Both acrylonitrile butadiene styrene (ABS) and polyethylene terephthalate glycol-modified (PETG) are thermoplastics used in 3D printing, often with high-temperature printers. They can both handle their fair share of stress and strain, can be recycled, and are both susceptible to moisture—although at differing degrees; one is far less hygroscopic than the other. Also, one deteriorates much quicker if left out, and one is a third of the price cheaper than the other. We won’t leave you in suspense any longer; read on to find out which is which.
What is ABS?
As a styrene-acrylonitrile copolymer, ABS’s properties have been changed by the presence of butadiene rubber. It’s durable, thanks to the styrene, and its heat-, chemical-, and impact resistance can be credited to the butadiene. This also helps it keep its shape and toughness during processing. This multipurpose thermoplastic, which today is used a lot in additive manufacturing, dates back to the mid-1940s when it was used to make bullet-proof plastic sheets. It was later patented in 1948 and made commercially available by the Borg-Warner Corporation in 1954. The following image shows a part we made with ABS here at Xometry:
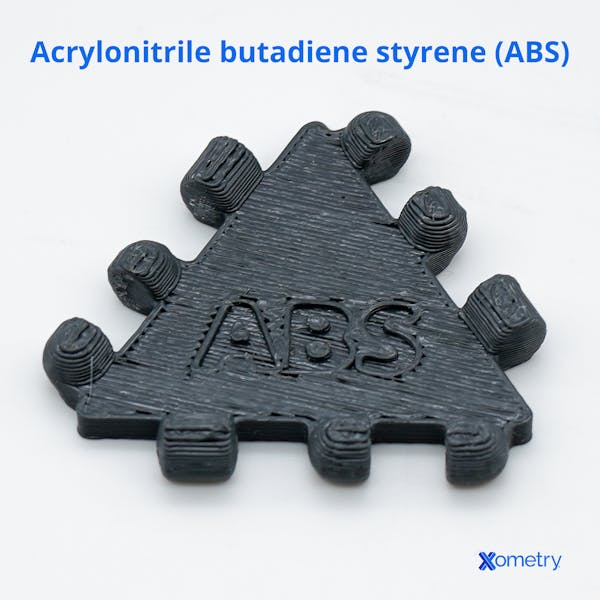
ABS responds quite well to post-processing; it can be painted, machined, and reworked, and is less susceptible to moisture in the air. It also works out to be rather cost-effective because it’s easily available and isn’t too pricey to produce. But, ABS does have certain drawbacks, too; it reacts negatively to UV radiation, is not very adhesive, and isn’t really resistant to chemicals.
What is PETG?
PETG is a pretty tough copolyester thermoplastic that was first made by modifying the glycol molecule found in polyethylene terephthalate (PET); PET is tough enough on its own, but once the glycol is modified, it becomes less brittle. It’s impact-, heat-, and humidity-resistant, and, with enough heat, can be molded into different shapes. Also, it’s not toxic, so it can be used to make things like transparent water bottles and products for the food industry. The image below shows a gear made from this material:
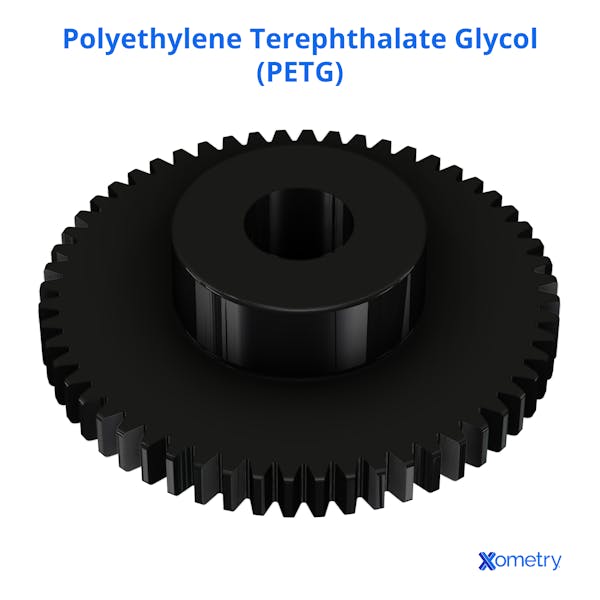
PETG fares quite well in alkaline and acidic environments and doesn’t warp as easily as ABS can. It’s also known as the best filament for making transparent items, and if you’ll be exposing it to UV light, that’s fine, too. The potential downsides of using PETG, though, are that it tends to be pricier than alternatives, like ABS, and can degrade over time if not stored properly because it can absorb quite a bit of moisture from the air. It’s also tricky to paint and might require a release agent like hairspray or glue from a glue stick to be coated onto the build plate to stop the material from sticking to it.
Side-by-Side Comparisons
The below table provides a quick and easy way to compare these two materials.
