A36 is a low-carbon, mild steel that was formulated by the American Society for Testing and Materials (ASTM) to be strong and tough so it can be used in structural applications, like buildings and bridges. It’s a common go-to in heavy machinery, automotive, and oil and gas. It’s also affordable! Let’s have a look at exactly what it’s made up of, how it’s made, and the various forms it comes in.
What is A36 Carbon Steel?
On A36’s resume, under strengths, you’ll find hardness, ductility, formability, and malleability, among others. Whether you need to put it through welding, punching, grinding, drilling, tapping, or machining, A36 will oblige without a complaint. In addition to all those benefits, A36 is a good magnetic field conductor because it’s paramagnetic (only slightly attracted to magnets), and it won’t let any electromagnetic waves get through, either. With all these perks, it’s little wonder that A36 is the most commonly used carbon steel in its category.
As well as iron and carbon, A36 has various other elements that give it all these wonderful properties. It consists of iron with manganese and carbon as the main alloying elements, and smaller amounts of silicon, copper, sulfur, and phosphorus (we’ll tell you the exact amounts of each a little further down). It’s made in much the same way as other carbon steels; the molten metals are mixed together and then hot rolled. Before the alloying elements are added, the iron ore is first melted in a coal furnace to burn the impurities away. After the other ingredients are thrown in, the molten mixture is put into ingots and left to harden before the hot rolling step of the process.
Its low carbon content makes it quite the task to figure out exactly how much carbon is in every batch made (but we’ve got a good formula for that below). It’s also quite heavy with a low strength-to-weight ratio, and it’s not particularly corrosion resistant (you can thank the lack of nickel and chromium in its composition for that).
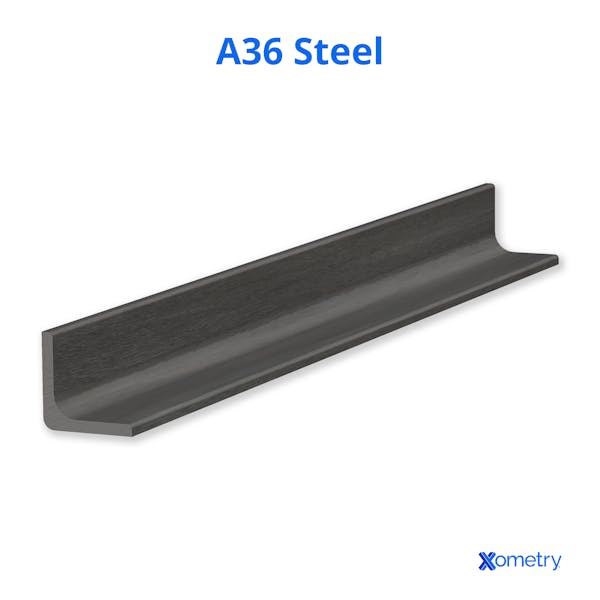
Element | Percentage |
---|---|
Element Iron | Percentage 98% |
Element Manganese | Percentage 1.03% |
Element Carbon | Percentage 0.25%–0.29% |
Element Silicon | Percentage 0.28% |
Element Copper | Percentage 0.20% |
Element Sulfur | Percentage 0.05% |
Element Phosphorous | Percentage 0.04% |
To calculate the volume fraction of carbon in A36 steel, you have to divide the volume of the carbon by the volume of all of the other elements. Here’s the formula:
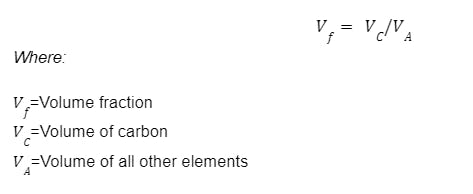
Volume fraction formula.
