Designing Accessible 3D Printing Products for People with Disabilities
Join Xometry's Greg Paulsen and listen in to a panel discussion focused on how to design human-friendly assistive devices with CNN journalist and filmmaker Miles O'Brien and the founders of Blue Heart Hero’s, Amin Hasani and Jed Tango.
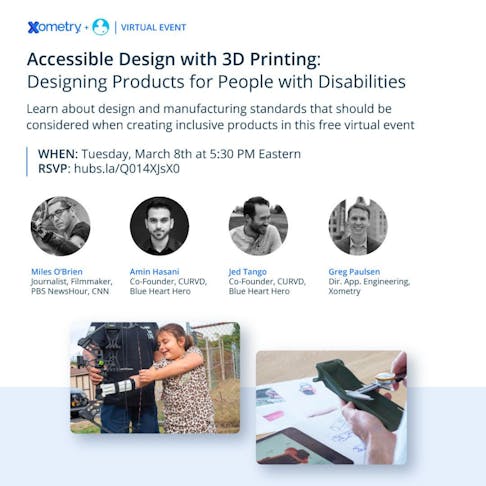
Prosthetic arms and legs are incredibly helpful solutions for people with limb differences, leaving them better equipped to tackle a variety of challenges. Unfortunately, their high cost and limited designs can keep them from being the best tool for every situation that people with limb disabilities face on a day-to-day basis.
In this recorded webinar, Xometry's Greg Paulsen and listen in to a panel discussion focused on how to design human-friendly assistive devices. CNN journalist and filmmaker Miles O'Brien and the founders of Blue Heart Hero, Amin Hasani and Jed Tango join the panel for a thought-provoking discussion about engineering products that are inclusive and accessible for people with disabilities. Designers who want to create products that will empower people with limb differences to navigate their environments are sure to love this discussion.
Full Transcript
Greg Paulsen: Everybody, thank you so much for joining today's event. I'm Greg Paulsen, Director of Application Engineering. And I'm just really, really excited about this topic that we'll be going over today.
Greg Paulsen: So this event is Accessible Design with 3D Printing: Designing Products for People with Disabilities. And we are featuring the founders of Blue Heart Hero who are making accessible devices, democratized almost by allowing for crowdsourced designs, utilizing 3D printing as part of their platform, as well as special guest Miles O'Brien.
Greg Paulsen: Before we get started though, I want to lay down some groundwork. We're going to start with some introductions and background. From there, we'll jump into Q&A surrounding some main topics around design for accessibility. And you, the audience, also have an opportunity to submit questions at any time in the Q&A tab using the GoToWebinar platform.
Greg Paulsen: So you should see Q&A there. You could go and submit your questions. And we'll try to get to as many as possible at the end of this event. This webinar is recorded, and we'll send an email with a recording for you to rewatch and share with your colleagues as well.
Greg Paulsen: But let's just jump into things. So very excited to introduce this team here. We should see some cameras popping up as we're going here. Yeah, there we go. I love it. For me, it's like the Brady Bunch, everybody just shows up on the screen here. Greg Paulsen: I am just so excited about this panel, so excited about talking about this. And I'm going to actually start by introducing Amin Hasani and Jed Tango who are co-founders of both CURVD, which we are all sporting our CURVD mugs here to show off today, and Blue Heart Hero. Amin, if you want to give a quick intro.
Amin Hasani: Yeah. Hi, everyone. Thank you so much for joining this webinar. Really excited about this event. I'm Amin Hasani. I'm the design director at PLUGOUT. I design products for major banks and airports in the US. Amin Hasani: And product design and 3D printing and technology is my passion. I've been designing products since I was 14. And my very first product was actually a wheelchair for kids with disabilities. And I made small prototypes and found my passion in product design.
Greg Paulsen: And Jed, how about you?
Jed Tango: How's it going, everyone? So my background is actually Naval engineering, and I got into this because me and Amin actually met years ago. And we were talking about what was happening and we got really excited about this.
Jed Tango: I actually moved in with Amin a few years ago to focus on this. And ever since then, we've been making a lot of progress in this field and making and designing a lot of stuff.
Greg Paulsen: And a special guest. So Amin and Jed emailed and they were like, "Oh, and Miles O'Brien will be joining on," which is just amazing. So we have Emmy-awarded independent journalist and filmmaker Miles O'Brien.
Greg Paulsen: So you may know Miles from NOVA, FRONTLINE. He's an aviation analyst on CNN, a science correspondent on PBS NewsHour. Miles, thank you so much for being here too today for this discussion.
Miles O'Brien: It's a real pleasure. I hope we can move the ball forward and teach some people a few things.
Greg Paulsen: I will also say what's exciting about this is as we talk, I think everybody has gadgets in front of them to talk about these. Because there are solutions and all these items actually really do help you have paradigm shifts, if you will, when you think about accessibility.
Greg Paulsen: And some of these, what I usually call a mental model, right? A mental model when I'm thinking about design, and we're going to discuss a lot about that today. Miles, I do want to spotlight a little bit further on you because you've had this experience in science and tech as a journalist, but there was an accident in 2014, correct?
Miles O'Brien: Yeah. I've been a science and technology journalist for about 30 years and starting at CNN in '92. And in the course of doing that, I did quite a few stories about promising solutions for the disabled, including amputees. And as I look back on those stories, I really didn't know what I was talking about. Miles O'Brien: In 2014, I learned what I was talking about in a very profound way. I was on assignment in Southeast Asia, stacking up some cases, a case fell on my arm. Wasn't in a good position to get to a hospital. Didn't think it was a big deal anyway. I got what's called acute compartment syndrome. One thing led to another.
Miles O'Brien: The blood flow stopped in my arm and it had to be amputated in an emergency surgery. So that was quite a story to tell, all of a sudden, in a very personal way.
Miles O'Brien: And so since that time, I've been going through a personal journey on how to return to life as I knew it. And along the way, I've been trying to share that story as much as possible with others as a way to help people figure out how to meet their own challenges.
Greg Paulsen: Thank you so much for being here to share because there's just so much that we could learn as well, especially when we're talking designs and these big ideas. I'm burying the lede here, but it's just very, very exciting to have your insight.
Greg Paulsen: Something I wanted to start with though is what we usually think of as these paradigms when you're talking about limb differences or amputees. And we're talking about the high-end prostheses. And I wanted to bring in a NewsHour clip.
Greg Paulsen: And this is going to be muted, but if you could walk through, this is a clip of you controlling a prosthetic arm. This is a very high-tech version here. So I'm going to run the roll here.
