher precision is required (such as bearing faces or hole diameters) some post-machining may be needed.
In addition to rapidly building parts with complex geometries, reducing material waste, and producing lightweight components with improved performance, 3D printing offers the engineer more design freedom than other fabrication methods.
3D Printing Advantages
The typical benefits of 3D printing in the aerospace industry are:
- Additive manufacturing allows for the consolidation of sub-assemblies into single components that are otherwise impossible to manufacture. Reduction of part count also reduces the risk of FOD, or foreign object debris.
- Additive technologies enable the creation of complexity in designs that is not otherwise feasible, with less advanced methods. 3D printing does not need to conform to line-of-sight features like machining requires.
- The nature of 3D printing enables rapid-iteration design changes without requiring any manufacturing equipment changes other than models in the 3D slicer.
- These processes equip designers and manufacturers with rapid, on-demand production anywhere in the world where there is equipment, reducing time-to-market and supply chain costs and reducing in-field infrastructure complexity.
- By strategic and cautious application of additive production processes, the supply chain is made leaner, more reliable, and more consistent.
3D Printing Disadvantages in Aerospace
The disadvantages of 3D printing in the aerospace industry include:
- Depending on the technology used and the level of precision required of the part in its function, some of these parts require additional post-processing. This phase involves additional tasks ranging from precision machining, through polishing, and coating to refine the 3D-printed components for specific needs. Post-processing typically requires delicate and skilled manual labor and therefore increases production time and costs. This can be in scale with the printed part cost, detracting from the undoubted benefits of streamlined manufacturing.
- The remarkable array of components that can be derived from 3D printing is constrained by the lack of precise selectable material grades, in many instances. Aviation-specific regulations necessitate specialized and tightly specified materials. Consequently, the aerospace engineering sector is limited by the number of material options, restricting the technology's ability to create a wider range of aircraft elements during this innovation/transition phase.
- While increasing productivity efficiency, 3D printing-driven production can greatly reduce cost efficiency. Where component costs outweigh schedule costs, it cannot serve. However, as a method for extremely fast creation of complex parts that are not cost sensitive, it has a place that is becoming more significant.
Application Examples
There has been exploration of various applications of 3D-printed structural components in the aerospace industry, with as yet limited in-flight uptake. Wing brackets, actuator components for aircraft, drone rotor blades, fuel nozzles, combustion chambers, and even parts of the engine's internal structure are a few examples of trailed and well received components. These uses highlight the remarkable adaptability and potential of this manufacturing method in its potential to impact the sector. It is clear that 3D printing is on the verge of reshaping the sector's manufacturing processes with its endless possibilities.
Materials
Some of the materials used in the 3D printing of aerospace structural components include:
1. Titanium Alloys
Titanium is a high performance material that is ideally suited to the aerospace sector, where its high cost is not prohibitive and its strength-to-weight ratio and exceptional corrosion performance are overwhelmingly beneficial. In addition, the manufacturing processes used for production of titanium parts are restricted and the difficulties of production are considerable. Additive manufacture short-circuits most of these manufacturing issues and delivers high performance parts that offer massively lower supply chain resistance and logistical difficulties.
2. Aluminum Alloys
Aluminum is by no means a poor second choice to titanium, as it delivers almost the same strength-to-weight ratio and a considerably lower raw material and (traditional) processing cost. A considerably easier supply chain for additive manufacturing materials means there are more options to select from, and build energies are lower, allowing its use of lower power equipment or in faster build operations. Aluminum generally offers good corrosion properties for aerospace applications and this can be considerably enhanced by anodizing, forming a controlled and precise oxide film on parts that excludes oxygen, even when wet.
