Austenitic stainless steels are versatile and popular materials, known for their corrosion resistance, high-temperature strength, and suitability for the fabrication process. Austenitic stainless steel is widely used across most higher-specification industrial and domestic applications. This preferential selection directly results from its exceptional corrosion resistance, high ductility, and generally good mechanical properties.
This article will further discuss austenitic stainless steel, its definition, types, grades, properties, and applications
What Is Austenitic Stainless Steel?
Austenitic stainless steel is one of the four main families of stainless steels, alongside the ferritic, martensitic, and duplex classifications. It consists of several materials, including: iron, chromium, nickel, manganese, and carbon. There are a large number of austenitic stainless steel grades, but the most common are 304 and 316.
The austenitic structure is a face-centered cubic (FCC) crystalline lattice, a consequence of which is the steel's unique properties. This structure also renders austenitic stainless steel non-magnetic, even though it primarily consists of iron, chromium (which is paramagnetic at elevated temperatures), and nickel (which is ferromagnetic).
What Is the History of Austenitic Stainless Steel?
Harry Brearley, an English metallurgist, is often credited with the discovery of stainless steel in 1913. He was working for Firth Brown Laboratories in Sheffield, England, trying to develop more-erosion-resilient steel for gun barrels. While experimenting with various compositions, he noticed that steel containing about 12.8% chromium exhibited remarkable resistance to rust and staining. This accidental discovery initiated the stainless steel era.
Independently, the German industrialist Friedrich Krupp and his metallurgy research team were also working on chromium-modified steel development around 1912–14. They managed to create high-chromium stainless steel, calling it "V2A" (meaning "Versuchsschmelze 2 Austenit" or "Experimental Melt 2 Austenite"). lt has similar properties to Brearley's material.
What Is Austenitic Stainless Steel Made Of?
Austenitic stainless steel’s primary constituent is Iron (Fe), enhanced with often significant proportions of key elements. Chromium is the primary alloying agent, accounting for between 16% and 26% of the steel, by mass. Nickel is another significant alloying agent ranging from 6% to 22%. Manganese is often added; its proportion typically falls between 2% and 6%. Carbon content is low, usually below 0.08%. Secondary alloying elements are also commonly present in smaller quantities such as: molybdenum, nitrogen, silicon, phosphorus, and sulfur.
How Are Austenitic Austenitic Stainless Steels Made?
Austenitic stainless steels are made through a process that involves several stages. The specific manufacturing process stages can vary depending on the grade of austenitic stainless steel being produced and the equipment used by the manufacturer. The process begins with adding the raw materials in the required proportions in an electric arc furnace or an induction furnace. Reducing agents are added to extract contaminants and oxides and render them as slag that floats to the top of the crucible. Once liquified, the liquid steel is further refined by processes such as Argon Oxygen Decarburization (AOD) or Vacuum Oxygen Decarburization (VOD, often referred to as vacuum arc remelting). The furnace is then tapped and the refined molten steel is poured into large ingots or continuous casting molds. The cast material is reheated and then passed through a series of hot roll stages. This is done to reform any inclusions or cavities, reduce the thickness of the steel and shape it into plates, sheets, or bars. After hot rolling, if it’s in its final, market-ready form then the steel will likely undergo annealing. Some grades of austenitic stainless steel are finished by cold rolling to further reduce the thickness, improve size precision and improve the surface finish. The cold-rolled stainless steel is pickled in an acid bath to remove any surface scale or impurities. Passivation, a process using acid or other chemicals, is then applied to promote the formation of a uniform, blemish-free protective oxide layer on the steel surface. The stainless steel coils, sheets, or plates are further processed and cut to the required dimensions, depending on the market need.
What Are the Characteristics of Austenitic Stainless Steel?
Austenitic stainless steels possess a characteristic group of distinct properties including:
- Excellent corrosion resistance, particularly resisting corrosion in acidic, alkaline, and chloride-laden environments.
- Non-magnetic, when annealed.
- Highly formable by a wide spectrum of metalworking processes.
- Good cryogenic behavior, retaining toughness and ductility at very low temperatures.
- Good high-temperature strength—some grades maintain good mechanical properties, including strength and creep resistance, at elevated temperatures.
- Hygienic and rejecting of contaminants; the smooth, non-porous, and unreactive surface of austenitic stainless steels makes them easy to clean and maintain.
