What is Urethane and How is it Used?
Urethane is a type of thermosetting plastic used in a wide range of specialized applications. Urethanes can be processed to make solids, foams, and occasionally films or even fibers. This article will explain exactly what urethane is and why it is such a useful engineering material.
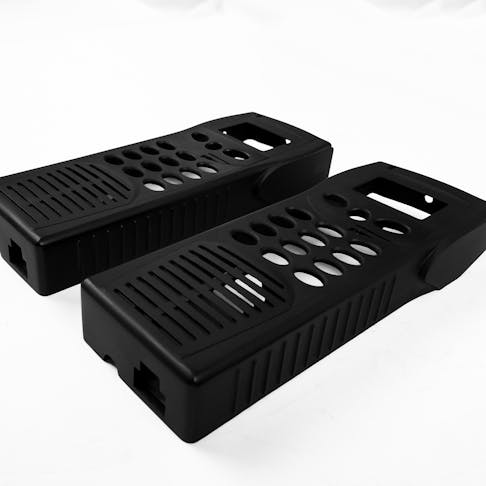
Types of Urethane
Urethanes are made from three fundamental ingredients known as polyols, isocyanates, and chain extenders. Each of these can be further modified and broken down into its own component ingredients. Ultimately there are six common urethane gades, each with its own set of unique advantages and disadvantages, some of which are described below.
- TDI PTMEG Polyether - This grade of urethane has good low-temperature flexibility and is resistant to microbial growth.
- MDI PTMEG Polyether - This grade has good dynamic properties and is very resilient.
- TDI Polyester - This grade of urethane is known for its excellent abrasion resistance and chemical resistance.
- MDI Polyester - This grade is used for applications that require toughness and abrasion or tear-resistance and which will ultimately require FDA approval for use with food.
- NDI Polyester - This is an advanced urethane that has excellent dynamic properties and has some of the best load-bearing capacities of all the urethanes.
- TDI Polycaprolactone -This grade has good dynamic properties and better hydrolysis resistance when compared to otherwise similar polyesters.
Urethanes can be supplied as a hot cure or cold cure compounds. Hot cure means the prepolymer and curative chemicals need to be heated before mixing. Cold cure means the prepolymer and curative can be mixed at room temperature. In general, hot cure polymers have superior properties.
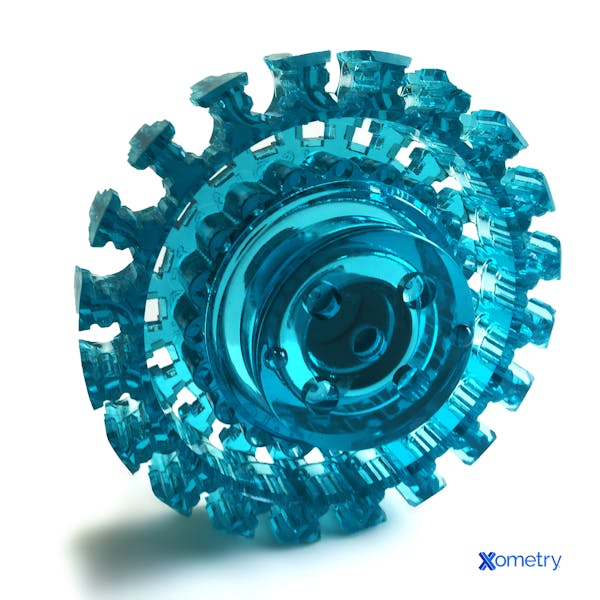
Urethane Properties
Urethanes have many different applications and are selected for products that can benefit from their unique strong points, some of the most important are listed below.
- Hardness - Urethane can be manufactured in a wide range of hardness values from 30 shore A (as soft as silicone) up to 75D (as hard as typical commodity thermoplastics like ABS). As such, urethanes can be used to manufacture vibration dampers as well as hard abrasion-resistant panels. The relation between the shore A and D hardness scales is indicated in Figure 1 below.
- Wear Resistance - Urethanes are primarily known for their exceptional resistance to abrasive and erosive damage and far outperform other elastomers like rubber in this regard. This abrasion resistance increases with hardness.
- Tear Strength - Urethanes have excellent tear strength and can resist tear growth even if the material has been nicked and is under tension. This is possible thanks to the long cross-linked polymer chains.