Miles O'Brien: Yeah. So this is me in Laurel, Maryland at the Applied Physics Laboratory, Johns Hopkins University.
Greg Paulsen: That's 20 minutes from me. Miles O'Brien: What's that?
Greg Paulsen: About 20 minutes away from where I am.
Miles O'Brien: Oh, cool. So they developed what's called the modular prosthetic limb, you see it there. Part of the reason it's sitting on a bench is it would be way too heavy, or at least at the time I was in there, way too heavy to wear. There are people wearing them now.
Miles O'Brien: And just called out of the blue without any real training. They attached some of those electrodes to my stomp and did a little bit of training. And I was able to do some things with it. It was actually kind of remarkable. But then when you really get down to the reality on this thing, it's pretty... Well, suffice to say, they set the bar pretty high, "they" being the Veterans Administration.
Miles O'Brien: It has 21 degrees of freedom, I believe. And it can curl a 50-pound barbell, which I'm not sure why anybody would want that, except I suppose there are probably some young Marines who came out of Iraq or Afghanistan who maybe wanted that. I don't know.
Miles O'Brien: And it pretends to do a lot of things, but what you realize very quickly is that, number one, it's heavy. Number two, it's extremely complex, power-hungry. And number three, the real choke point is in the stomp. How do I get what I want it to do through here and into those amazing servos at our fingers?
Miles O'Brien: And you soon realize that that's an important choke point. And while it looks really cool to see somebody operating that, my ability to do much with that was extremely limited and still would be extremely limited even if I got some specialized surgery to make it better to control that limb. And in the end, that limb still did not have sensory feedback. Miles O'Brien: And so I walked away thinking it probably would do just about what this thing does, this thing is about 150-year-old technology or more, and with a great more deal of complexity and weight and everything else.
Miles O'Brien: As I mentioned to you before, Greg, I covered the space program for quite a long time at CNN. And I know that, engineers, when they build a spacecraft, they're always thinking about two things; power consumption and weight. And this thing does pretty well on both. It's very light and zero power consumption. And that thing is just the opposite. Miles O'Brien: And so there's a component of it perhaps trying to answer too many needs at once. And with all due respect to engineers, who I love dearly, they tend to want to answer that need. And sometimes, just sometimes, the simple solution is, in fact, the better one.
Greg Paulsen: Absolutely. Rolling back in that, which is how... This is an engineer, a team of engineers given that design, that is looking at this, thinking, "How can I...", "How can I fix this? How can I fix you?"
Greg Paulsen: And this goes into the next slide that I have here or the next question, which is just the everyday impact. Right? So the "why." Right? The "why" and the mission when we're talking about enablement devices. But would you see that, I used this phrase the other day, of that ableist undertone?
Miles O'Brien: Yeah.
Greg Paulsen: [inaudible 00:09:58] and just talk about these everyday things that seem standard but can be very tough.
Miles O'Brien: Yeah. So I think people see somebody like me with a missing limb, they want it fixed. They just want to get it fixed and make you look normal and whole, and just replace what you lost.
Miles O'Brien: This is an amazing piece of engineering here, this thing that nature has given us. And it's not so easy to replicate it, as we have learned. We're way, way, way far ahead on lower-limb prosthetics, a couple of reasons for that. First of all, there's like... I think it's about a seven or eight or maybe even close to a 10- to-1 ratio of lower-limb amputees versus upper-limb.
Miles O'Brien: Number two, the leg-foot-knee has a very specific kind of just one purpose, locomotion. And this thing does amazing things. And it's very difficult to come up with an engineering solution.
Miles O'Brien: And so I think what happens is, with that ableist undertone, [inaudible 00:10:59] the engineer thinks, "Well, how can I do this and make that?" When, in fact, that's a tough challenge. We're a long way from it. It's certainly a goal worth pursuing.
Miles O'Brien: But in the meantime, we tend to overlook the fact that this hook is pretty good. And there's a whole array of other gadgets that you can deploy to get through your life in a meaningful way and a very fulfilled way. You just have to get out of that idea that you're going to replace this. What you need are some tools in the toolbox, as I have in front of me here.
Greg Paulsen: Yeah. And that leads in, and actually, I was going to say, Amin and Jed, for this question here, beyond a prosthesis... So I think that's a lot of what you've seen and how your world has started. But what have you seen from when you talked to your clients and your community and just observations that you have made?
Jed Tango: Yeah. I'll take this. Yeah. Miles put it so clearly, of the issues with these cool robotic hands. And that's the reason why we started. We were like, "Oh, there's all these cool things online."
Jed Tango: We did more research. It's not accessible to people. And there was a lot of 3D-printed ones that were like actual robotic hands, but that's not even close to feasible. So we were like, okay, what if we just design and make other things that were easy to print on the simple FDM printer, and leverage the design of the part to help with everyday tasks?
Jed Tango: And that was what we were really focused on because it's what we're talking about, [inaudible 00:12:39] these tools or stuff that we could use.
Amin Hasani: Yeah. And at the beginning, it was very simple that we wanted to just accomplish one task, fix one thing, and then see how it goes from there. And we decided to design something that looked subtle, nothing that stands out. And we decided to design a watch-looking strap. Amin Hasani: So at the beginning, we designed a fork holder or anything that has a round handle, that would have something flexible, a 3D-printed flexible part. A very simple grip that design was. And at the bottom, it had a little strap. It looked like a watch, but you could easily slide flatware and pen and pencil.
Amin Hasani: And after that, we realized we're onto something. It's a different direction. And Jed is holding one of our latest designs. Jed Tango: Yeah. So to show, this is like a watch. And I could put it on my watchband here. And then if you push down on it, it clicks it in. And this is kind of like a simple thing that we're talking about where it's like, this is a simple solution to hold this. This is super cheap to
Amin Hasani: We had a little rotation. We made it even simpler at some point that it's just one little piece that prints in five minutes, costs probably five to 10 cents. And it goes on any bracelet, watchband, and you could have a pen just sticking in it, really easy. Amin Hasani: And the idea was that if this is already on your watch, with one simple movement, it could grab anything round like a brush or a pen off of a flat table. So you wouldn't need any outside help.
Miles O'Brien: Cool.
Greg Paulsen: That's really cool. I was going to say, when you were talking earlier [inaudible 00:14:39]. I'm eyeing Miles' table right now, by the way, [inaudible 00:14:43].