Property | Value |
---|---|
Property Density | Value 2.84 lb/in^3 |
Property Yield strength | Value 36,259 psi |
Property Hardness | Value 67–83 Rockwell |
Property Magnetism | Value Ferrous magnetic |
Property Machinability | Value 72% |
Property Cutting speed | Value 120 ft. per minute |
Property Melting point | Value Between 2,590–2,670°F |
Property Specific heat capacity | Value 0.11 Btu/lb 348 Btu-in/hr-ft2 F |
Property Thermal conductivity | Value 348 Btu-in/hr-ft2 F |
A36 Carbon Steel Forms
These are the common forms that ASTM A36 carbon steel can be found in and how they’re used.
Sheet: This is between 0.018” and 0.250” thick and used for vehicle bodywork, walls/bulkheads, or build tanks.
Bar: These are used in structural applications, like concrete reinforcement, because concrete has a high compressive strength and a low tensile strength.
Plate: Similar to sheets, plates are 0.25” or more in thickness, but are used for structural applications (whereas sheets just look pretty).
Hot-rolled: This is the most common form and creates a rougher surface finish. It’s done at really high temperatures (1,562–2,192°F), and puts strain on the steel to ramp up the dislocation density of the steel’s microstructure. This results in work hardening and creates grain elongation (stretching out the tiny grains that make up the metal).
Annealed: This also uses high heat of 1,550–1,600°F and involves heating and then cooling the steel slowly to remove impurities and make it less brittle. The process reduces the steel’s hardness but also helps reduce internal stress, making it less likely to cause damage to cutting or shaping tools.
Cold-drawn: Stronger and harder than hot-rolled steel, cold-drawn A36 is made at a lower temperature and can be made into bars, tubes, spindles, wires, shafts, and other items that need to have a nice aesthetic.
Equivalent International A36 Grades
While it’s difficult to exactly match A36 with the equivalent international standards (each will no doubt have a slightly different composition and properties), we list some comparable grades in the table below.
Country standard | Equivalent grade |
---|---|
Country standard European | Equivalent grade S235JRG2 |
Country standard German | Equivalent grade St 37-2 |
Country standard Canadian | Equivalent grade 260W |
Country standard Japanese | Equivalent grade SS400 |
Country standard Indian | Equivalent grade E250 |
Country standard Chinese | Equivalent grade Q235B |
Country standard ISO | Equivalent grade E 235 |
A36 vs. 1018 Carbon Steel
These two steels are quite similar, but 1018 has a lower carbon content (around 0.18%), is stronger, and more easily machinable. 1018 is great for rotating parts, but A36 is chosen for things like I-beams and cables. Since A36 is typically hot rolled, it’s cheaper to make than 1018, which is hot rolled and needs quite a lot of manual labor. If you need something economical and you’re not after super high strength and machinability, A36 is ideal. Otherwise, go with 1018.
A36 vs. A572 Steel
ASTM carbon steels A36 and A572 have most of the same alloying elements, just in different amounts—something that changes some of the properties, i.e., yield and tensile strength. A572 has more manganese and silicon, which makes it stronger than A36 and able to bear more weight as it’s a high-strength low-alloy (HSLA) steel.
How Xometry Can Help
We hope you enjoyed learning about A36 carbon steel and that we answered all your queries. To learn more about it, contact one of our reps. We also offer many related manufacturing services, and it’s easy to get a free and instant quote—simply upload your designs to the Xometry Instant Quoting Engine®.
Disclaimer
The content appearing on this webpage is for informational purposes only. Xometry makes no representation or warranty of any kind, be it expressed or implied, as to the accuracy, completeness, or validity of the information. Any performance parameters, geometric tolerances, specific design features, quality and types of materials, or processes should not be inferred to represent what will be delivered by third-party suppliers or manufacturers through Xometry’s network. Buyers seeking quotes for parts are responsible for defining the specific requirements for those parts. Please refer to our terms and conditions for more information.
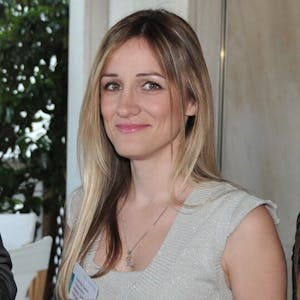