Centrifugal casting stands as a unique and versatile casting technique. It has demonstrated its cost-effectiveness in producing complex shapes with reduced machining needs and lowered manufacturing expenses when contrasted with forgings and fabrications (e.g. stamping). Centrifugal castings are used for components such as bushings, rings, engine cylinder liners, large pipes, and many more.
This article will discuss the process of centrifugal casting, shedding light on its advantages, disadvantages, and its wide array of applications.
What Is Centrifugal Casting?
Centrifugal casting is a manufacturing process used to create cylindrical components with a central axis of rotation. This technique involves rotating a mold around a central axis at speeds typically ranging from 300 to 3000 rpm while pouring molten material into the mold. The centrifugal force generated by the rotation spreads the molten material against the inner surface of the mold, resulting in the desired shape of the finished product. This method is often employed for producing large pipes, cylinder liners, and hollow cylindrical components cast from a variety of materials, including: metals, concrete, and glass. While centrifugal casting maintains tight dimensional tolerances on the outer surface, the inner diameter is typically cast slightly undersized, allowing for subsequent machining to achieve the precise inner diameter required.
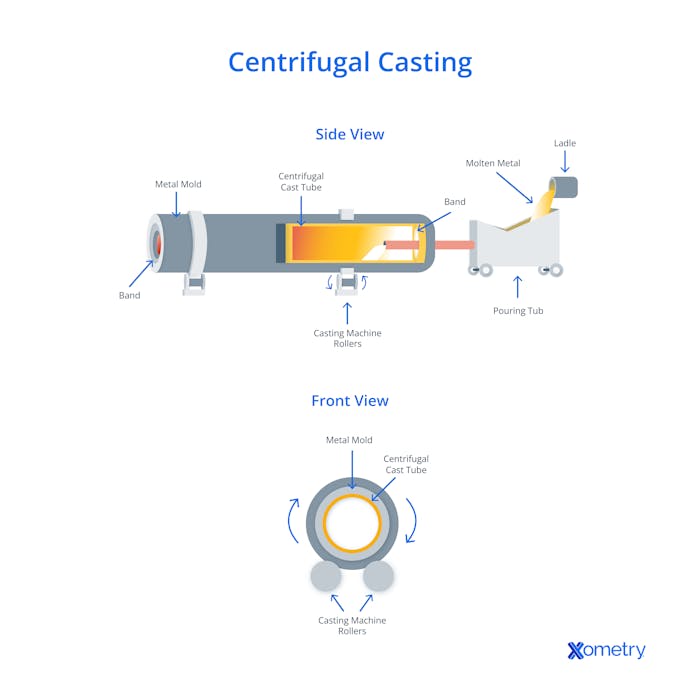
Schematic of the centrifugal casting process
What Is the Origin of Centrifugal Casting?
The initial patent for centrifugal casting was granted to Anthony Ekhardt, an Englishman, in 1809. Within a few years, additional patents were issued in Germany and America. However, progress in perfecting the technique remained slow and inconsistent for more than a century. A significant turning point in the method's evolution took place in the aftermath of World War I, particularly in the casting of pipes. During this period, centrifugal casting of pipes became a viable and competitive manufacturing approach.
Before the widespread adoption of centrifugal casting for pipes, pipes were typically made using labor-intensive methods such as: wrought iron or steel welding, clay shaping and firing, wooden stave construction, and cast iron casting. These methods had limitations in terms of seam strength, corrosion resistance, and size and shape variability. Centrifugal casting became competitive with these traditional methods in the early 20th century. This marked a significant advancement in pipe manufacturing.
What Is Another Term for Centrifugal Casting?
Variations and specific applications within the centrifugal casting method have led to the use of other terms such as "spin casting" and "rotocasting." "Spin casting" is often applied to describe specific adaptations of centrifugal casting, particularly those involving rubber molds or processes geared toward specific industries like jewelry making. "Rotocasting" may refer to variations of centrifugal casting used in certain applications, but it is less commonly encountered in general casting terminology. These terms are used to specify certain subtypes or adaptations of the centrifugal casting process.
