Most materials can be described in terms of their ductility or brittleness. These terms align with opposite ends of a spectrum about a material's response to external forces and loads. Brittle materials tend to fracture suddenly with little deformation, while ductile ones deform significantly before breaking.
Brittle materials like ceramics and glass are known for their compressive strength and dimensional stability. On the other hand, ductile materials, a class that includes many metals, are prized for their capacity to absorb energy through plastic deformation, making them suitable for structures that see dynamic loads and impacts. These contrasting properties profoundly impact material selection, structural design, and product performance.
This article will look at the differences between brittleness and ductility, how materials on this spectrum behave, how the values are calculated, and the concept’s overall importance.
What Is Ductility?
Ductility, a physical property of materials, characterizes their capacity to be stretched, pulled, or drawn into thin wires or threads without fracturing. It quantifies how much the material can deform or elongate under stress before reaching a point of total failure. Ductility is predominantly associated with metals. Metallic bonds — those in which electrons freely flow between atoms — permit atomic sliding and material stretching.
The extent of a metal's ductility is contingent upon electron count and organization within atoms. Electrons nominally orbit the atom's nucleus in rings, known as electron shells, with valence electrons residing in the outermost shell and migrating between atoms. Generally, metals with more valence electrons and more electron shells in general exhibit the highest ductility. Elevated temperatures augment a metal's ductility by rendering valence electrons more mobile.
To learn more, see our guide on What is Ductility.
How Does Ductility Work?
Metals have unique atomic structures characterized by closely packed atoms arranged in a crystalline lattice. The outermost electrons of these atoms are relatively free to move throughout the lattice. This electron mobility is key to the ductile behavior of metals.
When an external force is applied to a metal, the closely packed atoms start to shift positions. The mobility of the free electrons allows atoms to slide past one another without causing immediate fracture. This movement is facilitated by defects in the crystal structure called dislocations. These dislocations move through the lattice, allowing the metal to undergo plastic deformation without catastrophic failure.
As the applied force increases, the metal begins to elongate or change shape in such a way that it will never return to its original dimensions. This is the plastic deformation phase. At this point, the material's stress-strain curve deviates from the initial linear elastic region and enters a non-linear plastic region. The metal can be deformed significantly without fracturing, as long as the applied force doesn't exceed its ultimate tensile strength.
As the deformation progresses, the metal may start to exhibit necking – localized narrowing of the material. This is due to the uneven distribution of stress along the specimen. If the applied force continues to increase and surpasses the material’s ultimate tensile strength, it will eventually fracture. However, compared to brittle materials, metals undergo substantial plastic deformation before reaching this point (except at extremely low temperatures). This plastic deformation allows for energy absorption and is a warning sign of impending failure.
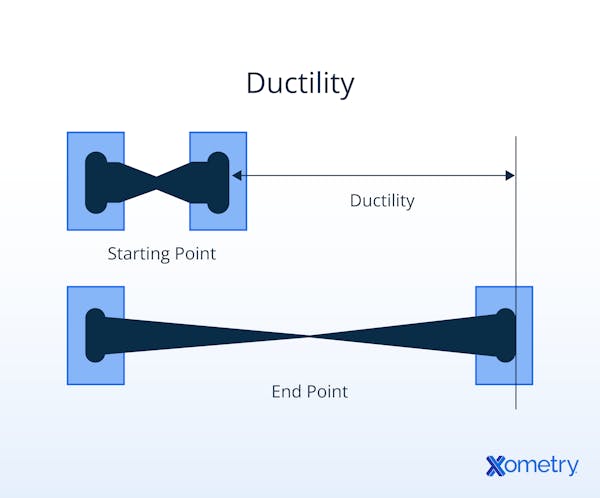
What Is the Importance of Ductility?
Ductility plays a crucial role in structural integrity. Ductile materials can bend and deform without breaking, which is particularly critical for structures that need flexibility. High ductility is especially essential in structural beams and cables. Additionally, ductile metals can be crafted into wires and usually remain flexible in that form.
