Fracture toughness tests determine a material's resistance to crack propagation and therefore fracture, which is one of the fundamental material properties. It works by applying a constantly increasing load to a material until failure, to work out how much energy can be absorbed. Fracture toughness is important to know as all materials have or will develop flaws during manufacture or service which are prone to crack propagation. The probability of failure can be determined by understanding how a material responds to stress at a stress concentration point.
This article will further discuss fracture toughness, its purpose, standards, and processes, as well as its challenges and benefits.
What Are Fracture Toughness Tests?
Fracture toughness tests apply a constantly increasing load to a material to work out the energy required to overcome a material's resistance to crack propagation. The fracture failure mode is initiated by a flaw in the material which could be a scratch, dent, or corrosion. From the flaw, a crack can propagate causing the material to fail. This test is mechanical and can be performed in conjunction with corrosion, fatigue, and or elevated temperatures. The results of the test may determine the service life span of a material.
To learn more, see our guide on What is Fracture Strength.
How Do Fracture Toughness Tests Work?
The fracture toughness test works by applying a constantly increasing load until the material fails. The material must first be prepared by creating a fatigue notch where the crack can propagate from. This process is usually done with EDM machining. Then the material is subject to loading. There are three modes of testing: mode 1, mode 2, and mode 3. Mode 1 applies loading in a tensile direction, mode 2 applies a load in-plane (resulting in shear stress), and mode 3 is a mixture of the two.
What Do You Need for Fracture Toughness Tests?
To implement a fracture toughness test, you will first need to prepare a testing sample that has a pre-initiated crack. This initial crack will ensure the crack propagates as intended. A universal testing machine can be used to carry out a fracture toughness test. This is useful as these machines can also carry out tensile testing. Aside from the material and equipment, a reference standard is desirable. These standards control the specifics of the machine and setup depending on the material being tested and the method of testing. Both ASTM and ISO have many standards for fracture toughness testing. Some common standards are:
- ISO 12135:2021: Metallic materials—Unified method of test for the determination of quasistatic fracture toughness.
- ISO 17281:2018: Plastics—Determination of fracture toughness (GIC and KIC) at moderately high loading rates (1 m/s).
- ASTM D5528: For interlaminar toughness of unidirectional polymer composites.
- ASTM D6671: Standard test method for mixed Mode I-Mode II interlaminar fracture toughness of unidirectional fiber-reinforced polymer matrix composites.
- ASTM E399: Standard test method for linear-elastic plane-strain fracture toughness of metallic materials.
- ASTM E1921-22a: Standard test method for determination of reference temperature, T0, for ferritic steels in the transition range.
The results of the fracture toughness test are expressed in stress per square root of crack length (MPa/M½). The goal is to have as high a value as possible as this represents a tough material.
What Is the Purpose of Fracture Toughness Tests?
Fracture toughness describes the cracking behavior of materials. If a material has a high fracture toughness, it is resistant to failure due to cracks; it may therefore have a high damage tolerance. A high fracture toughness also demonstrates a material's resistance to fatigue.
What Are the Standards of Fracture Toughness Testing?
There are a large number of standards that may be relevant to a fracture toughness test depending on the material used, and the fracture testing method. Here are some common standards used:
- ISO 12135:2021: Metallic materials—Unified method of testing for the determination of quasistatic fracture toughness.
- ASTM E1820-23b: Standard test method for measurement of fracture toughness.
- ASTM E399: Fracture toughness of metallic steels.
- ASTM D5045-14(2022): Standard test methods for plane-strain fracture toughness and strain energy release rate of plastic materials.
- ASTM E1921: For reference temperature of ferritic steels.
- ISO 12108:2018: Metallic materials—fatigue testing—fatigue crack growth method.
- ISO 13586:2018: Plastics: determination of fracture toughness (GIC and KIC)—linear elastic fracture mechanics (LEFM) approach.
To learn more, read our guide on What are ASTM Standards.
What Is the Process of Fracture Toughness Tests?
There are several methods of fracture toughness test which are similar but with slight variations, including: G, K, J, Crack Tip Opening Displacement (CTOD), and Crack Mouth Opening Displacement (CMOD). CTOD test is one of the common methods of determining the fracture toughness of a material. The test is generally performed by starting with a material with a crack in it and loading said material into a 3-point bend test. The steps for carrying out a CTOD test are as below:
- Prepare the test sample by machining a notch at the material midpoint, then induce a fatigue crack at the machined notch.
- Load the specimen into a 3-point bending setup machine.
- Attach a strain gauge to either side of the crack to accurately measure the strain throughout the test.
- Apply a load until failure and record the results.
What Are the Benefits of Fracture Toughness Tests?
