Copper-nickel alloys (CuNi) are used extensively in various industries and applications. Composed primarily of copper and nickel, these alloys possess unique properties that make them highly valued across sectors.
This article aims to provide a comprehensive overview of copper-nickel alloys, exploring their definition, diverse applications, and benefits. Additionally, it will delve into the potential drawbacks associated with their use.
What Is a Copper Nickel Alloy (CuNi)?
Copper-nickel alloys, also known as CuNi or cupronickel alloys, are a group of alloys consisting primarily of copper and nickel, with small amounts of other elements added to enhance such properties as strength, corrosion resistance, hardenability, weldability, and castability. The most common types of CuNi alloys are the 90/10 and 70/30 compositions. The 90/10 alloy contains 90% copper and 10% nickel, while the 70/30 alloy contains 70% copper and 30% nickel. There are also high-strength copper-nickel-based alloys containing aluminum or tin, such as Cu-Ni-Al and Cu-Ni-Sn, which are designed for improved mechanical performance in specific applications. For more information, see our article All About Nickel Alloys.
What Is the Importance of Copper Nickel (CuNi) Alloys?
Copper-nickel alloys are significant because of their unique combination of properties. These properties include exceptional corrosion resistance, high thermal stability, moderate electrical conductivity, good mechanical strength, antibacterial properties, and long-term durability, enabling their widespread use across diverse industries and applications. For example, CuNi alloys maintain their mechanical properties at elevated temperatures, making them well-suited for heat exchangers, power generation equipment, and other high-temperature environments. CuNi’s electrical conductivity makes it an important material in electrical and electronic applications such as wiring, connectors, and terminals.
When Did Copper Nickel Alloys Start Being Used?
Cupronickel has a long history dating back over a thousand years. Its earliest known use can be traced to China in around 300 BCE. Chinese records detail the process of creating "white copper" by heating and mixing copper, nickel, and saltpeter.
Nickel-containing copper alloys were also used in some ancient coinage, such as in Greece, though systematic use of cupronickel coins became more common in the 19th century. In later years, cupronickel underwent a "rediscovery" in Europe through alchemical experiments. During the period following the Civil War in the United States, cupronickel was employed by the US Mint to stamp three-cent and five-cent pieces. As silver grew scarce during the war, cupronickel served as an alternative. Finally, in recent decades, cupronickel has been used as cladding or coating for American 50-cent pieces, quarters, and dimes.
What Are the Advantages of Copper Nickel Alloys?
Copper-nickel alloys offer several advantages that make them valuable in numerous applications. Some key benefits are listed below:
- Possess exceptional resistance to corrosion, particularly in marine and seawater environments.
- Copper-nickel alloys can withstand thermal cycling and exhibit good resistance to oxidation, contributing to their durability in high-temperature environments.
- Can be tailored to meet specific requirements by adjusting the composition and proportions of copper, nickel, and other alloying elements.
- Can be easily fabricated and joined using common techniques like welding, brazing, and soldering.
- Exhibit resistance to biofouling, the accumulation of organisms on submerged surfaces, which is advantageous in marine environments.
- The corrosion resistance, strength, ductility, and durability in a wide range of environments of CuNi alloys contribute to their long service life and low maintenance requirements.
- They are known for their recyclability, making them environmentally friendly options.
What Are the Disadvantages of Copper Nickel Alloys?
Like any material, copper-nickel alloys also have certain disadvantages, such as:
- Copper-nickel alloys can be more expensive than other common alloys due to the higher cost of copper. Nickel price fluctuations can impact the overall cost of copper-nickel materials.
- Copper-nickel alloys are generally considered less machinable than some other common alloys, such as stainless steel or aluminum alloys. The presence of copper in these alloys can cause higher tool wear and reduced cutting speeds. Machining homogeneous Cu-Ni alloys proves challenging due to their high toughness, resulting in poor machinability, particularly in their soft state. These alloys tend to produce long, pliable chips, leading to frequent issues with chip removal and adversely affecting the achievable surface quality.
How Are Copper-Nickel Alloys Processed?
Copper-nickel alloys undergo various specific processing techniques depending on the intended application and the desired final product. Some common methods used are listed below:
- Copper and nickel are melted in appropriate proportions. The metals are melted together in a furnace or other suitable equipment, ensuring proper mixing and homogenization. Other alloying elements or trace elements may also be added to enhance specific properties or meet particular requirements.
- After the alloying process, the molten copper-nickel alloy is cast into desired shapes and sizes. Casting methods include sand casting, investment casting, and continuous casting.