- Good weldability, in the low-carbon content (such as 304L and 316L) grades, displaying low sensitization (carbide formation at grain boundaries).
- Unlimited recycling potential, without any loss of properties.
What Is the Color of Austenitic Stainless Steel?
The color of austenitic grades reflects the chromium and nickel content, ranging from dull to bright silver, depending on the surface condition.
What Does Austenitic Stainless Steel Look Like?
Austenitic steels look like bright metal. It has a silver color that ranges from textured, through matte to mirror finish, depending on the degree of surface modification.
What Are the Different Types of Austenitic Stainless Steel Grades?
Austenitic stainless steels are a wide family with some extreme diversity of properties. Listed below are the different types:
1. 304 Stainless Steel
304 stainless steel is often referred to as "18-8" stainless steel due to its main alloying constituents being 18% chromium and 8% nickel. It is one of the most widely used and versatile grades, known for its excellent corrosion resistance, formability, and hygienic properties. Aside from chromium and nickel, 304 contains manganese (2% max.), and a small amount of carbon, silicon, phosphorus, and sulfur. 304 stainless steel finds applications across all industries and product sectors, including: storage tanks, worktops, sinks, cookware, tanks, piping, surgical instruments, and implant materials.
2. 316 Stainless Steel
316 stainless steel is composed of chromium (16–18%), nickel (10–14%), and molybdenum (2–3%). This provides enhanced corrosion resistance, particularly in chloride-rich environments such as: marine and swimming pool equipment. Stainless steel 316 is non-magnetic in the annealed condition, offers superior corrosion resistance compared to 304, exhibits good high-temperature strength and creep resistance, retains its toughness and ductility at low temperatures, and is hygienic and easy to clean.
316 stainless steel is widely used in applications such as: marine hardware, boat fittings, offshore structures, reactors, heat exchangers, storage tanks, medical instruments, surgical implants, pharmaceutical processing equipment, exterior cladding, handrails, and structural components.
3. 303 Stainless Steel
303 stainless steel is free-machining stainless steel. It contains sulfur (0.15–0.35%) to improve its machinability but this results in reduced corrosion resistance, compared to other austenitic stainless steel grades. Aside from sulfur, the typical composition of 303 alloys is: 17–19% chromium, 8–10% nickel, 1% silicon, and small amounts of carbon, manganese, and phosphorus. SS 303 is known for its improved machinability, good corrosion resistance in mild environments, lack of magnetism, and ability to retain good ductility and formability. It is commonly used in applications in which machinability is a primary requirement, such as: screw machining, shafts and pins, valve and pump components, bushings and bearings, as well as nuts and bolts.
4. 321 Stainless Steel
321 stainless steel is a grade of stainless steel that is stabilized with titanium (0.4–0.7%). The addition of titanium provides improved weldability, resistance to sensitization, and intergranular corrosion at elevated temperatures. Other properties of 321 SS are: excellent resistance to general corrosion, maintaining good mechanical properties and strength at elevated temperatures, good ductility and formability, and being easily weldable using common welding methods, such as TIG or MIG welding.
321 stainless steel is commonly used in applications in which high-temperature resistance and corrosion resistance are essential, such as: components in aircraft exhaust systems, jet engine parts, afterburners, heat exchangers, exhaust systems, pipes, fittings, and vessels used in the oil and gas industry.
5. 310 Stainless Steel
310 steel is a grade that was specifically developed for high-temperature applications. It contains an elevated proportion of chromium (24–26%) and nickel (19–22%), providing excellent oxidation resistance and high-temperature strength. SS 310 is known for its: exceptional strength and resistance to deformation at elevated temperatures, good general corrosion resistance in many environments, particularly in mildly acidic and alkaline conditions, good ductility and formability, and is more readily weldable than most austenitic stainless steels, as it’s largely immune to sensitization.
310 stainless steel is primarily used in applications that involve exposure to intermittent or continuous high-temperature environments and elevated risk of oxidation. Examples are: furnace components, trays, baskets, radiant tubes in heat-treating furnaces, tubes, pipes, and vessels in hot processes in chemical plants, polymerization chambers, gas turbines, steam turbines, boiler parts, and exhaust systems.
