Anyone interested in the benefits and fantastic results of additive manufacturing has a long list of methods to choose from. One that’s worth noting in the mix is binder jetting, which mixes the worlds of liquids and powders to make printed products for the art, aerospace, medical, and industrial sectors (and then some).
For those not quite familiar with binder jetting, we’ll go into more detail about what the process entails, its downsides and upsides, and what applications it’s usually best for.
What Is Binder Jetting?
Binder jetting (or BJ) is one of the many 3D printing technologies out there, but more specifically it functions by using an industrial printhead to combine and bond a liquid agent and powder. It can print sand, metal, composite, and ceramic parts in this way and is perfectly capable of creating high-quality builds. Two examples of systems, machines, and software that exist out there are ProJet MJP 5600 from 3D Systems and J5 MediJet from Stratasys.
How It Works
Let’s go a little more in-depth with how binder jetting works. The steps for printing a part with binder jetting are:
- First, you’ll create a CAD file of your design. This will then get sliced and send instructions to the binder jetting printer in the correct sequence.
- Then, a roller will coat the build platform in an even, thin layer of powder.
- Next, the printhead moves around, applying the liquid binder adhesive onto specific areas of the powder based on the sliced file of the object.
- The build platform is then lowered by the thickness of one layer.
- Another layer of powder is spread around by the roller and the same steps happen again, with the binding agent being dropped down onto specific parts of the powder. This happens layer by layer until you have your finished product.
- Once it’s finished, any powder that wasn’t used will be left over and cleaned off the build platform.
Applications
There are so many uses for this kind of 3D printing, and this condensed list only covers a small portion of them:
- Prototypes
- Aerospace components
- Casting patterns
- Jewelry
- Full-color decorative objects
- Cores and molds
- Tooling
Types of Binder Jetting
The type of binder jetting machine you’ll use depends on what binding agent and powder are used. Some common types of binders used in binder jetting include:
Polymer Binders
Polymer binders are usually paired up with ceramic powders and can be taken off with heat treatment. They have a lower viscosity and apply pretty easily through BJ printing.
Water-based Binders
You’ll find these binders working in tandem with sand or other mineral powders. They’re more environmentally friendly and can be easily removed through drying or sintering.
Solvent-based Binders
Solvent-based binders work best with metal and ceramic powders, and they can be removed through a process aptly named solvent debinding. They have a high solid content and are a breeze to apply to the bed.
Furan Binder
Furan binders are created with furfuryl alcohol and often get used with sand powders to make molds and cores for casting, especially more complex designs. They have good mechanical strength and thermal stability and can be cured by heat or acid catalysts. You can strip the molds pretty easily from the casting.
Silicate Binder
Made from sodium silicate or potassium silicate, these binders are another option when it comes to casting and work well with sand powders (and are great for ferrous metals once the mold has been made). They have good refractory properties and have no problem with high temperatures. They get cured through drying or by adding an acid catalyst.
Phenolic Binder
Another option for casting purposes is phenolic binders (made from phenol-formaldehyde resins). They have good mechanical strength and dimensional stability and can be cured by heat. They’re fantastic if you need high-strength, high-temperature products.
UV Binder
You’ll need access to a UV light for this type of binder and they don’t work with many materials (photopolymer resins are best), but they do produce high-resolution and complex parts.
Materials for Binder Jetting
There are many materials you can use for binder jetting. Here’s a rundown of the main types:
- Metals: Stainless steel, titanium, aluminum, and copper, which create parts with high strength and durability.
- Ceramics: Tiles, sanitary ware, and insulators, using materials like alumina, zirconia, and silicon carbide.
- Sand: Mixed with a binder (like furan, silicate, or phenolic) to make molds and cores for foundry casting.
- Plastics: Powders like polyamide, polypropylene, and polycarbonate to make consumer goods or parts for the automotive and medical industries.
- Composites: Carbon fiber and glass fiber mixed with a polymer binder.
