SLA (Stereolithography) was among the first 3D printing technologies to be commercialized. It employs acrylic or other resins that must be cured using an ultraviolet (UV) laser. The technology has been reinterpreted in various ways. Its selection of materials has also grown significantly—you can now find rigid, flexible, heat resistant, chemical resistant, biocompatible, and other resin options. Xometry instantly quotes this process, and has done so since 2018. It's one of our most popular 3D printing processes.
The SLA process takes a 3D model of a component and renders it into solid plastic. The computer model is first digitally “sliced” into layers so the printer can methodically bond each slice to the one before it. SLA machines print prototype parts, test components, medical aids, tools, cosmetic test pieces, and much more.
This article provides a background understanding of SLA technology's advantages, materials, applications, and more.
An Introduction to SLA 3D Printing
SLA is a 3D printing process that uses a scanning UV laser to cure the surface layer of photosensitive resin. The resin is supplied in a bath, and, in the vast majority of SLA machines, the part is built upside-down. With each layer, the build plate will move upward, making it appear as if the part grows out of the liquid polymer. The machine must also print necessary support structures to support overhangs within the design.
The UV-sensitive photopolymers used in the process are collectively referred to as ‘resins.’ They are photo-catalyzed acrylic monomers that become crosslinked when exposed to UV laser light. This principle allows the machine to create details as small as the laser beam’s width.
SLA models are sometimes printed in a partially cured state. These models require post-processing in the form of extra UV exposure to complete the cross-linking process. This additional process step helps eliminate partially solidified resin that didn’t fully cure due to back-scatter and diffraction of the UV beam. Whether or not post-curing is performed, all parts must be washed after printing is complete to remove the surface resin. Washing is generally done in an isopropyl alcohol bath. The removal of the printed support scaffold takes place afterward.
For more information, see our article on everything about 3d printing.
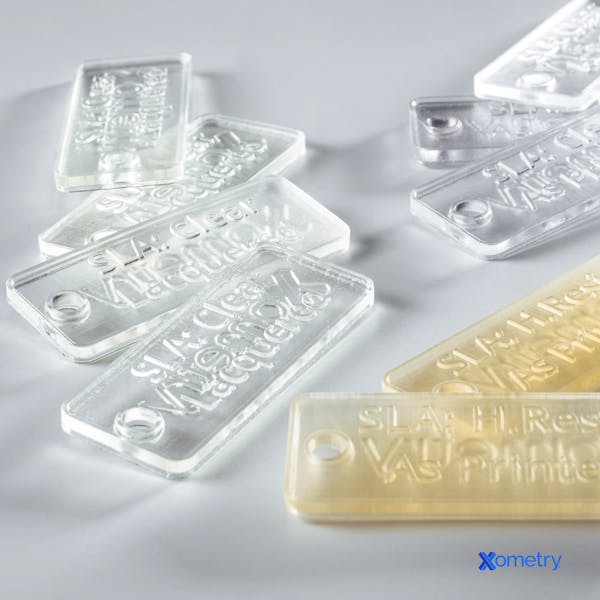
The Light Source for SLA 3D Printing
The SLA 3D printing light source is a UV laser that acts as the stereolithography machine’s curing mechanism. This light source is precisely tuned to the catalyst used in the resin. However, different manufacturers use different wavelengths. The most common SLA laser is a 395 µm wavelength laser diode system. It produces 300-500 mW of power in the beam that is collimated to a diameter of around 300 µm. A variety of other laser light sources can be found in some equipment, with catalysts to suit their frequency range. Other types of UV light sources are used in whole-layer stereolithography. These lamps employ either a projector made of microscopic mirrors (in the case of digital light processing or DLP printers) or an LCD mask (usually referred to as masked stereolithography or MSLA).
SLA 3D Printing's Applications and Uses
SLA 3D Printing is used for applications such as:
- Prototyping: Since they can include fine details, SLA-printed parts can be used as engineering test models.