What Is the Importance of Centrifugal Casting in Manufacturing?
Centrifugal casting is important for its ability to yield components characterized by high material integrity and soundness. The centrifugal forces that distribute the molten metal to the walls of the mold achieve a uniform material distribution around the circumference of the part. It also reduces porosity, which improves the mechanical properties of the resulting casting.
An essential aspect that sets centrifugal casting apart is its specific focus on producing rotationally symmetric stock materials in standard sizes. Centrifugal casting primarily produces components that are further refined through machining. This approach not only minimizes material waste but also streamlines production cycles and contributes to cost efficiency.
How Does Centrifugal Casting Work?
Centrifugal casting works by introducing molten metal into a heated rotating mold. The mold's rotation can be either vertically or horizontally aligned, depending on the desired configuration of the final part. Centrifugal (or, more accurately, centripetal) force due to the rapid rotation of the mold distributes the molten metal onto the walls of the mold at pressures that can reach nearly 100 times the force of gravity. The controlled solidification advances from the outer diameter toward the bore. During controlled solidification, the denser components, with greater momentum, move towards the wall, displacing less dense elements and impurities. Additionally, the rapid rotation prevents the less dense components from being flung as far outward, resulting in their concentration towards the inner diameter. After the casting has solidified, the part is extracted from the mold. Any remaining impurities within the inner diameter are then machined away. This results in a nearly flawless structure without cavities, defects, or gas and shrinkage porosity.
What Makes Centrifugal Casting Stand Out Among All Types of Casting?
Centrifugal casting's uniquely valuable features include the production of fully dense castings with good mechanical properties; the ability to process parts ranging from the small to the very large; the range of materials that can be cast, including not just most metals, but also concrete, ceramics and glass; and the ability to cast one layer of material inside another (for example, concrete-lined cast iron pipe). Unlike most casting methods, which rely on gravity or applied pressure to fill a mold, centrifugal casting spins the mold while liquid metal is poured into it, and the rotational forces fill the mold. This distinctive approach eliminates the need for gating systems and risers. To learn more, see our guide on Types of Casting Processes.
What Are the Steps in the Centrifugal Casting Process?
The process is further explained in the following list of steps:
1. Prepare the Mold
The inner surface of the mold is coated with refractory material, typically between 1-1.15 mm in thickness. In true centrifugal casting, this coating process involves preheating the mold and then applying the ceramic slurry while the mold is spinning. Following this application, the coated mold is subjected to a drying and curing process, ensuring the refractory coating adheres securely to the mold surface. Cleaning the mold surface before applying the refractory coating remains a crucial step to remove any contaminants or debris that could affect the surface finish and integrity of the cast part.
2. Pour the Molten Metal Into the Mold
The casting metal is heated beyond its melting point and poured directly into the mold through a spout, without the need for a gating system.
3. Pour the Molten Metal Into the Mold
The mold is either rotated while the molten metal is being poured into it or is set into rotation after the pouring is completed. The rotation rate generally falls between 300 and 3000 rpm — it depends on the project specifics.
4. Centrifugal Forces Distribute the Molten Metal
The centrifugal forces generated by the rotation of the mold cause the molten metal to be pushed toward the outer wall of the mold cavity.
5. Maintain Mold Rotation Until Molten Metal Solidifies
The mold continues to spin after pouring is finished, allowing the part to cool and fully solidify and harden. The rotation aids in maintaining a sense of uniform material distribution around the inner circumference of the mold.
6. Remove Solidified Casting From Mold
Once the casting is solid and the desired part hardness is achieved, the mold is removed and opened to extract the finalized solidified casting. The specifics of the process can vary based on the type of centrifugal casting being performed, such as true centrifugal casting or semi-centrifugal casting.
What Are the Three Different Types of Centrifugal Casting?