Greg Paulsen: Some of the things, you're right, it's beyond the prosthesis. There's just enablement devices that you have. And actually, if you want to show through some of your favorites and also talk about a story, how'd you discover this? You sent me the Amazon list of this is the cool stuff. How'd you get to that Amazon list of items and what was your discovery process all the way?
Miles O'Brien: Well, what I discovered is that if you try to... It's kind of like telling the engineer to replace the hand. If you tell a person that you have one arm and you have to figure out how to relive your life, it's too big a problem. Right? And it's kind of overwhelming.
Miles O'Brien: And so after I realized that that was a bad course to go on, I started doing it one problem at a time. And one of the first ones I had to deal with was, well, first of all, how do you wash your back in the shower? So I got one of these things, and I lean against the wall and scrub that way. That was a good little revelation. Got a little hand grippy thing too, which is kind of nice, kind of a scrubby thing.
Miles O'Brien: But the other thing was, how do you do breakfast? Right? Bagel cutter, that was a good thing. That's a very one-arm-friendly kind of thing. And I remember very distinctly going through day by day, figuring out how to scrub up. How do you do a pepper grinder with one hand? You get a battery-operated one.
Miles O'Brien: It's not typically designed for ADL, but it works. How do you cut your meat? You could have that fancy, modular, prosthetic limb or you could get one of these, one of these rocker knives that you just... Or a mezzaluna, as some people call them.
Miles O'Brien: Then this stuff is amazing, it's called Dycem. You see that blue thing in the middle? It's sticky stuff. So this is my opportunity to open my bottle of wine here, because it is that time here where I am. So you got to get the electric bottle opener, but you want to put it on the Dycem because it sticks. This is the problem, you have to hold things in place. Right? Greg Paulsen: Always about counterpressure, right? [inaudible 00:17:03] challenges are just counterpressure.
Miles O'Brien: Yes, exactly. So look at that. If I just push down on it, the bottle won't spin. So if I had my prosthetic on, I could have managed it with that. But if I didn't, what would I do? And that would be a terrible travesty.
Miles O'Brien: So opening a bottle of wine was another one, that was one of my earlier ones. That might have been before the bagel, actually. Then there's things like elastic shoelaces. I think you can see those. Right? Little zipper pull things.
Miles O'Brien: This is a really cool thing. This is called a knork. And if you see, it has kind of a curved side to it, which allows you to cut, not steaks, but it allows you a cutting motion. Knife and fork, knork.
Miles O'Brien: And then with all due respect to your nail clipper thing, I found this little electric thing, which is pretty cool. It works pretty well. And I can hold it down with my toes if I have to and just put my nails in there. So that's just a few of the things. Miles O'Brien: And I do remember though, all of this takes a lot of time and attention. I felt like I was thrust at being a one-armed MacGyver. And at the end of the day, I was just exhausted. Just because all of this ram space that you don't even think about for all these things you do subconsciously, suddenly, I was thinking about how am I going to trim my nails? Or whatever the case may be.
Miles O'Brien: And then I remember one morning, it actually was bagels. I was sitting out of my balcony in Washington and I was just sitting there reading the morning news, and I was munching on a bagel. And it occurred to me that I just had done that whole thing subconsciously, just like I had done when I had two hands. That was such a great moment.
Miles O'Brien: And I realized that if I just go step by step through all these things, I'll get to that point where it is subconscious. And I'm there. I will say this though, one of the things... It does take longer. Things take longer. And you have to build a little more...
Miles O'Brien: I get up a little earlier than I used to. I take a little more time to get dressed. But other than that accommodation, I don't, I don't have to think about it as much.
Miles O'Brien: So it just proves we're all very adaptable, obviously. But you have to go into it with a mindset of not assuming somebody's going to make you this beautiful, fantastic arm that can curl 50 pounds, but figuring out your assortment of tools that are going to get you through the day.
Miles O'Brien: And, with the help of smart people like you guys, to come up with clever ideas that just make those little things work. Suddenly, you've got an array of things that make the whole thing really pretty much like it was before.
Miles O'Brien: It's obviously different. I don't call it a disability. I call it more an inconvenience. But there are tools out there if you're willing to think outside your able box, that ableist undertone. And focus on where you are right now. Don't focus on what you lost, but focus on what you have, and that's the key.
Greg Paulsen: That's great. And I think that's actually a really, really great segue. We talked about Blue Heart Hero and sharing your story because you're right, it's not the prosthesis, it's looking at, I would say... I don't even want to call them simple solutions. But it's stuff that when you use it, you're like, "Oh, wow."
Greg Paulsen: Even as you [inaudible 00:20:37] Miles, you have the bagel cutter. I've seen that bagel cutter for decades and didn't even think about, yes, it is a single-hand device.
Miles O'Brien: Yeah. Yeah.
Greg Paulsen: So yeah. Amin, tell us about Blue Heart Hero.
Amin Hasani: Yeah. A few years ago, Jed and I were working on this project with our mutual friend, which was a 3Dprinted jig that would go on a partial limb. And it had a fork all the way at the end, but the fork was way too far and it wouldn't really work in a sense. Amin Hasani: The idea was there and we realized potential that this direction has 3D printing. And it was actually the first time I was introduced to 3D printing. So I remember we set up a 3D printer. It was a party and we were in a back room working on this printer. And around 3:00, 4:00 AM, we finished the installation, we 3D-printed a little ring.
Amin Hasani: And I'm telling Jed, "Hey, there must be a website full of great ideas that make the world more accessible and easy." And we looked it up all night, nothing came up. And we decided to jump on it. And if nobody else did it, we know how to make this, we are designers.
Amin Hasani: And we got together and started Blue Heart Hero. We designed a number of different solutions; some of them worked, some of them didn't. One of the designs was a little competition that me and Jed had. And we decided to make nail clippers easy to work with.
Amin Hasani: So we both did some designs, and Jed's design won by the popular vote on our social media channel, which is this piece that I'm holding right here. And I'm going to take the nail clipper out so you could see the part. It has a little cut inside and just a simple base.
Amin Hasani: And going back to how is this anything better than what Miles has? We wanted to make sure people have access to everyday objects like this. Yes, granted, that design, the electric one, is beautiful, it's perfect. But let's say you're on a trip. You go to the pharmacy, grab one of these that you could find at any market, but you can't use it properly.
Amin Hasani: Something like this that is 3D-printable, you could print it in a few minutes. If you don't have access to 3D printers today, you could find a 3D printer in every block. You're going to find an engineer, a designer, or a company like Xometry that has all the resources to deliver the design to you in less than a few days.
