ABS injection molding is a common manufacturing process that involves injecting molten plastic into a mold cavity under high pressure and temperature. This technique is used in the automotive, consumer products, and construction industries for producing various components and products. We’ll cover the definition, uses, process, and techniques involved with ABS injection molding below, but for a brief recap, take a look at our short video below:
What is ABS Injection Molding?
ABS (acrylonitrile butadiene styrene) injection molding is a standard way to make ABS plastic products. ABS is a strong and lightweight thermoplastic polymer that’s easy to work with. The process involves adding molten ABS into a mold cavity and then removing it after it cools. It’s a fast and useful method that’s used to craft ABS products at an affordable cost. It’s a popular go-to for household appliances, tools, and medical devices. It’s used to make Lego bricks, computer keyboard keys, power tool housings, and power outlet fittings, and in the automotive sector, is used for dashboards, seat belt parts, door trim, and bumpers. Below is a picture of a part made with ABS injection molding
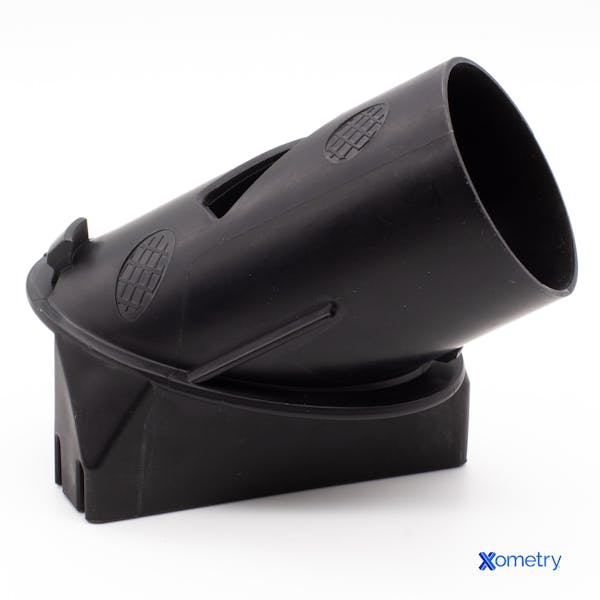
Almost any thermoplastic can work for injection molding. They can be filled with reinforcing additives like glass or carbon fiber fillers. You can also inject metals if it’s combined with a plastic filler, allowing the metal powder to flow through the mold. That said, additional sintering is needed for metal injection molding. The ABS injection molding process is the same as with most other thermoplastics. Resin pellets get fed into a hopper, where they’re melted and injected into a mold using high pressure. Once it’s cooled and re-solidified, it’s removed from the mold. The simple and efficient process makes it perfect for high-volume production, and it creates very little waste, too.
The intricacy of the parts you can make is only limited by a set of well-established DFM (design for manufacturing) guidelines that are created specifically for injection molding. It can make multi-featured, complex parts with metal inserts or overmolded soft-grip handholds, and you can easily add a range of colors (think: Lego bricks). This is all without the need for much human intervention, something that keeps labor costs to a minimum and also makes the parts more affordable for customers (obviously the cost and time required increase with the complexity of the part). ABS is easy to shape, recyclable, resistant to chemicals and heat, and has a low melting temperature. It won’t allow dirt to get in, but it doesn’t do too well in UV light and prolonged outdoor exposure. To give it a little more power against the elements, it can be painted or electroplated with metal.
ABS’s viscosity increases when heated past its plasticizing temperature (unlike most other amorphous plastics), so it needs to be kept at or below that temperature for good results, especially when it comes to molding thin-walled components. Aside from an increase in viscosity, higher temperatures can chemically degrade ABS, if kept well above the plasticizing temperature. The plastic could also warp if it cools unevenly, but this can be prevented by using a mold with evenly spaced cooling channels. It could also shrink unevenly during cooling, creating sunken areas on the surface, if the temperature is too high or the injection pressure isn’t sufficient. Again, these marks (known as sink marks) can be avoided if you use a mold with a high gate pressure.
In relation to the actual injection molding process, there’s a high initial investment for the machinery (which is why it’s better suited for high-volume production), and a minimum part quantity is needed to break even on mold costs. In addition, some may find the DFM’s rules a little limiting when it comes to more creative designs. These standards were created to improve part quality and consistency, as well as cover things like wall thickness limits, the location of reinforcing features (like ribs), and the best hole location/size.
ABS Injection Molding Techniques
Depending on what you’re trying to make with this method, the technique will be different. Here are some examples:
- Thin wall: Due to the aforementioned high viscosity, pressure has to be increased for thin-walled parts, and the molds have to be designed to handle the added pressure.
- Large and hollow: Creating large, thin, or hollow parts is generally difficult, but using water- or gas-assisted injection molding can help. This technique presses the molten plastic against the sides of the mold to create even thickness and smoothness.
- Thick wall: Standard techniques can create sink marks on thick-walled parts. One way to handle this is by using compression injection molding. This adds a specific amount of molten plastic into a mold to create the final part. It also reduces internal stresses. Sink marks can also be managed with thinner mold walls or higher thermal capacity in the mold.
- Multi-material: If you need components made from various materials, consider techniques like insert molding or overmolding. For example, cordless drills have their handles overmolded onto ABS to improve the tool’s grip.
How Xometry Can Help
Xometry provides a wide range of manufacturing capabilities, including CNC machining, 3D printing, injection molding, laser cutting, and sheet metal fabrication. Get your instant quote today.
Copyright and Trademark Notice
- LegoⓇ is a registered trademark for LEGO JURIS A/S CORPORATION DENMARK KOLDINGVEJ.
Disclaimer
The content appearing on this webpage is for informational purposes only. Xometry makes no representation or warranty of any kind, be it expressed or implied, as to the accuracy, completeness, or validity of the information. Any performance parameters, geometric tolerances, specific design features, quality and types of materials, or processes should not be inferred to represent what will be delivered by third-party suppliers or manufacturers through Xometry’s network. Buyers seeking quotes for parts are responsible for defining the specific requirements for those parts. Please refer to our terms and conditions for more information.
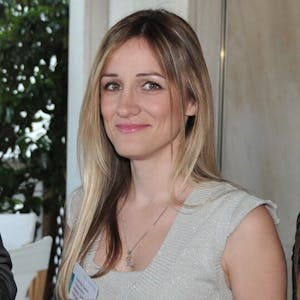