6. 904L Stainless Steel
904L stainless steel is highly resistant to corrosion, particularly in aggressive environments containing sulfuric acid, chlorides, and other corrosion sources. It contains high levels of chromium (19–23%), nickel (23–28%), and molybdenum (4–5%), delivering exceptional corrosion resilience. 904L stainless steel is also non-magnetic, delivers elevated strength and toughness, retains good ductility and formability, and exhibits good weldability.
904L stainless steel is primarily used in applications in which particularly high levels of corrosion resistance are required such as: equipment, pipes, and storage tanks exposed to corrosive chemicals and acids, offshore platforms, heat exchangers, and pipes that come into contact with seawater and corrosive environments, boat and ship components exposed to saltwater, equipment used in the production and handling of pharmaceuticals, and in digester vessels and bleach plants.
7. 347 Stainless Steel
347L stainless steel is a stabilized stainless steel that contains niobium and tantalum (0.6%). These elements improve the steel's resistance to sensitization and intergranular corrosion, especially in high-temperature environments. The typical composition of 347L is 17–19% chromium, 9–13% nickel, 2% manganese, and small amounts of carbon, phosphorus, silicon, and sulfur. 347L stainless steel offers good general corrosion resistance and enhanced resistance to sensitization and intergranular corrosion, particularly in high-temperature environments. It also maintains good mechanical properties and strength at elevated temperatures, retains good ductility and formability common to the austenitic grades, and is readily weldable using common welding methods.
347L stainless steel is primarily used in applications such as: heat exchangers, furnace components, tubing for oil refining and petrochemical industries, exhaust manifolds and other components in jet and piston engines and aircraft components, pipes, fittings, and equipment used in corrosive chemical environments.
What Grade of Austenitic Stainless Steel Is Best?
There is no one grade of austenitic stainless steel that is best for all applications. Selection depends upon a number of factors. In many cases, the best choices are quite clear because of one performance metric. For example, 304 is generally the best choice for parts that require cryogenic strength, while 321 is best for parts that need good weldability.
What Are the Properties of Austenitic Stainless Steel?
Austenitic stainless steels (generally belonging to the 200 and 300 series definitions) are a broad family. For example, the higher nickel content steels in the 300 series (plus 904L as a series outlier) have the following general properties:
- Non-magnetic.
- Excellent corrosion resistance.
- Easily weldable.
- High strength at elevated temperature.
- Improved machinability.
Austenitic stainless steels in the 200 series use low nickel levels and trigger the conversion from ferritic to austenitic microstructure using manganese. This composition opens up another set of property variants. It is important to note that various advantageous physical and chemical properties are induced by variations in alloying agents.
What Are the Physical Properties of Austenitic Stainless Steel?
The broad family of austenitic stainless steels possesses a useful range of properties. Some of its physical properties include:
- Generally weldability by all normal processes, with particular alloys suffering lower carbide sensitization.
- Excellent formability, fabrication capability, and ductility (in the annealed state).
- Great hygiene characteristics and resistance to contamination/staining.
- Good retention of properties at high temperatures and in some cases outstanding cryo temperature performance.
- Non-magnetic, in the annealed state.
- Hardenable by cold work only, with some magnetic response in the work-hardened state.
What Are the Chemical Properties of Austenitic Stainless Steel?
These steels also offer some attractive chemical properties which are listed below:
- Face-centered cubic microstructure.
- Inertness, or lack of chemical interaction, with a wide range of environments.
- Universally high corrosion resistance to pH neutral, mildly acid/alkaline, and wet environments.
- Selected grades offer extreme corrosion resistance in highly acid/alkaline and high chloride environments.
- The tendency in some alloys to carbide formation at crystal boundaries weakens corrosion resilience. This is resisted by the addition of stabilizing metals that resist this chemical process.
What Are the Applications of Austenitic Stainless Steel?
Austenitic stainless steels find very broad applications in the more demanding end-use cases. These applications are listed below:
1. Medical Equipment
Austenitic stainless steels are widely utilized in the medical equipment sector, due to their attractive combination of properties. This material offers cleanability, high corrosion resistance, biocompatibility, and resilience under sterilization by the most aggressive means. Some applications include: implants and prostheses (hip and knee implants, plates, screws, and dental implants), intrusive medical devices (endoscopes, catheters, and syringes), general hospital equipment (surgical tables, chairs, trays, cabinets, and medical carts), and sterilization tools, autoclaves, and other sterilization equipment.