How To Calculate Ductility?
Ductility is assessed through two methods, both of which require a sample to be loaded until its failure point. One method gauges the sample’s elongation while the other measures the reduction in cross-sectional area. To calculate the ductility through the elongation of a material, the following equation is used:
% elongation = (final length - initial length)/initial length x 100% = (L(f) -L(0))/L(0) x 100%
To calculate the ductility of a material using the reduction of the sample’s cross-sectional area, this equation can be used:
% reduction of area =( initial area-final area)/initial area x 100% = (A(0)-A(f) )/A(0) x 100%
What Are Examples of Ductile Materials?
Most metals exhibit good ductility. The most ductile metals include: silver, gold, aluminum, platinum, copper, and terbium. A few metals, such as high-carbon steel and tungsten, are not very ductile. Non-metals are generally not as ductile, with the exception of some polymers at elevated temperatures. To learn more, see our guide on Ductile Materials.
What Are the Advantages of Ductility?
Ductile fracture has several advantages over brittle fracture, including:
- It is more predictable and controllable than brittle fracture, following a well-defined stress-strain curve and exhibiting deformation before failure.
- It is more forgiving of flaws and defects. Ductile materials can accommodate local stress concentrations and distribute the load around crack tips.
- It absorbs energy during the process of plastic deformation and non-fatal crack propagation.
- The energy-absorbing nature of ductile fracture improves a material's ability to withstand impacts and dynamic loads.
- Ductility helps mitigate residual stresses caused by welding and joining methods so that heat-affected zones are less likely to crack.
What Are the Disadvantages of Ductility?
Although ductility can offer some advantages, it also has some drawbacks:
- Ductile materials may deform excessively, potentially causing loss of functionality or structural integrity in certain applications.
- The plastic deformation associated with ductile fracture can lead to a reduction in strength and stiffness of the material.
- Highly deformable materials are often heavy and expensive.
- Many ductile metals are vulnerable to environmental factors such as temperature variations, corrosion, fatigue, and creep. This can accelerate deterioration and increase the risk of premature failure.
- The combination of excessive deformation, reduced strength, and susceptibility to environmental factors can lead to unexpected or premature failure, especially if not properly accounted for in the design and maintenance processes.
What Is Brittleness?
Brittleness is a mechanical property that describes a material’s tendency to fracture, break, snap, or crack with minimal plastic deformation when subjected to stress. Brittle materials are characterized by their lack of noticeable yielding or elongation before failure. Unlike ductile materials, which can deform significantly before breaking, brittle materials exhibit sudden and often catastrophic failure with little or no warning. Examples of brittle materials include: ceramics, glass, and certain types of cast iron. Brittle behavior is influenced by factors such as: material composition, crystal structure, temperature, and loading conditions.
For more information, see our guide on What is Brittleness.
How Does Brittleness Work?
The behavior of a material, whether brittle or ductile, is influenced by its internal atomic bonds. Brittle materials typically have strong and highly directional bonds which can make them resistant to deformation.
In brittle materials, such as ceramics, the arrangement of atoms in the crystal lattice doesn't easily allow for dislocation movement. The inability of atoms to move past one another means that brittle materials do not experience significant plastic deformation under stress.
When stress is applied to a brittle material, cracks can propagate through the material very quickly due to the lack of dislocation movement. This leads to sudden and catastrophic failure, often without any warning signs. In short, the material does not bend before breaking. The material breaks along planes of weakness or imperfections.
Brittleness is associated with low energy absorption during fracture. Very little energy is absorbed before the material breaks, so the fracture itself is very rapid and clean. Brittleness can be affected by temperature and loading rate. Lower temperatures and higher loading rates increase the likelihood of brittle behavior. At low temperatures, atomic movement is restricted, and cracks can propagate more easily.