Amin Hasani: And we thought if we could make this accessible to everyone through a low-cost solution, then we have accomplished something. We could apply that to different products.
Jed Tango: And to go down the list where the real mission [inaudible 00:23:27], it's like, we got this idea, we've got the clip. We're like, "Oh, wow. We could really network and use the internet." Jed Tango: And other people, like me and Amin, these designs, some of these designs like that nail-clipper jig, I think me and him, it took us less than an hour to design it. And we had a working prototype. And it was a few minutes for us to design something, but life-changing for someone else that actually needs to use that nail-clipper jig. And then on top of it too, it's like a cheap, simple print, and accessible for more people.
Jed Tango: So when we were working on this together, we realized if we get a website and we invite more people to participate, other engineers and other designers, we could really take advantage of the internet and what 3D printing is really for.
Jed Tango: And then while we were doing this, I think the next thing to talk really quick is we want to invite people, and the point of this [inaudible 00:24:16] too. And then people are listening that want to help out or participate. We have an ongoing design contest right now for kitchen accessibility. Miles is in his kitchen. Jed Tango: But going back a little bit to what's going on, we launched a design contest for Mia, she lives out in Long Island. She was born with a partial hand. Her family's part Native American, and so they have a long tradition of doing archery.
Jed Tango: So with that, we were like, "Oh. Maybe we could have a design contest." So we did. We were like, "Hey, who could think of an attachment or a jig for her to do archery?" That went around the internet. We had Brett in Australia actually send in a really good design, and we 3D-printed it out. Yeah. So yeah, we got the parts here.
Jed Tango: So this attachment was designed for Mia. And seeing the photo of the main testing that we did, she can now do archery with this 3D-printed part.
Greg Paulsen: Yeah. And I was going to say, what's cool about digital manufacturing, so 3D printing, it always had... I've been around long enough for us trying to figure out the buzzwords for 3D printing in the industry. We didn't call it 3D printing first. It made its name later on. Greg Paulsen: But we were trying to say, is this DDM, direct digital manufacturing, or rapid prototyping? A lot of these phrases were coming out. But I actually had a soft spot in my heart for that direct digital manufacturing.
Greg Paulsen: One of the things that people take for granted with additive manufacturing is the minimum thing you need to make a part is the file. In every other process, if you're traditionally machining a part, if you're injection molding, you have up-front tooling, you have up-front expenses, you have a lot of tribal knowledge.
Greg Paulsen: The machinists themselves are brilliant craftsmen that are actually working and figuring out tool approaches, jigs, work holdings, where a lot of that is digitized in a 3D printer, where it says, place the file [inaudible 00:26:26], orient the way you want, and go.
Greg Paulsen: So it also does open up to a wider audience, including if I have access to designing, I can actually now design for these naval devices. I can now make a little bit more impact and get something rapidly sourced. Greg Paulsen: We saw the same thing, by the way, around March to June 2020 with PPE response. Right? Designs everywhere coming out, but 3D printing was at the core there.
Greg Paulsen: I wanted to touch base on CURVD too because I think it is such a unique idea. Because sometimes when we talk about disabilities, there are very overt ones, there are also more subtle ones, or sometimes there's symmetry but there may be nerve damage or there may be mobility challenges.
Greg Paulsen: But tell me a little bit about CURVD and what was that inspiration? And how does that play a part with Blue Heart Hero?
Amin Hasani: Yeah. So at Blue Heart Hero, when we realized these designs need to be open source and available for free for 3D printer owners, people who want to make, and at different parts of the world. We do have some of these designs on our website at cost, which is the cost of 3D printing and shipping.
Amin Hasani: And at the end of the day, Blue Heart Hero is a not-for-profit company that we want to focus on providing solutions for open source, and giving people access to these designs at a low cost.
Amin Hasani: So while we were developing these ideas, we tackled another problem, which was drinkware. And while we're brainstorming on the ideas of different attachments, we're looking at these gift shop mugs, these ceramic white mugs that you find everywhere, that the simple handle, with a little tweak, we could enable a lot of other people to have access to this everyday product.
Amin Hasani: And if the tooling cost doesn't change, if the production cost doesn't change, shipping, and the overall look of it, it's a great idea to just launch a product from scratch, kind of like re-engineering this everyday product that fits more people, a wider audience. And that way, we are enabling more people to have access to the task of drinking beverages, et cetera.
Amin Hasani: So we designed the mug after many prototypes. We made a batch of, I think, 200 handmade mugs in Long Island, New York. That's the 3D-print version while we were developing the mug. We sent it to 200 people with and without disabilities, people who were collectors, which one of them is Jed's dad, who has been extremely helpful so far. Amin Hasani: And we connected with Lucky Fin Project, which they primarily support kids with a partial limb. And we had friends that had arthritis and Parkinson's. And the feedback that we received from people was incredible. Everyone loved the design, but the quality needed to match the common ceramic mugs in the market.
Amin Hasani: So after that, me and Jed, we saved a little money. We did a production of these mugs that he's holding. And after that, we realized we're onto something great, which Jed is not even using the handle. Greg Paulsen: I was going to say.
Amin Hasani: And after that, we started getting more buzz. And companies realized that they could use these for their marketing purposes for merch and employee gifts. And that way they could share their care for inclusivity. Amin Hasani: And for that, we realized this has to be its own company, a for-profit company that Jed and I redesign everyday products. And like Miles was showing us the scrubbing thing, we have ideas for a towel that he could use with one hand, and he could wipe his body just using one hand. That's coming next after the mug.
Amin Hasani: We have more ideas that we're working on. We get a lot of requests from women that they need underwear that they could put on with one hand. And when you think about it, there aren't that many solutions in the market that they could easily have access to.
Amin Hasani: Yes, we could have something unique, a unique design, something maybe medical-looking, but that is not our approach. We want an everyday product and at the same cost of the industry standard, and something that doesn't stand out. That's why our mug looks very familiar.
Greg Paulsen: Yeah. I was going to say, I think it's the normalizing of inclusive design, which I actually really enjoy that a lot. And you were showing some of this, but I do want to show one of your users in this video of just the usage of this.
Greg Paulsen: And you can imagine, in this case, it's being held, but it could be on a table. Again, it's all about keeping something still while applying leverage against it.
Amin Hasani: Yes. Greg Paulsen: And Miles, you were talking about putting cream cheese on a bagel. And I could just imagine the chase of going down that way.
