What is Direct Part Marking?
Direct part marking plays an important role in all manufacturing industries. By applying a mark on an item, a company can track it throughout its full life cycle and thus ensure transparency, quality, and accountability. A marking also serves to keep track of which parts are which and sometimes serves an aesthetic purpose. There are several methods of part marking, each with its own advantages; some of the most popular include laser marking, engraving, screen printing, ink stamping, and bagging and tagging. We’ll be covering what part marking is, why it’s important, its applications, and how these common methods of part marking work throughout this guide.
Direct Part Marking (DPM) is the process of placing unique identification markers directly onto a manufactured part’s surface. These markers, which can be code, symbols, text, dates, or serial numbers are known as direct part marks and they hold key information about the component they identify.
Direct part marks are considered a permanent marking since they are expected to endure as long as the component itself. In fact, this durability is one of the main advantages they have over stick-ons or other attachable labels; they are applied in such a way that they cannot be discarded, ripped, concealed, wiped off, or quickly deteriorate. They also can be applied to almost any surface, no matter the shape, size, and material. However, depending on these factors, together with the environment and the item’s function, different types of marks might be needed.
Occasionally, other types of part marking may be needed, such as putting tags or labels on a part. We will go into more detail about the different types of part marking in a later section.
Direct Part Marking Applications
There are countless applications of indirect and direct part marking within various industries, including the automotive, electrical, aerospace, and medical technology fields to name a few. DPM can be used to mark anything from a vehicle’s engine and printed circuit board to surgical tools and jewelry.
Direct part marking helps with managing recalls, improving product quality, eliminating manual data gathering methods, and empowering more sophisticated inventory management systems. DPMs are frequently utilized for the purpose of automatic part identification. The identification process is crucial for regulating, verifying and error-proofing different production methods, preventing product mix-ups, ensuring high quality standards are being met, and developing traceability. Moreover, part identification is used on flexible assembly lines in order to make sure that the right parts, which can be oftentimes indistinguishable, are used on the right production line.
Traceability Meaning
Traceability is a process that tracks parts throughout their entire lifecycle. The goal of traceability is to track the origins and destinations of a part from the acquisition of raw materials and parts to machining, assembly, distribution, and sales. Once the material is formed into a part, direct part marking provides “cradle-to-grave traceability,” i.e., it ensures traceability of all marked parts, even those that are subject to harsh environments, excessive handling, or reprocessing. From these markings, a company can find which suppliers the part comes from, and later find out whether the parts have been delivered to the right places. It also helps in tracking parts as they move throughout a single plant.
Some of traceability's benefits include:
- Product authenticity verification
- Protection against counterfeits
- Ability to determine product location for recall events and service requests
- Ability to always find a product’s location in the supply chain
As the standards, requirements, and demand for transparency in every segment of the supply chain are constantly growing, so is the importance and application of traceability across industries.
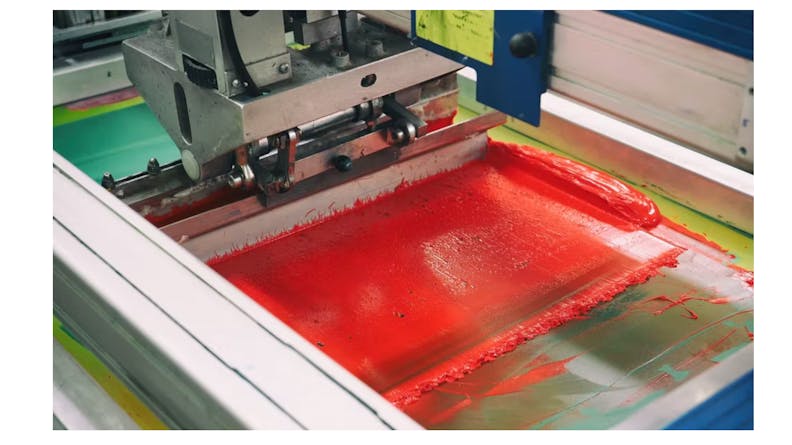
Some of the most major types of direct and indirect part marking include laser marking, engraving, screen printing, ink stamping, and part tagging (also known as bagging and tagging). Choosing the right marking method depends on numerous factors, such as the roughness and thickness of the surface and the part’s size, geometry, and function. In this part of the guide, we’ll provide more insight into each of the different types of part marking methods so you can select the right type for your particular use.