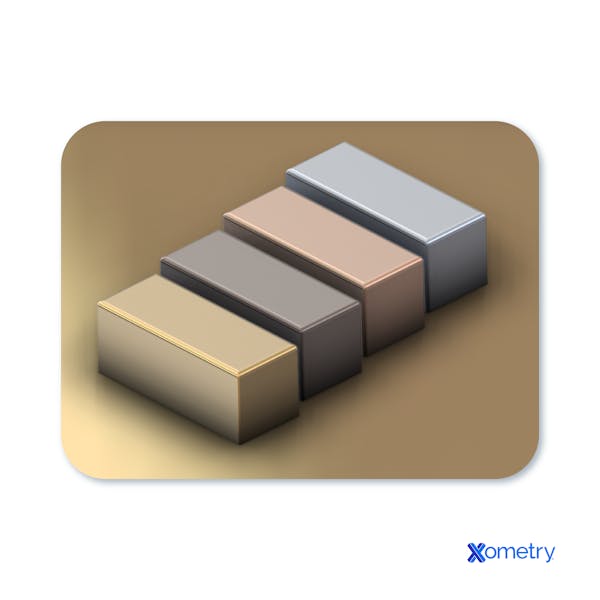
3. Nickel Alloys
Nickel alloys offer extreme performance at high temperatures, as well as excellent corrosion resistance. 3D-printed nickel alloy parts have attracted a lot of interest in the aerospace sector, especially for experimental use in turbine blades, real in-flight application in combustion chambers and exhaust parts for gas turbines, as well as rocket engine components in hot use. Nickel super alloys play a crucial role in enhancing the overall efficiency and reliability of critical systems.
4. Stainless Steel
Stainless steels of several grades are widely used in additive manufacturing across various non-aerospace sectors, bringing strength and exceptional corrosion resistance to tooling, industrial equipment, and more. 3D printed parts from stainless steel can offer robust, long-lasting structural and functional components for high-stress applications in aerospace. Parts that underpin the successful operation of air and spacecraft in landing gear, including the struts and support structures, are made from this alloy family and must meet the astonishing pounding demands of landing. The distinctive combination of resistance to corrosion, strength, and durability sets stainless steel apart and makes it an ideal choice for strength critical (rather than weight critical) components in the sector. Despite stainless steel's greater strength, aluminum exhibits a significantly superior strength-to-weight ratio, but a lower resilience under cyclic loading.
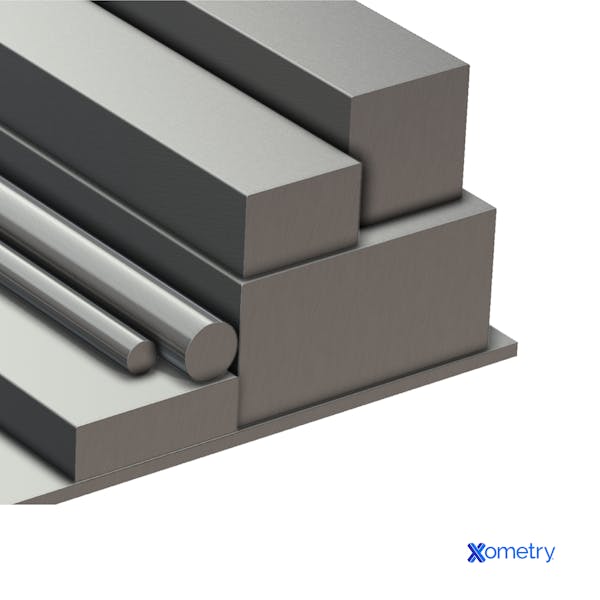
5. Carbon Fiber Reinforced Polymers (CFRPs)
Carbon fiber reinforced polymers (CFRPs) are rapidly being adopted as good material options in many applications that need low weight and high strength. CFRP combines the low weight of polymers with the strength of metals. They play an increasingly pivotal role in the aerospace industry, by improving fuel efficiency, reducing emissions, and enhancing the overall performance/lift capacity of aircraft and spacecraft and improving shock resilience. CFRPs can reduce an aircraft's weight by up to 20%. The 3D printing of sandwich structures with various core shapes, using continuous carbon fibers, can be applied to a range of structural elements in aerospace, in common with other high value sectors. Modern aircraft commonly use carbon fiber reinforced polymer (CFRP) sandwich structures for their elevators, rudders, and steering blades as flight control surfaces.
6. High-Performance Polymers
High-performance polymers, such as PEI (ULTEM), PEEK, PEKK and PPSU, exhibit mechanical remarkable properties, and high-temperature resistance compared to many standard polymers commonly used in engineering applications. Polymers such as nylon, ABS (acrylonitrile butadiene styrene), or polyethylene are considerably more fragile under load and heat. Combining discontinuous carbon fibers with the high-performance polymer PEKK delivers a composite material with greatly improved properties.
7. Ceramic Composites
Ceramic composites are increasingly available for additive manufacture processes, but they are slow in adoption because of a restricted knowledge base, outside specialist fields. Their advantages are considerable—great toughness, hardness and exceptional resistance to elevated temperatures, making them ideal for extremely demanding aerospace applications. Ceramic parts printed using additive manufacture hold great potential for the aerospace sector, offering light weight, high strength and great environmental resilience, but necessarily restrictive safety certifications are time-consuming and as-yet not achieved. Although techniques like IJP and 3DP produce porous materials, there are few appropriate surface treatments and sealants. To learn more, see our guide on What is Ceramic.
