PP (Polypropylene) is a semicrystalline thermoplastic. It is the second most commonly used commodity plastic after polyethylene. PP finds its main application in food packaging and consumer products. Polypropylene was first discovered in 1951 by J. Paul Hogan and Robert Banks, employees at Phillips Petroleum at the time. It was later perfected by German scientist Karl Rehn. His work enabled the mass production of polypropylene.
PP’s use in 3D printing is not so widespread. It can be difficult to print due to its propensity to warp. PP needs a heated build volume and a relatively high build plate temperature. PP 3D printing filament can be supplied in translucent or colored varieties or filled with various additives like glass fiber, talc powder, or an ethylene copolymer. The three main advantages of 3D printing with polypropylene are that it has: excellent fatigue resistance, good chemical resistance, and good interlayer bonding. This article will discuss the general characteristics of polypropylene, along with its composition, properties, and limitations, and compare it with other 3D printing filaments.
What is PP 3D Printing?
3D printing is the process of making a part by subsequently building up a part layer by layer by depositing melted plastic. Polypropylene filament can be used as a raw material for 3D printing. It is gaining acceptance and market share as technical difficulties with printing this thermoplastic is solved. As such PP (polypropylene) 3D printing filament is one of the most popular materials for printing living hinges due to its excellent fatigue resistance and toughness. Polypropylene also has excellent chemical resistance to a wide range of acids, bases, and solvents at room temperature making it widely used in the medical and automotive industries. For more information, see our guide on 3D printing.
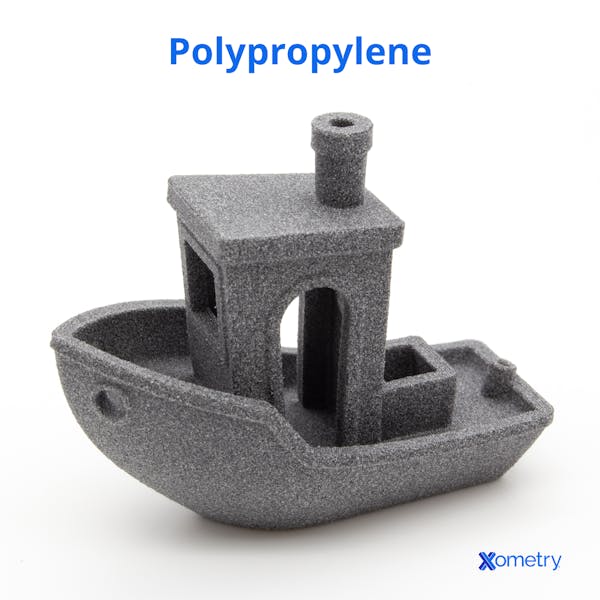
What is the Composition of PP Filament?
Polypropylene is a semicrystalline monomer with the formula (C3H6)n. It is produced via chain-growth polymerization of propene. Polypropylene is available as a homopolymer (general purpose grade), a block copolymer (incorporates between 5 and 15% ethylene), and a random copolymer (incorporates randomly arranged co-monomers along the main polypropylene molecular chain and includes between 1 and 7 % ethylene). Black titanium oxide pigment can be added to color the plastic and improve its UV (Ultraviolet) light resistance. Glass-filled polypropylene filament is available to increase standard polypropylene's heat deflection temperature at the expense of impact resistance.
What Are the Properties of PP Filament?
Some key properties of polypropylene are listed below lists some key mechanical and thermal properties of PP 3D printing filament:
- Polypropylene has a melting temperature of 130°C and a heat deflection temperature of 64.1°C.
- One of the most important properties of PP is its chemical stability. This chemical stability means that it is resistant to many different chemicals, including acids and alkalis.
- Polypropylene can resist impact loading with braking or shattering.
- Polypropylene can withstand millions of stress cycles without failing.
