Wondering who, or rather what, you should call on for top-tier corrosion resistance and strength? The answer lies in 316 stainless steel, a material that’s a hearty blend of chromium, nickel, and molybdenum. As the second most popular stainless steel (trotting along after 304 stainless steel), 316 is a favorite among many Xometry customers who use it to create all sorts of custom components and products. Catering to marine manufacturers, chemical plants, medical device manufacturers, and even the food industry, it's used in a wide breadth of industries.
It has the helpful ability to exist in harsh environments that would see other materials crumble, so it’s certainly a worthy option to consider when you’re comparing and contrasting different kinds of steel. If you’d like to familiarize yourself with 316 stainless steel’s composition, properties, applications, and pros and cons, read on.
What is 316 Stainless Steel?
Stainless steel is an iron alloy, but you’ll find that 316 stainless steel (also called SAE 316 stainless steel) has a few special ingredients that differentiate it. Upon inspecting its chemical composition, you’ll see it’s made up of a mix of different elements. It’s a member of the largest class of stainless steels, called austenitic, which essentially tells you about its specific crystalline structure (face-centered cubic arrangement), that it’s not magnetic, and has high corrosion resistance.
Chemical Composition
316 stainless steel in particular has a makeup of iron, chromium, nickel, molybdenum, and carbon, as seen in the pie chart below. In addition, there are a few other trace amounts of elements sprinkled in, such as: <= 2% manganese, <=1% silicon, <= 0.045% phosphorous, <= 0.030% sulfur, and <= 0.1% nitrogen. It’s the molybdenum in its composition that makes it different from its more popular cousin, 304 stainless steel.
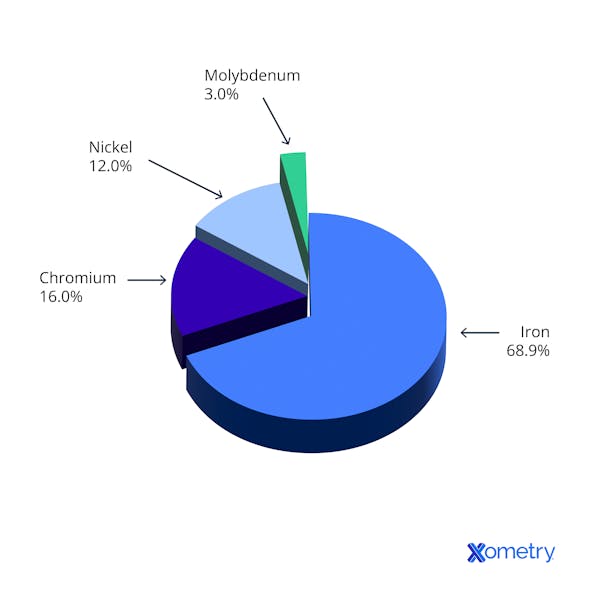
A pie chart displaying the chemical composition of 316 stainless steel.
Property | Value |
---|---|
Property Yield Strength | Value 205 MPa |
Property Hardness | Value 95 HRB |
Property Magnetism | Value Nonmagnetic |
Thermal Properties
As far as stainless steel goes, you’ll notice that 316 and other steels under the austenitic category aren’t as thermally conductive as ferritic steels. The thermal conductivity value for 316 stainless steel is 16.3 W/mK, which is relatively low (just look at aluminum, which has a conductivity of 400W/mK). You can slightly impact that number depending on the structure and composition of the steel you’re working with.
This kind of material also expands and contracts more than others, and 316 stainless steel’s coefficient in particular between 20°C and 200°C is about 16.5 x 10-6/°C. One advantage you’ll find when it comes to working with extreme temperatures is that this kind of steel has a high melting point, ranging between 1,370°C to 1,400°C. It also has decent creep resistance, meaning you won’t have to deal with the steel becoming deformed under high temperatures.
How 316 Stainless Steel Is Made
You’ll need an electric arc furnace (EAF) to create 316 stainless steel. This machine is where you’ll funnel in scrap steel and raw materials, as well as all the additional components that give the stainless steel its strength and corrosion resistance, including iron ore, chromium, nickel, and molybdenum.
