The material jetting category covers multiple 3D printing processes. While the processes vary widely, all operate by applying “printed” droplets of liquid or liquified resin to a Z-table, building up sequentially to reproduce the part as defined by the CAD file. Material jetting technologies encompass many market sectors such as jewelry, engineering, aerospace, and medical. These technologies serve in the most demanding applications.
This article will dive deeper into the applications and process of material jetting.
An Intro to Material Jetting
Material jetting is an inkjet printing process where inkjet-type printheads apply droplets of material to print a model slice. These “inks” can be pure photopolymer or pure waxes, or they can contain ceramic or metal particles. Some machines have heads for applying color to the model. Material jetting falls into three categories, by the nature of the materials they use:
- PolyJet: PolyJet builds plastic prototypes by jetting photopolymer droplets into the build platform and solidifying them using UV light.
- NanoParticle Jetting (NPJ): NPJ is a technology developed by XJet. It uses suspensions of powdered material (usually metal or ceramic) to build parts.
- Drop on Demand (DOD): DOD uses the bubble-jet approach to apply wax to a Z-table moved in the X-Y plane to build casting patterns for fine components like jewelry.
Material Jetting Applications
Material jetting is used widely in the more demanding applications for 3D printed parts. Examples of industries and their applications are:
- Medical: Colored and precise parts are often used for medical visualization models, for example, printing organs and structures within a patient built from PET scan models.
- Jewelry: DOD wax printing is widely employed to make casting patterns for limited production runs by lost wax casting.
- Engineering: PolyJet systems are widely used in the production of engineering test pieces or prototypes. These printed parts offer very high resolution and accuracy and allow at least partial simulation of real material behavior in highly detailed and delicate parts.
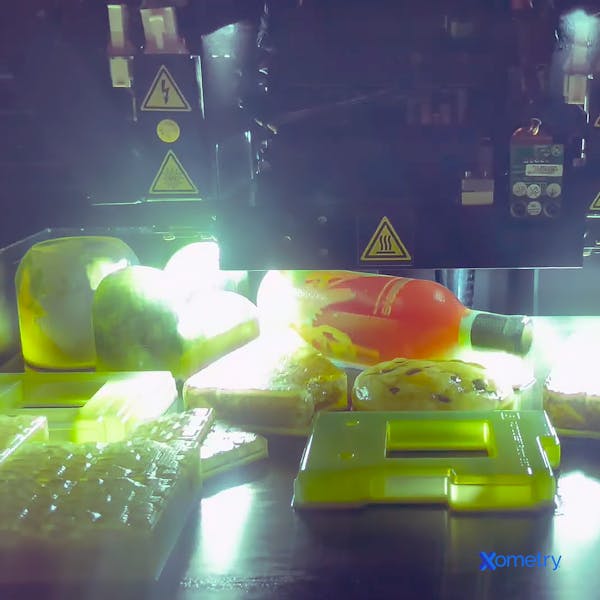
Advantages of Using Material Jetting for Your Parts
Some of the advantages of using material jetting are:
- Production of small, finely detailed metal parts is more practical and effective. Material jetting can produce details as small as 16 µm in 60% density.
- In the production of small (up to 300 mm) components, PolyJetting achieves higher accuracy, better reproduction of detail, and best-in-class delivery of fine features – down to surface textures in the 0.05 mm range.
- At 0.016 mm, material jetting offers the best Z-axis resolution in the sector.
- Despite high Z-resolution (i.e. thin layers), the commonly used wide printheads employed in most material jetting technologies allow for build speeds to remain competitive with, for example, FDM. FDM offers much lower Z resolution – thick layers – but builds on a single nozzle, point-to-point process.
- Direct printing of bio-compatible parts is practical in material jetting.
Cons of Material Jetting
Material jetting’s limitations are:
- Plastic components printed by material jetting have some sensitivity to light and will degrade in elevated UV environments.
- Material jetting materials tend to be among the highest-priced, often exceeding $1000 per kg.
- The equipment is among the most expensive in the sector to both buy and operate.
- As the printheads handle viscous and curing fluids, it is necessary for clearing processes to be carried out during and after builds. This increases material consumption and labor costs.
- The water-soluble build-support materials result in the need for a delicate post-process to wash away supports.
- Some methods require a UV cure post-processing to cure the resins fully.
- Build envelopes are generally small (below 300 mm per axis).
The nature of the processes used in material jetting applications results in the highest practical resolutions in all three axes. Printed parts can achieve dot resolutions in the printed image (slice) approaching that of paper printers.
The Material Jetting Process - How it Works
The material jetting process in 3D printing works by jetting the materials. Depending on the material, two processes can be applied—either a bubble-jet process (for volatile materials) or a piezo jetting mechanism (for non-volatile materials). The flow of droplets from the printhead is also variable between technologies. DOD systems eject a single droplet when instructed. The material traverses the limited-port-count printhead in X-Y to the next droplet positions, depositing individual drops of print material. PolyJet, on the other hand, acts in the same drop-on-demand way, except that the printhead is wide and contains many jetting ports that are individually addressed. Droplets land in pre-defined positions on the table and coalesce to form a precise “picture” of the model slice.
Curing or hardening is dependent upon the nature of the materials. Volatile materials will immediately cool and solidify, once they hit the cooler build surface. UV-cured resins, on the other hand, will cool on the surface and their viscosity will rise to allow them to gel sufficiently to stay in place. A UV lamp will then pass over them, fully or partially curing the catalyzed cross-linking that results in a solid polymer. For some wax printers, a fly cutter passes over the printed and hardened surface, to provide a smooth, flat platform for the next layer to be applied to. In all cases, once a slice is printed, the table will drop by one layer thickness to allow the next vertical layer to be applied.
For more information, see our guide to 3d printers.
Materials Used in Material Jetting
The materials used in material jetting are alumina (aluminum oxide), zirconia, stainless steel, waxes, and UV-cured resins. These UV-cured resins are generally formulated from modified acrylic monomers. A growing variety of types of print resin are available to suit various applications. Examples are resins of various colors and clarities, including lens quality, high temperature, and rubbers of various hardnesses.
Summary
Xometry provides a wide range of manufacturing capabilities including custom 3D printing services, CNC machining, injection molding, laser cutting, and sheet metal fabrication. Get your instant quote today.
Disclaimer
The content appearing on this webpage is for informational purposes only. Xometry makes no representation or warranty of any kind, be it expressed or implied, as to the accuracy, completeness, or validity of the information. Any performance parameters, geometric tolerances, specific design features, quality and types of materials, or processes should not be inferred to represent what will be delivered by third-party suppliers or manufacturers through Xometry’s network. Buyers seeking quotes for parts are responsible for defining the specific requirements for those parts. Please refer to our terms and conditions for more information.
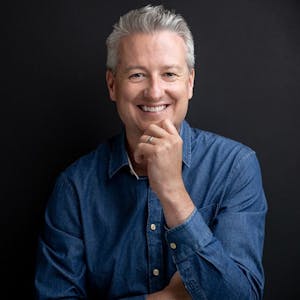