All of these services are available from Xometry. To ensure, however, that your markings are exactly to your specifications, when ordering from us please upload a 2D drawing in the Notes and Drawings tab showing the marking’s text, color, and location.
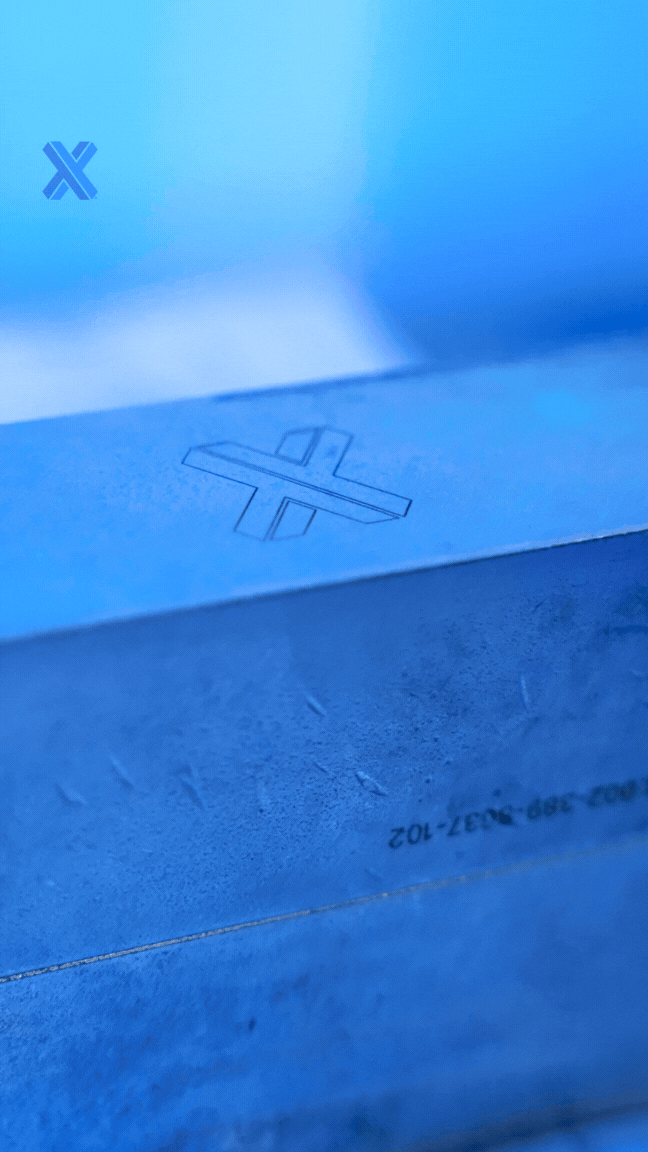
The Laser Marking Method
Laser marking changes the surface by using a low-powered beam, which moves slowly over the substrate surface with little to no penetration. This technique can generate linear and 2D codes, alphanumeric codes, and optical characters on a wide range of surfaces. The final marking effect largely depends on the marking head, lens, and wavelength specified. Different laser marking methods include ablation, engraving, foaming, and etching. Depending on the material, the process can also employ different lasers, from a fiber laser to a CO2 laser.
Apart from being highly precise, laser machines have extremely high processing rates, which translates to boosted throughput and efficiency in high-volume production scenarios. In fact, some marking processes may need only 1-3 seconds. Moreover, laser marking can aid in the reduction of operational and other costs, since they don’t use consumable parts. All of these factors can contribute to lower service costs. On the other hand, though, this method has limited movement – it can operate only on a two-dimensional plane. Because of this, lasers might have trouble processing materials with high hardness or a low ignition point.
Laser marking is best kept to flat surfaces, but Xometry can also mark larger round parts (with > 4” radius of curvature). Laser marking also works with anodized parts, yielding a crisp, clean text when done correctly. If you’d like to order laser marked parts from Xometry, please provide font and character height (range) for this marking. If none is provided, font and size will be performed according to best shop practice. You can also attach a DXF file for the marking if you so desire by including it in the PDF field of the quoting page. If you’re interested in rotary laser marking specifically, please send a quote request to support@xometry.com.