2. Power Generation
The beneficial properties of austenitic stainless steels are extensively applied in power generation and related applications. For example, steam turbines and ancillary equipment generally use 304 and 316. Boiler tubes and heat exchangers also make extensive use of 304, 316, and 321 alloys, exploiting their resistance to corrosion/oxidation at elevated temperatures. Other applications include: condensers in power plants, gas turbines, exhaust systems, flue gas desulfurization (FGD) systems, and in water treatment plants.
3. Architectural Structures
Austenitic stainless steel alloys are extensively used in architectural structures because of their appropriate and beneficial properties, such as aesthetic qualities and corrosion resistance. They’re ideal for both indoor and outdoor applications, such as: exterior cladding, handrails and balustrades, an architectural mesh of perforated sheet and expanded metal, as well as sculptures and art installations.
4. Chemical Processing Equipment
Some austenitic stainless steels are universally applicable to chemical processing equipment due to their exceptional corrosion resistance in aggressive and hot chemical environments. Some examples of their applications are: storage tanks, pressure vessels, pipes, heat exchangers (both tube and plate), agitators and mixers in chemical reactors and mixing vessels, as well as valves, distillation equipment, filters, and fittings used in chemical processing equipment to control the flow of corrosive fluids.
5. Kitchenware and Appliances
Austenitic stainless steel alloys are a popular material choice for kitchenware and appliances due to their excellent combination of properties, suitable for various culinary applications. Cookware is very commonly made from 304 and 316 because of the material's corrosion resistance, durability, and non-reactivity with food. Other examples include: cutlery, kitchen sinks, refrigerators, dishwashers, ovens, cook pots, mixing bowls, and measuring cups.
6. Aerospace and Automotive Components
Austenitic stainless steels are used in various aerospace applications for their unique combination of properties, making them optimal for high-stress, high-temperature, and life-critical components in aircraft and spacecraft. Certain grades, particularly 304 and 321, are used in aircraft exhaust systems. Other applications include: components within hydraulic, pneumatic, and fuel systems, turbine blades, compressor discs, exhaust nozzles, bolts, nuts, coolant tubing, and valves, aircraft frames and structures, wing leading edges, flap actuators, and landing gear components.
What Are the Benefits of Austenitic Stainless Steel?
Austenitic stainless steels offer various significant benefits that render them highly desirable across all industries. Some of the benefits include:
- Corrosion resistance, from good to outstanding, is available across the alloy range.
- High strength at elevated temperatures, with some alloys displaying remarkable capability.
- Aesthetic appeal, accepting attractive textured or polished surfaces that endure through heavy use.
- The entire family is non-magnetic when annealed and only lightly magnetic when fully work hardened.
- The alloys are ideal for providing hygienic surfaces for all sectors.
- All of the alloys are ductile and malleable, and work hardening only slowly.
- Certain low-carbon, elevated-nickel alloys are highly biocompatible.
What Are the Limitations of Austenitic Stainless Steel?
Austenitic stainless steels also have performance limitations that represent critical limitations in specific applications. Some of the limitations are:
- High cost, which is a result of the heavy use of relatively expensive metals such as nickel, manganese, tantalum, and titanium.
- While selected alloys in the group offer good high-temperature performance, there are competing materials that can considerably outperform in this regard.
- Sensitization and weld sensitization are big issues with some of these alloys.
- The inability to heat treat these steels for hardening limits their applications.
- The need to anneal to minimize magnetic sensitivity can be an extra burden in manufacturing.
- These alloys are very poor-bearing materials, suffering from adhesive wear or galling.
- In high chloride environments, chloride-induced stress corrosion can result in cracking and pitting. This results in premature failure of wet-area marine parts such as fuel tanks.
Why Use Austenitic Stainless Steel?
The selection of austenitic stainless steels for particular applications is a delicate balance between the relative benefits and consequent weaknesses of the various alloys. In many applications, they are the ideal option, offering a great balance between strength, corrosion resilience, processability, cosmetics, and cost. If cost sensitivity or cosmetic requirements are less critical, or strength or component weight is more critical, other options can be considered. On balance, austenitic stainless steels are the answer for the vast majority of moderately high-temperature, cryogenic, or corrosion-risk applications.
