Thermoplastics and thermosets are two classes of plastic materials. They differ from each other in their properties, the methods used to manufacture them, and their product applications.
Thermoplastics are used to make many everyday products such as water bottles, straws, apparel, luggage, and machinery components in automobiles and aircraft. Thermoplastic products can be produced by a variety of plastic fabrication methods such as injection molding, blow molding, extrusion, and thermoforming.
Like thermoplastics, thermosets are also in common use and are often employed in situations where heat and environmental stability are critical factors. Therefore, thermosets are often found in electronics, heavy appliances and machinery, and chemical processing equipment. Fabrication of thermoset products is usually accomplished through reaction injection molding and resin transfer molding. It is important that designers understand the differences between the two materials to be able to choose the best material options for their products. This article will compare thermoplastic vs thermoset in terms of applications, properties, and costs.
What is a Thermoplastic?
Thermoplastics are a group of plastics that are useful because they can be heated and softened or melted for forming, then hardened into a desired shape after cooling, without undergoing permanent chemical changes. This makes it possible for them to easily be recycled by simply reheating them and forming them into a new shape. At room temperature, thermoplastics are solid. At high temperatures, though, thermoplastics begin to soften and eventually completely melt at a temperature well above the glass transition temperature.
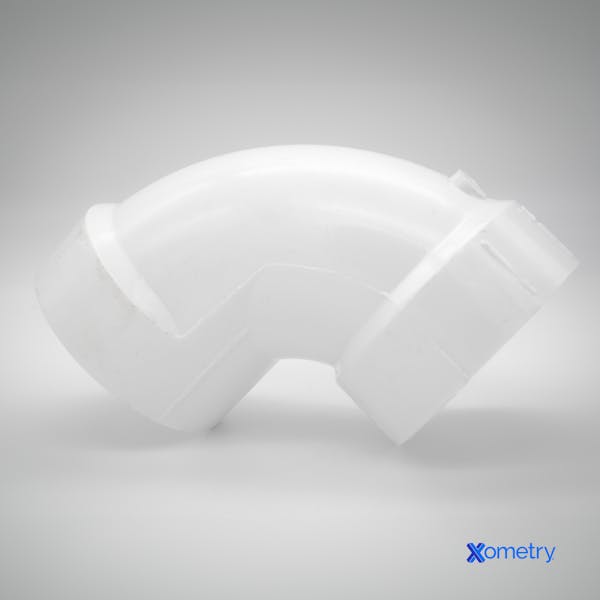
Materials like polypropylene (PP), polyethylene (PE), polycarbonate (PC), nylon, and polyoxymethylene (POM) are all examples of thermoplastic materials. The most common processes used to make parts composed of thermoplastics are injection molding, extrusion, and thermoforming. Thermoplastics are used in several industries for several applications, including: textiles, food containers, cookware, hand and power tools, pipes and electrical cables, machinery and construction components, medical devices, and many more.
What is a Thermoset?
Thermosets are polymerized plastics composed of individual monomers that are liquid or soft solid at room temperature. When heated, or when certain chemicals (catalysts) are added, thermosets harden irreversibly. The applied heat (or chemical catalyst) causes the polymer chains in a thermoset plastic to cross-link with each other, holding the molecules more firmly in position. Crosslinking changes the properties of the material, making it impermeable and rigid. Once the crosslinking chemical changes take place, thermosetting polymers cannot be remelted or reprocessed.
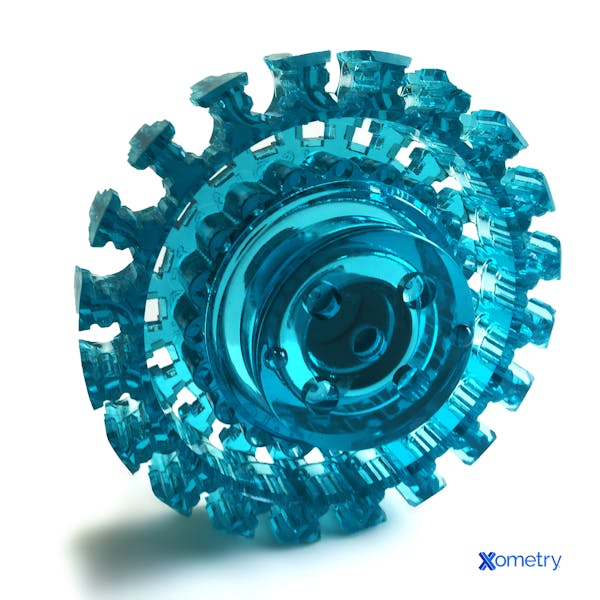
Like thermoplastics, thermoset products are made using molds, but with slightly different processes, such as reaction injection molding or resin transfer molding. Due to the cross-linking process, thermosets are highly corrosion-resistant and resistant to creep. This makes thermosets ideal for applications that require high strength-to-weight ratios or excellent thermal and environmental stability, like air intake manifolds in automobiles or disc brake pistons in heavy machinery. Phenolic resin, silicone, polyurethane, and epoxy are some examples of thermoset materials.