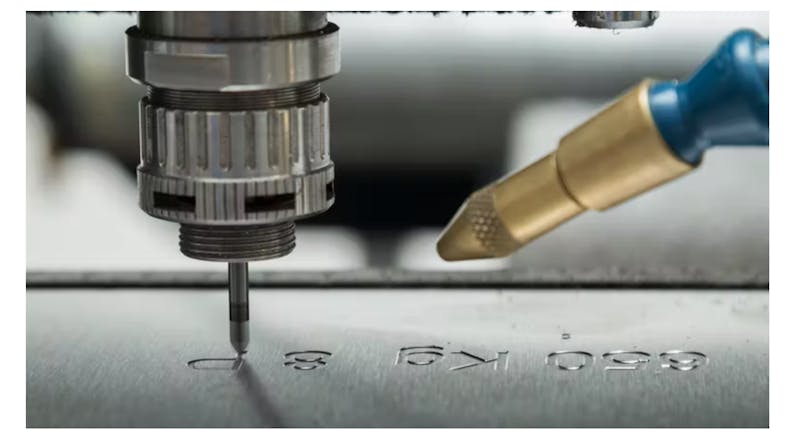
Machine engraving a metal part.
Source: szelltib/Shutterstock
Engraving Marking
Engraving uses a laser beam or machine tooling to physically remove materials from the substrate surface. This creates a cavity on the substrate surface which is noticeable to the eye and the touch. Laser engraving marking technique places information on the surface of a part or component by penetrating below its surface. CNC (Computer Numerical Control) engraving uses computer-controlled equipment that employs milling routes created by CAD-CAM software. It improves speed and reduces the number of errors as compared to manual engraving machines.
Since engraved marks are extremely durable, they are the preferred choice for items that would experience high wear. By repeating passes, 3D designs and deep engravings can be achieved. Laser engraving is suitable for many materials, such as wood, glass, textiles, paper, plastic, and metals such as aluminum. A mechanical engraving’s advantage, on the other hand, is its price – it is relatively low-cost compared to other marking methods. However, it can be difficult to process small details with the mechanical engraving technique.
Lasers can be used for marking in terms of both engraving and etching, so the terms and applications of these processes are often confused. The key difference is that engraving removes material, while etching raises parts of the surface to create the desired code or design. Both are types of laser marking. You can learn more about laser marking vs. laser engraving vs. laser etching in our article on the subject.
Machine engraving is the cheapest and easiest way to get part marking at Xometry. It is also preferred by most CNC machine shops as it can be easily implemented during the machining process, is low risk, and reduces reliance on 3rd party part marking vendors. This method works for both flat and round surfaces. However, no matter the surface, please try to model at least .030” deep for your engraving. Xometry will also need to apply a radius to any sharp internals featured in the text.
Machined engravings can also be backfilled with ink to increase contrast or for aesthetic purposes. In the case of backfilling an engraving, it is especially important to maintain a minimum depth of at least 0.030” to facilitate the filling. If the engraving depth is not specified, we will complete the engraving to this depth and proceed to backfill. Please be aware that this procedure may result in increased lead times due to ink curing times.
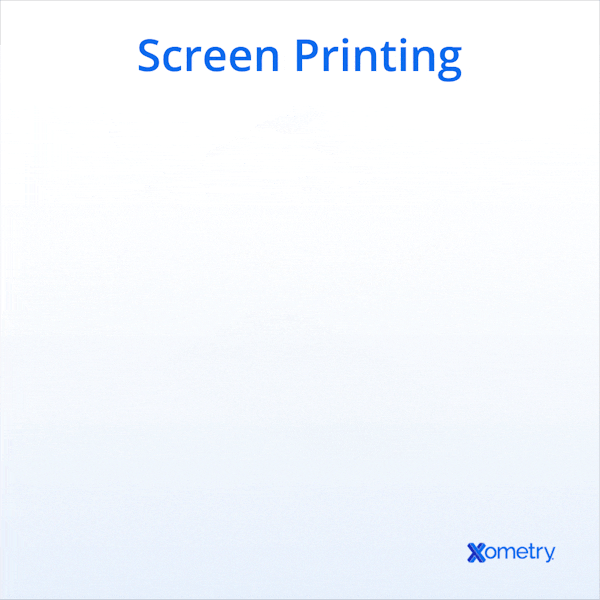
Screen Printing Plastic and Other Materials
This part marking technique is also known as silk-screen printing. The screen printing method uses a mesh to transfer ink onto a substrate and a stencil to block ink, as needed, to print the desired text or image onto the substrate. The ink is then dried under high-powered UV light, achieving a durable and highly resistant print. Apart from plastic, silk-screening is used on a variety of other materials, such as metal, wood, glass, and textiles. In fact, this versatility is a huge benefit of the silk-screen printing technique. Moreover, the marking is steam and water-resistant and it will not tear, fade, or peel off. If you have a small number of items, however, this might not be the best choice since it can be costly and impractical in such scenarios.