- Copper-nickel alloys can be hot-worked to shape them into desired forms. Hot working methods include hot rolling, hot extrusion, and hot forging.
- Copper-nickel alloys can also be cold-worked at room temperature to enhance their mechanical properties and achieve specific shapes. Cold working methods include cold rolling, cold drawing, and cold forming.
- Heat treatment is often performed on copper-nickel alloys to optimize their properties. Common methods include annealing and, for specific high-strength grades, solution treatment and stress relieving.
- After the primary processing steps, copper-nickel alloys may undergo machining operations such as cutting, drilling, milling, and turning to achieve specific dimensions and surface finishes. Finishing operations like polishing, grinding, and coating may also be performed to enhance the appearance and protect the surface of the alloy.
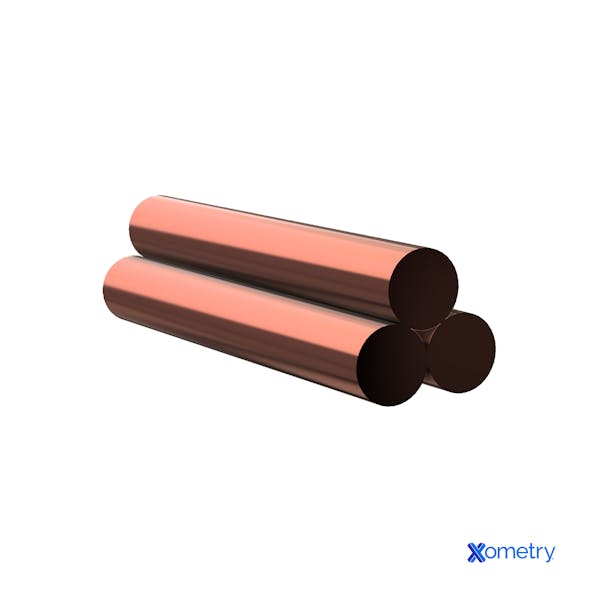
Copper Nickel Alloy Rods
What Are the Common Applications of Copper Nickel (CuNi) Alloys?
Listed below are some of the common applications of CuNi alloys:
1. Pipe Nipples
Copper-nickel alloys are commonly used in pipe nipples, especially in industries where corrosion resistance is crucial. They are often used in piping systems that transport corrosive fluids, such as seawater or brine. Their resistance to corrosion and biofouling (see Advantages) makes copper-nickel pipe nipples suitable for marine environments and other harsh conditions.
2. Cooling Loops
Copper-nickel alloys are utilized in cooling loops, particularly in industries such as power generation, chemical processing, and oil refining. Their corrosion and biofouling resistance make them ideal for cooling systems that circulate seawater or brackish water. They help maintain the efficiency and longevity of cooling equipment while reducing the risk of corrosion-related failures.
3. Marine Hardware
Copper-nickel alloys are widely used in marine hardware because of their proven durability in seawater conditions. They are employed in various marine applications, including shipbuilding, offshore structures, and underwater equipment. Examples of marine hardware made from copper-nickel alloys include seawater valves, pumps, condensers, strainers, and sheathing for ship hulls.
4. Desalination
Copper-nickel alloys are well-suited for desalination plants, particularly in multi-stage flash (MSF) and multiple-effect distillation (MED) systems, where they are used in tubing and heat exchangers. Desalination involves the removal of salt and other impurities from seawater to obtain fresh water. Their resistance to seawater corrosion makes copper-nickel alloys a reliable choice in desalination processes.
5. Seawater Piping Systems
Copper-nickel alloys are widely employed in seawater piping systems, especially for transporting corrosive seawater or brackish water. They are used in a range of applications, including seawater intake systems, cooling water systems, and fire protection systems. Copper-nickel pipes and fittings provide durable and reliable performance in corrosive seawater environments (see Advantages).
What Is the Strength Range of Copper-Nickel Alloys?
The strength of copper-nickel alloys can be influenced by cold work and alloy composition. Cold working increases dislocation density, which strengthens the alloy, especially its yield strength, at temperatures below the annealing and recrystallization points. Alloy composition offers several avenues of strengthening for copper-nickel alloys: simple solid solution strengthening, spinodal decomposition strengthening, and precipitation (age) hardening accomplished through heat treatments.
What Is the Electrical Resistivity Range of Copper-Nickel Alloys?