- Manufacturing: SLA creates functional parts for situations that don’t demand much stress resilience.
- Engineering and product designing: SLA parts can be hand-finished and painted to create quality pre-tooling prototypes.
- Jewelry: SLA machines can build cosmetic test articles for jewelers.
- Dental works: SLA can create various dentistry products, including soft tissue, tooth, bone-implant materials, and casting cavities for polyurethane and silicone molding.
- Healthcare: SLA processes can manufacture medical implants using specialized materials.
Materials Used in SLA 3D Printing
SLA 3D Printers can print using these materials:
- General-purpose acrylic resins: These materials are available in various toughnesses and transparencies.
- Flexible polyurethane elastomers: Used for flexible parts.
- Rigid polyurethanes: These have good cosmetic value, are more durable than general-purpose materials, and are well suited for product-trial or prototype pieces.
- Rigid resins: These are chemically and thermally stable and suited to engineering test parts.
- Dental and medical resins: These resins are medically safe and make for faster builds, quality finishes, and transparent items like mouthguards, splints, etc.
- ESD resins: These resins are suited to making electrostatically safe jigs for manufacturing.
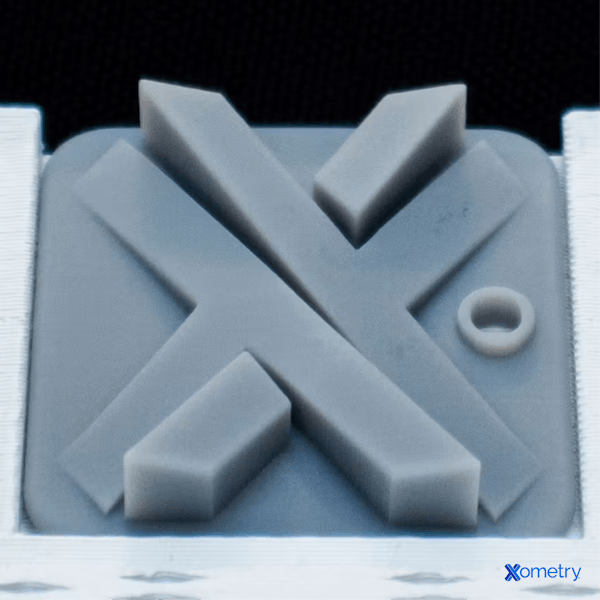
How SLA 3D Printing Works
SLA 3D printing works by moving a UV laser in the X-Y plane. The UV light triggers catalysts in the liquid monomer resin. The print plate begins at the surface of the resin pool, and regions where the laser strikes both resin and the solid plate surface then get polymerized and affixed to the build plate. With that ‘layer’ complete, the build plate moves up, allowing the next layer to affix itself to the previous one. By repeating this process, the part will appear to grow out of the liquid pool. Prints usually begin with the part’s bottom, and the part is printed upside-down.
Once removed, the part must be washed to remove any uncured resin. Any support scaffolding elements can then be cut away.
SLA Printing's Print Parameters
An SLA machine’s print parameters are usually fixed by the manufacturers. It is only the part orientation and layer height that can be changed. Table 1 below shows a comparison of the two common SLA printer orientations:
Setting | Bottom-up SLA Printers (Desktop) | Top-down SLA Printers (Industrial) |
---|---|---|
Setting Typical layer height | Bottom-up SLA Printers
(Desktop) 25 to 100 µm | Top-down SLA Printers
(Industrial) 25 to 150 µm |
Setting Dimensional accuracy | Bottom-up SLA Printers
(Desktop) ± 0.5% (lower limit: ± 0.010 to 0.250 mm) | Top-down SLA Printers
(Industrial) ± 0.15% (lower limit: ± 0.010 to 0.030 mm) |
Setting Build size | Bottom-up SLA Printers
(Desktop) Up to 145 x 145 x 175 mm | Top-down SLA Printers
(Industrial) Up to 1500 x 750 x 500mm |
Table 1. SLA Printer Characteristics
What Distinguishes SLA 3D Printing?