Greg Paulsen: This is where the design concept comes in. So I wanted to just briefly talk about how we're related with Blue Heart Hero. Why are we having this webinar right now? First off, we're very passionate about inclusivity equity and using technology to its fullest.
Greg Paulsen: And we're in a unique situation because Xometry is the largest global manufacturing marketplace. And you talk about 3D print, we have eight unique additive manufacturing processes. And that's just part of over a dozen manufacturing processes. So even traditional molding, casting, machining, sheet cutting, all those services are inclusive with us.
Greg Paulsen: But with that, you have access not just to that desktop technology, right? Amin, you're holding the desktop prototype, and Jed has the SLS prototype, which is a higher-end of additive manufacturing, so yeah.
Greg Paulsen: Also, we can vapor-smooth now, which makes SLS just so much better too. And it gives that access. So not only are you able to work in prototype or lower-cost solutions, but we have tools like our instant quoting engine that you can go upload that 3D file and, very, very quickly, get pricing, lead times, and configure your part through.
Greg Paulsen: This is just a real quick demo, then we're going to get back to the questions, I swear. But Xometry's portal is really neat because it does give access to all these technologies. You're not buying the machines. You're essentially renting the space or renting utilization. Greg Paulsen: You see prices and lead times right away. We're connected with over 10,000 manufacturers. So you can see here, this is Mia's brace being uploaded. You can see pricing and SLS, which is priced here as an additive manufacturer product.
Greg Paulsen: But you can very quickly go review this item, select different manufacturing processes. So you can see all these different additive processes plus your traditional processes available.
Greg Paulsen: In this case, let's go and bring this into... I'm doing product development, right? I want to go lower-cost. So I'm moving to an FDM process. We actually do have an FFF platform. And you can go and select your colors and just press Order, and you get your parts in a few days.
Greg Paulsen: So you don't even need the printer. The printer helps because you could get the files, but it just gives you access as well.
Amin Hasani: And Greg, I want to mention something here real quick. Well, we talked about having all of our designs available to people for a quick purchase and 3D printed by you guys. So we're already going to recommend the material, offer the colors that are available.
Amin Hasani: But while I was trying to get the minimum cost to produce some of these parts, I realized, while I know the 3D-printing process and all the lists that you put there, for someone who is not familiar with 3D printing, it's a big problem, a bit of a headache.
Amin Hasani: But when I uploaded the file, the recommendation was spot-on. And the pricing and everything, I didn't need to go back and change the process or the material. It was very interesting. With the shape of the geometry, the software, it recognized the best and lowest-cost 3D-printing methods.
Greg Paulsen: That's really cool because we use AI and machine learning as part of our technology platform. And we've built so many parts that we can literally create a predictive model.
Greg Paulsen: It's almost like, you know how Netflix would give you that 97% match score? Similar to that, where, based on the geometry like yours, which has never existed in the world, we've never made it before, but as soon as you uploaded it, based on the geometry, parts that look like this are typically purchased in this process.
Greg Paulsen: So you can always configure later, but it does save you a click. And for those who are not familiar with the 14 different types of manufacturing technology, it definitely does help at least put you closer to the bullseye on that go.
Greg Paulsen: Before we get back to the questions, we have been talking about this design contest. This is a design contest with Blue Heart Hero and Xometry. It is kitchen enablement devices. Sky is the limit. Give Miles something else for his tabletop [inaudible 00:36:06]. Miles O'Brien: Yeah.
Greg Paulsen: And it's funny because he was showing this electrified bottle opener. And I actually was like, "I kind of wanted to make a bottle opener." So I may still submit for this contest. But this is open to everybody.
Greg Paulsen: So if you have a creative idea, some sort of enabling design, our platform will be 3D printing what we're looking for, for this particular contest. But you could read about... You could email your designs and submit to Blue Heart Heroes website, as well as there's more information on Xometry's site. And we'll be sharing that along with the recording of this.
Greg Paulsen: But I do want to encourage everybody to give it a try and just think about this. And this is actually a really great segue because the question is, how do I think like this? If I have a symmetrical function, what should I be thinking? What should my mental model be when I'm designing for accessibility? Jed, how did you approach this?
Jed Tango: So we had people work with us before on the project. And right now... Actually, it's funny. So one of our interns working with Blue Heart Hero, he's working for us, and a while ago, he actually broke his wrist. And he was in a cast.
Jed Tango: And he was like, "Yeah, it was really hard for me to do a lot of things. I struggled with things." And I was like, "Okay. Great. What were the things that you struggled with?" And I also realized that he's watching now too, so it's kind of funny that he knows I'm calling him out. Jed Tango: But it was good because it was something where it was a little eye-opening. When you lose something... Most people don't... We all have two hands. And it's like, we pick something up, we use the hands. But if you physically remove your hand and you try actually using your design with that one hand, it's a whole different ball game.
Jed Tango: And Miles, before how he was explaining when he was in the kitchen and he was like, I couldn't do this and couldn't do that and couldn't do that. Because most people that have two hands, we would never think, "Oh, what could be done?"
Jed Tango: So it's just thinking about it in a different way, understanding different forces [inaudible 00:38:20] that too. And there's an innate way to grab something or there's an innate way to do something like that. And so going through that trial and effort and just thinking about it in that one way gives you a huge leg up to how that part would work.
Amin Hasani: And also, the whole purpose of us starting this company is to bring communities together. We're actively working on a new website, which right now it's Live, but it's missing a lot of pieces.
Amin Hasani: We're going to have a lot of not-for-profits that are around disability coming together with the industrial designer communities and engineers. And both communities could communicate and talk about their needs and what engineers and designers need, like feedback.
Amin Hasani: We're having different design requests on our website that engineers and designers could pick those topics. And even schools, now we have Columbia and Cornell University interested to work with us. I think RISD, RIT.
Amin Hasani: And we're really excited because all the requests we have on our website are from the disabled community. And we could have students work on real problems for real people and task-based solutions, and one solution at a time that we have a library full of ideas that just makes the world more accessible.
Amin Hasani: And come to think of it, it's not just for people that are either missing a limb or have a hidden or visible disability. A lot of tasks, for me, it's hard. And I'm always like, "I'm sure with a 3D-print piece, I could make this easier." And I keep notes on these ideas.
Amin Hasani: And I know as we grow, we're obviously going after the disabled community because they're underrepresented, solutions are not everywhere. And with 3D printing, we could make an impact. But slowly, we could grow this into a bigger audience.
