5 Key Prototyping Phases
A common misconception about prototyping is that it’s reserved for early in the product development cycle. But the truth is, many engineers use prototyping in several phases, iterating early and often to present, test, and perfect their ideas.
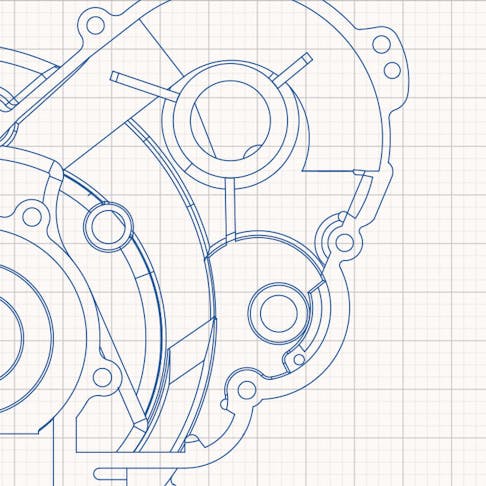
With 3D printing and online manufacturing services, it has never been easier to produce a prototype quickly and cheaply. Many engineers know that prototyping is not just for early rapid prototype development, but can also play a role throughout various phases of validating a new product. From engineering to sales to market research, having an updated prototype in hand can be immensely valuable to achieving the best project results.
To help you perfect your design and save on costs, we’ve put together a list of 5 key prototyping phases, and which manufacturing processes are best suited for each.
Product Concept
Product concept models, or physical mockups, are often used to sell an idea to internal and external stakeholders. The goal of a product concept is to develop a sales model and is useful in the early stages of product development.
In this stage, prototypes can have a wide range of prices, depending on what is needed – from quick and relatively inexpensive 3D printed prototypes that can bring a concept to life within a few days, to more polished, professional-looking sales models that are typically more time-consuming and resource-intensive to produce (e.g., CNC machining). The sales models can often be used for marketing promotional materials; you may even get preliminary feedback from a customer base to improve engineering requirements.
Best processes: CNC Machining, 3D Printing Services, Urethane Casting
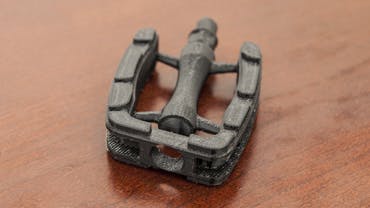
FDM (Fused Deposition Modeling)
Proof of Concept
The goal of a proof of concept prototype is less cosmetic and more functional. Its requirement is to demonstrate the product’s core functionality and prove that the design works as intended. This is often referred to as a benchtop model because it may use off-the-shelf items in its assembly to save on costs and prove out the product functions.
Selective Laser Sintered (SLS) 3D printed nylon is a valuable tool for building a proof of concept design, fixtures, and other features because of its low cost across various geometries. It is not uncommon to use several manufacturing processes when building a proof of concept in order to achieve functional goals.
Best processes: Selective Laser Sintering (SLS), HP Multi Jet Fusion (MJF), Metal 3D Printing, Sheet Metal, Urethane Casting, CNC Machining
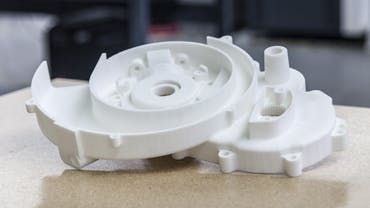
SLS (Selective Laser Sintering) 3D Printing
Industrial Design
Industrial designs are generated to validate the aesthetics, ergonomics, or scale of a product. In this stage, the prototype simulates the final product, and the aim is to analyze for the best usability and overall ease of use. If the design is an electromechanical system, then this is typically where the engineers are mindful of how much internal space is required to package the PCBs and internal mechanisms while also accommodating external features like cosmetics and ergonomics. Typically, the focus is on using similar materials to the final product. For example, PolyJet 3D printing can create rubber-like parts, and SLA has several materials that simulate injection molded pieces. Carbon DLS also plays a powerful role for smaller components, as it can directly transition into scaled production without injection mold tooling requirements. Along with metal CNC machined prototypes and metal 3D printing, there are also some great, low-cost alternatives for building metal parts, e.g., SLS nylon with nickel plating.
Best processes: Stereolithography (SLA), Carbon Digital Light Synthesis (DLS), PolyJet, Selective Laser Sintering (SLS), HP Multi Jet Fusion (MJF), Metal 3D Printing, Sheet Metal, Urethane Casting, CNC Machining
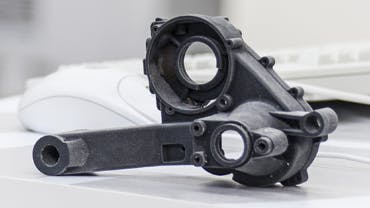
PolyJet 3D Printing
Functional Prototype
The functional prototype is where the proof of concept meets the industrial design. This is a product that could be shared directly with a stakeholder to use and provide feedback against. Functional prototypes are typically still made before any major investments in production tooling to mitigate any costly mistakes or revision changes down the line. Potential applications include testing aerodynamics, mechanical performance, mechanical properties, and thermal performance.
Functional prototypes often require end-use durability and smoother surface finishes. Because of this many photopolymers are not suitable and instead, thermoplastic 3D printing, urethanes, and silicone materials are used as well as machined and metal fabricated parts.
Best processes: Urethane Casting, HP Multi Jet Fusion (MJF), Carbon DLS, Sheet Metal, CNC Machining, Fused Deposition Modeling (FDM)
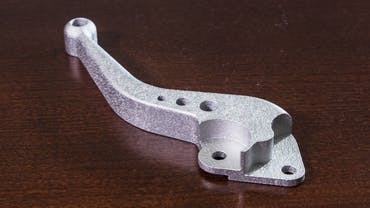
DMLS (Direct Metal Laser Sintering) 3D Printing
Pre-Manufacturing Research
Pre-manufacturing research models are designed to get into the hands of your early adopters, key stakeholders, and potential evangelists for your product. This should be a refined version of the functional prototype made in lower volumes than the forecasted production once your product is into the market. Market evaluation should give any final feedback critical to your product’s success, and internal team members may be working on manufacturing, assembly, and supply chain logistics planning.
Although some 3D printing processes can scale parts that have end-use function, like Carbon DLS, this phase often requires prototype injection mold tooling or bridge tooling to rapidly deploy the product at a small scale in the final required materials. These tools may have a shorter lifespan than the production tool, comparing thousands to hundreds of thousands of cycles, but can give an accurate market introduction putting the best foot forward.
Best processes: Carbon DLS, Urethane Casting, CNC Machining, Sheet Metal, Injection Molding Services
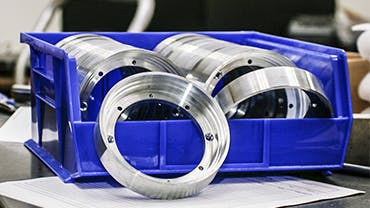
CNC Machining
For tips on how to take your product from start to finish, check out the quick tips in our Product Development Guide.
If you don't know where to get started with mechanical engineering design and need to start from the ground up, check out these online mechanical engineering courses.
