You may have encountered black oxide-coated steel frequently and not thought much about it because it looks unremarkable. At Xometry we instantly quote metal black-oxide coated parts all the time; it remains one of our most popular finishes. But the truth is, it’s an old, simple, and very powerful method for rust-protecting steel that extends the cosmetic and functional life of dry-environment steel parts for many years.
Black oxide, also known as blackening, is a type of chemical-conversion coating by deliberate and controlled oxidation, applied to ferrous metals for corrosion resistance and aesthetic appeal. It is often coupled with an oil film for improved oxidation resilience. In addition to these characteristics, black oxide coatings offer good abrasion resistance due to the hardness of the oxide film, and they also improve the thermal stability of parts. This is typically achieved in a more cost-effective manner than other coating techniques, such as electroplating or painting.
Black oxide coating is commonly preferred for steel components that will not be subjected to moisture or chemical exposure. It quickly turns to brown oxide under wet conditions and will suffer badly from acid marking when handled.
This article will offer you a solid background in black oxide coating, its importance, purpose, applications, and advantages.
What Is Black Oxide?
Black oxide coatings are a type of chemical-conversion coating and are created through a chemical reaction between iron atoms on the substrate surface and oxidizing salts in a chemical bath. This forms a moderately integrated and well-attached layer of Fe3O4 magnetite or black iron oxide. Black oxide coating is typically applied to ferrous materials like steel or iron to improve the substrate’s corrosion and wear resistance. Additionally, the coating adds an aesthetically appealing matte black finish to parts, which is why the process is also sometimes referred to as “blackening.” This class of coating has been applied by metalworks and blacksmiths for centuries. The process of blueing steel and iron, which means heating it in the air to induce the resulting cobalt-blue color, is chemically similar to black oxide coating and has been used since the Iron Age for cosmetic and corrosion resistance purposes and to impose a less robust but easier to achieve Fe2O3 coating on the metal.
In this day and age, black oxide is used in various industries and applications due to its unique combination of properties. Xometry’s customers in aerospace, automotive, electronics, and firearms frequently make use of the finish for their custom parts.
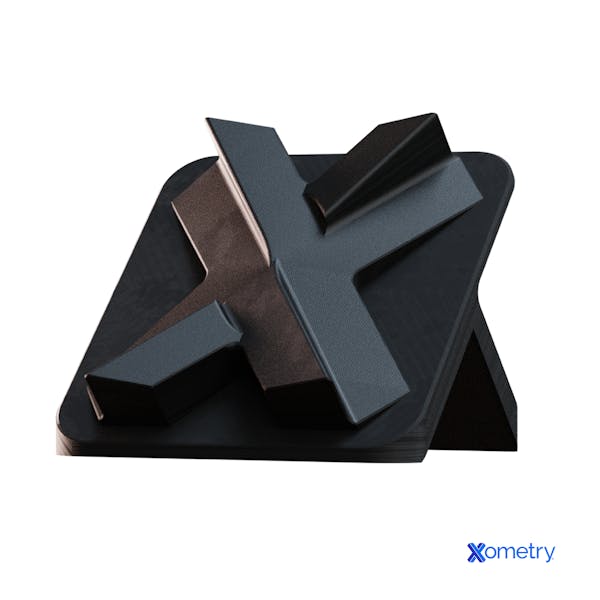
Black Oxide Compared With Other Metal Coatings
Black oxide coating is distinct from most other metal coatings in its application to parts. Unlike other finishes that Xometry offers, such as painting and powder coating — processes that blanket the substrate with a protective layer that is at best only mildly chemically bonded to it — black oxide coatings are created through a direct chemical reaction of the surface atoms to form a closely coupled film. Black oxide is present as a distinct layer on the surface, but it transitions from oxide to metal in a progression through the thickness. As a result, it is well integrated with the metal substrate, offering a more robust and uniform finish.
While black oxide coatings are generally the more eco-friendly option compared to other coating types like painting or electroplating, the black oxide coating process utilizes some chemicals that are harmful to the environment. Chemicals such as nitrates, sodium hydroxide, and others are hazardous but generally less harmful than chemicals used in other coatings. The environmental impact of the process pivots on the disposal of waste and wash-contaminated fluids. If this is managed in compliance with best practices, no toxic chemicals are released.
How Black Oxide Works Step by Step
As mentioned previously, black oxide functions by a chemical conversion process applied to the surface of ferrous metals. The steps for the process of applying black oxide coatings are:
- Contaminants such as dirt, grease, pre-existing rust, dust, and oils are removed from the parts through a thorough cleaning of the surfaces. An alkaline detergent or acid etch-cleaning may be used, depending on the material and its condition.
- Once cleaned, the parts are immersed in a blackening solution containing the requisite oxidizing salts. The solution composition may include sodium hydroxide, nitrates, nitrites, and a variety of other chemicals. The bath is held at a controlled temperature during the coating process, typically 285–305°F.
- The chemicals in the solution react with the iron on the surface of the parts and create magnetite (Fe3O4). The degree of blackening depends on the amount of time the part is immersed in the solution, the operational temperature of the bath, and the efficacy/concentration of the solution. Typically, the part is treated for between 5 and 40 minutes.
- The parts are removed from the salts and thoroughly rinse with water.
- A sealing compound or oil is applied to the black-oxide-coated metal. This is a critical step to enhance the coating's corrosion resistance and durability.
The resulting black oxide coating provides mild corrosion resistance, surface albedo (reflection, luster, etc.), and improved aesthetics. The process is also exploited for its ability to maintain dimensional accuracy and conductivity while enhancing durability and scratch resistance.