How Long Will Austenitic Stainless Steel Last?
It depends. Austenitic stainless steel is a highly durable material family that can serve in appropriate applications for indefinite use. Failure modes for components made from these materials fall into broad categories that can generally be considered out-of-specification use. For example, a fracture may result from periodic or extreme overstress that the component design did not take into account. Fatigue is also a failure mode that results from cyclic loads that approach the design limits of the component and cause progressive failure by crack propagation from stress concentrators and flaws. This can be amplified by exceeding the heat tolerance of the material.
Is Austenitic Stainless Steel Better Than Stainless Steel?
Austenitic stainless steel IS stainless steel. In most regards, however, austenitic steels exceed the average performance of the typical stainless steels of other families such as martensitic, and ferritic. In terms of corrosion resistance, austenitic stainless steels offer among the best properties. In strength, they tend to be slightly lower strength than martensitic stainless steels but maintain their strength at higher operational temperatures than other stainless steels. Austenitic stainless steels are generally more weldable than other types. These steels offer better formability and machining properties than most other stainless steel types.
Can Austenitic Stainless Steel Get Rusted?
Yes, austenitic stainless steel can rust. Rust is specifically brown iron oxide. These steels are susceptible to chloride and acid attack, which can result in highly localized pitting corrosion. In marine applications, seawater exposed components of a lower cost or poorly selected grade can develop brown staining that is iron oxide, resulting from chloride (salt) attack.
Will a Magnet Stick to Austenitic Stainless Steel?
No, austenitic stainless steels have intrinsically low to zero susceptibility to magnetic fields. When the material has been “worked” either by forming or machining, crystalline structural changes occur that create a low-grade response to magnets.
Is Austenitic Stainless Steel an Alloy or Metal?
Austenitic stainless steels are alloys. Steel itself is an alloy of iron and carbon, plus a range of other intentional and accidental additions. Austenitic steels are alloys containing (in addition to iron): low carbon levels introduced from the steel that is the primary constituent, chromium, which makes the material harder and forms the chromium oxide surface barrier that makes the material “‘stainless”, and nickel or managanese that induces the austenitic crystalline structure. Nickel also enhances the corrosion resistance of the alloys. To learn more, see our guide on Alloy Properties.
What Is the Difference Between Austenitic Stainless Steel and Ordinary Steel?
Austenitic stainless steel costs more and has higher corrosion resistance and maximum service temperature than medium carbon steel. On the other hand, medium carbon steel has an excellent hardenability as opposed to the poor hardenability of austenitic steel. To learn more, check out our article on Ordinary Steel.
What Are Other Types of Stainless Steel Beside Austenitic Stainless Steel?
Three other stainless types, for example, are: martensitic stainless steels, ferritic stainless steels, and duplex stainless steels.
What Is the Difference Between Austenitic Stainless Steel and Martensitic Stainless Steel?
Austenitic stainless has very high corrosion resistance compared to the moderate quality of martensitic stainless steel. Austenitic’s cost and max service temperature are also a lot higher than that of martensitic steel. But martensitic steel has moderate hardenability compared to austenitic steel’s poor hardenability.
Summary
This article presented austenitic stainless steel, explained it, and discussed its composition and various applications. To learn more about copper, contact a Xometry representative.
Xometry provides a wide range of manufacturing capabilities and other value-added services for all of your prototyping and production needs. Visit our website to learn more or to request a free, no-obligation quote.
Disclaimer
The content appearing on this webpage is for informational purposes only. Xometry makes no representation or warranty of any kind, be it expressed or implied, as to the accuracy, completeness, or validity of the information. Any performance parameters, geometric tolerances, specific design features, quality and types of materials, or processes should not be inferred to represent what will be delivered by third-party suppliers or manufacturers through Xometry’s network. Buyers seeking quotes for parts are responsible for defining the specific requirements for those parts. Please refer to our terms and conditions for more information.
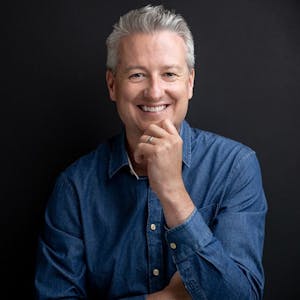