Once you’ve popped these into the furnace, the electrodes heat up the metal and it turns into a molten material. The piping hot mixture can then be cast, cooled, and cut into whichever form you desire, whether that’s bars, rods, or sheets.
Common Forms of 316 Stainless Steel
You’ll find stainless steel available in many different forms, with these six being some of the most common.
1. Sheet
If versatility is what you’re after, sheets of stainless steel are hard to beat. These large, flat surfaces are cold-rolled, and you can cut them into a variety of sizes, with widths ranging from 0.5 mm to 6 mm. You may look to this format for many items you’d find in the kitchen, like cookware, grills, sinks, countertops, and refrigerator, dishwasher, and freezer finishes. Xometry can laser or waterjet cut sheets of 316 stainless steel to create flat parts or patterns. You can learn more about this on our sheet cutting services page.
2. Bar
Bars are also known as rods, and you can find them in cylindrical or rectangular shapes in several different widths or diameters. This type of SAE 316 stainless steel offers up the same properties as sheet metal, but bars can provide more strength and bear heavier loads. You’ll notice this kind of format in applications for construction and marine industries, and its finish is smoother and free of that well-known brushed texture found in homes. We often source bar stock when customers choose stainless steel for their CNC-machined parts.
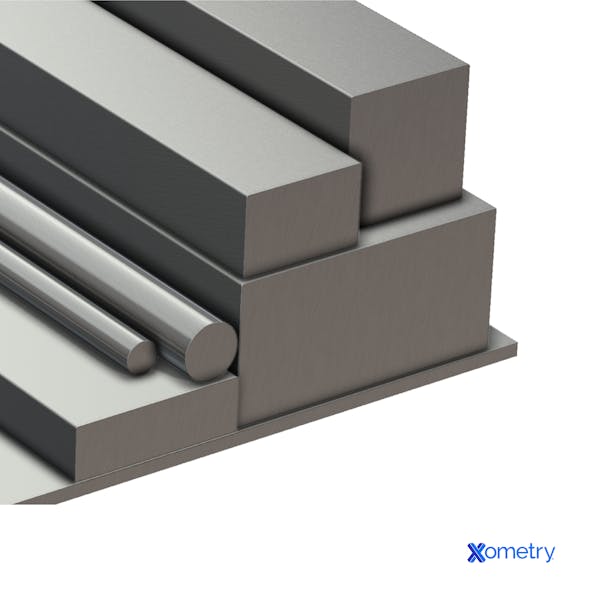
316 stainless steel in bar and rod form.
3. Plate
Perhaps you like the idea of stainless steel sheets but require a thicker width. That’s where stainless steel plates come in handy as these are similar to the aforementioned format but come in widths of 6 mm or thicker. Unsurprisingly, this makes plates a great choice if you’re involved in industries that need chemical processing equipment, structural components for buildings, or pressure vessels. We can also machine plates or use waterjet cutting to cut them into various flat shapes.
4. Hot-Rolled
This format of stainless steel comes from a process called hot rolling, in which you heat the material past the temperature point where it loses its crystalline structure and then reshape it and allow it to cool. This is great if you want stainless steel that can be formed and welded more easily. It’s more involved than other formats and moves molten steel from an argon oxygen decarburization vessel into a cooled continuous caster, where it’ll cool and solidify into a slab shape. You’ll find that the most popular applications for it are in the automotive, industrial equipment, and construction industries.
5. Cold Drawn
The cold-drawn process (also known as cold working and cold rolling) works with stainless steel in a cooler environment than the broiling furnaces of hot-rolled, normally hovering around room temperature. They are normally in rod shape with smaller diameters, and you’d choose this style of processing if smooth finishes and hardness are vital to you. Precision components, shafts, and fasteners are a few kinds of products you could create from this format of 316 stainless steel.
6. Annealed
With annealed stainless steel, you’re putting it through an additional process to maintain its strength and formability while also boosting its corrosion resistance. It’s also called solution treatment steel and focuses on “resetting” or “relieving” the steel so it can be worked on and reshaped once more without cracking or breaking under pressure.
