Digital Light Processing (DLP) and Selective Laser Sintering (SLS) are two popular 3D printing technologies. Each of these processes yields high-quality, precise results and has different advantages depending on the project specifications, materials, and overall application. DLP utilizes a projected light source to create a part. It contains a digital interface that beams an image of the specific cross-section across the platform so that all points of the resin layer are cured. SLS, on the other hand, utilizes a laser in conjunction with a powder bed. The laser sinters a surface layer into the powder repeatedly until the product is constructed and all erroneous powder is removed.
The main differences between SLS and DLP are: cost, printing speed, precision quality, and technical characteristics. DLP uses support layers as a schematic and often yields a more precise product. SLS can produce several parts in the same build process. This makes SLS generally cheaper, faster, and more durable for multiple-part builds. This article will further discuss the differences between SLS vs. DLP, their advantages, and disadvantages, as well as the alternatives to both.
DLP Definition and Comparison to SLS
DLP is a resin 3D printing process known for its accuracy and resolution. It uses a resin base and a support structure system to craft a product. DLP was developed in the 1980s by Larry Hornbeck of Texas Instruments. DLP utilizes a build structure that stretches down into a resin tank. This allows the parts to be created layer by layer, starting upside down. DLP technology also contains a digital interface. This interface beams an image of the specific cross-section across the platform so that all points of the resin layer are cured. DLP is also the most versatile due to the availability of different resins. SLS, on the other hand, is known to require more material and can be messier.
For more information, see our guide on Digital Light Processing.
What Are the Advantages of DLP Compared to SLS?
DLP has the following advantages compared to SLS:
- DLP produces more precise and accurate printed parts compared to SLS. The support structure allows for fine detailing and intricate process specifications with very accurate results.
- DLP-printed parts have a better surface finish compared to SLS.
- DLP has a higher part sizing range than SLS. DLP units have the ability to create larger individual parts with finer detailing than SLS machinery.
- DLP produces parts with higher resolution compared to SLS parts.
What Are the Disadvantages of DLP Compared to SLS?
DLP has the following disadvantages compared to SLS:
- DLP requires a support structure. It creates a “skeleton” of the final product, which layers are then constructed around. This increases the time required for completion and doesn’t allow for many parts to be made in a single build as SLS does.
- DLP-printed parts are less durable and have lower tensile strength than SLS.
- DLP has lower scalability than SLS. DLP requires individual production part by part in one build. This means the process is less easily scaled.
- DLP has slower build times due to the support structure.
SLS Definition and Comparison to DLP
SLS is an additive manufacturing process that works by sintering polymer powder with a high-power laser to construct a product layer by layer. In SLS, a base is filled with polyamide or nylon powder. This base contains a build platform and a knife structure which applies a coating of powder to the build platform. The laser fuses the powder, the knife applies another powder layer to the build structure, and another layer is “sintered” or printed. SLS uses a slicer technology that divides the product specifications into very thin sections. This guides the laser according to the desired part geometry. SLS was first created in the 1980s by Dr. Joe Beaman and Dr. Carl Deckard. SLS has been fine-tuned over the years to become more precise. It is the popular choice for batch production and rapid prototyping because of its efficiency and consistently strong parts. It is preferred over DLP for a single build with multiple parts and has an easier post-production process.
To learn more, see our article on Selective Laser Sintering (SLS).
What are the Advantages of SLS Compared to DLP?
There are several advantages of SLS over DLP:
- SLS parts require no support structures, unlike DLP-printed parts. SLS uses a laser to fuse powder layers to construct a product.
- SLS can print multiple parts in a single build faster than DLP.
- SLS uses different polyamide powders that create stronger end-use products compared to DLP.
- SLS has high scalability and can create several products in a single build.
- SLS is more cost-effective for batch production.
- SLS has better layer adhesion and increased tensile strength due to the powder fusion process compared to DLP. DLP’s layer adhesion can also be weakened by the removal of the support structure.
What are the Disadvantages of SLS Compared to DLP?
The disadvantages of SLS compared to DLP are as follows:
- SLS does not offer the same level of precision and fine detailing that DLP does because it does not operate using a support structure. Bead blasting during post-processing is harmful to smaller detailing and lettering, thin walls, corners, and holes.
- SLS has fewer compatible materials compared to DLP.
- SLS is more expensive for individual parts in a single build than DLP.
- SLS has a higher processing time for individual parts in a single build.
Comparison Table Between DLP and SLS
The table below shows the comparison of DLP vs. SLS:
Attribute | DLP | SLS |
---|---|---|
Attribute High-resolution | DLP Yes | SLS No |
Attribute Low range of tolerance | DLP Yes | SLS No |
Attribute Multiple parts in a single build | DLP No | SLS Yes |
Attribute Requires support structure | DLP Yes | SLS No |
Attribute Allows post-production customization | DLP No | SLS Yes |
Attribute Has a high level of fine detailing | DLP Yes | SLS No |
Table. DLP vs. SLS Comparison
SLS is the best choice for durable parts and for parts that don't need details or a support structure. On the other hand, DLP is better if the customization requires fine detailing with precise surface finishes and lower-range tolerances.
