Stereolithography (SLA) and digital light processing (DLP) are two types of 3D printing that build parts by polymerizing a liquid photopolymer resin. SLA employs an ultraviolet laser to trace the shape of each layer. DLP, on the other hand, projects a mask of a whole cross-sectional layer at a time. SLA produces parts with smoother surface resolution whereas DLP can print significantly faster and more cheaply. SLA printing is ideal for applications that need detailed surface resolution.
This article will compare SLA vs. DLP in terms of their differences, materials, and printing technology.
SLA Definition and Comparison to DLP
Stereolithography is a photopolymer-based 3D printing technology. It was first invented by Hideo Kodama in 1980. Six years later, SLS was commercialized and patented by Charles Hull. SLS works by shining a UV laser against a scanning mirror. The mirror directs the laser light in a pattern that traces out the cross-sectional pattern of a single layer of the part. This laser light polymerizes the photosensitive resin wherever it hits a solid surface – either the build platform or the previous layer. After each layer is polymerized, the build platform moves upwards. The part will thus appear to grow out of the liquid.
SLA 3D printers can produce larger parts with more consistently smooth organic surfaces when compared to DLP 3D printers.
For more information, see our article on What is SLA 3D Printing.
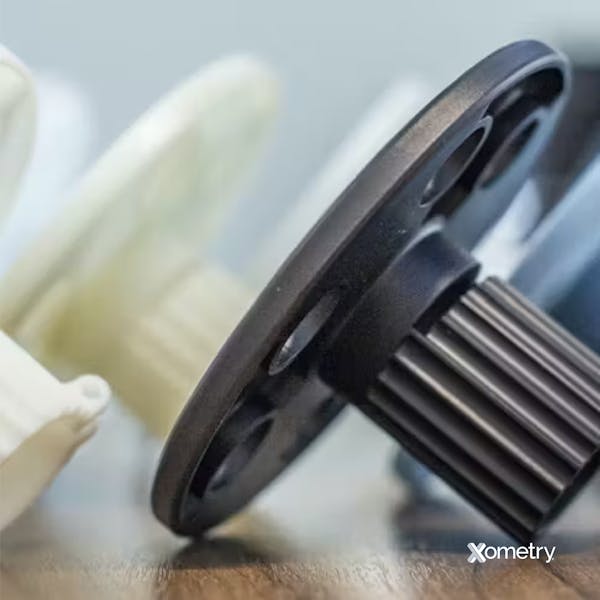
Advantages of SLA Compared to DLP
Listed below are some key advantages of SLA vs. DLP:
- SLA parts have smoother surfaces than those of DLP. This is especially noticeable on curved surfaces.
- SLA printers, in general, can be created with larger build volumes without sacrificing print resolution.
Disadvantages of SLA Compared to DLP
Listed below are some key disadvantages of SLA vs. DLP:
- SLA 3D printing machines are typically more expensive than DLP machines.
- SLA machines are slower than DLP machines. This is because SLA traces a single laser across the entire cross-section of the part whereas DLP is able to polymerize an entire layer at once.
FREE SLA 3D Printing Design Guide
DLP Definition and Comparison to SLA
Digital light processing is a photopolymer-based 3D printing technology. It was invented in 1987 by Texas Instruments. DLP projects a UV light onto the build platform to polymerize each part layer. The layer’s cross-section must be masked so only the specified areas get polymerized. This masking is done with a DMD (Digital Micromirror Device) containing thousands of microscopic swiveling mirrors to direct light. They are arranged into a digital pattern for each layer to direct the UV light to the photopolymer or a heat sink below. Alternatively, LED screens can be used as the light source, and the masking is done by simply turning off the LEDs wherever polymerization is not required. The resolution of a DLP 3D printer depends on the resolution of the LED or DMD array as well as the distance from the light source to the polymerization zone. DLP parts comprise cubic volumes called voxels – essentially 3-dimensional pixels. This means any curved edge will look like it was built from many tiny cubes.
DLP 3D printers are cheaper and can print significantly faster than most SLA 3D printers. The image below shows a typical DLP printer:
To learn more, see our guide on What is DLP.