There exist three variations of centrifugal casting. These are listed and discussed below:
1. Centrifuging
Centrifuging or centrifuge casting, requires positioning mold cavities of varying shapes at a specified distance from the spin axis. Under the influence of centrifugal forces, molten metal is propelled into the mold cavities through the sprue and runner. Similar to true centrifugal casting, the properties of the castings can vary as a function of their distance from the spin axis. This technique finds application in the creation of smaller components such as: jewelry, miniature bushings, and sleeves.
The mold's design incorporates cavities surrounding a central sprue and interconnected by runners. Molten metal is carefully introduced to the sprue, and it flows from there to the runners to eventually fill each mold cavity. The molten material can be poured into a mold that is either already rotating or stationary at the outset of the casting process. The pouring ceases once the required molten metal volume for the castings, along with the necessary runner and sprue quantities, has been delivered. Rotation is maintained post-pouring to ensure complete distribution within the cavities during the solidification phase. The operator (or the control system) halts the mold’s rotation once the castings have solidified adequately, allowing for the extraction of components from the mold.
2. Semi-Centrifugal Casting
Semi-centrifugal casting is a technique that utilizes centrifugal force to create solid castings instead of the tubular shapes made by true centrifugal casting. In the illustrated example of the semi-centrifugal casting in Figure 2 below, the molds are configured with a riser located at the rotation axis to facilitate the flow of molten metal:
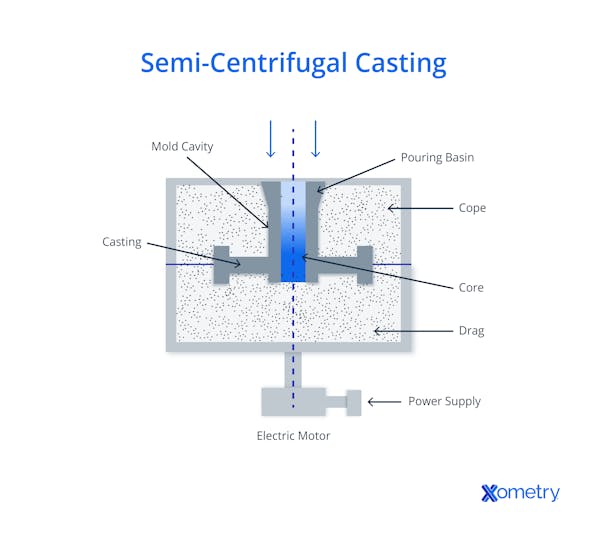
A disposable or permanent mold is arranged around a central sprue, where molten metal poured. This molten material then flows into a rotating mold under the influence of the centrifugal force induced by the rotation. Pouring is stopped once the mold and sprue have been filled. Rotation persists post-pouring. The ongoing rotation ensures that the parts of the casting furthest from the axis of rotation remain fully dense throughout the solidification phase. Once the castings have fully solidified, the equipment discontinues rotation, allowing for the extraction of the finished cast pieces.
This method is employed to craft various components such as: pulleys, spoked wheels, gear blanks, nozzles, and brass bushings. Parts made by semi-centrifugal casting display higher density in their outer regions than at the central axis. This process finds particular application in fabricating items such as spoked wheels, which exhibit rotational symmetry, consequently eliminating the central casting region. This removal of the center section concurrently eliminates the lowest-density part of the cast.
3. True Centrifugal Casting
In the true centrifugal casting process, molten metal is introduced into a rotating mold. The mold's rotation can be either vertical or horizontal, with horizontal rotation being more popular. Horizontal-axis centrifugal casting is primarily used for producing tubular components such as: bushings, tubes, pipes, and rings. The molds employed are typically constructed from materials such as: iron, steel, or graphite, and a refractory lining is applied to them to extend their operational life. The mold surfaces are designed to accommodate a variety of external profiles for pipe casting.
