Etching is a critical step performed before the anodization of aluminum or aluminum alloys, to improve the quality of the final treatment. Etching removes any surface contaminants or oxides from the component, leaving a clean and uniform surface that is better able to be anodized. This stage has significant effects on the quality and aesthetics of the part coating in real-world environmental resilience. A range of possible surface finishes can be achieved by etching, from a fine matte finish to a visible crystalline texture that results from longer and more aggressive processing.
This article will discuss what is the etching process for anodization, its importance, and the types of chemicals used.
What Is the Etching Process for Anodization?
The etching process for anodization involves a number of distinct stages. It is necessary to perform these steps correctly to avoid cross-contamination issues. The process is listed below:
- Cleaning: Clean the part using solvents or detergent solutions to remove any oil and water-soluble residues.
- Etching: With the surface degreased and cleaned, immerse the part in the etching solution which may be acid or alkaline in nature. The selection of etchant depends on the required surface finish and the type of aluminum alloy being etched. The part will remain in the etching solution for a couple of minutes to several hours, depending on the type of etching solution, the concentration of the chemicals, and the degree of etching required. This stage in the process exposes a fresh metal surface, free of any oxides or contaminants, that provides an excellent keying for the oxide film by being rough, micropitted, and of a much larger surface area than the original flat surface.
- Neutralization: After etching, remove the part from the solution and neutralize it in a corresponding pH solution (alkali for acid etch and vice versa) to curtail the etching process.
- Rinse: Rinse the material thoroughly with deionized water to remove any remaining acid/alkali or reaction residues.
- Drying: Dry the part in warm air before further processing.
For more information, see our guide on Everything You Need to Know About Aluminum Anodizing.

Why Etching Is Important Before Proceeding With Anodizing?
Etching before anodizing brings a variety of interrelated benefits that can be both technically and aesthetically important. These are listed below:
- Improved Adhesion: Etching creates a micro-roughened surface that provides a greater surface area and better keying for the oxide layer to adhere to. This results in better adhesion and a more durable and uniform finish.
- Improved Appearance: Etching produces a matte surface, free from the cutting or casting tell-tales that are naturally present on machined or otherwise processed aluminum parts. This makes for better aesthetics in the finished part.
- Improved Corrosion Resistance: Better adhesion results in a more robust and well-integrated oxide film on the parts. Aggressive removal of existing oxides and contaminants ensures greater uniformity in the formation of the oxide film. The surface is free of chemically weak spots at which the film is at risk of failure, peel, and corrosive attack.
- Improved Color Uniformity: Aluminum parts can be color anodized by control of the anodizing conditions. This is more commonly achieved by the application of dyes after anodizing. Such dyes penetrate into the oxide film and become color-fast as long as the anodizing remains undamaged. Parts that were imperfectly etched (or anodized without etching) will suffer very non-uniform coloration, as the thickness and properties of the oxide layer will be non-uniform.
How Is Etching Done?
Etching is an alkali or acid-based chemical erosion of the part surface. This is done to expose uncontaminated, oxide-free, and finely crystalline material that is best suited to the electrochemical oxidation process of anodizing. Immersion in (commonly proprietary) chemical formulations is used to attack the surface and chemically ablate oxide and metallic material to form a keying and visually appealing surface upon which the anodizing layer can be applied.
How Long Is the Etching Process Before Getting Ready for Anodization?
Preparatory and final wash, rinse, and drying processes are fast. The etching stage, however, can take from a few minutes up to hours and even days. This depends on the nature of the etchant, its concentration, and the desired surface qualities that the part requires. The more coarse the required finish, the longer the etch process will take. Although, most parts receive a relatively short (1–3 hours) etch process to produce a fine matte surface finish that is now widely characteristic of anodized aluminum.
What Are the Types of Etching Processes?
These are the most common types of etching to precede anodizing:
- Chemical Etching: Chemical etching uses an acid or alkaline compound to remove surface oxides and the metal exterior itself. This creates a uniform and anodizing-ready surface. The selection of the etching solution depends on the grade of aluminum being prepared and the required surface finish. This is a precise and widely used process.