Comparison of PP Filament Properties
Table 1 lists the properties of PP 3D printing filament in comparison to a range of other high-performance filaments:
Property | PP | ABS | PETG |
---|---|---|---|
Property Tensile Modulus (MPa) | PP 234 ± 16 | ABS 1699 ± 113 | PETG 1711 ± 45 |
Property Tensile Stress @ Yield (MPa) | PP 8.6 ± 0.4 | ABS 38.1 ± 0.3 | PETG 46.2 ± 0.8 |
Property Elongation @ Yield (%) | PP 18.7 ± 3.0 | ABS 4.1 ± 0.1 | PETG 5.9 ± 0.1 |
Property Flexural Modulus (MPa) | PP 250 ± 9 | ABS 1317 ± 28 | PETG 1489 ± 25 |
Property Flexural Strength (MPa) | PP 9.4 ± 0.3 | ABS 21.5 ± 1.8 | PETG 50 ± 3.5 |
Property Charpy Impact Strength (kJ/m2) | PP 49.1 ± 3.2 (Notched) | ABS 1.5 ± 0.1 (Hinge) | PETG 7.9 ± 0.6 (Notched) |
Property Hardness (Shore D) | PP 42 | ABS 76 | PETG 76 |
Property Heat Deflection Temperature (0.455 MPa) | PP 64.1 ± 3.6 | ABS 86.6 ± 0.4 | PETG 76.2 ± 0.8 |
Property Glass Transition Temperature (°C) | PP -20 | ABS 100.5 | PETG 77.4 |
Property Melting Temperature (°C) | PP 130.6 | ABS 200 | PETG 230-250 |
Table Credit: Comparison of PP vs ABS vs PETG
What Are the Limitations of 3D Printing with PP?
Polypropylene (PP) is not commonly used for 3D printing due to the general difficulties involved in the process. The key challenges to using PP 3D printing filament are:
- It tends to warp during printing if temperatures are not precisely controlled. A heated print volume is therefore needed to limit shrinkage and warping.
- Printed PP tends to detach from the print bed if a suitable adhesive is not applied.
- It will degrade under long exposure to UV light. Although this problem can be mitigated with additives, PP is generally not suited to outdoor applications.
Listed below are some of the key benefits of printing with polypropylene:
- It is resistant to a wide range of solvents, bases, and acids at room temperature. However, PP is not resistant to nitric acid with a concentration above 65% or sulphuric acid above 93%.
- It has excellent fatigue resistance. PP is widely used for living hinges (i.e. flexible hinges that rely on a material's ability to flex), which can undergo millions of stress reversal cycles without permanent deformation.
- PP has excellent impact resistance when compared to more commonly used engineering thermoplastics like nylon or ABS.
Why is PP Used in 3D printing?
PP (Polypropylene) 3D printing filament is not very mechanically strong. However, it does have some unique uses such as living hinges, translucent containers, and wearable device straps. This uses is due to its excellent fatigue strength and chemical resistance. PP is also widely used in the medical and automotive industries. Like most thermoplastics, polypropylene is also recyclable.
How to Use PP in 3D Printing
PP 3D printing filament is one of the more difficult thermoplastics to print. However, if the correct settings are used there is no reason why excellent results can’t be achieved. Listed below are some tips for printing with polypropylene:
- PP 3D printing filament does not easily bond to an unprepared build plate. Packaging tape applied to the build plate will create a good bond to the first printed layer, and so will certain specialized glue sticks, such as Magigoo PP.
- Polypropylene will easily warp during printing if the print environment is not maintained at a relatively high temperature of 45°C. That being the case, an enclosed print volume is recommended.
- A “raft” is a printed base on top of which an actual part can be printed. Using a raft will protect the base layer of the part, as sometimes the part will bond too well to a properly prepared build plate, and removing the part can damage its base. A raft can be easily removed by simply pulling it off.
What Are the Best Configuration Settings for PP 3D Printing?