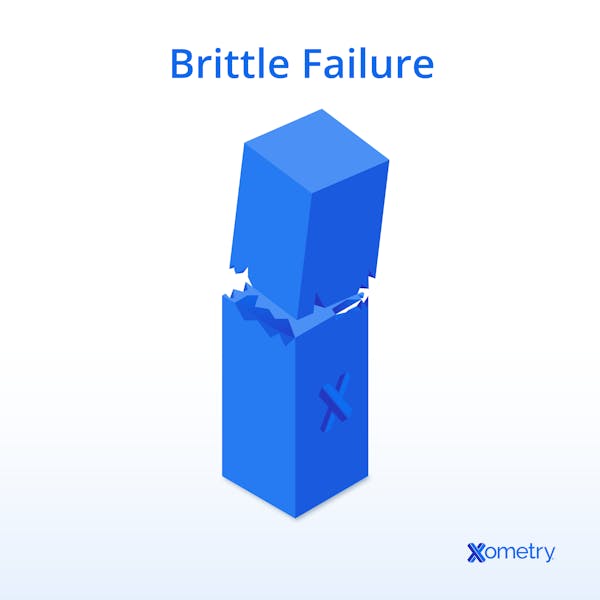
What Is the Importance of Brittleness?
Brittleness is an important property in material science and engineering industries. Such material behavior can have major impacts on the effectiveness and longevity of a design. While brittle materials are frequently chosen for their strength, their propensity for sudden fracture poses significant risks. Because brittle failure can lead to catastrophic consequences, it's often better to use more ductile materials — even if they’re heavier or more expensive — in order to improve the structure’s reliability.
How To Calculate Brittleness?
Brittleness is not typically quantified with a single numerical value. Rather, it is understood based on the material’s behavior under stress and its response to deformation. However, a few qualitative and semi-quantitative measures can be used to assess brittleness. Two of these parameters are the ductility of the material and its critical stress value.
Brittleness is evaluated through a tensile test of the material’s ductility. If it demonstrates low ductility during the tensile test, it is categorized as brittle. The widely recognized procedure for conducting tensile tests on metallic materials is ASTM E8, while for plastics, ASTM D638 provides the corresponding methodology. The tensile test requires a standardized test specimen which is loaded with progressively greater tensile force until the specimen fractures. During the test, the stress and strain values experienced by the specimen are measured to help determine both ductility and, by extension, brittleness.
There are two formulas that can be used to calculate a material’s ductility. One is based on the percentage elongation and the other on reduction in the cross-sectional area of a sample when subjected to fracture loading.
To calculate the ductility through the elongation of material, use the following equation:
% elongation = (final length - initial length)/initial length x 100% = (L(f) -L(0))/L(0) x 100%
To calculate the ductility of a material using the reduction of the cross-sectional area of a sample, fill in this equation:
% reduction of area =(initial area-final area)/initial area x 100% = (A(0)-A(f) )/A(0) x 100%
Another parameter that gives insights into the brittleness of a material is the critical stress point. The term "critical stress" in the context of brittle materials is often used to refer to the stress level at which brittle fracture occurs. Unlike ductile materials that undergo plastic deformation before failure, brittle materials tend to break suddenly without significant warning. The critical stress for brittle fracture is the stress value at which this abrupt fracture is expected to take place. To calculate this value, three fundamental parameters are required, namely: the Specific Surface Energy (γs), Modulus of Elasticity (E), and Length of Crack on the Surface (a).
The formula for determining the critical stress of a brittle material is as follows:
σ(0c) = (2Eγ(s)/πa)^0.5
Where:
σ(c): Brittle Material Critical Stress
E: Modulus of Elasticity
γ(s): Specific Surface Energy
a: Length of Crack on the Surface
What Are Examples of Brittle Materials?
Glass, ceramics, graphite, and certain metal alloys are all characterized by minimal plasticity. In such materials, cracks can emerge without notable plastic deformation and swiftly progress into brittle fractures.