The electrical resistivity of different CuNi alloys is given in Table 1 below:
Alloy Identification Symbol | 20 °C (Electrical resistivity in Ω·mm2/m) | 100 °C (Electrical resistivity in Ω·mm2/m) | 200 °C (Electrical resistivity in Ω·mm2/m) | 300 °C (Electrical resistivity in Ω·mm2/m) | 400 °C (Electrical resistivity in Ω·mm2/m) | 500 °C (Electrical resistivity in Ω·mm2/m) |
---|---|---|---|---|---|---|
Alloy Identification Symbol CuNi2 | 20 °C (Electrical resistivity in Ω·mm2/m) 0 | 100 °C (Electrical resistivity in Ω·mm2/m) 0.057 | 200 °C (Electrical resistivity in Ω·mm2/m) 0.064 | 300 °C (Electrical resistivity in Ω·mm2/m) - | 400 °C (Electrical resistivity in Ω·mm2/m) - | 500 °C (Electrical resistivity in Ω·mm2/m) - |
Alloy Identification Symbol CuNi6 | 20 °C (Electrical resistivity in Ω·mm2/m) 0.1 | 100 °C (Electrical resistivity in Ω·mm2/m) 0.107 | 200 °C (Electrical resistivity in Ω·mm2/m) 0.114 | 300 °C (Electrical resistivity in Ω·mm2/m) 0.123 | 400 °C (Electrical resistivity in Ω·mm2/m) - | 500 °C (Electrical resistivity in Ω·mm2/m) - |
Alloy Identification Symbol CuNi10 | 20 °C (Electrical resistivity in Ω·mm2/m) 0.15 | 100 °C (Electrical resistivity in Ω·mm2/m) 0.156 | 200 °C (Electrical resistivity in Ω·mm2/m) 0.162 | 300 °C (Electrical resistivity in Ω·mm2/m) 0.169 | 400 °C (Electrical resistivity in Ω·mm2/m) 0.175 | 500 °C (Electrical resistivity in Ω·mm2/m) - |
Alloy Identification Symbol CuNi23-Mn | 20 °C (Electrical resistivity in Ω·mm2/m) 0.3 | 100 °C (Electrical resistivity in Ω·mm2/m) 0.308 | 200 °C (Electrical resistivity in Ω·mm2/m) 0.315 | 300 °C (Electrical resistivity in Ω·mm2/m) 0.323 | 400 °C (Electrical resistivity in Ω·mm2/m) 0.331 | 500 °C (Electrical resistivity in Ω·mm2/m) 0.339 |
Alloy Identification Symbol CuNi30-Mn | 20 °C (Electrical resistivity in Ω·mm2/m) 0.4 | 100 °C (Electrical resistivity in Ω·mm2/m) 0.404 | 200 °C (Electrical resistivity in Ω·mm2/m) 0.41 | 300 °C (Electrical resistivity in Ω·mm2/m) 0.417 | 400 °C (Electrical resistivity in Ω·mm2/m) 0.424 | 500 °C (Electrical resistivity in Ω·mm2/m) 0.432 |
Alloy Identification Symbol CuNi44 | 20 °C (Electrical resistivity in Ω·mm2/m) 0.49 | 100 °C (Electrical resistivity in Ω·mm2/m) 0.49 | 200 °C (Electrical resistivity in Ω·mm2/m) 0.49 | 300 °C (Electrical resistivity in Ω·mm2/m) 0.49 | 400 °C (Electrical resistivity in Ω·mm2/m) 0.49 | 500 °C (Electrical resistivity in Ω·mm2/m) 0.49 |
Table Credit: https://www.copper.org/applications/marine/cuni/properties/DKI_booklet.html#gen
How Is the Corrosion Resistance of Copper Nickel Alloy?
Copper-nickel (CuNi) alloys have very good corrosion resistance, especially against seawater. The corrosion resistance of CuNi alloys is primarily attributed to the protective oxide layer that forms on their surface when exposed to air or moisture. This oxide layer acts as a barrier, preventing further corrosion even in aggressive chloride-rich environments like seawater.
What Are the Physical Properties of Copper Nickel Alloys?
The physical properties of CuNi alloys are outlined in Table 2 below. The minimum and the maximum values define the typical range for these alloys. For more information, see our article All About Nickel Alloys.