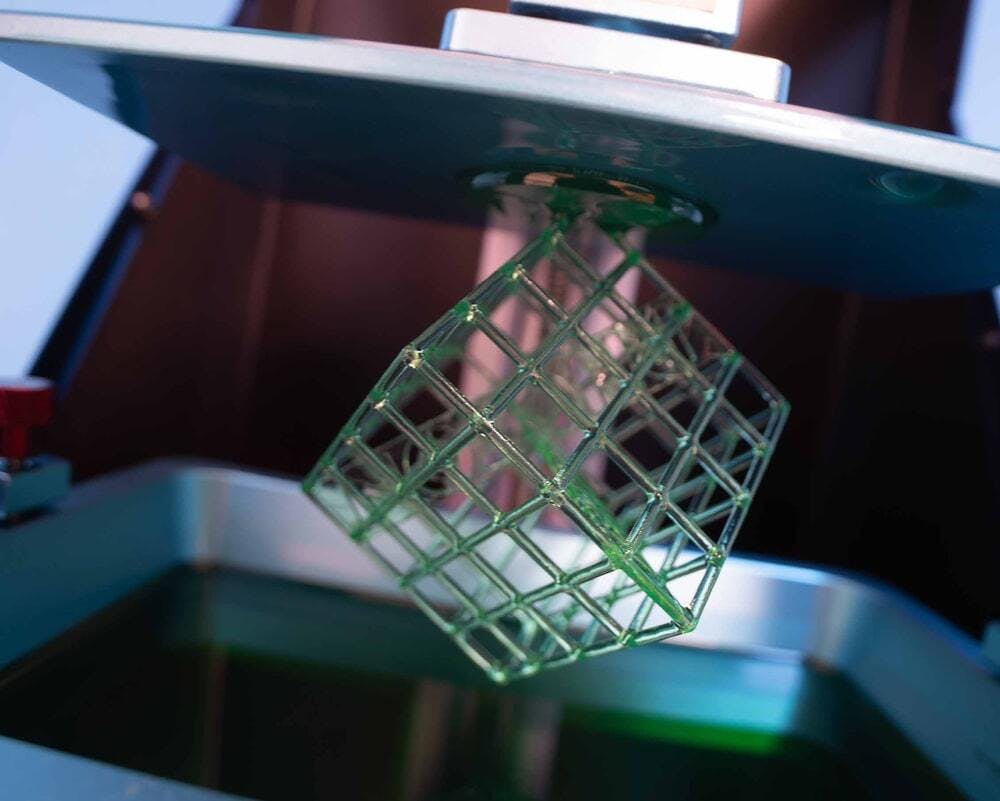
Advantages of DLP Compared to SLA
Listed below are some key advantages of DLP vs. SLA:
- DLP printers can print multiple or large parts faster than SLA. This is due to the fact that the entire print bed can be exposed to the light from the projector. Each layer gets polymerized at once.
- DLP light sources are easier to replace and calibrate. This is in contrast to SLA which often requires the machine to be sent back to the manufacturer for repairs.
Disadvantages of DLP Compared to SLA
Listed below are some key disadvantages of DLP vs. SLA:
- DLP printers have smaller build volumes. A DLP’s print resolution decreases with distance from the light source. A large build volume means more distance, so if it were too big, the resolution would fall to unacceptable levels.
- DLP cannot produce truly smooth curved faces. Any complex or organic shape will be built from many smaller cubic voxels. This gives the part a pixelated look. However, this is only noticeable upon close inspection.
Attribute | SLA | DLP |
---|---|---|
Attribute Print resolution | SLA 25 - 300 microns without voxel pixelation | DLP 25 - 300 microns with voxel pixelation |
Attribute Can print larger parts | SLA Yes | DLP No |
Attribute Wide range of material colors | SLA No | DLP No |
Attribute Minimum feature size | SLA 100 microns | DLP 100 microns |
Attribute Can produce very smooth organic surfaces | SLA Yes | DLP No |
Attribute High-speed printing | SLA No | DLP Yes |
Attribute Has isotropic material properties | SLA Yes | DLP Yes |
Attribute Minimum wall thickness | SLA 0.1 to 0.3 mm | DLP 0.1 to 0.3 mm |
Attribute Parts need support structures | SLA Yes | DLP Yes |
Attribute Largest print volume | SLA 335 x 200 x 300 mm | DLP 192 x 108 x 370 mm |
Table. SLA vs. DLP Comparison
Comparisons on Key Dimensions
Technology comparison: Both SLA and DLP produce parts by polymerizing a liquid photopolymer resin with a UV light source. Both technologies print parts upside down with the build plate slowly moving out of the resin vat and the part thus appearing to grow out of the photopolymer. DLP 3D printers polymerize an entire layer at a time whereas SLA 3D printers scan the cross-section of each layer using a single focused laser. SLA printers can create smoother parts than DLP printers that tend to have a pixelated type effect on complex surfaces.