Greg Paulsen: And Miles, when you've spoken with medical advisors that you're working with, building a prosthetic, have you ever given them feedback? What considerations, what advice would you have for engineers working in this field?
Miles O'Brien: Listen, listen, listen. It's so good to hear you guys talk about actually speaking to the end-user because my sense of the prosthetics industry is that they tell you what to do.
Miles O'Brien: Here's a little example. They made me this. You see this electric... It's called a Griefer device. It's not charged up at the moment. The reason it's not charged up is I don't use it. And the reason I don't use it is I'm not allowed to adjust it myself. You have to take it into the prosthetist to have them put a gadget on it to change the grip strength or whatever I say.
Miles O'Brien: Why isn't that on my iPhone, for gosh sakes? And why haven't you asked me? Unfortunately, I found that out a little late in the game. I didn't realize. I just assumed I would be able to work with it. It's amazing how much...
Miles O'Brien: I mean, it's just like the arm that can curl a 50-pound dumbbell. Who really wanted that? I guess maybe somebody said that'd be a cool idea. But was that really on the list of things that a typical amputee really wanted? I doubt it. I doubt it.
Miles O'Brien: What I want, as I put it out here, I just want something to hold things in place. This thing can do 90-plus percent of everything really, and you just need a helper. Miles O'Brien: For example, one of the things that really trips me up if you want to come up with a good design, I still have trouble doing zippers, especially a coat that's elastic, trying to get the thing together, get the zipper cinched in, pull. Because you have to hold and pull, right?
Miles O'Brien: And if I don't have this on, I don't have an easy way of doing that. That can be a bit of a challenge. So I tend to shop around that. I'll get something with Velcro or whatever. But has anybody really ever sat down and tried to solve that problem for amputees? I challenge you guys right now to try that.
Miles O'Brien: But I do think, it's kind of amazing to me how little people actually really listen to what the needs are of people who are disabled. And maybe it goes back to that kind of ableist undertone. We know better. We're going to make you an arm that can do the heavy lifting and do all the 21 degrees of freedom.
Miles O'Brien: But really, that's not what we're asking for. That's really not it. We want some simple tools to get through the day like you guys are thinking about. And that is exactly the philosophy that I would go along with.
Miles O'Brien: I hear from recent amputees all the time, they always reach out to me, what do I do? Can I get my arm back? And I said, "I hate to say this, but you have to get over that. You're not getting your arm back. It's not going to happen, despite what you might see on TV." It may look really cool, but if you really look at what they're doing with it, they're opening and closing pretty much.
Miles O'Brien: So what is the mission? Stay focused on what the task is. Stay within the defined mission. And don't let the mission creep happen, which we all do. Right? You want to add... Well, we can just add one more thing, we'll just add... And then we'll just do just one more thing.
Miles O'Brien: And pretty soon, you've got a $200,000 thing that weighs 80 pounds and operates for an hour on a charge. And the minute you perspire, it starts going in circles.
Miles O'Brien: So you have to watch the complexity. There's a sweet spot between utility and complexity, and simplicity, and usability, and all those things. I would think, as an engineer, just being in that space would be interesting, trying to solve for that as opposed to just hanging ornaments on the Christmas tree.
Greg Paulsen: Oh, you're making me very introspective right now, so thank you. That's the point of this is like, how many dumb things have I said in my past [inaudible 00:44:21] I could solve someone's problem?
Greg Paulsen: And that goes down to these false notions where I think you talk about the scope creep like, "And it can also... And it can also..." And actually, I saw a comment earlier on the questions, so this is also [inaudible 00:44:35].
Greg Paulsen: As we're talking, any questions, please use the Question & Answer tab. We'll get to them very soon here. But somebody made a comment saying that their father, who's an amputee, also prefers the hook over other prosthetics. It's their utilitarian item. So it's just really interesting to think about that as well.
Greg Paulsen: But yeah, on this question, false notions about designing for accessibility, do you have any advice? I think you said some of this, but like, "Don't do this." What is that advice there? Miles O'Brien: You talking to me?
Greg Paulsen: Yeah. Yeah. Miles O'Brien: Yeah. Listen, I don't want to get too heavy with you guys, but I do think it's kind of cruel. Not purposely, but it is a bit cruel, because we do give people who are recently injured, a false hope that there is a replacement out there for me, right?
Miles O'Brien: They've seen the kid with the robot arm or whatever, and they think it's just going to be fine and they're going to attach this thing and off they go. I think that's not right. That is not right. We have to be honest with people about what can happen. And it's not that grim. It's just real.
Miles O'Brien: I'm a reporter. I always follow the money. If the arm costs $200,000, there's probably a reason they're pushing it, right? As opposed to this one which is $15,000, which, frankly, I'm not sure how that happens. How is that 15,000 bucks? I'm sure you guys could 3D-print this thing for a lot cheaper. And I would welcome that, as a matter of fact.
Miles O'Brien: But I do think that we have to be careful about raising false hopes among people who've gone through traumatizing injuries and making them feel like it's going to be okay. And it's just, I'm going to go.
Miles O'Brien: A lot of this, we're Americans, we look for silver-bullet solutions, right? We can just go and we can buy our way to being whole again, but that's not how it works.
Miles O'Brien: But it's okay to buy our way, one little gadget at a time, to being functional again. It's a slightly different philosophy, but it's more real. And it's still a hopeful philosophy, it's just not... Well, it's realistic.
Miles O'Brien: And so I want you all to keep that in mind as you design things for the disabled, that you are potentially giving people a lot of hope that their lives are going to be better. And if you can't deliver, that's not good.
Greg Paulsen: Absolutely. I think it's very, very well-said. On the note of 3D-printing prostheses, it is something that we definitely see an uptick in.
Greg Paulsen: There are certain materials that can be freeform printed, won't trigger sensitivity issues as far as skin sensitivity, irritability, those types of tests, and can actually behave like a firm elastomer. Or you can have stuff like a carbon-filled material that could behave extremely rigid. Greg Paulsen: And it does allow for, hopefully... Our goal, the 3D-printing overhead promise, to your point, is to help increase inclusivity, reduce costs. What usually happens though is you see the hype curve where the first time it happens, it's overpriced, and then eventually, it normalizes. And we're seeing that more and more in the additive industry as well.
Greg Paulsen: So I think as you go from castings, so forming castings, to digital modeling through scanning, all those things help decrease that barrier from what do you need to 3D print? A 3D file.
Greg Paulsen: Right now, everything around the prosthetics market is more about manual tasks because it has been craftsmanship for the longest time. And it's still digital craftsmanship, but now you're using a digital sculpting pen instead of the physical tools.