What Are the Advantages of Brittleness?
Brittleness is generally not considered an advantageous property in materials. Unlike ductility, brittleness often leads to sudden and catastrophic failures without warning. However, in some specific applications, brittle materials can offer certain advantages:
- Brittle materials are often extremely hard, which can be advantageous in combating wear, abrasion, and scratching.
- They typically retain their mechanical strength and stability at high temperatures.
- Some materials can transition from brittle to ductile behavior under specific conditions. This can provide a safety buffer against sudden failures and make the material more versatile.
- Brittle materials such as glass and ceramics make for good precision cutting tools and blades. Their ability to break cleanly and predictably can result in precise cuts and edges.
- Glass, though brittle, is transparent, making it valuable for windows, optical lenses, and display screens.
What Are the Disadvantages of Brittleness?
Here’s a breakdown of the disadvantages associated with brittle materials:
- They can fail abruptly without significant warning.
- Brittle fractures absorb little energy before failure, as there is minimal plastic deformation.
- They are generally less tough than ductile materials, making them less able to absorb energy from impacts or loading.
- The lack of plastic deformation in brittle materials can limit design flexibility. Structures cannot easily accommodate changes in shape or load distribution.
- They’re sensitive to defects, imperfections, and microcracks. Such can act as stress concentrators and trigger fractures even under relatively low stress levels.
- Some brittle materials like ceramics can be challenging to machine due to their tendency to chip or fracture during cutting and shaping processes.
- The sudden failure of brittle materials can pose safety risks, especially when human lives or critical infrastructure are involved.
Which Is Stronger, Ductile or Brittle?
Materials with brittle characteristics (such as ceramics, concrete, and untempered steel) exhibit greater strength (higher yield point and ultimate tensile strength) and hardness than similar ductile materials. This is attributed to their limited plastic elongation and deformation capacity. Instead of deforming under stress, these materials experience failure through the breaking of intermolecular bonds, necessitating tensile stress along those bonds.
Does Low Ductility Mean Brittle?
Yes. A significant degree of ductility signifies that a material is more likely to undergo deformation rather than fracture when subjected to tensile stress. Conversely, low ductility suggests that a material is brittle and prone to fracture rather than substantial deformation.
What Does the Stress-Strain Curve for Ductility and Brittleness Look Like?
Both brittle and ductile materials exhibit distinct stress-strain curves. Their contrasting behaviors make for very different curves.
For brittle materials, the stress-strain curve is typically steep and linear, followed by an abrupt end. Initially, as stress is applied, these materials exhibit linear elastic behavior. This means that they deform proportionally to the applied stress and return to their original shape upon stress removal. The slope of this initial linear portion is known as Young's Modulus or elastic modulus. As the stress increases beyond a certain point, however, these materials quickly reach their ultimate strength. The deformation becomes unstable, and the material fractures suddenly and without significant plastic deformation (permanent change in shape). The point where this fracture occurs is known as the ultimate stress or fracture stress.
For ductile materials, the stress-strain curve displays a different pattern. Similar to brittle materials, ductile materials begin with linear elastic behavior. However, their linear portion might extend further, indicating more elastic deformation. Beyond a certain stress level, known as the yield stress, ductile materials enter the plastic deformation region. Here, they exhibit a non-linear stress-strain relationship. Plastic deformation involves the permanent movement of dislocations within the material's crystal structure, allowing it to change shape without fracturing. The yield point is where this plastic deformation begins. The stress required to cause further deformation decreases compared to the initial yield stress. This region is characterized by the necking phenomenon, where localized narrowing of the material occurs.
The Ultimate Tensile Strength (UTS) point is reached at the peak of the stress-strain curve This is the maximum stress the material can withstand before necking and eventual fracture. After the UTS point, the material necks and eventually fractures. Unlike brittle materials, ductile materials exhibit substantial plastic deformation before fracturing. This deformation allows them to absorb energy before failing. It’s also a warning sign of impending failure, making these materials more suitable for applications that need to survive excessive stresses long enough for people to safely disengage from the device or item.