Property | Minimum Value | Maximum Value | Unit |
---|---|---|---|
Property Average Atomic Volume | Minimum Value 0 | Maximum Value 0.0073 | Unit m3/kmol |
Property Density | Minimum Value 8.5 | Maximum Value 8.95 | Unit Mg/m3 |
Property Latent Heat of Fusion | Minimum Value 220 | Maximum Value 240 | Unit kJ/kg |
Property Melting Point | Minimum Value 1384 | Maximum Value 1508 | Unit K |
Property Specific Heat | Minimum Value 384 | Maximum Value 386 | Unit J/kg·K |
Property Thermal Conductivity | Minimum Value 19 | Maximum Value 66 | Unit W/m·K |
Table Credit: https://www.nickel-alloys.net/article/copper-nickel-alloys-alloys-with-copper.html
What Are the Mechanical Properties of Copper Nickel Alloys?
Copper-nickel (CuNi) alloys possess a range of mechanical properties that make them suitable for a number of applications. The specific mechanical properties can vary depending on the alloy grade and heat treatment, but some typical values are outlined in Table 3.
Property | Minimum Value | Maximum Value | Unit |
---|---|---|---|
Property Bulk Modulus | Minimum Value 130 | Maximum Value 170 | Unit GPa |
Property Compressive Strength | Minimum Value 85 | Maximum Value 550 | Unit MPa |
Property Ductility | Minimum Value 3 | Maximum Value 44 | Unit % |
Property Yield Strength | Minimum Value 85 | Maximum Value 550 | Unit MPa |
Property Fracture Toughness | Minimum Value 26 | Maximum Value 79 | Unit MPa·m1/2 |
Property Poisson's Ratio | Minimum Value 0.34 | Maximum Value 0.35 | Unit - |
Property Shear Modulus | Minimum Value 45 | Maximum Value 58 | Unit GPa |
Property Tensile Strength | Minimum Value 267 | Maximum Value 624 | Unit MPa |
Property Young’s Modulus | Minimum Value 120 | Maximum Value 156 | Unit GPa |
Does CuNi Alloy Rust?
No, copper-nickel alloys do not rust because they are not iron or steel, and the term only applies to iron-based alloys. Plain-carbon steels do not have an adherent oxide, which severely limits their corrosion resistance potential. CuNi alloys, on the other hand, have a tightly adherent, protective oxide. As a result, they are well-suited for applications that demand long-term durability, including the construction of saltwater pipelines and marine vessels.
Is Copper Nickel Alloy Expensive?
Yes, copper-nickel alloys are expensive. The cost of copper-nickel (CuNi) alloys can vary depending on several factors, including the specific alloy grade, market conditions, and the quantity and form of the material being purchased. Generally speaking, CuNi alloys tend to be more expensive than stainless steel.
Is CuNi Alloy Safe?
Yes, copper-nickel alloys are considered safe for many applications, but they have some important caveats. In terms of human health, CuNi alloys are generally safe. Copper and nickel are naturally occurring elements found in the environment, food, and water. However, prolonged exposure to elevated concentrations of copper or nickel dust, fumes, or particles, especially in occupational settings, can pose health risks. It is important to follow safety measures, such as ensuring proper ventilation and wearing personal protective equipment when handling CuNi materials.
What Is the Difference Between Copper Nickel Alloy and Alloy Steel?
Copper-nickel alloys and alloy steels are distinct materials with different compositions, properties, and applications. Copper-nickel alloys primarily consist of copper and nickel as the main alloying elements. In contrast, alloy steels are iron-based and encompass a range of steel compositions with various alloying elements, such as carbon, chromium, molybdenum, and manganese. While copper-nickel alloys excel in corrosion resistance, alloy steels are sought after for their mechanical properties. The choice between these materials depends on the specific requirements of the application at hand, be it corrosion resistance or mechanical strength.
Summary
This article summarizes the definition, properties, advantages, and applications of copper-nickel alloys. To learn more about these alloys, contact an Xometry representative.
Xometry provides a wide range of manufacturing capabilities and other value-added services for all of your prototyping and production needs. Visit our website to learn more or to request a free, no-obligation quote.
Disclaimer
The content appearing on this webpage is for informational purposes only. Xometry makes no representation or warranty of any kind, be it expressed or implied, as to the accuracy, completeness, or validity of the information. Any performance parameters, geometric tolerances, specific design features, quality and types of materials, or processes should not be inferred to represent what will be delivered by third-party suppliers or manufacturers through Xometry’s network. Buyers seeking quotes for parts are responsible for defining the specific requirements for those parts. Please refer to our terms and conditions for more information.
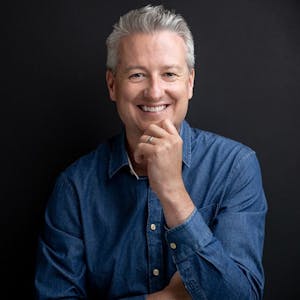