DLP vs. SLS: Technology Comparison
DLP and SLS have different technologies. DLP uses a resin base and a support structure system to craft a product layer by layer. It can effectively create very precise designs with low-range tolerances and high resolution. SLS, on the other hand, uses a high-powered laser to sinter polymer powders. SLS creates durable parts for batch production in a single build.
DLP vs. SLS: Material Comparison
DLP uses resins that are available in different varieties depending on application needs. The most common DLP materials are polypropylene (PP) and ABS plastic. PP allows for an increased focus on intricate designs, precision, and accurate detailing. ABS plastic, on the other hand, is cost-effective and provides great heat and chemical resistance.
SLS uses different powders in its printing technology. The most popular choices are PA (polyamide) and plastics (nylon). These materials are economical and easy to work with. Nylon, in particular, has many variations that allow for focusing on different product priorities.
DLP vs. SLS: Product Applications Comparison
SLS is best used for product applications that need high durability but do not require a high level of detail. Additionally, if the product application calls for unique material parameters, SLS will offer a variety of options. DLP-printed parts can boast intricate geometries and build quality with higher precision. DLP is applicable for products that require a very low range of tolerance. It is also the most economical and efficient option for individual parts.
DLP vs. SLS: Print Volume Comparison
SLS does not require a support structure. As a result, this printing technology has the capability to produce many parts in a single build. If the desired application requires high-volume batch production, then SLS would be the best choice. On the other hand, DLP is better suited for fine detailing individual parts in a single build.
DLP vs. SLS: Surface Finish Comparison
SLS provides a lower-quality surface finish than DLP: generally at 100–250 RMS. This is reasonable for less-precise product requirements. Bead blasting during post-processing makes fine lettering and detailing difficult to maintain. DLP, on the other hand, has the capacity for high-resolution products and ideal surface finishes. In most cases, micro resolutions are available in the range of 0.004 to 0.001 inches. Because of this, products with intricate details and very few imperfections can be effectively created using DLP.
DLP vs. SLS: Cost Comparison
SLS printers are more expensive than DLP printers. An entry-level DLP printer can be bought for as low as $500. While an SLS printer can cost anywhere from $10,000 to $100,000. SLS is better suited for multiple parts in one print. In contrast, DLP is more cost-effective for singular parts. A single part with multiple components must be completed in multiple builds, which is less efficient in terms of cost and time.
What Are the Mutual Alternatives to DLP and SLS?
A mutual alternative to SLS and DLP is:
- FDM: FDM (fused deposition modeling) operates similarly to both SLS and DLP but uses filament spools instead of a powder or resin base. This technology requires the use of 3D computer graphics software to design the product and determine specifications. It is an economical option but has looser tolerances and fewer design options.
What are the Similarities Between DLP and SLS?
DLP and SLS processes are similar in many ways:
- Both additive manufacturing processes utilize the heat from light to form a solid from a base, whether resin or powder. This heat source differs also: DLP uses a UV projector while SLS uses the heat of a UV laser.
- Both methods break down the part's geometry into cross-sections and construct the final product layer by layer. Software is utilized to guide the laser according to the input design.
What are the Other Comparisons for DLP Besides SLS?
Aside from SLS, another alternative to DLP is:
- DLP vs. SLA: SLA (Stereolithography) also uses a laser beam to cure a resin. However, the heat used in DLP comes from a UV light projector while the SLA heat source is a UV laser beam. The laser is then reflected on a set of mirror galvanometers which cures the resin layer. They are very similar in terms of accuracy, tolerance, and resolution. The differences mostly lie in the specific process parameters and printer design. For more information, see our article on SLA vs. DLP.
What are the Other Comparisons for SLS Besides DLP?
Aside from DLP, another alternative to SLS is:
- SLS vs. SLM: SLM (selective laser melting) is very similar to SLS. The main difference lies in the heating process of the powder base. Sintering fuses the powder together using heat. Melting on the other hand goes one step further and literally melts the powder into a singular component. This means that SLM will create a more durable part because there are no voids in the product. However, the powder used in SLM must be a monomer because a single melting point is needed for the heating process to work. For more information, see our article on SLS vs. SLM.
Summary
This article provided a contrast between DLP and SLS 3D printing technologies. To learn more about DLP vs. SLS and which application is suited for you, contact a Xometry Representative.
Xometry offers a full range of 3D printing services for your project needs. Visit our Instant Quote Engine to get a free, no-obligation quote in minutes.
Disclaimer
The content appearing on this webpage is for informational purposes only. Xometry makes no representation or warranty of any kind, be it expressed or implied, as to the accuracy, completeness, or validity of the information. Any performance parameters, geometric tolerances, specific design features, quality and types of materials, or processes should not be inferred to represent what will be delivered by third-party suppliers or manufacturers through Xometry’s network. Buyers seeking quotes for parts are responsible for defining the specific requirements for those parts. Please refer to our terms and conditions for more information.
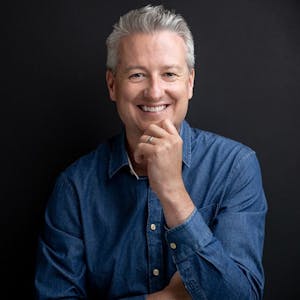