SLA is distinguished from other 3D printing systems and processes through its wide range of materials with very diverse properties and cosmetic qualities. SLA materials have improved and diversified significantly since first appearing in the market. Another distinguishing factor for SLA is its surface finish—one of the highest standards in the industry. The largest SLA machines were designed for the automotive industry and can build whole body panels, dashboards, etc.
SLA Post-Processing Options
SLA post-processing starts by removing uncured ‘wet’ resin. Bottom-up printers must be drained before post-processing while top-down equipment requires no such delay. In both cases, however, parts must be washed to remove any remaining liquid. Though manual spray-booth washing is still common, automatic solutions are marketed for this washing stage. Some resins require additional post-curing under UV radiation. Once complete, support scaffolds are then removed either manually or by automated equipment. At this point, models are usually considered complete. Any further processing such as sanding or painting is typically aimed at improving the part’s cosmetic appearance.
Benefits of SLA 3D Printing
SLA 3D printing offers a wide range of advantages. These are shown in Table 2:
Benefits | |
---|---|
Benefits Material properties | SLA has a wide range of material properties, depending on the supplier. |
Benefits Flexibility | Few 3D printing processes can offer pseudo-elastomer materials, but SLA is a good option for such. |
Benefits Part surface finishes | SLA produces parts with great surface finishes. They are suited to high-spec finishes and also readily accept paint. |
Benefits Fine details of parts | SLA is good for fine details as long as the right equipment, resin, and service provider is chosen. Features down to 0.1 mm are easy to achieve. |
Benefits Uniformity of resolution | SLA has high resolution along the Z-axis but less so in X-Y. Care in process selection and build orientation are important. |
Benefits Production of complex parts | SLA can accurately reproduce complex parts. |
Benefits Curved surfaces | Z-steps on curved surfaces are barely detectable. |
Benefits Print process | The print process can be quick, assuming the overall part is not too tall along the printer’s Z-axis. |
Table 2. SLA 3D Printing Benefits
Drawbacks | Description |
---|---|
Drawbacks High cost of parts | Description Print resin costs $200 per liter. |
Drawbacks Wear resistance | Description Most SLA materials perform poorly in situations of abrasion or stiction, so they shouldn’t be used in moving assemblies. High-strength SLA materials are better but cost more. |
Drawbacks High cost of equipment | Description Industrial SLA machines cost $200,000 while less capable desktop machines start at $3,750. |
Drawbacks Laser-based system | Description Laser-based systems require very careful safety monitoring and training. |
Drawbacks Demanding machine maintenance | Description The lasers and liquid resin make machine maintenance demanding or challenging to perform. |
Drawbacks Different resolution | Description Because the resolution in the X-Y plane is different from that along the Z-axis, some fine details may not come out right. |
Drawbacks Selective material properties | Description Parts made from simpler and more common resins tend to be brittle and may creep under a steady load. |
Table 3. Drawbacks of SLA 3D Printing
Xometry provides a wide range of manufacturing capabilities including Stereolithography (SLA) 3D Printing service and value-added services for all of your prototyping and production needs. Request an instant quote today.
Disclaimer
The content appearing on this webpage is for informational purposes only. Xometry makes no representation or warranty of any kind, be it expressed or implied, as to the accuracy, completeness, or validity of the information. Any performance parameters, geometric tolerances, specific design features, quality and types of materials, or processes should not be inferred to represent what will be delivered by third-party suppliers or manufacturers through Xometry’s network. Buyers seeking quotes for parts are responsible for defining the specific requirements for those parts. Please refer to our terms and conditions for more information.
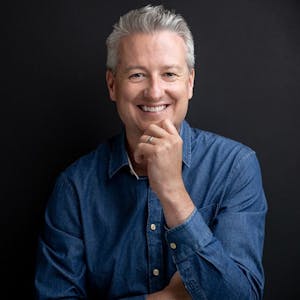