FDM, which stands for Fused Deposition Modeling, and MJF, an abbreviation for Multi-Jet Fusion, are both types of 3D printing, but they differ in a few ways. In this article, we’ll learn a bit more about them, compare their pros and cons, and answer some frequently asked questions.
What is FDM?
Originally developed and made commercially available in 1988 by Scott Crump, fused deposition modeling is one of the most popular methods of 3D printing today. It works by pumping a thin thermoplastic filament through a heated nozzle and depositing it layer-by-layer to make the part. It’s relatively cheap compared to MJF printing—which is more popular in industrial settings—and is usually easier to get hold of.
The beauty of FDM printers is that they are compatible with filaments from different companies, but MJF printers are limited to materials from HP. FDM does have a couple of drawbacks, too, especially when compared to MJF, which we’ll discuss later. For starters, it produces parts with a low-quality surface finish. Another disadvantage is that FDM printed parts tend to be anisotropic, meaning they’re not as strong in the z-direction because of poor interlayer bonding. We have an article on FDM 3D Printing which we recommend you check out for more information. This is an image of a part made using FDM printing:
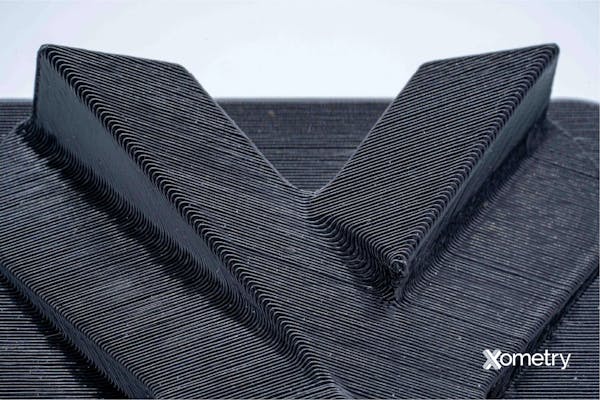
What is MJF?
Multi-jet fusion is another type of 3D printing that was created by the company HP in 2016. It’s quite different from FDM in that it requires several steps before a part is complete, the first of which is adding a thin layer of powder to the printing bed and heating it to just under its sintering temperature. The next part is adding a fusing agent to the powder in the shape of the part’s cross-section. Then a detailing agent is added to the exterior edges to help them be sharper and more crisp.
When that’s done, a source of heat is passed over the plastic, which sinters the particles together wherever the fusing agent is. It’s pretty clear that MJF is more advanced than methods like FDM, and that’s why it’s used a lot in high productions. MJF has some further advantages when compared to FDM, including that its parts come out highly accurate and faster, and that’s partly because you can print more than one part at a time. Also, unlike FDM, MJF parts are isotropic, making them uniform when it comes to their mechanical properties, regardless of direction.
On the other side of the coin, however, MJF printers are among the most expensive types of 3D printers available today—way more expensive than the most advanced FDM printers. They also have a very limited amount of color options, and can only be dyed black, whereas FDM printers can print in lots of different colors. You can check out our article on MJF to learn more about it. The following image shows a part printed using an MJF printer:
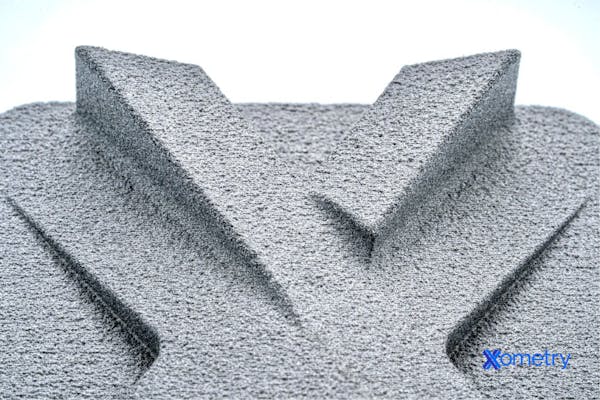
Attribute | MJF | FDM |
---|---|---|
Attribute Print resolution | MJF 80 microns | FDM 50 to 500 microns |
Attribute Minimum feature size | MJF 0.25 mm | FDM 1 mm |
Attribute Parts need to cool down after printing | MJF Yes | FDM No |
Attribute It can produce high-strength parts | MJF Yes | FDM Yes |
Attribute Minimum wall thickness | MJF 0.5 mm | FDM 1 mm |
Attribute Print speed | MJF 300 cm3/hour | FDM 10 cm3/hour |
Attribute The parts need support structures | MJF No | FDM Yes |
Attribute Largest print volume | MJF 370 x 274 x 375 mm | FDM 1000 x 1000 x 1000 mm |
FDM vs. MJF Comparisons
Xometry’s Senior Solutions Engineer, Matt Schmidt, says about these methods: “Both FDM and MJF are great platforms for prototype and production. MJF prices are often very competitive with FDM and offer better mechanical part properties, production costs, and surface quality, while FDM can offer a wider material selection, greater part size capability, and colors. They are very different platforms, and the decision is often based upon each platform's unique build capabilities mentioned previously, and whether they fit the customer's need. Cost could be a non-factor if the part does not meet a cosmetic need, for example."
What’s the Difference in Materials Used?
FDM printers can work with a whole range of materials, including both rigid and flexible thermoplastics of different colors. MJF printers, on the other hand, are restricted to materials like nylon, polypropylene, and thermoplastic polyurethane, but they can make stronger prints than FDM printers.
What’s the Difference in How the Products are Used?
Parts made with an FDM printer can be pretty versatile, so they can be used for things like functional and visual prototypes and mechanical components on limited production runs. MJF parts are usually stronger and tougher, so they’re great for low-volume functional parts as an alternative to injection molding which is way more expensive for low production volumes.
How Much More Expensive is MJF?
Well, you can buy a top-of-the-range FDM printer for around $7,000, but MJF printers usually start at $270,000. The answer is painfully obvious. However, if you need to print FDM or MJF parts, you can use our online quoting engine today and source them directly from Xometry!
How Xometry Can Help
If you have any further questions regarding FDM or MJF, or any 3D printing process for that matter, feel free to reach out to one of our representatives who would be happy to help you. We also offer a huge range of manufacturing services, like CNC machining and laser cutting. Feel free to get a no-obligation quote and get started today. Don’t worry, it’s free.
Disclaimer
The content appearing on this webpage is for informational purposes only. Xometry makes no representation or warranty of any kind, be it expressed or implied, as to the accuracy, completeness, or validity of the information. Any performance parameters, geometric tolerances, specific design features, quality and types of materials, or processes should not be inferred to represent what will be delivered by third-party suppliers or manufacturers through Xometry’s network. Buyers seeking quotes for parts are responsible for defining the specific requirements for those parts. Please refer to our terms and conditions for more information.
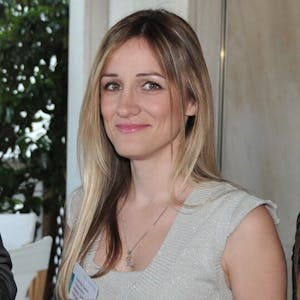