Greg Paulsen: This is actually really great to move into some Q&A. And please, as we're concluding today, feel free to continue to add some questions and we'll work through. I actually do have a question for Jed and Amin. What has been your greatest challenge, and conversely, your biggest success up to this point with Blue Heart Hero?
Amin Hasani: The challenge, I would say how people project their understanding of normal, and how we tried educating them about disability. And while we don't have a visible disability, but we couldn't really explain to people how we're trying to look at this problem differently because they would ask us, "Okay, did any of you have a partial limb?"
Amin Hasani: And we tried to explain that disability is not limited to a wheelchair and a prosthetic arm. There are many different types of... Actually, 15% of the population of the world has some sort of disability. And when you hear that number, it's kind of shocking. Amin Hasani: And I always explain to people that, how do you look at disability? Do you consider someone who's really tall, handsome, and athletic, a disabled person? And they say no. But when it comes to fitting into a small car, on a bike, or going through a standard-sized door, they're not able to accomplish that task easily. So are we considering them disabled?
Amin Hasani: And again, that's the part that people start thinking that, okay, it's task-based, it's around products, tasks, and services. And if you could fix those for a wider audience or more people, then less number of people are considered disabled by society. Amin Hasani: And the solution to this big problem is not just robotic limbs. And that was the biggest challenge so far. And for the success.
Jed Tango: Yeah. I'll take it. Xometry here is probably the best example of this is we're really utilizing this new technology of 3D printing. It's like, this idea would've been going nowhere if we didn't have a platform where... You know Xometry, where it's like you showed your website, you could upload a model, and you get 3D-printed out. It's a digital file that could be emailed across the world and be made somewhere else.
Jed Tango: And so our biggest success, I think, would be really leveraging on that. And 3D printing really came through on giving physical parts and jigs and attachments and objects to people that need them. And this is the part where it's like, we're going to move forward with that and really make some more parts that are 3D-printed and help more people out. Amin Hasani: Yeah. We had one design that someone from India lost both of his hands in an accident. And he said he can't grab a pen and pencil, and he's not used to not having two hands. And we sent him the 3D files and actually found him a 3D print shop in his neighborhood because he wasn't familiar with the technology.
Amin Hasani: He 3D-printed it, as he said, for the cost of a cup of coffee, the next day. And less than 48 hours, he wrote us a letter and emailed us a letter, which was very touching.
Miles O'Brien: That's awesome. That's a good story. Much respect to you guys. You guys do great work. Amin Hasani: Thank you, Miles.
Jed Tango: Thank you.
Miles O'Brien: Beautiful thing. It's a beautiful thing.
Amin Hasani: 8 And by the way, we already uploaded the zipper project on our website.
Jed Tango: Yeah.
Greg Paulsen: Live updating the website as we're going. Jed Tango: Yeah.
Miles O'Brien: It's got to be incredibly gratifying to get a response like that when you've made that kind of an impact in someone's life. That's what it's all about, right?
Amin Hasani: We have a video of Mia, the little girl from our first design contest. I was having a meeting with her parents and herself at a table in a diner in Long Island. And we gave her the nail clipper and the jig separately, and she was playing around with it.
Amin Hasani: And she's seven years old, she's full of energy. And she was born with a partial limb. So she is used to not having fingers on one hand. And forcing a prosthetic arm for her, it just doesn't make sense.
Amin Hasani: And not only... She needed surgery and meds, all of that aside, it wasn't really a solution for her. All she needed was to grab a pen and pencil with one hand or be able to accomplish tasks by herself.
Amin Hasani: Long story short, she starts playing with these two. She has no idea what these are. At some point, she realizes this goes in here and this lays flat. So she starts playing with it with her fully-developed hand. And then suddenly, she just screams like, "Oh my God!" She puts this down. She starts pushing it with her partial hand and trimming her nails for the very first time.
Amin Hasani: And she tells her mom, "Mommy, look, I'm doing it myself." And she didn't know how to do it, right? So she was going really fast. And her mom is like, "Oh, you have to take your time. Look at the profile of your nail." And she had this serious face. I grabbed the camera, I taped it. It's on our website and on our YouTube.
Amin Hasani: And she trims her nail, she looks at her fingers. And then it's not in the video, but after that, she tells me, "With this, I could draw with my hand." And then immediately she says, "Can I do archery?" And that was when we decided, okay, we have to launch a design contest so everyone knows she could accomplish tasks by herself with simple ideas.
Miles O'Brien: That's awesome. That's awesome. Greg Paulsen: That's amazing. And also, I think, as a dad too, I also know the stubbornness of a kid being like, "I can do it myself." And the excitement when they do is just... It's amazing. [inaudible 00:54:36] because it's like, yes, you can do that task now too. It's fantastic.
Amin Hasani: And by the way, a lot of people might ask why we 3D-printed this at home, in our apartment in Brooklyn, and we needed to come to Xometry for a higher-end 3D print.
Amin Hasani: Two reasons. One is this is the coarse print. And it breaks if you apply a lot of pressure. It is safe for just testing and making sure the dimensions, everything worked. But after that phase, for a functional part that's water-resistant, it could work for years. And there is no risk of breaking because this will be on her hand. Any mistake could cause serious damage. Amin Hasani: Now, Mia can practice with the 3D-print piece that Jed was holding, which you guys sent us. So this was just for testing. And after this, Xometry enabled us to give her a piece that actually worked for her.
Greg Paulsen: That's great. I have a couple of great questions here. Actually, one is more about this ideation, because you're talking about zippers, and the infamous putting on socks question.
Greg Paulsen: I know there's been some occupational therapy products out there, but is this something... Miles and Amin and Jed, has this been a common request as well from... Miles, from personal experience, is there technology there?
Miles O'Brien: Yeah. That's what I don't need a helper for. I can do that with one hand. I've got a technique figured out for doing that. I think, for people with other limited mobilities and, certainly, bilateral upper-body amputees would have a problem with that. So I haven't really thought about that one much. You guys probably have though.
Jed Tango: Yeah. It's funny that you said that, what you said. Most people, they found a technique that works. In clothing in general and things that you would interact with, zippers are a great example, we've heard that before too.
Jed Tango: And shoe-tying is another one, where it's like, those are really just difficult tasks. And it's like unless you go out of your way to buy around it or you get something else... I know socks and shoe putting on, there's already some accessibility stuff with the shoehorn and certain things like that where you could use that to put on the sock if you don't have the dexterity for it.