- Compressive Strength - Urethanes perform well in applications that require compressive resistance and can be used for fall-arrest dampers found in elevators or at the end of railway lines. Urethanes are incompressible (apart from urethane foams) and as such need to be given enough space to expand when under load.
- Tensile Strength - Urethanes are not commonly used in tensile applications due to their extreme elongation and creep.
- Heat Build-Up - Urethanes are insulators and tend to build up heat when used in dynamic applications at high loads and high speeds. They are rarely used in these types of applications as they tend to fail rapidly once their internal temperature reaches the material’s degradation point. There are, however, exceptions to this in some of the more advanced urethane formulations.
Processing Urethane
Several components are necessary for the processing of urethanes. Both the prepolymer and curative must be prepared separately. They then get mixed and introduced into the casting mold. Finally, it has to set for a predetermined amount of time and may need a post-curing step as well.
1. Hand Processing
Small-batch urethane production is normally performed using hand-processing techniques. The process is described in detail below.
- Prepolymer Preparation - Depending on the type of urethane, the prepolymer may arrive as a solid or a liquid, if it is a solid it needs to be melted down in an oven. Next, the component masses can be calculated; the mixing ratio is normally specified by the material supplier. This ratio can be varied slightly in order to favor certain mechanical properties such as abrasion resistance or compressive strength, though in general this is not required. The correct amount of prepolymer must then be weighed out in preparation for the mix. Most prepolymers should be degassed by placing them under vacuum to remove any air bubbles from the material and thus ensure a high-quality end product free of bubbles.
- Curative Preparation - Next, the curative must be prepared. Once again, this component may be provided in liquid or solid form, each of which has its own set of advantages and disadvantages. The curative can then be weighed out according to the ratio calculation in preparation for mixing. If the urethane needs to be colored, pigment is most often added to the curative mix. Experts generally recommend mixing the pigment into the curative to make it easy to see if all the curative has been properly mixed in with the prepolymer. Very little pigment is required to color a part; as little as 2% of the total mix mass will successfully color the part.
- Mold Preparation - Next, the mold can be prepared. The mold can be made of fiberglass, steel, or even silicone. It needs to be lubricated with a mold release agent to prevent the part from sticking to the mold’s surfaces. Molds for hot cure urethanes should be heated before casting as this helps prevent the formation of surface defects.
- Casting - Once everything is ready, the material can be mixed. In the case of hot cure urethanes, the prepolymer and curative must first be heated to the recommended temperature then thoroughly mixed. Mixing must be done in a way that limits the introduction of air into the mix. After mixing, a second degas process is performed and the material can be cast into the mold. Urethane set times can vary from a couple of minutes to an hour. Note that materials that have short set times are best processed by machine rather than by hand.
2. Machine Processing
Urethane can be mixed using a machine called a dispenser. This machine mixes the prepolymer, curative, and pigment automatically and injects it into a mold. The whole process is similar to injection molding and does not require any hand processing.
3. Post Curing
Most urethanes need to be post-cured in an oven to achieve their final properties. In some cases, a part may be demolded after an hour but must be left in an oven for up to 16 hours for the remaining cross-linking to occur.
Which Urethane is Best for my Application?
Choosing the correct urethane is a challenging task that requires an understanding of all the advantages and disadvantages of the different grades. So many versions of urethane exist that the selection process can easily become overwhelming. Xometry has extensive experience with selecting the correct grade for specific applications and can help choose the perfect urethane for your unique job. Contact a Xometry expert or get an instant quote on urethane casting today.
Disclaimer
The content appearing on this webpage is for informational purposes only. Xometry makes no representation or warranty of any kind, be it expressed or implied, as to the accuracy, completeness, or validity of the information. Any performance parameters, geometric tolerances, specific design features, quality and types of materials, or processes should not be inferred to represent what will be delivered by third-party suppliers or manufacturers through Xometry’s network. Buyers seeking quotes for parts are responsible for defining the specific requirements for those parts. Please refer to our terms and conditions for more information.
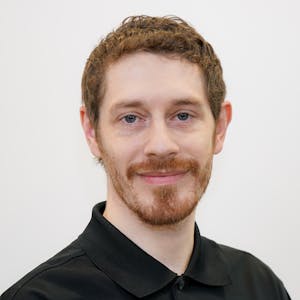