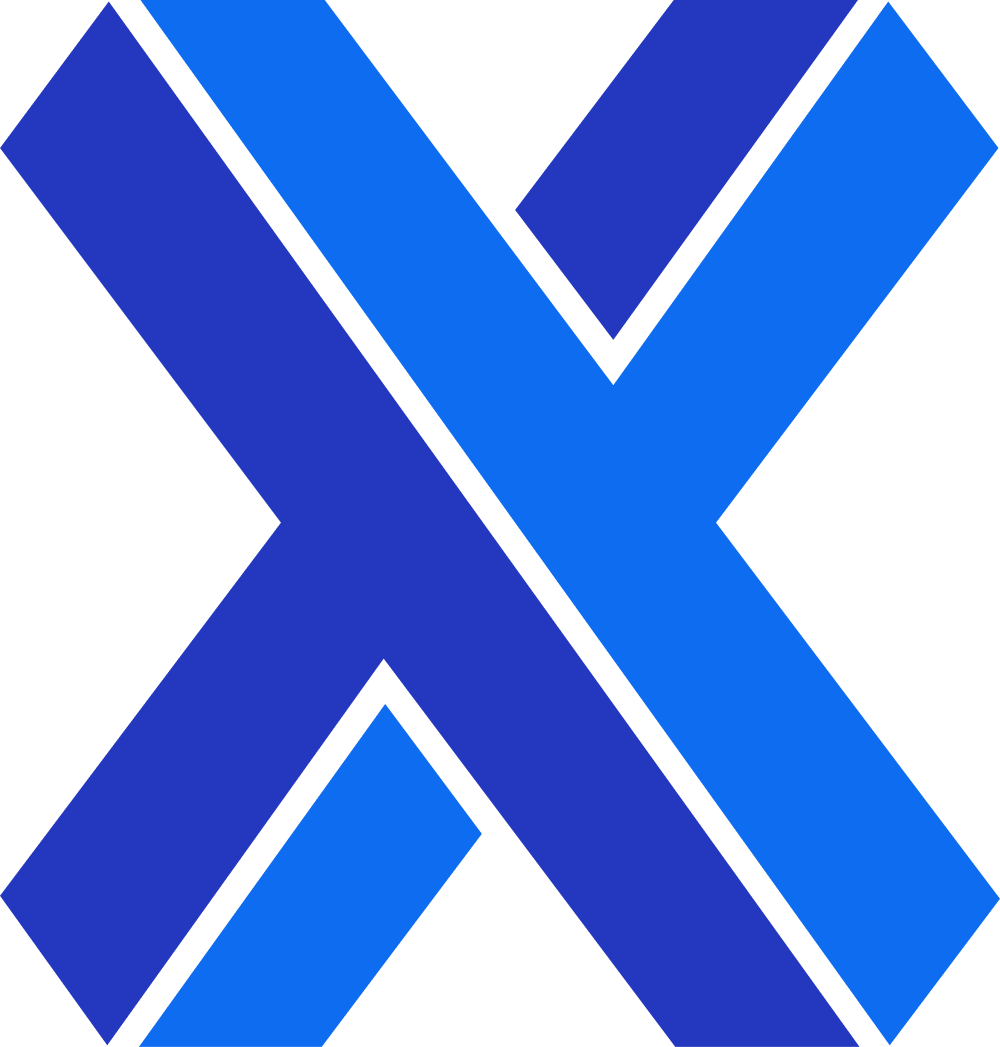
What This Steel Is Used For
Similar to 304, you’ll find that 316 stainless steel is everywhere you look. Here are just a few of the items, appliances, and components it can be transformed into:
- Cookware
- Storage equipment
- Finishes for freezers, dishwashers, fridges, and other appliances
- License plates
- Lightbulb bases
- Boat fittings
- Vessels for holding chemicals and corrosive materials
- Marine hardware
- Offshore structures
- Surgical instruments
- Implant components
Country | Equivalent Grade |
---|---|
Country United States | Equivalent Grade ASTM/UNS S31600 |
Country European Union | Equivalent Grade EN/DIN 1.4401, X5CrNiMo17-12-2 |
Country Germany | Equivalent Grade DIN X5CrNiMo17-12-2 |
Country United Kingdom | Equivalent Grade BS 316S31, BS 316S33 |
Country France | Equivalent Grade AFNOR Z6CND17.11 |
Country Japan | Equivalent Grade JIS SUS 316, JIS SUS 316L |
Country China | Equivalent Grade GB 0Cr17Ni12Mo2 |
Country Russia | Equivalent Grade GOST 08X17H13M2T |
Worldwide Grades of Stainless Steel
Advantages and Disadvantages
Here’s what you should know when it comes to the advantages and disadvantages of 316 stainless steel:
Advantages
- Corrosion resistance: 316 stainless steel is a winner if you need a material with superior corrosion resistance, whether that’s working with chlorides and acids or building structures for marine environments.