Material comparison: Both SLA and DLP make use of photopolymers that are cured by a UV light. Variants of these photopolymers are available with either short or long molecular chains. Short chains produce stiffer parts while longer-chain polymers make parts more flexible. Photopolymers need to be cleaned in a solvent bath once they’re finished to remove any uncured resin. A post-curing stage using UV light may also be needed to ensure optimal properties.
Applications comparison: SLA and DLP can both produce highly accurate parts with very fine features. They’re often used to create casting patterns for jewelry pieces or custom dental molds designed to perfectly replicate a patient's dental structure. If parts are to be used in medical or mechanical applications, they generally need to be post-processed to ensure optimal mechanical properties.
Print volume comparison: SLA printers can be built around larger print volumes. This is because the resolution of the print is not affected by the distance from the light source. The narrow laser cures only a single point worth of photopolymer at any given moment. DLP printers, on the other hand, need to have a relatively shallow resin bath as the resolution degrades with distance. The light source needs to be placed close to the layer to be polymerized. Print volume on DLP printers can be increased with the help of higher resolution light sources but this makes the printer significantly more expensive.
Surface finish comparison: SLA and DLP produce some of the smoothest surface finishes of any 3D printing technology. When compared to each other, SLA prints have better surface finishes, especially on complex curved surfaces. An SLA laser will more closely follow a complex curve. DLP printers, meanwhile, will create curves by approximating them with multiple cubic structures. This results in a pixelated appearance on complex surfaces. The effect is only noticeable upon close inspection and in many cases is not visible to the casual observer.
Machine cost comparison: In general, DLP printers are cheaper than SLA printers. A typical SLA printer can cost $3,750 whereas an entry-level DLP printer can cost as little as $500.
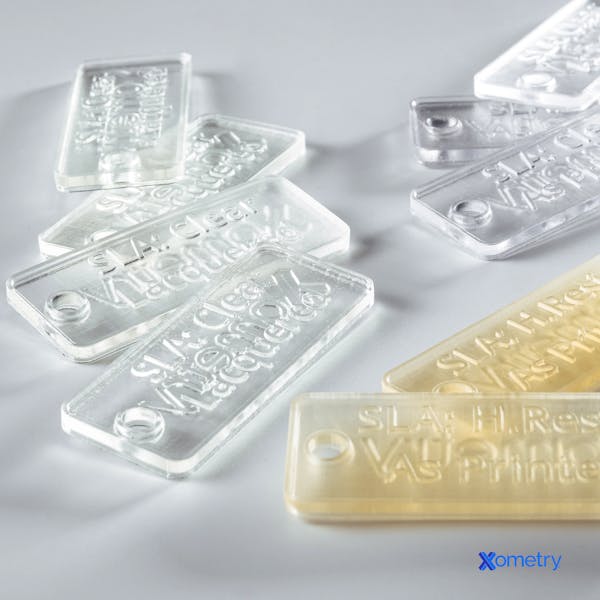
Alternatives to the SLA and DLP
SLA and DLP are excellent 3D printing styles, but there is another alternative technology that can achieve a similar result:
- MJF: Multi-jet fusion is a powder-bed fusion technology. It creates parts by first laying down a thin layer of powder which is heated close to its sintering temperature. Then fusing and detailing agents are placed across the powder in the shape of the part cross-section. Finally, an infrared heat source sinters the treated powder together. This process creates parts with surface finishes that are not as good as SLA or DLP but do come close.
Similarities Between SLA and DLP
Listed below are some of the similarities between SLA and DLP:
- Both SLA and DLP can produce parts with very high levels of accuracy.
- SLA and DLP make parts by curing liquid photopolymer materials.
- Printed parts from both styles need to be post-processed via a solvent bath and post-curing under a UV light.
How Xometry Can Help
Xometry provides a wide range of manufacturing capabilities including CNC machining, 3D printing, injection molding, laser cutting, and sheet metal fabrication. Get your instant quote today.
Disclaimer
The content appearing on this webpage is for informational purposes only. Xometry makes no representation or warranty of any kind, be it expressed or implied, as to the accuracy, completeness, or validity of the information. Any performance parameters, geometric tolerances, specific design features, quality and types of materials, or processes should not be inferred to represent what will be delivered by third-party suppliers or manufacturers through Xometry’s network. Buyers seeking quotes for parts are responsible for defining the specific requirements for those parts. Please refer to our terms and conditions for more information.
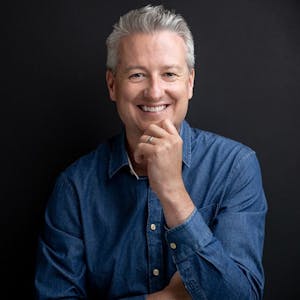