Some benefits of fracture toughness tests include:
- Help to determine the safety of the material.
- Help to determine the life of a material.
- Allow for cost savings through reduced premature maintenance.
What Are the Challenges of Fracture Toughness Tests?
There are several reasons why a fracture toughness test may be challenging to carry out, including:
- Small defects in sample preparation result in massively different results.
- The requirement for many different loading heads for different tests.
- It is not possible to test specimens of a very small thickness.
- Requirement for creating a fatigue crack in the notch before testing.
- Requirement for complex equipment and highly trained operators.
What Should Be the Rating To Pass the Fracture Toughness Tests?
Fracture toughness testing is not the same as most testing methods in which materials either meet the requirement or don’t. With fracture testing, the results have a larger “gray” area. This is mainly because there is a requirement in fracture toughness testing to form a fatigue crack before testing. This crack is hard to repeatedly create and therefore results may vary between a “Pass” or a “Fail”.
What Is the Failure Rating of Fracture Toughness Tests?
Similarly to passing a fracture toughness test, the failure rating of a fracture test will depend on the criteria set out. Additionally, it is not as clear cut as “all specimens tested must meet the load requirement.” If one out of three specimens fails, the probability of fracture may be worked out to judge how likely a material is to fail due to fracture.
What Are the Materials Used for Fracture Toughness Tests?
Fracture toughness testing has been around for a long time. In this period, metals and polymers have mostly been tested. While composites have also been around for quite some time, they are still being used in new applications today which require new fracture toughness testing. A list of materials that are fracture tested includes:
- Metallics
- Polymers
- Composites
- Ceramics
How Are the Materials Being Prepared for Fracture Toughness Tests?
Material specimens are prepared for a fracture toughness test by EDM machining a notch into the test specimen. There are two main shapes to a test specimen—Single Edge Bent (SE(B)), and Compact Tension (C(T)). An SE(B) specimen is long and rectangular with a notch cut in the midpoint of the length. A C(T) is a square with a notch cut at the midpoint of the height of the square and two holes on either side of the notch to load a tensile force. The thickness of the specimen is determined by the standard used. In ASTM E399, testing aluminum, the three thicknesses to test are ⅛", ¼", and ¾".
Can Fracture Toughness Test Be Used for Any Type of Materials?
Yes, any material may be tested for fracture toughness. However, not all test specimens of material will yield the same result. Thin test specimens will have a higher fracture toughness as they have a bigger plastic deformation and are less brittle. As a specimen thickens, its fracture toughness will reduce until it is constant for any thickness. This constant fracture toughness is known as K1c. K1c is often the fracture toughness value used to represent a material's toughness.
Is ASTM the Standards Used for Fracture Toughness Test?
Yes, a large number of ASTM standards apply to fracture toughness testing. The standard used will depend on the material being tested. Some common ASTM standards are E1820-23b (standard test method for measurement of fracture toughness), E399 (fracture toughness of metallic steels), D5045-14(2022): Standard test methods for plane-strain fracture toughness and strain energy release rate of plastic materials, and E1921 (for reference temperature of ferritic steels).
What Is the Difference Between Fracture Toughness Tests and Impact Tests?
The difference between fracture toughness and impact toughness is that a fracture test measures the energy required for crack propagation, whereas an impact test measures the energy required for crack formation. Because these properties are different they are also tested differently. To test fracture toughness a tensile load is applied at a constant rate which is slow enough to avoid any dynamic stresses. Oppositely, during impact tests, the material will experience a sudden absorption of energy. A material may be able to absorb stress plastically during a fracture toughness test, but may not be able to absorb the energy fast enough in an impact test.
Summary
This article presented fracture toughness tests, explained them, and discussed their purpose and standards. To learn more about fracture toughness tests, contact a Xometry representative.
Xometry provides a wide range of manufacturing capabilities and other value-added services for all of your prototyping and production needs. Visit our website to learn more or to request a free, no-obligation quote.
Disclaimer
The content appearing on this webpage is for informational purposes only. Xometry makes no representation or warranty of any kind, be it expressed or implied, as to the accuracy, completeness, or validity of the information. Any performance parameters, geometric tolerances, specific design features, quality and types of materials, or processes should not be inferred to represent what will be delivered by third-party suppliers or manufacturers through Xometry’s network. Buyers seeking quotes for parts are responsible for defining the specific requirements for those parts. Please refer to our terms and conditions for more information.
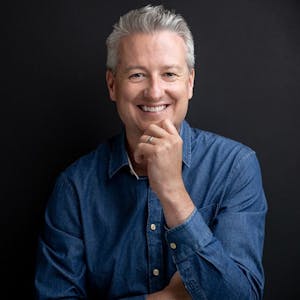