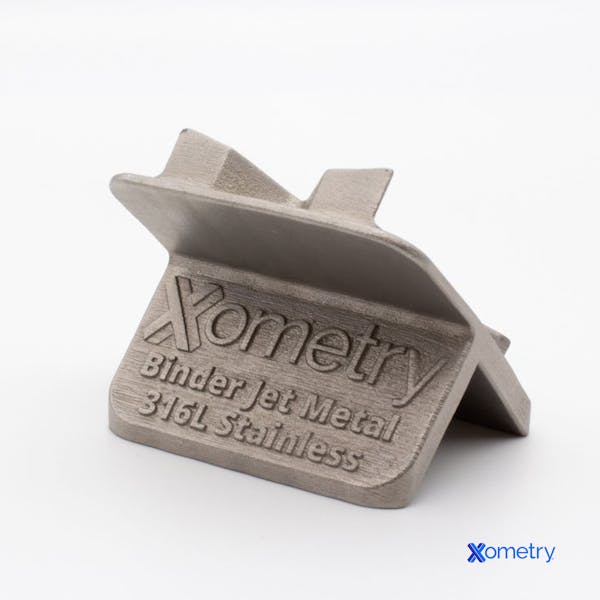
Advantages and Disadvantages
Here are some of the perks of using binder jetting printing over other methods:
- Capable of creating builds with precise dimensions
- Works at room temperature (which helps cut down on warping and residual stresses
- You can create both large and small builds with BJ
- It’s a lot faster when you compare it to other 3D printing techniques
- It’s more affordable and energy-efficient than laser models
- Materials like ceramic and metal powders tend to be cheaper
- The unbound powder serves as a natural support and gives more flexibility and less waste
- Any unused powder can be repurposed for future print jobs
Although it has a decent list of advantages, there are also some downsides to be aware of with binder jetting:
- Metal builds made with binder jetting can have higher porosity and lower mechanical properties
- It’s not always an option for structural parts
- In their “green” state, parts can be brittle
- Post-processing is almost always required, which lengthens the timeline
- Binder jetting is usually more low-resolution than other 3D printing methods
Binder Jetting vs. Material Jetting
Often manufacturers will compare the difference between binder jetting and material jetting. While they have a few similarities, there are some differences to note too, which we’ve put together in the table below.
Property | Binder Jetting | Material Jetting |
---|---|---|
Property Printing process | Binder Jetting Deposits a binding agent onto a bed with a thin layer of powder | Material Jetting Deposits photopolymer droplets that are solidified through a UV light |
Property Advantages | Binder Jetting No need for support structures, offers multiple colors, can use multiple materials | Material Jetting Surface appearance is clean and quality, can print with multiple colors, has dimensional stability |
Property Disadvantages | Binder Jetting Post-processing is necessary and parts can be brittle | Material Jetting Parts can be brittle and mechanical properties aren’t as great |
Property Materials | Binder Jetting Ceramics, some polymers, metals, sand, and composites | Material Jetting Photopolymers |
Property Applications | Binder Jetting Prototypes, aerospace components, casting patterns, jewelry, cores and molds, tooling | Material Jetting Prototypes, anatomical models, designs |
Property Manufacturers | Binder Jetting 3D systems, ExOne, VoxelJet, Digital Metal | Material Jetting Stratasys, 3D systems, Mimaki, XJet |
Binder Jetting vs. Material Jetting
FAQs on Binder Jetting
How Much Does Binder Jetting Cost?
Typically, binder jetting machines cost upwards of $100,000. For business owners and manufacturers this is often pretty economical since these printers don’t use as much power and use cheaper materials.
Is Binder Jetting a Fast 3D Printing Process?
Yes, in fact, binder jetting is often considered the fastest 3D printing technology. It can produce high volumes in a shorter period of time without losing out on precision.
Does Binder Jetting 3D Printing Require Support?
No, binder jetting typically doesn’t need any kind of additional support structures because the powder that’s rolled onto the print bed offers this already. This means that several parts can be printed at the same time on the same powder bed, which is ideal for low-to-medium batch production.
Does Binder Jetting Only Work With Metals?
No, binder jetting works with far more materials than just metals. You can also print with sand, ceramics, and some polymers.
How Xometry Can Help
We have numerous 3D printing services you can get quotes for at Xometry outside of just binder jetting, including plastic 3D printing, FDM printing, PolyJet printing, and stereolithography (SLA).
Disclaimer
The content appearing on this webpage is for informational purposes only. Xometry makes no representation or warranty of any kind, be it expressed or implied, as to the accuracy, completeness, or validity of the information. Any performance parameters, geometric tolerances, specific design features, quality and types of materials, or processes should not be inferred to represent what will be delivered by third-party suppliers or manufacturers through Xometry’s network. Buyers seeking quotes for parts are responsible for defining the specific requirements for those parts. Please refer to our terms and conditions for more information.
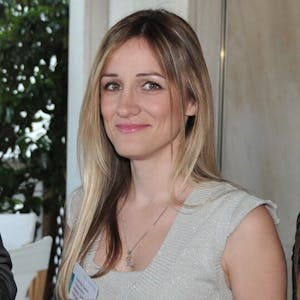