Jed Tango: That is a really good thing. And moving forward, we'll put that on our website too, we can do a clothing thing. Because there is a lot there, because of how much [inaudible 00:57:28] clothing there is and stuff like that too.
Miles O'Brien: I've had some shirts with magnetic buttons, which are kind of nice. I can do buttons with one hand, but it gets old. And so there are some that have... Tommy Hilfiger has a whole clothing collection which is aimed at people with disabilities, which I give them a lot of credit for.
Greg Paulsen: That's great.
Amin Hasani: Miles, actually, the company reached out to us for a possible collaboration at CURVD that we do products with their help. And the community that they have gives the best feedback. And yeah, we're really excited for that.
Greg Paulsen: That's awesome. I actually had a question on that. And we'll do two more questions. One of these is mine. How do you access your community? How did you get your original community? How did that grow?
Amin Hasani: For us, it was mostly just trying to distribute out. We don't have that much PR or marketing budget. So it's me and Jed trying to be ourselves, show the real work that we've done. And yeah, make phone calls, send emails. And out of 100 emails, two or three comes back, and those make a real impact.
Amin Hasani: Like Miles here, it was out of luck. We got lucky that we got in touch with him. And he really liked our work. And with Xometry as well, it was just one message on LinkedIn that we found you guys. Same as Lucky Fin, we reached out to Molly, the founder of Lucky Fin, showed her a few things that we've done in the past. And she was very interested to help us connect with their community.
Amin Hasani: But with the help of you guys and the webinar, the design contest, we're going to reach out to more communities, universities, industrial designer groups, and just expand.
Greg Paulsen: That's great.
Miles O'Brien: I would just interject here. I think this is better mousetrap stuff. You're building better mousetraps, the world will find you.
Greg Paulsen: That's great. Miles, I got a question for you, which is tying in with the Blue Heart Hero contest. Do you have any ideas for a 3D-printable assisted device that would help make kitchens more accessible?
Miles O'Brien: Let me see. What do you think about the kitchen? What do you think would be good in the kitchen? I'm looking at my girlfriend who does really all the cooking. Oh, yeah. No, no, no. Something that we don't have. A design thing that would be good.
Amin Hasani: [inaudible 00:59:53].
Miles O'Brien: Oh, yeah. She's really the cook. Everybody needs a [Suzy Tobias 01:00:00]. That's what you need. The [Suzytron 3000 01:00:04]. No, I'm trying to think. There's not a ton of things that I haven't solved, believe it or not. But I got to think about it. Is there someplace I can post this if I think about something when it hits me?
Greg Paulsen: We'll post it.
Amin Hasani: On our new platform. Miles O'Brien: All right. Yeah.
Amin Hasani: Yeah. [inaudible 01:00:23]. Miles O'Brien: I'm going to think about it. I will come up with a challenge. I realize I gave you zippers, and that's not kitchen stuff. But let me think about it.
Greg Paulsen: This is great.
Miles O'Brien: I should have been ready with this. I'm sorry. This was my opportunity and I blew it.
Jed Tango: [inaudible 01:00:35].
Greg Paulsen: Well, I really want to thank you all. We're right at time. And this has just been an amazing discussion about design. I think building that paradigm shift, just how to think about it. Miles, to your point, don't assume. Ask. Learn and listen.
Greg Paulsen: And just the additive [inaudible 01:01:01] you can do is really amazing. I'll run through, but any final words from you all before we go? Any final pieces of advice?
Miles O'Brien: I will say this. I think that 3D printing, additive designs like this offer a tremendous... I mean, there are precious few people like me, as Amin and Jed have found out. There aren't many upper-limb amputees out there.
Miles O'Brien: And so really, there's no economies of scale to build things for them. That's a lot of why lower-limb prosthetics are so much better. There's just a bigger market out there. And so the ability to do one-off designs like this and do one or two of them and it's okay, you don't have to order, go to an injectionmolding factory in China and order 50,000 as a start.
Miles O'Brien: Because that's pretty much everybody who is an upper-limb amputee in the US right there. So it is really a powerful tool, which I think it's been interesting watching this develop over time, and to combine great minds that are thinking like you are with these tools. I look forward to all kinds of new MacGyver tricks coming down the road.
Amin Hasani: Thank you. Jed Tango: Yeah. Thank you. Yeah. And you hit the head on the nail. Literally, the head on the nail. I know that's the best part
Amin Hasani: [inaudible 01:02:28].
Jed Tango: Yeah. With Xometry here too, it's like... And that's why we're working well together, us and Xometry, because we can make five parts or hundreds
Miles O'Brien: That's okay. It's okay to do that. Right?
Jed Tango: Yeah.
Miles O'Brien: I'll tell you one thing, it has nothing to do with kitchens, my next task is to get my pilot's license back. And I need a gadget that'll attach my prosthetic more effectively to the wheel of the airplane, so we can talk about that offline.
Amin Hasani: Yeah. 100%. Jed Tango: Yeah. That actually would be a fun project. Miles O'Brien: You talk about a small percentage of people who have that particular problem, one-arm pilots, but here I am. See? This is why 3D printing is awesome.
Greg Paulsen: [inaudible 01:03:07] population of one. It is so absolutely true there. Miles O'Brien: Right. Yeah.
Jed Tango: Yeah.
Greg Paulsen: Awesome. Well, again, thank you all for this wonderful event. I really appreciate it. Miles, you've been just tremendous with your experience and background, and again, tribal knowledge from the other side as a patient, as well as just your background in science and technology. It's really just pretty amazing.
Greg Paulsen: Amin and Jed, thank you so much. We're looking forward to seeing the designs coming through the design contest, and what else we'll come up with through Blue Heart Hero.
Greg Paulsen: 8 Please, I recommend everybody on this webinar give it a try, give it a thought. And even if there's an idea, you don't have access to CAD, reach out to us. Maybe you can find some solutions there too, because there's other people that want to get involved. So this is a community [inaudible 01:04:01] for sure.
Amin Hasani: And we're trying to post more about 3D modeling and 3D printing on our website, education for adults, for kids. Slowly, as we grow, we're going to help with that part as well.
Greg Paulsen: Great. All right. Thank you all. Have a wonderful evening. This has just been a wonderful conversation.
Miles O'Brien: Thank you. Amin Hasani: Thanks, everyone.
Miles O'Brien: Enjoyed it.
Jed Tango: Thank you.
Greg Paulsen: Cheers.