- High temperature resistance: This kind of stainless steel won’t crumble under extreme heat, and will remain strong and resistant to corrosion while you subject it to these high temperatures.
- Nontoxic: 316 stainless steel is non-toxic and resistant to bacterial growth, which makes it a great choice if you’re manufacturing food containers or cookware.
- Superb surface finish: You can process many formats of 316 stainless steel to create smooth and sleek finishes, which is ideal for decorative purposes or use in homes.
Disadvantages
- High cost: Thanks to its higher alloy content, 316 can be more expensive than other versions of stainless steel, including the more popular 304.
- Lower machinability and formability: Relative to other kinds of stainless steel, 316 may not be the best choice if you need a high level of machinability and formability. It also isn’t the most thermally conductive material when you compare it to other kinds of metals and alloys.
Other Notes on 316 Stainless Steel
When you’re reading up on different types of stainless steel and researching 316’s benefits, there are a few other things worth noting.
Machinability Rating for 316 Stainless Steel
It’s completely possible to machine and work with 316 stainless steel in all sorts of applications; we machine the material all the time. That being said, you’ll find other grades like 303 stainless steel have a higher machinability rating than the former. This is because 316 is harder (thanks to that molybdenum), so while that in itself can be a positive, it doesn’t help with machinability. This makes machining parts from the material a longer process, which can increase lead time and costs.
316 vs. 304 (8-18) Stainless Steel
As you know, 304 stainless steel (which also goes by 8-18 stainless steel) is the most popular, with 316 being the second most common choice. The biggest difference is the tiny portion of molybdenum content that’s found in 316. Because 304 doesn’t have the 2–3% addition of this element, you’ll find it’s not as corrosion resistant as 316 stainless steel.
It’s clear that 316 stainless steel brings a list of helpful traits when you’re looking to manufacture certain goods and structures. Knowing its composition, properties, and benefits and downfalls will help you determine if it’s the right material for your needs.
How Xometry Can Help
316 stainless steel is just one of the many grades of stainless Xometry offers. Whether you need it precisely machined, sheet cut, bent, or even 3D printed, we have the solutions to meet your needs. Best of all, we offer instant pricing and lead times for custom parts made from stainless steel materials. Simply upload your files to the Xometry Instant Quoting Engine® to get started.
Disclaimer
The content appearing on this webpage is for informational purposes only. Xometry makes no representation or warranty of any kind, be it expressed or implied, as to the accuracy, completeness, or validity of the information. Any performance parameters, geometric tolerances, specific design features, quality and types of materials, or processes should not be inferred to represent what will be delivered by third-party suppliers or manufacturers through Xometry’s network. Buyers seeking quotes for parts are responsible for defining the specific requirements for those parts. Please refer to our terms and conditions for more information.
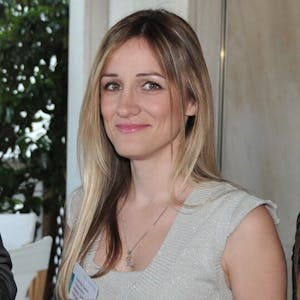