Physical Properties of Black Oxide Coatings
The physical properties of black oxide coatings are:
- Black oxide coating enhances the hardness of the outer surface. This increased hardness has value in applications in which resistance to abrasion and wear is crucial, providing a durable surface that withstands mechanical stress.
- The coating lends a lower coefficient of friction and greater scratch resistance to part surfaces.
- Beyond the functional physical enhancement of the surface, black oxide coatings also add to the aesthetics of components in the form of a matte black finish.
Thermal Properties of Black Oxide Coatings
The thermal properties of black oxide coatings are:
- Black oxide coatings are thermally stable, which allows them to withstand elevated temperatures without loss of film integrity. This is essential in applications in which components may be exposed to heat, such as in engine components, gun barrels, or high-temperature industrial environments.
- Black oxide coatings are additionally effective at dissipating heat, compared with bare steel, as the color increases the emissivity. This is particularly useful for components in which managing heat is crucial for optimal performance, such as in electronic devices or machinery.
Get Instant Pricing for Custom Black Oxide Coated Parts
Industries Where Black Oxide is Most Commonly Used
We see customers from a wide range of industries who use black oxide coatings for a variety of component applications. These applications most commonly include:
- Automotive fasteners, brackets, wheel components, brake components, trim pieces, and other automotive parts.
- Aerospace fasteners and brackets, landing gear components, avionic components, trim pieces, and more.
- Electronics connectors, contacts, housings, enclosures, and circuit board components.
- Hand tools, measurement gauges, jigs, dies, fixtures, tool holders, and other tools.
- Screws, bolts, nuts, washers, and threaded rods for industrial environments.
- Machine components, fasteners, rollers, gears, shafts, and more.
The Different Types of Black Oxide
There are two basic classifications of black oxide coatings — hot and cold.
- Hot Black Oxide: The hot black oxide coating is the most commonly used type and involves immersing parts in a boiling bath of alkaline salts, nitrites, and nitrates. The bath’s temperature is typically 285-305 ºF depending on the exact composition of salts used. Applying a black oxide coating above this temperature range will result in a red or rusty appearance while coatings below this temperature range will take longer to process.
- Cold Black Oxide: Compared to hot black oxide, cold black oxide coatings can be applied at room temperature. However, the cold black oxide process immerses parts in a more chemically aggressive bath containing phosphoric acid, copper-based solutions and selenium-based solutions. Despite being an easier method to apply, cold black oxide coatings do not achieve the same level of consistency, durability, or corrosion inhibition.
Advantages of Black Oxide
We recommend using a black oxide coating for a number of reasons:
- It offers significantly enhanced corrosion resistance for ferrous metals, protecting them from progressive oxidation and some other forms of attack.
- It can provide an attractive, uniform, matte black finish that makes it popular for decorative applications and makes it useful for functional applications in various industries.
- It contributes to improved hardness, lower friction, and wear resistance of the metal, which serves to extend the lifespan of products.
- Typically measured in millionths of inches, the coating thickness adds virtually no extra thickness to part surfaces, making it ideal for high-precision parts with tight tolerances.
- Compared to other coating methods like, our electroplating services or powder coating, black oxide is often more cost-effective.
The Disadvantages of Black Oxide
Despite its many advantages, black oxide coatings do have some drawbacks:
- They are only generally applicable to ferrous metals, meaning metals like aluminum do not react well with the process.
- Applying black oxide coatings is somewhat labor-intensive due to the need to clean parts before the coating process and sealing the parts after.
- The sealing process is necessary to enhance corrosion resistance but adds a step to the overall coating process.
- In comparison with many other steel-finishing options such as Xometrys powder coating or metal plating options, black oxide coatings are less durable and offer shorter service life in wet or acidic environments.
If these shortcomings have you considering other coatings, feel free to explore more of our metal finishing options via our metal finishes gallery.
Common Misconceptions of Black Oxide
There are some common misconceptions about black oxide that we’d like to clear up. Firstly, it is a widespread belief that all black oxide coatings provide adequate corrosion resistance in humid or acidic environments. If the sealing step is skipped, then the blackening process alone will not improve resistance to corrosion. We recommend ensuring the surface is sealed and is maintained by re-oiling over time, as well as keeping parts dry to assist with keeping corrosion at bay. Ultimately you may need to consider other types of coatings and finishes for especially wet or corrosive environments where greater protection is needed.
Another misconception is that black oxide coatings suffer from weak adhesion and are prone to chipping or peeling. When applied correctly by following proper surface preparation and process parameters, black oxide forms an integral layer with the metal, which ensures strong adhesion.
Finally, some believe that black oxide can significantly affect part dimensions. While the coating does have a measurable thickness, typically between 0.5 and 2.5 microns (0.0000196” - 0.00098”), it is negligible for most parts and applications.
How Xometry Can Help
Xometry provides various manufacturing capabilities, including machining and other value-added services for all your prototyping and production needs. Visit our website to learn more or to request a free anodizing quote.
Disclaimer
The content appearing on this webpage is for informational purposes only. Xometry makes no representation or warranty of any kind, be it expressed or implied, as to the accuracy, completeness, or validity of the information. Any performance parameters, geometric tolerances, specific design features, quality and types of materials, or processes should not be inferred to represent what will be delivered by third-party suppliers or manufacturers through Xometry’s network. Buyers seeking quotes for parts are responsible for defining the specific requirements for those parts. Please refer to our terms and conditions for more information.
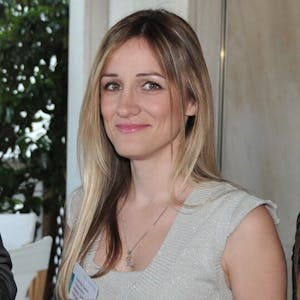