Silk screening is best achieved on open, flat surfaces since it requires the area to be accessible to a frame that will support the screen in the process. Any screen printing project to be handled by Xometry should be accompanied by a DXF file to ensure a precise and properly sized screen is made. For this purpose, you should also attach a DXF file to the same location on the quoting site as PDFs.
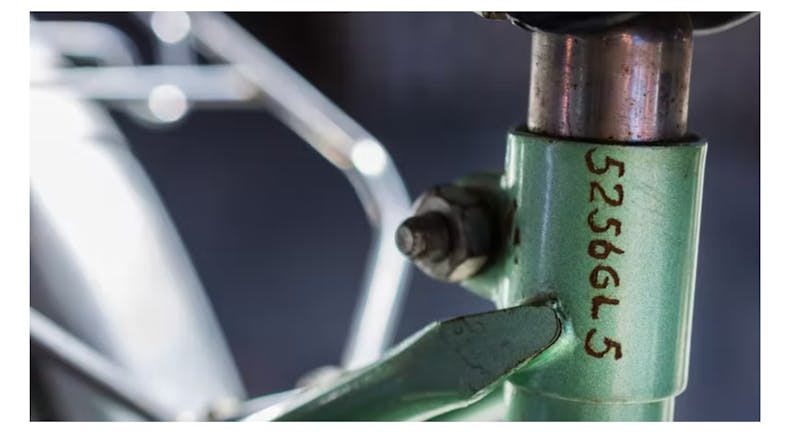
Ink stamping on metal.
Source: alberto gardin/Shutterstock
Ink Stamping on Metal and Other Materials
Ink stamping applies ink characters by any method that doesn’t damage the surface of the part. If the part is coated, clear lacquer or topcoat may be applied to the part marking. Ink stamping can be applied by rubber stamping or silk screen methods.
Ink stamping has a bit more flexibility in comparison to silk screening because it can be placed anywhere the stamp can access. However, this comes at the cost of precision. Unlike laser engraving or machine engraving, ink stamping does not introduce a risk for corrosion since material is not removed from the surface. It is also a great method for high-contrast applications.
Like laser marking, this technique is most suitable for flat surfaces and surfaces whose radius of curvature is larger than 4”. If ink stamping is not necessary, however, we usually advise choosing machine engraving or laser marking instead. Ink stamping is a purely functional process and should not be utilized for cosmetic markings (as described below); please prioritize legibility in your design to ensure the end result has clear, readable marks.
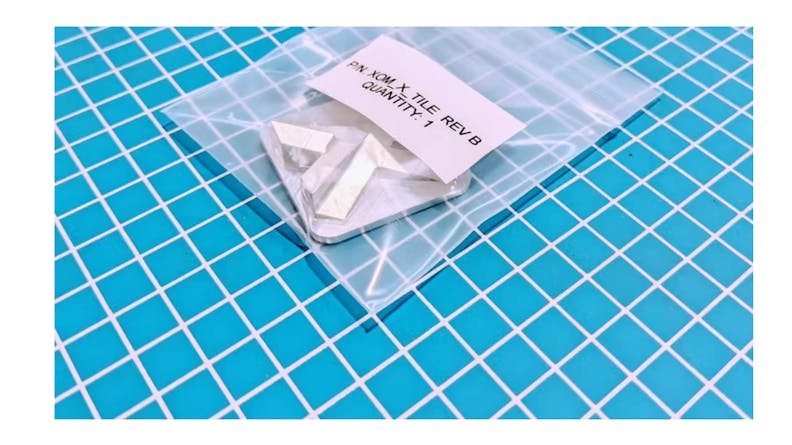
A product with a part identification tag.