Attribute | ABS | PETG |
---|---|---|
Attribute Strength | ABS High | PETG High |
Attribute Durability | ABS Moderate to high, can be brittle under impact | PETG High |
Attribute Hygroscopic properties | ABS Absorbs moisture, needs drying before printing | PETG Absorbs moisture, but less than ABS |
Attribute Prone to degradation | ABS Yes, especially under UV exposure and high heat | PETG Less prone, but can degrade under prolonged UV exposure |
Attribute Good layer adhesion | ABS No, layers can delaminate if not printed correctly | PETG Yes, excellent layer adhesion and less warping |
Attribute Speed | ABS Between 30 and 70 mm/s | PETG Around 60–100 mm/s |
Attribute Heat resistance | ABS Will not melt or stick to itself under 100°C and could warp or twist out of shape | PETG Can melt around 50°C to 80°C |
Attribute Chemical resistance | ABS Poor, can be damaged by acetone, some oils, and solvents | PETG Good, resistant to many chemicals, including acids and alkalis |
Attribute Biodegradability | ABS Not really, takes a long time to decompose | PETG Not really, slightly more than ABS |
Attribute Recyclability | ABS Yes, at specialized facilities | PETG Yes, more easily than ABS |
Attribute Cost (varies between brands) | ABS Around $20 per kg | PETG About $30 per kg |
Attribute Coloring | ABS Filament can be dyed, and final part can be painted in any color | PETG Difficult to dye or paint because adhesives don’t bond well with it |
Attribute Applications | ABS Helmets, keyboard keys, pipes, fittings, vacuum cleaners, toy bricks, wall socket faceplates | PETG Kitchen utensils, dishes, drink containers, water bottles, food industry applications |
Attribute Post-processing | ABS Responds well to acetone smoothing | PETG Less responsive to acetone smoothing, can be sanded or polished |
Attribute Warping | ABS Prone, especially on large prints or without a heated bed | PETG Not likely, much less prone than ABS |
ABS vs. PETG Attributes
Frequently Asked Questions on ABS and PETG
Do these materials release any odors during printing?
Yes, but PETG releases fewer particles which, in turn, creates a much milder odor. ABS, though, will need a properly ventilated area because the odor can get quite strong.
How accurate can parts be?
Printed PETG parts can actually be more accurate than ABS parts, and that’s mainly due to the fact that ABS part dimensions can change slightly as they cool down. Also, the material is more prone to warping, shrinking, and environmental sensitivity—all factors that can change its final look. If you want your 3D printed part to have a certain size and shape, with strictly no deviations, ABS might not be the best choice. You could try PETG, PLA (polylactic acid), or Nylon instead.
Are there any mutual alternatives to both ABS and PETG?
Yes, there are two: nylon and polycarbonate. They’re both used in additive manufacturing, especially FDM (fused deposition modeling), and have quite good impact resistance, similar to the two materials we discussed in this article.
What else can we compare ABS to?
Aside from PETG, ABS can be compared to other materials like PLA and ASA (acrylonitrile styrene-acrylate). The former is not very resistant to heat, so it’s not a good idea to use it for anything more than a hobbyist project. ABS, although less stiff than PLA, is actually up to four times more impact-resistant. It’s also more durable and 25% lighter. When it comes to ASA—a material that matches ABS in terms of strength—it works out more expensive than ABS, and that’s largely because its properties are better, like toughness, impact resistance, reaction to UV radiation, and ease of use.
What else can we compare PETG to?
PETG is a good comparison to materials like PET mentioned earlier and TPU, which is an abbreviation for thermoplastic polyurethane. PET has a higher working temperature than PETG and can stay rigid. Where it can’t compare with PETG, however, is in shock resistance, high heat, impact resistance, and flexibility. TPU is more flexible than PETG, but not as tough. It can also stick better to cooler printing beds (40–60°C).
How Xometry Can Help
For any other information on filaments or processes for 3D printing, reach out to one of our representatives, as additive manufacturing is our forte here at Xometry. You can also get started on your next project in a matter of minutes by uploading your designs to our Instant quoting page to receive your free, no-obligation quote.
Disclaimer
The content appearing on this webpage is for informational purposes only. Xometry makes no representation or warranty of any kind, be it expressed or implied, as to the accuracy, completeness, or validity of the information. Any performance parameters, geometric tolerances, specific design features, quality and types of materials, or processes should not be inferred to represent what will be delivered by third-party suppliers or manufacturers through Xometry’s network. Buyers seeking quotes for parts are responsible for defining the specific requirements for those parts. Please refer to our terms and conditions for more information.
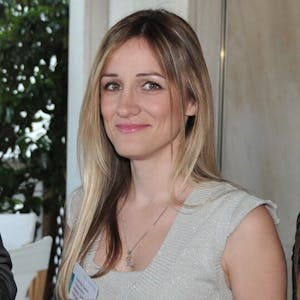