- Electrolytic Etching: This approach to etching uses an electrolytic cell to erode the aluminum surface. The aluminum is connected to the anode; the cathode is generally stainless steel or carbon. The electrolyte is usually a caustic soda solution, which ionizes the oxidized metal at the surface. It removes the oxygen and returns the surface to a pure metallic state. The cell erodes the surface of the aluminum, converting it uniformly to bare metal.
- Mechanical Etching: Mechanical etching uses abrasion with sandpaper, wire brushes, or blasting media to erode the surface to bare, fresh metal. This method is generally used when a specific type of surface finish is required such as “brushed”, which is highly directional linishing.
- Plasma Etching: Plasma etching involves the use of a plasma of argon or oxygen, to etch the aluminum surface by ablation. The charged particles in the plasma remove the surface contaminants and oxides. This process is relatively high cost and not widely used, despite the fact that it is very fast acting. It requires only seconds to complete and requires no washing, neutralization, or drying phases.
What Is the Advantage of the Etching Process Before Anodizing?
Etching prior to anodizing delivers some significant advantages as listed below:
- Better anodizing adhesion due to the micro-roughening of the surface.
- Better uniformity of coating as the entire surface is equally reactive. This avoids corrosion weak spots in the resulting oxide layer.
- Uniform coloration, either by color anodizing or by surface dye, as surface oxide thickness is more consistent.
- Improved cosmetics, removing machining marks and surface variations to leave a uniform matte finish.
What Are the Types of Etching Chemicals Used?
Most aluminum etchant chemistries are proprietary and not published in detail. However, the generally accepted and most common chemical etching process uses the following range of dissolved materials in varied proportions, in an aqueous solution:
- 1–5% ammonia (HNO3) for aluminum oxidation.
- 65–75% phosphoric acid (H3PO4) to dissolve the main aluminum oxide (Al2O3).
- 5-10% methanol (CH3COOH) for wetting and buffering.
- And deionized water (H2O) for dilution, to control the rate of etching.
Are Etching Chemicals Hazardous?
No. While the etchant chemistries are not entirely without toxicity, they are not significantly harmful unless sprayed into the eyes or imbibed. They can produce skin irritation, but the material is easily washed away with water. Fumes can be mildly irritant. Basic handling precautions such as PPE, a carbon-filter breathing mask, acid/alkali-resistant plastic gloves, and a well-ventilated workspace are enough to meet required workplace safety standards. There are no long-term exposure issues, and no physiological or medical consequences are likely from regular work with these chemicals.
Is the Etching Process Applicable to Anodizing Titanium?
Yes. While etching prior to the anodization of titanium will improve both the function and cosmetics of the anodized parts, the etch solution recommended is based on ammonium persulfate (APS, (NH4)2S2O8)and sodium fluoride (NaF).
Can Etching Be a Physical Process?
Yes. Etching by grit blasting, linishing, and sanding can give good results, but the mechanical abrasion marks will remain highly visible in the finished part. At times, this is a desired finish and therefore the right process to choose. Brushed (which means linished) aluminum was a popular finish in the early consumer use of the metal, but its use has greatly diminished in recent times.
Sand/garnet grit blasting can be effective in producing coarse matte surfaces. It offers a route to quicker deep etching than chemical processes. Skill, however, is required in producing uniform results even across a single part.
Summary
This article presented etching before anodization, explained it, and discussed the process and its advantages. To learn more about etchining, contact a Xometry representative.
Xometry provides a wide range of manufacturing capabilities and other value-added services for all of your prototyping and production needs. Visit our website to learn more or to request a free, no-obligation quote.
Disclaimer
The content appearing on this webpage is for informational purposes only. Xometry makes no representation or warranty of any kind, be it expressed or implied, as to the accuracy, completeness, or validity of the information. Any performance parameters, geometric tolerances, specific design features, quality and types of materials, or processes should not be inferred to represent what will be delivered by third-party suppliers or manufacturers through Xometry’s network. Buyers seeking quotes for parts are responsible for defining the specific requirements for those parts. Please refer to our terms and conditions for more information.
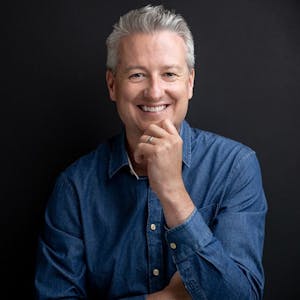