Part Identification Tags
If the marking cannot be done directly on an object because of its size, the risk of destroying it, or other factors, you can use part identification tags, also known as the bag and tag method. This technique applies a tag to the part’s bag or container with the required identification information.
The main advantage of the bagging and tagging method is that it is very simple and it doesn’t cause any damage to the item itself. However, once the packaging material is removed, the part’s marking is lost, which is a considerable downside if identification is later needed.
In a Xometry bag and tag order, if parts are high-quantity, they may be grouped as long as they are not allowed to contact one another in shipment. In the case of grouped parts, an additional line will be added to the tag calling out the quantity explicitly. If the quantity exceeds 10, the parts may be bundled and tagged.
Ordering Part Marking with Xometry
Are you in need of part marking? You can get your quote in seconds with Xometry. We've included our guidelines around each process above to ensure your order is exactly to your requirements. However, we've got some additional information below on the types of markings we perform and what we'll do in case of missing information to ensure your order gets to you on time while remaining to your specifications.
Materials That Can Be Marked at Xometry
Xometry can mark parts in a wide range of materials, including metals, plastics, composites, rubber, woods, and foams. Some of our most popular materials include:
- Steel, including hot and cold rolled, annealed, hardened, blue tempered, zinc galvanized, and pickled and oiled steel
- Stainless steel, include spring tempered, brushed, hardened, and annealed varieties
- Copper, including annealed copper
- Bronze and brass, including bearing bronze and spring silicon bronze
- Aluminum, including pre-anodized aluminum
- Titanium, including Grade 2 and Grade 5
- Nickel, including annealed nickel
- Plastics, including ABS, acrylic, acetal, HDPE, nylon, polycarbonate, polypropylene, PETG, PTFE, and UHMW-PE
- Composites such as carbon fiber and Garolite
- Rubber and gasketing materials, including nitrile, cork-nitrile blend, paper fiber-nitrile blend, EPDM, and silicone rubber, as well as PTFE
- Wood, including cherry, poplar, and red oak hardwoods as well as birch, hardboard, plywood, and MDF
- Foam, including EVA, polyurethane, silicone, flame retardant, and high temperature varieties
In addition to marking, most of these materials can have other finishing options applied such as bead blasting, anodizing (both type II and III), powder filming, chem filming, painting, and other custom finishes.
Part Marking Design Best Practices
Ready to order your part markings? Here are some helpful guidelines to ensure they come out exactly the way you want them:
General Marking Best Practices
- Remember to scale your design to the finished size. If it’s not properly to scale, it can cause problems with the final marking’s proportions or size.
- Make sure you clearly annotate the information that will go into the marking (such as part number and revision level).
- Please also clearly annotate the location where the marking is to be applied in your drawing. You should use note flags and bounding boxes to show the marking location to ensure your vision is clearly laid out for the manufacturer.
- Don’t forget to specify your character size requirements, to ensure characters don’t end up too small or large for your application.
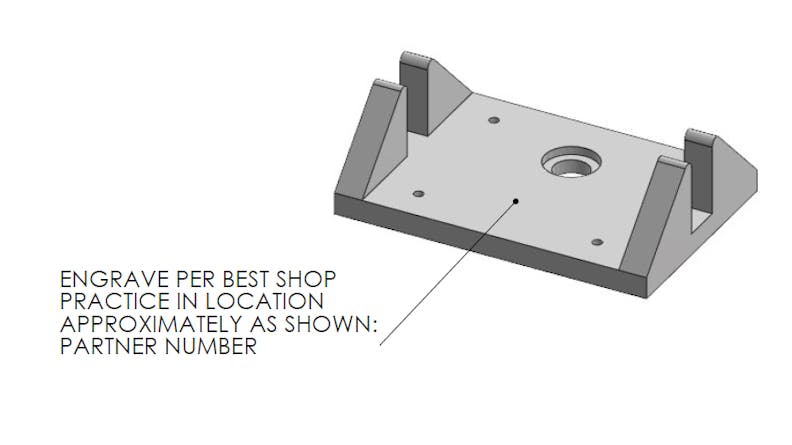
An example of how to show part marking placement when submitting a quote.
Machine Engraving and Laser Marking
- Remember to specify how deep your marking should be.