The working principle of true centrifugal casting involves the direct pouring of molten metal into the mold without the need for gating mechanisms. The spinning mold imparts an initial tangential motion to particles of molten material resting on its surface. These particles tend to move tangentially due to their inertia, but the centripetal force exerted by the mold redirects them inward, preventing them from being expelled from the mold and compelling them to adhere to the inner wall of the cavity. Following the completion of the pour, the mold continues to rotate until the part has solidified sufficiently. Once the casting has set, the mold is removed and opened, and the finished part is extracted for subsequent processing. Products generated by true centrifugal casting are fully dense, particularly in the outer sections where the centrifugal force is highest.
The advantages of this method include: high density, superior mechanical strength, adequate outer surface finish, and a fine-grained structure in the castings. Nonetheless, some drawbacks of centrifugal casting include potential inaccuracies in the inner surface diameter, limitations in producing highly complex hollow parts, substantial initial investment requirements, and challenges associated with casting very small inside diameters, particularly in terms of operational safety factors and reduced effectiveness of the centrifugal process at smaller sizes.
What Metals Can Be Centrifugally Cast?
The metals commonly used in centrifugal casting include:
1. Stainless Steel
Stainless steel is a preferred material for centrifugal casting due to its excellent corrosion resistance, strength, and durability. It is suitable for both true centrifugal casting and semi-centrifugal casting, depending on the complexity of the component and specific application requirements. Stainless steel material lfinds extensive use in diverse industries, including: chemical processing, food production, and aerospace.
2. Nickel Alloys
Nickel alloys are highly regarded for their exceptional high-temperature and corrosion resistance properties, making them indispensable in critical applications within the aerospace industry, petrochemical processing, and power generation equipment. Nickel alloys are commonly utilized in true centrifugal casting to ensure precise material properties for demanding applications. To learn more, see our guide on Nickel Alloy.
3. Copper
Copper and its alloys are celebrated for their superb thermal and electrical conductivity. This makes them essential materials in electrical components, plumbing systems, and various engineering applications. Copper alloys are versatile and frequently employed in both true centrifugal casting and semi-centrifugal casting, depending on the part's complexity and required conductivity. To learn more, see our guide on Copper Physical Properties.
4. Cast Iron
Cast iron, including variants like gray iron and ductile iron, is a trusted choice for heavy-duty applications. It is often used in the manufacturing of pipes, rolls, and automotive components. Cast iron is particularly well-suited for true centrifugal casting, where high material density and strength are essential.
5. Aluminum
Aluminum alloys are lightweight and have good corrosion resistance, making them invaluable in weight-sensitive industries like automotive and aerospace. Aluminum alloys can be employed in a variety of centrifugal casting methods, including true centrifugal casting, semi-centrifugal casting, and centrifuging, depending on the specific application requirements. To learn more, see our guide on the Properties of Aluminum.
6. Steel
Various types of steel, including carbon steel and alloy steel, can be centrifugally cast. They offer a balance of strength and versatility and are used in a wide range of applications across industries like manufacturing and construction. Steel can be used effectively in both true centrifugal casting and semi-centrifugal casting, tailored to meet the complexity and material properties needed for specific components. To learn more, see our guide on Steel Properties.
Can Magnesium Be Used as a Casting Metal for Centrifugal Casting?
No, magnesium is not well-suited for centrifugal casting, however, its alloys (e.g., aluminum-magnesium alloys) are often used.
What Are Some Applications of Centrifugal Casting?
Centrifugal casting produces a substantial array of components suitable for both industrial and consumer goods. For instance, this technique finds application in casting: cylinder liners, gearbox components, and various other parts. Centrifugal casting’s utility extends further to crafting sinker bars and furnace tubes crucial in petrochemical plants, as well as fabricating intricate medical implants like hip replacements and dental crowns. Centrifugal casting is also the technology of choice for uses such as: hydraulic wear rings, military and defense components, jet engine compressor cases, and other high-reliability applications.
What Industries Use Centrifugally Cast Products?