How Do Ductility and Brittleness Affect a Material's Response to Applied Stress?
Ductile materials are easily elongated into wire-like forms and exhibit distinct deformation when subjected to pressure. On the other hand, brittle materials tend to fracture rather than elongate, often resulting in clean breaks. This characteristic makes it relatively simple to rejoin the fractured pieces since the pieces don’t deform prior to breaking apart.
How Do Temperature and Strain Rate Affect Material Ductility and Brittleness?
Some materials can transition from ductile to brittle behavior based on their temperature and strain rate. On a molecular level, temperature is a gauge of atom mobility; greater mobility in a solid equates to a propensity to deform. Meanwhile, strain rate dictates the velocity at which deformation is applied to a substance. The interplay between these factors gives rise to the material's toughness. Elevated temperatures generally enhance ductility by simplifying the movement of dislocations within the material's structure. Conversely, lower temperatures render materials more brittle by inhibiting dislocation mobility and promoting cleavage fracture. The ductile-to-brittle transition temperature is a critical point where materials shift from ductile to brittle behavior, depending on factors like composition and structure.
Strain rate also plays a role in the fracture toughness of a material; higher strain rates, such as those experienced during rapid loading, can push materials towards brittle behavior because dislocations don’t have enough time to fully shift. Slower strain rates, typical of steady loading, promote ductility by only forcing dislocations to move gradually.
The interaction of temperature and strain rate can intensify these effects – cold temperatures and high strain rates can lead to extremely brittle behavior.
Which Type of Material Failure Is Associated With Ductility and Brittleness?
Brittle fracture refers to material breakage without substantial plastic deformation or with only minimal plastic deformation prior to the fracture. Substances like rock, glass, concrete, and cast iron behave like this, thus earning them the “brittle” label. On the other hand, ductile fracture involves significant plastic deformation prior to fracture. Materials exhibiting ductile fracture characteristics include: soft steel, other malleable metals, rubber, and plastics.
Can Metal Be Ductile and Brittle?
Yes. Broadly speaking, metals tend to display more ductile characteristics when subjected to higher temperatures. However, the scenario changes as the temperature decreases to room temperature or below. Metals that exhibit limited deformation capacity before fracturing are categorized as brittle, which essentially stands in contrast to their ductile nature at higher temperatures. This phenomenon is referred to as the ductile to brittle transition. The temperature at which this transition occurs is heavily influenced by the metal's composition. This behavior is most commonly observed in steel.
Other factors also influence the ductility and brittleness of metals. The transition from ductile to brittle behavior is affected by factors like: temperature, loading/strain rate, alloy composition, and microstructure.
Summary
This article presented ductility vs. brittleness, explained each of them, and discussed their key differences. To learn more about ductility and brittleness, contact a Xometry representative.
Xometry provides a wide range of manufacturing capabilities and other value-added services for all of your prototyping and production needs. Visit our website to learn more or to request a free, no-obligation quote.
Disclaimer
The content appearing on this webpage is for informational purposes only. Xometry makes no representation or warranty of any kind, be it expressed or implied, as to the accuracy, completeness, or validity of the information. Any performance parameters, geometric tolerances, specific design features, quality and types of materials, or processes should not be inferred to represent what will be delivered by third-party suppliers or manufacturers through Xometry’s network. Buyers seeking quotes for parts are responsible for defining the specific requirements for those parts. Please refer to our terms and conditions for more information.
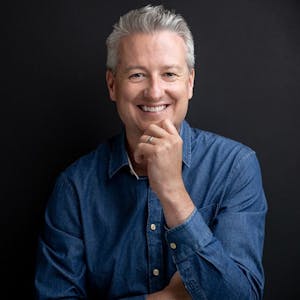