- For machine engravings with logos or special text, please include a 3D CAD file with the engraving.
- Aim for shallower engravings or etchings for medical part markings; deeper cuts can trap more airborne germs, as well as being abrasive to gloves.
- For laser marking, please provide all artwork in the form of vector files (such as a DXF) for logos.
Silk Screen Printing
- For markings with special font or logos, please provide artwork files in the form of a vector file such as a DXF. You can learn more about quoting with DXFs in our help article through the link.
- Avoid CMYK colors (colors that are the exact same cyan, magenta, yellow, or black as the ink). This can result in two problems: either that part of the design won’t be printed out, or the printer will output an extra unnecessary color and cost more in the final print.
- Please ensure that you specify the colors you need as well as the dimensions of the marking location.
- Remember that the more colors you use, the more expensive the final print will be.
- Keep in mind how the ink color will look against the part- dark ink on a dark material won’t be easy to read.
Functional Vs Cosmetic Markings
At Xometry, part markings come in two general forms: functional and cosmetic. It’s important to keep the differences between these markings in mind when ordering.
Functional marks have the exclusive purpose of conveying specific part information, like part number, rev, port indicators, and axis identifiers.
Cosmetic marking, on the other hand, calls for specific graphic needs to be met. The cosmetic marks may be logos or other designs which have to have certain aesthetics, so they need to be visually flawless. If this is the marking you need, please state so clearly in the “Notes” section, or on the print itself. In case of any questions regarding Visual Acceptance Criteria (VAC), Xometry will contact you prior to quoting or production in order to clarify the expectations.
Part Marking Rework
Xometry’s policies also differ for functional and cosmetic marking orders with missing or conflicting information:
Missing Location Information
Functional Markings: We will mark the part (set) in a uniform manner in the requested method, with the location selected per best shop practice. Xometry will refrain from selecting faces that are 32Ra or tighter when possible.
Cosmetic Markings: We will place the project ON HOLD, extending lead time as required until we can get the required locating information.
Missing/Incorrect Contents
Functional Markings: If we make a mistake on a functional marking that cannot be removed, we will strike through the marking (preventing complete obliteration) and redo the corrected marking in the same method adjacent to the first marking.
Cosmetic Markings: If we make a mistake on a cosmetic marking, we will reach out with detailed images to discuss acceptance or rejection on a case-by-case basis.
Method Deviations
Functional Markings: If we cannot mark the part in the selected method due to a process constraint, we will reach out to confirm an acceptable alternative. If the prints supplied specify multiple marking methods, we will proceed to the next method allowable per print. If we cannot mark the part in the selected method due to size constraints (tiny parts and huge parts), we will either Bag and Tag or Wire Tag accordingly.
Cosmetic Markings: We will place the project on hold, extending lead time as required until resolution.
Note on Proprietary Methods: If the prints provided reference a part-marking specification that is not supplied, we will proceed with Xometry standards superseding. If the additional part-marking specification is included, we will review and adhere, reaching out if we have any questions.
Conclusion
Part marking will place a distinctive identification mark onto a manufactured part, aiding its traceability throughout the production process and supply chain. In the case of direct part markings like ink stamping or engraving, this information will remain for the lifetime of the part. We offer both functional and cosmetic markings for your needs. If you’re in need of part marking, whether for high volume production or prototypes, you can get your quote in seconds with Xometry today. Our partner network has the ideal shop and machines for your job.
Special thanks to contributor Gracija Nikolovska for writing this article.
Disclaimer
The content appearing on this webpage is for informational purposes only. Xometry makes no representation or warranty of any kind, be it expressed or implied, as to the accuracy, completeness, or validity of the information. Any performance parameters, geometric tolerances, specific design features, quality and types of materials, or processes should not be inferred to represent what will be delivered by third-party suppliers or manufacturers through Xometry’s network. Buyers seeking quotes for parts are responsible for defining the specific requirements for those parts. Please refer to our terms and conditions for more information.
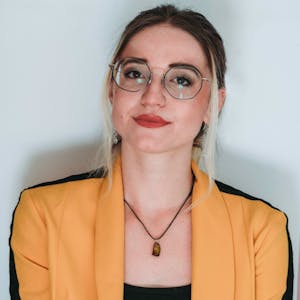