Centrifugal casting finds diverse applications across multiple industries due to its unique advantages and capabilities. For example, centrifugal casting serves the automotive sector by producing a variety of critical components such as: cylinder liners, pistons, pipes, tubes, and cylinders made from various metals and alloys. The aerospace industry relies on centrifugal casting to create components that meet rigorous standards such as rocket nozzles for aerospace propulsion systems. The method is employed in the production of reaction vessels, columns, and other chemical processing equipment. The resulting components exhibit excellent corrosion resistance and structural integrity. Centrifugal casting is also applied in creating high-quality jewelry pieces, and ornamental items. It allows for intricate designs and ensures the proper filling of fine details.
What Is the Quality Level of Centrifugally Cast Products?
Centrifugal casting is renowned for producing high-quality components. These components reach full density and are free from oxides, gas porosity, and any other nonmetallic inclusions.
Are Centrifugally Cast Products Heat Resistant?
Yes, when the alloy used to make a centrifugal casting is heat resistant, then the cast product will be heat-resistant. But the level of heat resistance depends on various factors including the type of metal used and the casting process parameters. Metals used in centrifugal castings, such as cast irons, a range of steel alloys, and non-ferrous metals such as bronze, can possess excellent heat-resistant properties.
What Are the Advantages of Centrifugal Casting?
Centrifugal casting offers several advantages, including:
- The rapid cooling induced by mold rotation promotes the development of a finer grain structure in the cast material. Simultaneously, centrifugal force propels molten material towards the mold's periphery. This combined effect results in improved structural integrity and superior mechanical properties in the final product.
- The forced outward flow of molten material serves to channel impurities and gasses towards the casting's center. The controlled solidification process further aids in minimizing undesirable microstructures. The process's rotational motion ensures even material distribution, contributing to the reduction of issues like porosity, inclusions, and segregation.
- Can create thin-walled sections (2.5 mm minimum) with a reduced risk of defects or inclusions. However, this is really only applicable to semi-centrifugal casting and centrifuging.
- Can bring out intricate details and features in the mold surface for crafting complex designs for jewelry. This advantage is specific to centrifuge casting and semi-centrifugal casting.
- A wide range of materials can be used to make centrifugally cast parts. This includes: iron, steel, stainless steel, various nickel, aluminum, copper, magnesium alloys, cement, concrete, glass, and pottery materials.
- The absence of gating systems and risers in centrifugal casting reduces the cost and material waste. However, it's important to note that in semi-centrifugal casting and centrifugal casting, the use of sprues, runners, and gating systems can have a beneficial effect on defect avoidance.
- It is suitable for producing both small and large components, offering versatility in component size and geometry. True centrifugal casting is well-suited for cylindrical or symmetrical parts, with size capabilities up to 6 meters in diameter and 15 meters in length.
- Parts often exhibit reduced anisotropy (directional variations in properties). The process often results in more uniform material properties throughout the component compared to other casting processes like sand casting.
- Has the ability to make two-layered castings.
- Produces round parts with no internal stresses.
- Centrifugal force separates less dense substances in the casting's bore area, including metal oxides, sulfides, gas, and other impurities, which are later machined away, leaving a defect-free part. This process is termed "secondary refining."
- Avoids mid-wall defects often seen in gravity or static castings by solidifying from the outside surface inward, resulting in parts free of shrinkage cavities, gas pockets, and blowholes.
What Are the Disadvantages of Centrifugal Casting?
Centrifugal casting has several drawbacks that render it incompatible with certain applications such as:
- The dimensions of the inner wall are poorly controlled compared to the outside wall.
- While centrifugal casting can produce a variety of sizes, it may be less suitable for highly complex hollow parts with intricate internal geometries.
- Achieving a high-quality surface finish may be more challenging with centrifugal casting compared to other casting methods, and additional finishing processes may be required.