Thermoplastic vs. Thermoset: Application and Uses
Despite the differences in fabrication methods and properties between thermoplastic and thermosetting materials, either one can successfully be used for some applications. For other applications, only the special properties of one type of plastic or the other will do. The list below highlights some of the shared applications of thermoplastic and thermosetting materials:
- Textiles and upholstery
- Food and beverage packaging
- Medical and science laboratory equipment
- Consumer products like toys, lamps, and office supplies
Listed below are the thermoset-exclusive applications:
- Construction materials such as adhesives, sealants, and insulation
- Lighting fixtures
- Components of light watercraft (boats, kayaks, jet skis)
Listed below are the shared applications between the two:
- Lightweight components in automobiles, aircraft, and heavy machinery
- Cookware and kitchenware
- Electronic components
- Piping and plumbing
Thermoplastic vs. Thermoset: Physical Properties
There are notable differences in the physical properties of thermoplastic vs. thermoset materials. Depending on the particular thermoplastic or thermoset material being compared, the two materials can be highly similar—almost identical in their properties—or wildly different. Table 1 below shows a general comparison of the properties of the two materials - using polypropylene (PP) and epoxy (thermoset) as the basis for comparisons:
Property | Thermoplastic (Polypropylene) | Thermoset (Epoxy) |
---|---|---|
Property Heat Deflection Temperature | Thermoplastic
(Polypropylene) Low heat deflection temperature (HDT) compared to thermosets | Thermoset
(Epoxy) Exceptionally high heat deflection temperature (HDT) compared to thermoplastics |
Property Wear Resistance | Thermoplastic
(Polypropylene) Similar wear resistance to thermoset | Thermoset
(Epoxy) Similar or lower wear resistance compared to thermoplastic due to filler materials and additives |
Property Abrasion resistance | Thermoplastic
(Polypropylene) Similar abrasion resistance to thermosets | Thermoset
(Epoxy) Similar abrasion resistance to thermoplastics |
Property Chemical Resistance | Thermoplastic
(Polypropylene) Poor resistance to certain chemicals, including organic and highly polar solvents and hydrocarbons | Thermoset
(Epoxy) High chemical resistance compared to thermoplastics |
Property Elasticity | Thermoplastic
(Polypropylene) More elastic than thermoset materials | Thermoset
(Epoxy) Less elastic than thermoplastics due to cross-linked, rigid bonds |
Property Density | Thermoplastic
(Polypropylene) Similar density to thermosets | Thermoset
(Epoxy) Similar density to thermoplastics |
Property Toughness | Thermoplastic
(Polypropylene) Higher toughness compared to thermosets | Thermoset
(Epoxy) Lower toughness compared to thermoplastic due to cross-linked bonds that make the material brittle. |
Recyclability and Sustainability
A major difference between thermoplastic and thermoset materials is how the two are recycled, and how sustainable they are for the environment. Thermoplastic materials can be reused several times after they are originally molded into parts. Because they can be remelted, existing thermoplastic parts can be ground into granules and used to make parts made out of 100% reclaimed plastic or can be mixed with a virgin thermoplastic resin to create new parts. Nevertheless, when simply discarded instead of being recycled, thermoplastic materials take decades to fully decompose in nature.
Thermoset materials, on the other hand, can neither be reused nor recycled. Because of the cross-linked bonds in thermoset materials, they cannot be remelted and reformed. While their thermal stability gives parts made from thermoset materials a long life, they are difficult, if not impossible, to recycle on a large scale. Additionally, since both thermoplastic and thermoset materials are petroleum-based, neither can be considered sustainable for the environment.
Thermoplastic vs. Thermoset: Cost
Most thermoplastics are often priced lower than thermosets. The difference in price lies in the tooling, materials, and labor needed to produce the thermoplastic and thermoset resins. Because thermosets require fillers and additives to complete the cross-linking process, thermosets are often more expensive. However, some thermoplastics can be more expensive than thermosets for the exact same reason. Regardless, both thermoplastic and thermoset materials are much more cost-effective than similar parts made from metals in certain applications.
Xometry provides a wide range of manufacturing capabilities including CNC machining, 3D printing, injection molding, laser cutting, and sheet metal fabrication. Get your instant quote today.
Disclaimer
The content appearing on this webpage is for informational purposes only. Xometry makes no representation or warranty of any kind, be it expressed or implied, as to the accuracy, completeness, or validity of the information. Any performance parameters, geometric tolerances, specific design features, quality and types of materials, or processes should not be inferred to represent what will be delivered by third-party suppliers or manufacturers through Xometry’s network. Buyers seeking quotes for parts are responsible for defining the specific requirements for those parts. Please refer to our terms and conditions for more information.
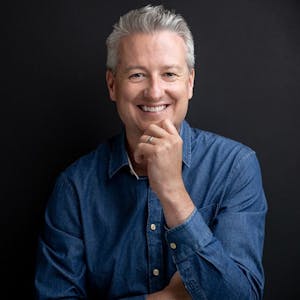