8. Invar®
Invar is an unusual nickel-iron alloy renowned for its extremely low coefficient of thermal expansion. This makes it ideal for applications requiring dimensional stability under highly variable temperature conditions, which property carries over into additive manufacture. This unique property makes it invaluable in various industries, including aerospace engineering. The innovative use of Invar in 3D printing is a pioneering approach that's still in the experimental stages, with the promise of offering enhanced capabilities in terms of dimensional control and stability.
9. Tantalum
In the aerospace sector, tantalum is used in critical parts that are subject to both high-temperature and high-stress operations. Tantalum's hot-corrosion resistance is particularly advantageous in aerospace applications, where exposure to exhaust gasses, hot-moisture and rapidly varying temperatures, is common in gas turbines. Tantalum, along with other refractory metals, is extraordinarily difficult to process by traditional means, but additive manufacture obviates these challenges. Specific applications include: turbine blades, nozzle segments for satellite propulsion, and components for hypersonic flight.
10. Cobalt-Chrome Alloys
Cobalt-chrome alloys are used for their good combination of properties—high strength, wear resistance, and biocompatibility. They are found increasingly in aerospace applications, particularly in gas turbine engine components, because of their ability to withstand high temperatures and rapidly varying mechanical stresses. Cobalt-chrome alloys serve in aerospace contexts for engine components, aircraft structural parts, rocket engine components, and heat shields. For more information, see our guide on Superalloys.
Regulatory Requirements for Aerospace 3D Prints
Yes. Prior to service in aircraft, 3D-printed aerospace structural components need to be FAA or EASA approved, after rigorous testing. The sector necessarily places a high priority on reliability and safety for the preservation of life (and equipment), so these components must go through stringent testing and validation procedures. Regulatory bodies such as the Federal Aviation Administration (FAA) and the European Union Aviation Safety Agency (EASA) have tight controls in place. These standards guarantee the safe and reliable operation of aircraft.
The Future
The use of additive manufacture in the aerospace industry is on a growth path. Aerospace manufacturers are gradually switching some load-bearing and hot area components from traditional casting to 3D printing, despite the current price implications in this fledgling, high cost supply. Growth in penetration and demand for additive manufacturing technology continues to develop in the sector. The use of 3D printing in aerospace is anticipated to increase over the next period as a result of developments in printing technology that are improving performance and dropping prices. For more information, see our guide on How Does a 3D Printer Work.
Comparing 3D Printing to Traditional Manufacturing
The process and materials used in 3D printing structural components for aerospace are worlds apart from those used in traditional manufacturing. 3D printing uses additive techniques to build parts layer by layer from a digital model as opposed to subtractive processes like machining or one-piece processes like casting. Complex geometries, greatly reduced waste, and agile development/testing cycles in design are made possible by this. Numerous materials have the potential to be 3D printed as an alternative to undergoing machining, molding, or casting procedures.
Xometry’s Solutions
Xometry is an AS9100 company that builds components used in flight and spaceflight. It can help you move from prototyping and research to flight-worthy manufacturing using direct metal laser sintering services (aluminum and stainless steel alloys), fused deposition modeling (ULTEM 1010), selective laser sintering (CF and FR materials), and traditional processes like CNC machining services (aluminum, titanium, PEEK, and more).
Check out Xometry’s Guide to Quoting Flight Parts to understand the best practices to communicate your project’s requirements.
Disclaimer
The content appearing on this webpage is for informational purposes only. Xometry makes no representation or warranty of any kind, be it expressed or implied, as to the accuracy, completeness, or validity of the information. Any performance parameters, geometric tolerances, specific design features, quality and types of materials, or processes should not be inferred to represent what will be delivered by third-party suppliers or manufacturers through Xometry’s network. Buyers seeking quotes for parts are responsible for defining the specific requirements for those parts. Please refer to our terms and conditions for more information.
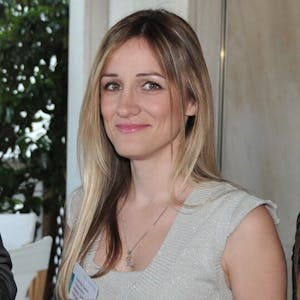