- Vertical centrifugal castings are generally limited to a length-to-diameter ratio of about 2:1. Exceeding this ratio may result in uneven metal distribution along the mold wall, impacting cost calculations.
- Irregularly shaped outside diameters are possible but may require expensive metal or graphite molds. The cost of tooling should be balanced with potential cost savings in post-processing.
- Casting very small inside diameters can be challenging, and the benefits of the centrifugal process decrease as size decreases. Operational safety factors can limit mold speeds for small inside diameters.
- Achieving high-quality castings depends on factors like: equipment, design, deep chill utilization, directional solidification, and high feeding pressure. Good foundry practices are essential for consistently producing high-quality castings.
- Centrifugal castings are not restricted to circular external shapes; they can take on various forms such as: elliptical, hexagonal, or fluted contours. However, it's important to note that the true centrifugal casting process confines the interior bore to a circular cross-section.
How Much Does Centrifugal Casting Cost?
Centrifugal casting, also known as spin casting, is often regarded as a cost-effective method, with a total investment requirement typically not exceeding $20,000. This stands in stark contrast to investment casting, which is more expensive (usually millions).
Is Centrifugal Casting the Same as Investment Casting?
No, centrifugal casting and investment casting are two distinct processes. Both investment casting and centrifugal casting have the ability to yield high-quality, near-net parts. A difference between the two methods lies in the fact that investment casting involves the use of disposable ceramic molds, which are removed from the cooled parts, whereas centrifugal casting utilizes durable dies that can be reused. Centrifugal casting is also unique in that it utilizes centrifugal force in the casting process.
In investment casting, the process begins with the creation of a wax pattern, which is an exact replica of the desired final part. This wax pattern is then encased in a ceramic mold, creating what is known as the "investment" or "lost-wax" mold. The term "investment casting" actually derives from this step, where the wax pattern is invested in the ceramic mold. Investment casting is known for its ability to produce high-fidelity parts with intricate details, and it is often regarded as a premium casting process for this reason.
What Is the Difference Between Centrifugal Casting and Sand Casting?
The main difference between true centrifugal casting and sand casting is that sand casting makes use of expendable molds made of sand, while true centrifugal casting uses permanent, metal molds. Some differences are listed below:
- Centrifugal casting involves the rotation of a mold at high speeds while molten metal is poured into it. In contrast, sand casting relies on a mold made from a mixture of sand and binders to shape the molten metal. This mold, formed around a pattern resembling the final object, accommodates the poured metal, which solidifies within the mold. Once the casting hardens, the sand mold is broken apart to unveil the final product.
- Centrigual casting typically utilizes permanent molds made from robust materials like steel, cast iron, or graphite. Sand casting is versatile and applicable to a wide array of casting sizes and shapes. Its applications encompass a wide spectrum of items, including: engine blocks, machinery parts, and artistic sculptures, making it well-suited for both intricate and larger-scale castings.
Summary
This article presented centrifugal casting, explained it, and discussed its various applications and advantages. To learn more about centrifugal casting, contact a Xometry representative.
Xometry provides a wide range of manufacturing capabilities, including casting and other value-added services for all of your prototyping and production needs. Visit our website to learn more or to request a free, no-obligation quote.
Disclaimer
The content appearing on this webpage is for informational purposes only. Xometry makes no representation or warranty of any kind, be it expressed or implied, as to the accuracy, completeness, or validity of the information. Any performance parameters, geometric tolerances, specific design features, quality and types of materials, or processes should not be inferred to represent what will be delivered by third-party suppliers or manufacturers through Xometry’s network. Buyers seeking quotes for parts are responsible for defining the specific requirements for those parts. Please refer to our terms and conditions for more information.
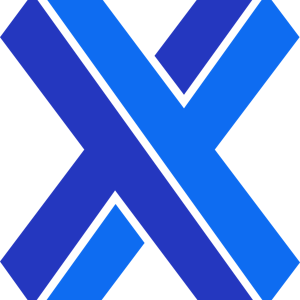