While a heated build volume and proper bed adhesion practices will make printing polypropylene much easier, it is still important to use the optimal settings. Listed below are some key parameters to use as starting points. However, it is always advisable to refer to the specific PP 3D printing filament technical datasheet for your specific printing filament to find the optimal settings. The following data in Table 2 are some of the important printer settings to determine and set before printing with polypropylene filament:
Printer Setting | Value |
---|---|
Printer Setting Bed temperature | Value 85-100°C |
Printer Setting Nozzle temperature | Value 205-220°C |
Printer Setting Print speed | Value 30-90 mm/s (slower speed produces better results) |
Printer Setting Retraction distance | Value 6.5 mm |
Printer Setting Infill Density | Value 20% |
What is the Best PP 3D Print Speed?
The printing speed for polypropylene can be anything from 30 mm/s to 90 mm/s. Printing at higher speeds will reduce overall print time but there will be increased dimensional instability. Printing at higher speeds will also improve overall part strength, as the time between each layer print is reduced, allowing for improved interlayer bonding. If higher printing speeds are desired, the 3D printer used must be rigid enough so that there isn't excessive vibration during printing. Too much vibration will reduce the part quality.
What is the Melting Temperature of PP Filament?
The general melting temperature of PP filament is 130.6°C. However, the melting temperature of PP 3D printing filament depends on the specific manufacturer and what additives were included. It is recommended to refer to the specific material technical data sheet before printing.
Is a Heated Printing bed Required when Printing with PP?
Yes, a heated printing bed is required when printing with polypropylene. Failure to print with a bed heated to at least 85°C will cause bed plate adhesion problems, resulting in a failed print.
What is a Good Wall Thickness for 3D Printing PP?
The optimal wall thickness for a polypropylene part depends on the end use of the part being printed. In general, a wall thickness of about 1 mm will be ideal. If a wall doubles as a living hinge, then the ideal print thickness can be as low as 0.4 mm.
What is a Good Wall Density for 3D Printing PP?
The optimal infill density for a nonfunctional mockup polypropylene 3D printed part is 20%. However, this density must be adjusted depending on the intended application. Load-bearing applications may require 50-80% infill density. The standard grid-type infill will be sufficient for the majority of applications.
Is PP Hygroscopic?
Polypropylene 3D printing filament is not hygroscopic. It does not readily absorb moisture.
What is the Difference Between PP and PLA in 3D Printing?
PLA (Polylactic Acid) is a rigid and brittle material that has poor fatigue resistance compared to polypropylene. However, PLA is significantly cheaper than PP 3D printing filament and is much easier to print.
What is the Difference Between PP and ABS in 3D Printing?
ABS (acrylonitrile butadiene styrene) has significantly better mechanical strength than polypropylene 3D printer filament. However, both materials are prone to warping and require heated build volumes during printing.
What is the Difference Between PP and PET in 3D Printing?
There is considerable overlap in the applications of PP and PET (Polyethylene Terephthalate). For example, both are used to safely store food and liquids. PP and PET also have similar temperature resistances and stiffness properties.
Summary
This article presented PP 3D printing filament, explained what it is, and discussed different factors to consider when using it in 3D printing. To learn more about PP 3D printing filament, contact a Xometry representative.
Xometry provides a wide range of manufacturing capabilities, including 3D printing and other value-added services for all of your prototyping and production needs. Visit our website to learn more or to request a free, no-obligation quote.
Disclaimer
The content appearing on this webpage is for informational purposes only. Xometry makes no representation or warranty of any kind, be it expressed or implied, as to the accuracy, completeness, or validity of the information. Any performance parameters, geometric tolerances, specific design features, quality and types of materials, or processes should not be inferred to represent what will be delivered by third-party suppliers or manufacturers through Xometry’s network. Buyers seeking quotes for parts are responsible for defining the specific requirements for those parts. Please refer to our terms and conditions for more information.
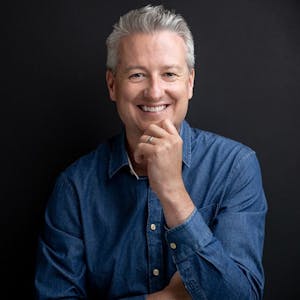